Are you gearing up for a career shift or aiming to ace your next interview? Look no further! We’ve curated a comprehensive guide to help you crack the interview for the coveted Cement Block Maker position. From understanding the key responsibilities to mastering the most commonly asked questions, this blog has you covered. So, buckle up and let’s embark on this journey together.
Acing the interview is crucial, but landing one requires a compelling resume that gets you noticed. Crafting a professional document that highlights your skills and experience is the first step toward interview success. ResumeGemini can help you build a standout resume that gets you called in for that dream job.
Essential Interview Questions For Cement Block Maker
1. What are the key components of a cement block maker machine?
The key components of a cement block maker machine include:
- Vibratory table: Vibrates the mold to ensure even distribution of concrete.
- Hopper: Holds the concrete or cement mixture before it enters the mold.
- Mold: Shapes the concrete into blocks and determines their size and shape.
- Ejector: Pushes the finished blocks out of the mold.
- Hydraulic system: Provides power for the vibration and ejection mechanisms.
2. How do you maintain proper moisture content in the concrete mix?
Maintaining Moisture Content in the Mix
- Regular moisture testing: Use a moisture meter to monitor the water content.
- Adjusting water ratio: Add or reduce water as needed to achieve the desired moisture level.
Effects of Moisture Content
- Too wet: Weak blocks, poor structural integrity.
- Too dry: Difficulty in compaction, brittle blocks.
3. What are the potential causes of cracks or defects in cement blocks?
Potential causes of cracks or defects in cement blocks include:
- Improper curing: Blocks cured too quickly or without proper moisture control.
- Poor compaction: Concrete mix not adequately compacted during molding.
- Overloading: Blocks subjected to excessive weight or stress.
- Contaminants in the mix: Impurities or debris can weaken the concrete.
4. How do you adjust the block size and shape using the machine?
Adjusting block size and shape using the machine typically involves:
- Changing the mold: Different molds are used for different sizes and shapes.
- Adjusting the compaction force: Higher force for denser blocks, lower force for less dense blocks.
- Modifying the vibration frequency: Slower frequency for larger blocks, faster frequency for smaller blocks.
5. What steps should be taken to ensure the safety of operating a cement block maker machine?
To ensure the safety of operating a cement block maker machine, it is crucial to:
- Wear proper safety gear: Safety glasses, gloves, and protective clothing.
- Follow manufacturer’s instructions: Adhere to all safety guidelines and operating procedures.
- Inspect the machine regularly: Check for any defects or damage before each use.
- Use proper lifting techniques: When handling heavy components or blocks.
- Be aware of potential hazards: Such as electrical hazards, moving parts, and dust exposure.
6. How do you troubleshoot common problems with a cement block maker machine?
To troubleshoot common problems with a cement block maker machine, consider the following:
- Blocks not forming properly: Check mold alignment, compaction force, and vibration settings.
- Blocks cracking or breaking: Assess curing conditions, moisture content, and proper handling.
- Excessive wear on components: Inspect for proper lubrication, alignment, and timely replacements.
- Machine overheating: Check hydraulic oil level, cooling system, and air circulation.
- Electrical issues: Refer to electrical diagrams, check connections, and consult an electrician.
7. Can you explain the importance of using the correct concrete mix design for the cement block maker machine?
Using the correct concrete mix design is crucial for:
- Block strength and durability: Proper mix ratios ensure optimal strength and resistance to wear.
- Consistency in production: Standardized mix design prevents variations in block quality.
- Efficiency and cost savings: Optimized mix design reduces waste and improves production efficiency.
8. How do you determine the optimal production rate for a cement block maker machine?
Determining the optimal production rate involves considering:
- Machine capabilities: Speed and efficiency of the specific machine model.
- Concrete mix consistency: Workability and setting time of the concrete mix.
- Production demand: Required output quantity and delivery schedule.
- Staffing and resources: Availability of skilled operators and supporting equipment.
- Environmental conditions: Weather, temperature, and humidity can affect production rates.
9. What quality control measures do you implement to ensure the production of high-quality cement blocks?
Quality control measures include:
- Raw material inspection: Checking the quality of cement, aggregates, and other materials.
- Concrete mix testing: Ensuring proper mix design, moisture content, and consistency.
- Block inspection: Monitoring size, shape, surface finish, and strength of produced blocks.
- Regular machine calibration: Maintaining accuracy and precision of the block maker machine.
- Recordkeeping and documentation: Tracking production parameters and quality control data.
10. Describe your approach to optimizing the efficiency of a cement block maker machine for maximum production.
Optimizing efficiency involves:
- Regular maintenance and servicing: Minimizing downtime and ensuring smooth operation.
- Operator training and monitoring: Enhancing skills and improving production techniques.
- Streamlining production processes: Reducing bottlenecks and improving material flow.
- Using automation and technology: Implementing systems to automate tasks and improve efficiency.
- Continuous improvement: Regularly evaluating and implementing efficiency enhancements.
Interviewers often ask about specific skills and experiences. With ResumeGemini‘s customizable templates, you can tailor your resume to showcase the skills most relevant to the position, making a powerful first impression. Also check out Resume Template specially tailored for Cement Block Maker.
Career Expert Tips:
- Ace those interviews! Prepare effectively by reviewing the Top 50 Most Common Interview Questions on ResumeGemini.
- Navigate your job search with confidence! Explore a wide range of Career Tips on ResumeGemini. Learn about common challenges and recommendations to overcome them.
- Craft the perfect resume! Master the Art of Resume Writing with ResumeGemini’s guide. Showcase your unique qualifications and achievements effectively.
- Great Savings With New Year Deals and Discounts! In 2025, boost your job search and build your dream resume with ResumeGemini’s ATS optimized templates.
Researching the company and tailoring your answers is essential. Once you have a clear understanding of the Cement Block Maker‘s requirements, you can use ResumeGemini to adjust your resume to perfectly match the job description.
Key Job Responsibilities
Cement Block Makers are responsible for setting up, operating and maintaining concrete block making machines. Their primary duties include ensuring the production of quality concrete blocks that meet specifications, conducting routine machine checks, performing basic repairs, and working in a safe work environment.
1. Production of Concrete Blocks
Concrete Block Makers are responsible for managing the entire concrete block production process. They start by setting up the concrete block making machine, including selecting and installing the correct molds and ensuring the machine is running smoothly.
- Monitoring the production process to ensure concrete blocks are produced according to specifications.
- Making necessary adjustments to the machine to optimize production efficiency and block quality.
- Packaging and stacking the finished concrete blocks for storage or transportation.
2. Machine Maintenance
Cement Block Makers are also responsible for performing basic maintenance on the concrete block making machine to ensure it remains in good working condition. This includes regular inspections, cleaning, lubrication, and minor repairs.
- Conducting daily inspections to identify any potential problems or maintenance needs.
- Performing routine cleaning and lubrication to prevent breakdowns and extend the machine’s lifespan.
- Carrying out minor repairs, such as replacing worn parts or tightening loose bolts, to keep the machine running smoothly.
3. Workplace Safety
Cement Block Makers must adhere to strict safety protocols to minimize the risk of accidents and injuries in the workplace. They are responsible for wearing appropriate personal protective equipment (PPE) and following established safety procedures.
- Maintaining a clean and organized work area to prevent tripping or slipping hazards.
- Using proper lifting techniques to avoid back injuries or strains.
Interview Tips
Interviewing for a Cement Block Maker position can be challenging, but by following these tips, you can increase your chances of success:
1. Research the Company and Position
Before the interview, thoroughly research the company and the specific Cement Block Maker position you are applying for. Learn about the company’s history, values, and products, as well as the responsibilities and expectations of the role.
- Tailor your answers to the specific requirements of the job by highlighting your relevant skills and experience.
- Prepare thoughtful questions about the company, the position, and the industry to demonstrate your interest and engagement.
2. Practice Common Interview Questions
Practice answering common interview questions to enhance your fluency and confidence during the actual interview. Some common questions for a Cement Block Maker position include:
- Why are you interested in this Cement Block Maker position?
- Tell me about your experience in operating and maintaining concrete block making machines.
- How do you ensure the production of high-quality concrete blocks that meet specifications?
- Describe your approach to workplace safety and how you prioritize it in your work.
3. Showcase Your Skills and Experience
Highlight your relevant skills and experience in your answers, quantifying your accomplishments whenever possible. Use the STAR method (Situation, Task, Action, Result) to provide clear and concise examples of your work.
- Emphasize your proficiency in operating and maintaining concrete block making machines, including any certifications or training you have received.
- Provide specific examples of how you have improved production efficiency, reduced downtime, or ensured the quality of concrete blocks.
4. Be Enthusiastic and Professional
Throughout the interview, maintain a positive and enthusiastic attitude. Demonstrate your interest in the position and the company, and express your eagerness to contribute to their success.
- Dress professionally and arrive on time for the interview.
- Be polite and respectful to everyone you meet, including the receptionist and other employees.
Next Step:
Now that you’re armed with the knowledge of Cement Block Maker interview questions and responsibilities, it’s time to take the next step. Build or refine your resume to highlight your skills and experiences that align with this role. Don’t be afraid to tailor your resume to each specific job application. Finally, start applying for Cement Block Maker positions with confidence. Remember, preparation is key, and with the right approach, you’ll be well on your way to landing your dream job. Build an amazing resume with ResumeGemini
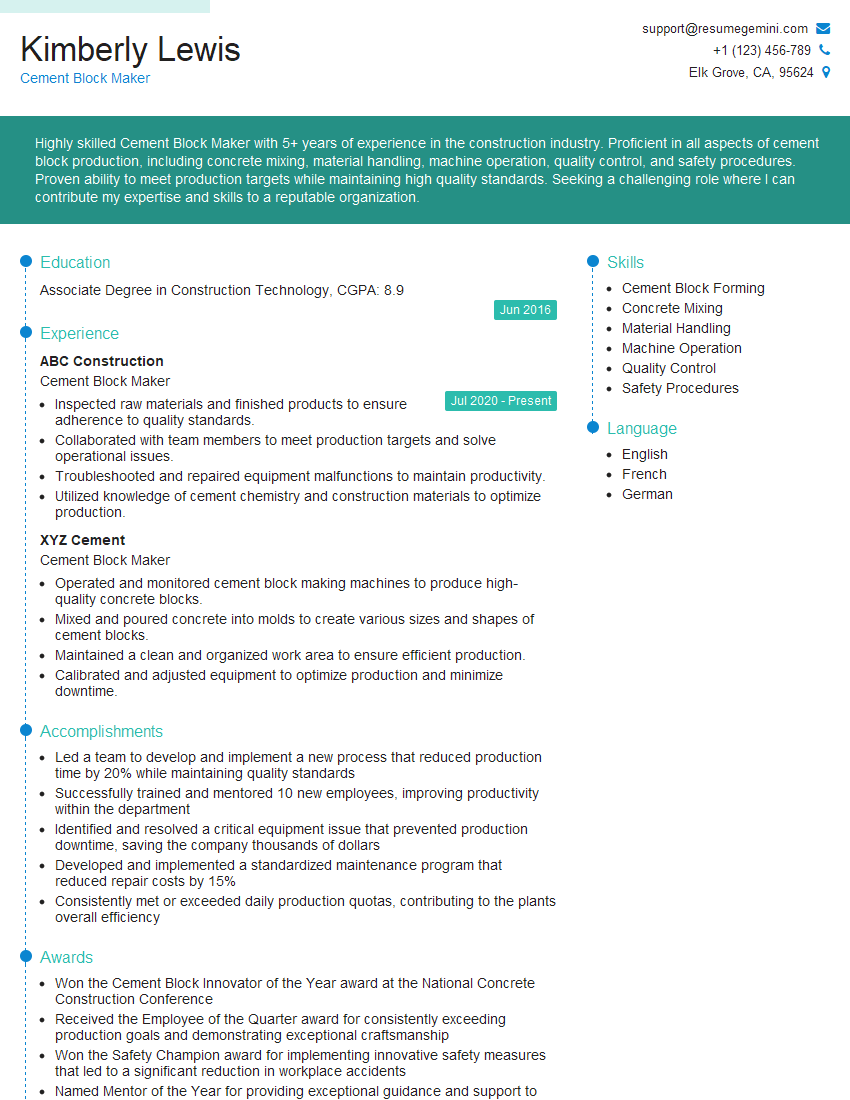