Feeling lost in a sea of interview questions? Landed that dream interview for Compress Machine Operator but worried you might not have the answers? You’re not alone! This blog is your guide for interview success. We’ll break down the most common Compress Machine Operator interview questions, providing insightful answers and tips to leave a lasting impression. Plus, we’ll delve into the key responsibilities of this exciting role, so you can walk into your interview feeling confident and prepared.
Acing the interview is crucial, but landing one requires a compelling resume that gets you noticed. Crafting a professional document that highlights your skills and experience is the first step toward interview success. ResumeGemini can help you build a standout resume that gets you called in for that dream job.
Essential Interview Questions For Compress Machine Operator
1. Explain the process of setting up a compress machine for production?
The process of setting up a compress machine for production involves several steps:
- Inspect the machine: Ensure that all components are in good condition and free from any defects.
- Gather necessary materials: Collect the required materials, such as inserts, die parts, and raw materials.
- Install the inserts and die parts: Securely install the inserts and die parts into the machine according to specifications.
- Calibrate the machine: Adjust the machine’s settings, including pressure, temperature, and cycle time, based on the production requirements.
- Load the raw materials: Feed the raw materials into the machine’s hopper or loading area.
- Start production: Initiate the production process and monitor the machine’s performance.
2. What are the common types of materials used in compression molding and their key characteristics?
Common types of materials used in compression molding include:
Thermoplastics
- Polyethylene (PE): Versatile, lightweight, and chemically resistant
- Polypropylene (PP): Durable, impact-resistant, and moisture-resistant
- Polystyrene (PS): Disposable, cost-effective, and good insulator
Thermosetting plastics
- Phenolic resins: Heat-resistant, electrical insulators, and resistant to wear
- Melamine resins: Durable, scratch-resistant, and food-safe
- Epoxy resins: High strength, excellent adhesion, and chemical resistance
3. Describe the different types of defects that can occur in compression molded parts and how to prevent them?
Common defects in compression molded parts include:
- Flash: Excess material that forms around the edges of the part due to improper mold closure.
- Sinks: Depressions in the part’s surface due to insufficient material flow.
- Voids: Air pockets within the part due to improper material compaction.
- Cracks: Fractures in the part due to excessive stress or improper curing.
To prevent these defects, ensure proper mold design, material selection, process parameters, and quality control measures.
4. Explain the importance of mold temperature control in compression molding?
Mold temperature control is crucial in compression molding for several reasons:
- Material flow: Temperature affects the viscosity of the material, influencing its flow and filling characteristics.
- Part quality: Proper temperature control helps achieve desired surface finish, dimensions, and mechanical properties.
- Cycle time: Optimizing mold temperature can reduce cooling time, resulting in faster production cycles.
- Mold life: Excessive temperatures can damage the mold, while too low temperatures may not provide sufficient heat transfer.
5. How do you troubleshoot common problems encountered during compression molding operations?
Troubleshooting common problems in compression molding involves:
- Identifying the problem: Analyze the symptoms, such as part defects, machine behavior, or process deviations.
- Tracing the root cause: Investigate potential causes based on knowledge of the process and equipment.
- Implementing solutions: Develop and implement corrective actions, such as adjusting process parameters, repairing faulty components, or modifying mold design.
- Verifying results: Test the implemented solutions to ensure effectiveness and prevent recurrence of the problem.
6. What safety precautions should be taken when operating a compression molding machine?
Safety precautions for operating a compression molding machine include:
- Proper training: Ensure thorough training on machine operation, safety procedures, and emergency protocols.
- Protective equipment: Wear appropriate protective gear, including gloves, safety glasses, and hearing protection.
- Machine guarding: Verify that all safety guards and interlocks are in place and functional.
- Hot surfaces: Be aware of potential hazards from hot surfaces, such as the press platen and molds.
- Emergency stops: Familiarize yourself with the location and operation of emergency stop buttons.
7. Describe the maintenance procedures you perform on compression molding machines?
Regular maintenance procedures for compression molding machines include:
- Daily inspections: Check for any visible damage, leaks, or unusual noises.
- Weekly maintenance: Lubricate moving parts, clean molds, and inspect hydraulic systems.
- Monthly maintenance: Perform more thorough inspections, including electrical checks and filter replacements.
- Annual maintenance: Conduct a comprehensive overhaul, including deep cleaning, component replacement, and calibration.
8. What is the role of quality control in compression molding?
Quality control in compression molding ensures:
- Product quality: Establish and maintain quality standards for molded parts.
- Process monitoring: Track production parameters and identify any deviations from specifications.
- Defect detection: Inspect finished parts for defects and implement corrective actions.
- Customer satisfaction: Meet customer requirements and maintain product consistency.
9. How do you stay updated on advancements in compression molding technology?
To stay updated on advancements in compression molding technology:
- Attend industry events: Participate in conferences, trade shows, and workshops.
- Read technical publications: Stay abreast of research papers, industry magazines, and technical articles.
- Connect with experts: Network with professionals in the field, join online forums, and seek guidance from industry leaders.
- Explore online resources: Utilize online databases, industry websites, and vendor information to gather knowledge about new technologies and trends.
10. Why are you interested in this position as a Compress Machine Operator?
I am eager to join your organization as a Compress Machine Operator for the following reasons:
- Passion for manufacturing: I have a strong interest in the manufacturing industry and find compression molding particularly fascinating.
- Skilled and experienced: My previous experience as a Compress Machine Operator has equipped me with the technical skills and knowledge required for this role.
- Quality-focused: I am dedicated to producing high-quality molded parts and maintaining a clean and safe work environment.
- Team player: I excel in collaborative settings and am eager to contribute my expertise to your team.
- Continuous learner: I am committed to continuous learning and keeping up with advancements in compression molding technology.
Interviewers often ask about specific skills and experiences. With ResumeGemini‘s customizable templates, you can tailor your resume to showcase the skills most relevant to the position, making a powerful first impression. Also check out Resume Template specially tailored for Compress Machine Operator.
Career Expert Tips:
- Ace those interviews! Prepare effectively by reviewing the Top 50 Most Common Interview Questions on ResumeGemini.
- Navigate your job search with confidence! Explore a wide range of Career Tips on ResumeGemini. Learn about common challenges and recommendations to overcome them.
- Craft the perfect resume! Master the Art of Resume Writing with ResumeGemini’s guide. Showcase your unique qualifications and achievements effectively.
- Great Savings With New Year Deals and Discounts! In 2025, boost your job search and build your dream resume with ResumeGemini’s ATS optimized templates.
Researching the company and tailoring your answers is essential. Once you have a clear understanding of the Compress Machine Operator‘s requirements, you can use ResumeGemini to adjust your resume to perfectly match the job description.
Key Job Responsibilities
Compress Machine Operators are responsible for the operation, maintenance, and repair of compress machines used in a variety of industries. They ensure that machines are operating efficiently and safely, and that products are produced according to specifications. Key job responsibilities include:
1. Machine Operation
Operate compress machines to compress air, gases, or other materials.
- Monitor machine performance and make adjustments as needed.
- Ensure that machines are operating safely and efficiently.
2. Machine Maintenance
Perform routine maintenance on compress machines, including lubrication, cleaning, and troubleshooting.
- Identify and repair mechanical problems.
- Replace worn or damaged parts.
3. Product Quality Control
Monitor the quality of compressed products and make adjustments to ensure that they meet specifications.
- Conduct quality control tests and inspections.
- Identify and correct product defects.
4. Safety and Compliance
Follow all safety regulations and procedures.
- Wear appropriate personal protective equipment.
- Maintain a clean and safe work area.
Interview Tips
Preparing for an interview can be a daunting task, but by following these tips, candidates can increase their chances of success:
1. Research the Company and Position
Before the interview, candidates should research the company and the position they are applying for. This will help them understand the company’s culture, values, and goals, as well as the specific requirements of the position. Candidates can use the company’s website, LinkedIn page, and other online resources to gather information.
2. Practice Answering Common Interview Questions
There are a number of common interview questions that candidates can expect to be asked, such as “Tell me about yourself” and “Why are you interested in this position?” Candidates should practice answering these questions in a clear and concise way. They should also be prepared to provide specific examples of their skills and experience that are relevant to the position.
3. Dress Professionally and Arrive on Time
First impressions matter, so it is important for candidates to dress professionally for their interview. They should also arrive on time, as being late can be seen as disrespectful.
4. Be Enthusiastic and Confident
Candidates should be enthusiastic about the position and the company they are applying to. They should also be confident in their abilities and qualifications. However, they should avoid being arrogant or overbearing.
5. Follow Up
After the interview, candidates should send a thank-you note to the interviewer. This is an opportunity to reiterate their interest in the position and to thank the interviewer for their time. Candidates can also use the thank-you note to address any questions or concerns that were not raised during the interview.
Next Step:
Now that you’re armed with a solid understanding of what it takes to succeed as a Compress Machine Operator, it’s time to turn that knowledge into action. Take a moment to revisit your resume, ensuring it highlights your relevant skills and experiences. Tailor it to reflect the insights you’ve gained from this blog and make it shine with your unique qualifications. Don’t wait for opportunities to come to you—start applying for Compress Machine Operator positions today and take the first step towards your next career milestone. Your dream job is within reach, and with a polished resume and targeted applications, you’ll be well on your way to achieving your career goals! Build your resume now with ResumeGemini.
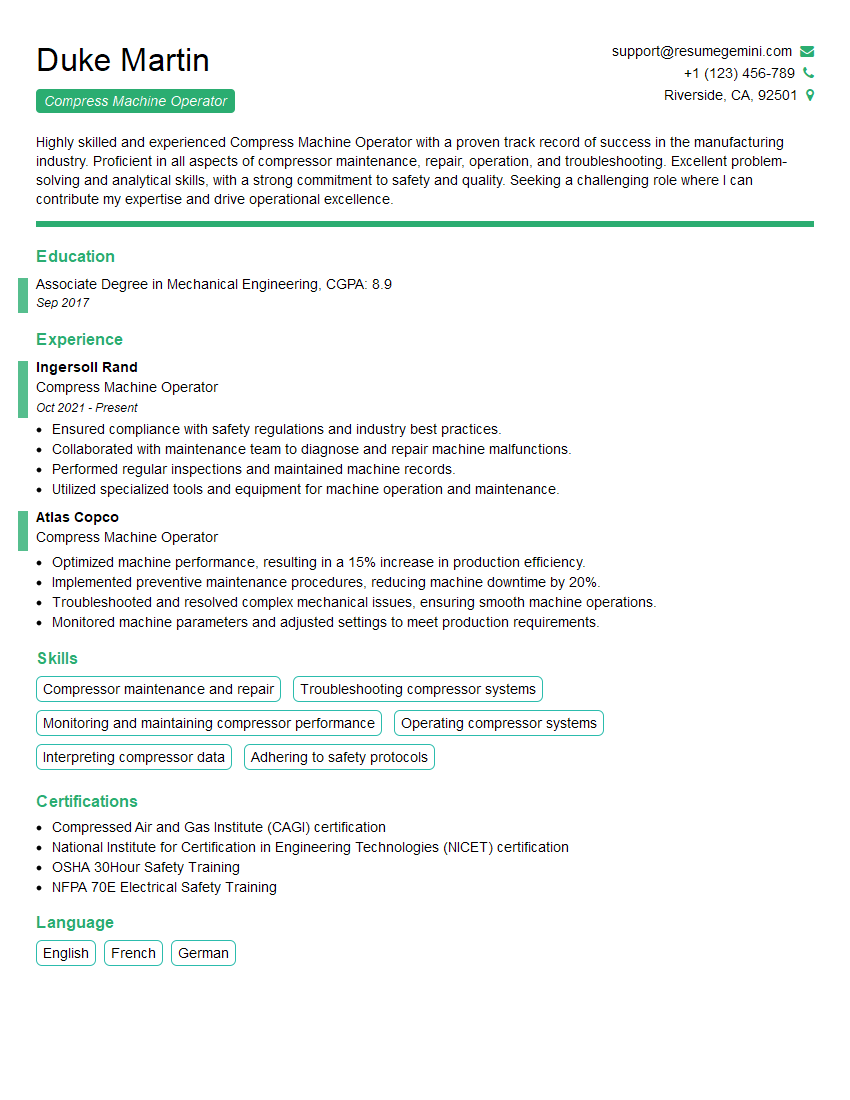