Are you gearing up for a career in Quality Cloth Tester? Feeling nervous about the interview questions that might come your way? Don’t worry, you’re in the right place. In this blog post, we’ll dive deep into the most common interview questions for Quality Cloth Tester and provide you with expert-backed answers. We’ll also explore the key responsibilities of this role so you can tailor your responses to showcase your perfect fit.
Acing the interview is crucial, but landing one requires a compelling resume that gets you noticed. Crafting a professional document that highlights your skills and experience is the first step toward interview success. ResumeGemini can help you build a standout resume that gets you called in for that dream job.
Essential Interview Questions For Quality Cloth Tester
1. What are the key responsibilities of a Quality Cloth Tester?
As a Quality Cloth Tester, my primary responsibilities would include:
- Performing physical and chemical tests on fabrics to evaluate their quality and meet industry standards.
- Identifying and diagnosing fabric defects, analyzing their causes, and recommending corrective actions.
- Maintaining and calibrating testing equipment to ensure accurate and reliable results.
- Documenting test procedures, results, and findings for analysis and reporting purposes.
- Collaborating with other departments to ensure quality standards are met throughout the production process.
2. What are the different types of testing you perform on fabrics?
- Tensile strength and elongation
- Tear strength
- Abrasion resistance
- Pilling and fuzzing
- Shrinkage and moisture absorption
- Colorfastness to light, washing, and dry cleaning
- Flammability
- Chemical resistance
- Water repellency and absorption
3. How do you interpret test results and determine the quality of fabrics?
I interpret test results by comparing them to established industry standards and customer specifications. I assess the fabric’s performance against these criteria to determine its suitability for specific applications. I also identify any areas where the fabric may not meet the desired quality and recommend corrective actions to improve its performance.
4. What are some of the challenges you face in your role as a Quality Cloth Tester?
Some of the challenges I face in my role include:
- Ensuring that all testing equipment is properly maintained and calibrated to produce accurate results.
- Keeping up-to-date with industry standards and regulations to ensure that our testing methods align with the latest requirements.
- Objectively assessing fabric quality and providing unbiased recommendations based on the test results.
- Maintaining a high level of attention to detail and precision throughout the testing process.
5. How do you stay informed about the latest developments in fabric testing?
To stay informed about the latest developments in fabric testing, I engage in the following activities:
- Attending industry conferences and workshops
- Reading professional journals and publications
- Participating in online forums and discussion groups with other quality control professionals
- Working closely with fabric manufacturers and suppliers to gain insights into new testing technologies and methodologies
6. What is your approach to problem-solving when you encounter a fabric that does not meet quality standards?
When I encounter a fabric that does not meet quality standards, I adopt the following approach to problem-solving:
- Identify the specific issue: I carefully inspect the fabric to identify the defect or issue that is causing it to fail the quality test.
- Investigate the cause: I research the fabric’s history, manufacturing process, and any other relevant information to determine the root cause of the problem.
- Recommend corrective actions: Based on my investigation, I propose specific actions that can be taken to improve the fabric’s quality and prevent the issue from recurring.
- Monitor and verify the results: I follow up on the implementation of corrective actions and monitor the fabric’s performance to ensure that the issue has been resolved effectively.
7. How do you communicate your findings and recommendations to stakeholders?
I communicate my findings and recommendations to stakeholders in the following ways:
- Written reports: I prepare detailed reports that summarise the test results, identify any quality issues, and provide specific recommendations for improvement.
- Verbal presentations: I present my findings and recommendations to management and other stakeholders in meetings or presentations, using visual aids to illustrate key points.
- Informal discussions: I engage in informal discussions with colleagues and clients to share my insights and provide guidance on fabric quality-related matters.
8. What is your understanding of the AATCC test methods?
AATCC (American Association of Textile Chemists and Colorists) test methods are widely used in the textile industry to evaluate the quality and performance of fabrics. I am familiar with a range of AATCC test methods, including:
- AATCC 8: Colorfastness to light
- AATCC 16: Colorfastness to washing
- AATCC 61: Tear strength
- AATCC 135: Dimensional change to laundering
- AATCC 147: Flammability of textiles
9. How do you ensure that your testing procedures are accurate and reliable?
I ensure the accuracy and reliability of my testing procedures by adhering to the following practices:
- Standard operating procedures: I follow established standard operating procedures (SOPs) for each test method to ensure consistency and accuracy.
- Calibration and maintenance: I regularly calibrate and maintain all testing equipment to ensure its proper functioning and accuracy.
- Quality control checks: I perform regular quality control checks on test results to identify any anomalies or errors.
- External audits: I participate in external audits conducted by accredited organisations to validate the accuracy and reliability of our testing procedures.
10. How do you handle situations where test results are inconclusive or contradictory?
When I encounter inconclusive or contradictory test results, I take the following steps:
- Repeat testing: I repeat the test to confirm the results and rule out any errors or inconsistencies.
- Investigate testing conditions: I examine the testing conditions, such as temperature, humidity, and equipment settings, to identify any potential factors that may have influenced the results.
- Consult with colleagues: I discuss the results with colleagues to gain their insights and perspectives.
- Seek expert advice: If necessary, I consult with experts or industry specialists to obtain additional guidance and support in interpreting the results.
Interviewers often ask about specific skills and experiences. With ResumeGemini‘s customizable templates, you can tailor your resume to showcase the skills most relevant to the position, making a powerful first impression. Also check out Resume Template specially tailored for Quality Cloth Tester.
Career Expert Tips:
- Ace those interviews! Prepare effectively by reviewing the Top 50 Most Common Interview Questions on ResumeGemini.
- Navigate your job search with confidence! Explore a wide range of Career Tips on ResumeGemini. Learn about common challenges and recommendations to overcome them.
- Craft the perfect resume! Master the Art of Resume Writing with ResumeGemini’s guide. Showcase your unique qualifications and achievements effectively.
- Great Savings With New Year Deals and Discounts! In 2025, boost your job search and build your dream resume with ResumeGemini’s ATS optimized templates.
Researching the company and tailoring your answers is essential. Once you have a clear understanding of the Quality Cloth Tester‘s requirements, you can use ResumeGemini to adjust your resume to perfectly match the job description.
Key Job Responsibilities
Quality Cloth Testers are accountable for the quality of textiles in a variety of settings, from manufacturing plants to retail stores. It is their role to ensure that fabrics meet the required standards and specifications, which can include testing for durability, colorfastness, and flammability. They may also be involved in developing and implementing quality control procedures, and training staff on quality standards. Overall, Quality Cloth Testers play a critical role in the textile industry, helping to ensure that consumers receive high-quality products.
1. Conducting Physical Tests
Quality Cloth Testers conduct a variety of physical tests on fabrics to assess their quality. These tests may include:
- Tensile strength testing: This test measures the fabric’s resistance to tearing.
- Breaking strength testing: This test measures the fabric’s resistance to breaking.
- Abrasion resistance testing: This test measures the fabric’s resistance to wear and tear.
- Pilling resistance testing: This test measures the fabric’s resistance to the formation of pills.
2. Conducting Chemical Tests
In addition to physical tests, Quality Cloth Testers also conduct chemical tests on fabrics to assess their quality. These tests may include:
- Colorfastness testing: This test measures the fabric’s resistance to fading.
- Shrinkage testing: This test measures the fabric’s resistance to shrinkage.
- Flammability testing: This test measures the fabric’s resistance to fire.
3. Developing and Implementing Quality Control Procedures
Quality Cloth Testers may also be involved in developing and implementing quality control procedures. These procedures may include:
- Establishing quality standards
- Developing testing methods
- Training staff on quality standards
- Monitoring quality control
4. Training Staff
Quality Cloth Testers may also be responsible for training staff on quality standards. This training may include:
- Teaching staff how to conduct physical and chemical tests
- Teaching staff how to interpret test results
- Teaching staff how to maintain quality control procedures
Interview Tips
Preparing for an interview for a Quality Cloth Tester position can be daunting, but with the right preparation, you can increase your chances of success. Here are a few tips to help you ace your interview:
1. Research the company and the position
Before you go to your interview, take some time to research the company and the position you are applying for. This will help you understand the company’s culture and values, as well as the specific requirements of the job. You can find information about the company on their website, social media pages, and Glassdoor.
2. Practice answering common interview questions
There are a number of common interview questions that you are likely to be asked, such as “Tell me about yourself” and “Why are you interested in this position?” It is helpful to practice answering these questions in advance so that you can deliver your responses confidently and concisely.
3. Be prepared to talk about your experience
In your interview, you will be asked about your experience and qualifications. Be prepared to talk about your experience in detail, and be sure to highlight your skills and abilities that are relevant to the position you are applying for.
4. Ask questions
At the end of your interview, you will be given the opportunity to ask questions. This is a great time to learn more about the company and the position, and to show the interviewer that you are interested and engaged.
Next Step:
Armed with this knowledge, you’re now well-equipped to tackle the Quality Cloth Tester interview with confidence. Remember, a well-crafted resume is your first impression. Take the time to tailor your resume to highlight your relevant skills and experiences. And don’t forget to practice your answers to common interview questions. With a little preparation, you’ll be on your way to landing your dream job. So what are you waiting for? Start building your resume and start applying! Build an amazing resume with ResumeGemini.
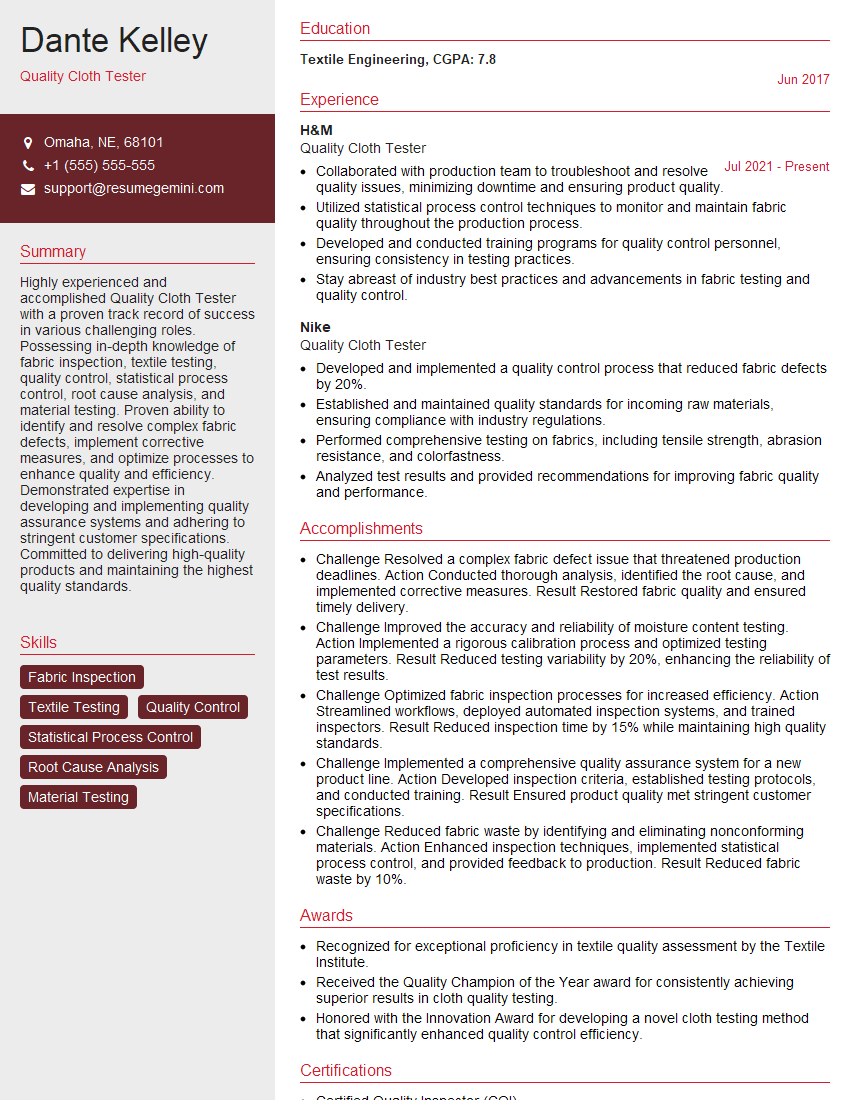