Are you gearing up for a career in Case Packer? Feeling nervous about the interview questions that might come your way? Don’t worry, you’re in the right place. In this blog post, we’ll dive deep into the most common interview questions for Case Packer and provide you with expert-backed answers. We’ll also explore the key responsibilities of this role so you can tailor your responses to showcase your perfect fit.
Acing the interview is crucial, but landing one requires a compelling resume that gets you noticed. Crafting a professional document that highlights your skills and experience is the first step toward interview success. ResumeGemini can help you build a standout resume that gets you called in for that dream job.
Essential Interview Questions For Case Packer
1. How do you ensure that the case packer is operating efficiently and producing quality cases?
To ensure efficient operation and quality case production, I follow a comprehensive approach that includes:
- Regular Maintenance: Adhering to scheduled maintenance plans, conducting thorough inspections, and promptly addressing any issues.
- Operator Training: Providing comprehensive training to operators on proper machine operation, troubleshooting techniques, and quality control procedures.
- Process Monitoring: Continuously monitoring the packing process to identify and rectify any deviations from optimal performance.
- Quality Checks: Implementing rigorous quality checks at various stages of the packing process to ensure that cases meet specifications and customer requirements.
2. How do you troubleshoot common case packer issues?
Mechanical Issues
- Jamming: Inspecting case flow, verifying conveyor alignment, and adjusting tension settings.
- Misalignment: Checking case guides, ensuring proper case orientation, and adjusting alignment components.
Electrical Issues
- Motor Failures: Diagnosing motor issues, replacing faulty components, and checking power supply.
- Sensor Malfunctions: Inspecting sensors, verifying wiring, and replacing malfunctioning sensors.
Product Issues
- Incorrect Case Size: Verifying case specifications, adjusting case former accordingly, and reconfiguring the machine settings.
- Product Damage: Analyzing product characteristics, modifying case design or packing materials, and adjusting machine speed and settings.
3. How do you prioritize tasks and manage multiple responsibilities in a fast-paced production environment?
In a fast-paced production environment, I prioritize tasks and manage multiple responsibilities effectively through:
- Planning and Organization: I plan my day in advance, prioritizing critical tasks and allocating time accordingly.
- Time Management: I employ time management techniques such as the Pomodoro Technique or Eisenhower Matrix to maximize productivity.
- Delegation: I delegate tasks to capable team members when necessary, providing clear instructions and monitoring progress to ensure timely completion.
4. How do you stay up-to-date on the latest case packing technologies and advancements?
To stay current with the latest case packing technologies and advancements, I engage in continuous learning and development:
- Industry Events: I attend industry conferences, exhibitions, and workshops to learn about new technologies and connect with experts.
- Technical Publications: I read trade magazines, journals, and online articles to stay informed about industry trends and advancements.
- Manufacturer Training: I participate in training programs offered by case packing equipment manufacturers to enhance my knowledge of their latest products and technologies.
5. How do you ensure compliance with safety regulations and maintain a safe working environment?
Safety is paramount, and I ensure compliance with regulations and maintain a safe working environment through:
- Regular Safety Inspections: I conduct regular inspections of equipment, work areas, and safety procedures.
- Training and Awareness: I provide comprehensive safety training to all operators and team members, emphasizing hazard identification, risk assessment, and emergency response protocols.
- Equipment Maintenance: I ensure that all equipment is properly maintained and functioning safely, adhering to manufacturer specifications.
- Personal Protective Equipment: I enforce the use of appropriate personal protective equipment, such as safety glasses, earplugs, and gloves.
6. How do you work effectively as part of a team to achieve production goals?
Teamwork is crucial, and I work effectively as part of a team to achieve production goals by:
- Communication: I maintain open and frequent communication with team members, sharing information, updates, and any challenges.
- Collaboration: I actively collaborate with colleagues, seeking input, sharing ideas, and supporting each other in achieving common objectives.
- Problem-Solving: When faced with challenges, I approach them as a team, brainstorming solutions and working together to find effective resolutions.
7. How do you handle working under pressure and meeting tight deadlines?
In a fast-paced production environment, I handle working under pressure and meeting tight deadlines by:
- Time Management: I plan my work effectively, allocate time wisely, and prioritize tasks to ensure timely completion.
- Stress Management: I employ stress management techniques such as deep breathing exercises and positive self-talk to maintain composure under pressure.
- Collaboration: I communicate with team members and supervisors to seek support and delegate tasks when necessary.
8. How do you improve efficiency and productivity in your work?
I am continuously seeking ways to improve efficiency and productivity in my work by:
- Process Optimization: I analyze existing processes, identify bottlenecks, and implement improvements to streamline operations.
- Technology Utilization: I leverage technology to automate tasks, improve data collection, and enhance decision-making.
- Training and Development: I invest in ongoing training and development to enhance my skills and knowledge, enabling me to work more efficiently.
9. How do you ensure product quality and minimize defects?
To ensure product quality and minimize defects, I employ the following strategies:
- Rigorous Inspections: I conduct thorough inspections at various stages of the packing process to identify potential defects.
- Defect Analysis: I analyze defects to determine their root causes and implement corrective actions to prevent recurrence.
- Continuous Improvement: I actively seek opportunities for improvement by evaluating processes, implementing best practices, and incorporating feedback from customers and team members.
10. How do you handle unexpected events or equipment failures that impact production?
When faced with unexpected events or equipment failures that impact production, I take the following steps:
- Rapid Response: I assess the situation quickly, prioritize actions, and respond promptly to minimize downtime.
- Troubleshooting: I utilize my technical expertise to troubleshoot equipment issues and identify solutions.
- Communication: I keep stakeholders informed of the situation, provide regular updates, and coordinate with maintenance personnel to resolve issues swiftly.
Interviewers often ask about specific skills and experiences. With ResumeGemini‘s customizable templates, you can tailor your resume to showcase the skills most relevant to the position, making a powerful first impression. Also check out Resume Template specially tailored for Case Packer.
Career Expert Tips:
- Ace those interviews! Prepare effectively by reviewing the Top 50 Most Common Interview Questions on ResumeGemini.
- Navigate your job search with confidence! Explore a wide range of Career Tips on ResumeGemini. Learn about common challenges and recommendations to overcome them.
- Craft the perfect resume! Master the Art of Resume Writing with ResumeGemini’s guide. Showcase your unique qualifications and achievements effectively.
- Great Savings With New Year Deals and Discounts! In 2025, boost your job search and build your dream resume with ResumeGemini’s ATS optimized templates.
Researching the company and tailoring your answers is essential. Once you have a clear understanding of the Case Packer‘s requirements, you can use ResumeGemini to adjust your resume to perfectly match the job description.
Key Job Responsibilities
Case Packers are responsible for preparing, packing, and labeling cases of products in a warehouse or manufacturing environment. They work in fast-paced, physically demanding roles and must be able to meet or exceed production quotas. Below are the key responsibilities of a Case Packer:
1. Case Preparation
Case Packers prepare cases for packing by assembling them, attaching labels, and ensuring they meet quality standards. They may also reinforce cases with packing materials, such as foam or cardboard, to prevent damage during transport.
2. Product Loading
Case Packers load products into cases, ensuring they are packed securely and efficiently. They may use manual or automated equipment to load products, and must take care to avoid damaging them.
3. Case Sealing and Labeling
Case Packers seal cases using tape, glue, or other materials to ensure they are secure and tamper-proof. They also attach labels to cases, which may include product information, shipping details, and barcodes.
4. Case Palletizing and Load Out
Case Packers palletize cases onto pallets, ensuring they are stacked securely and safely. They may use forklifts or other equipment to move pallets, and must take care to prevent damage to cases or products.
Interview Tips
Preparing for an interview for a Case Packer position can help you make a strong impression and increase your chances of success. Here are some interview tips and hacks to help you ace the interview:
1. Research the Company and Position
Before the interview, take some time to research the company and the specific Case Packer position you are applying for. This will help you understand the company’s culture, values, and goals, and tailor your answers to the specific requirements of the position.
2. Practice Answering Common Interview Questions
There are a number of common interview questions that you are likely to be asked, such as “Tell me about yourself” and “Why are you interested in this position?”. Practice answering these questions in advance so that you can deliver clear, concise, and compelling responses.
3. Highlight Your Skills and Experience
Be sure to highlight your relevant skills and experience during the interview. For example, if you have experience in packing and handling products, or if you are proficient in using forklifts or other equipment, be sure to mention this in your answers.
4. Be Enthusiastic and Professional
First impressions matter, so be sure to be enthusiastic and professional throughout the interview. Dress appropriately, arrive on time, and be polite and respectful to the interviewer.
Next Step:
Now that you’re armed with interview-winning answers and a deeper understanding of the Case Packer role, it’s time to take action! Does your resume accurately reflect your skills and experience for this position? If not, head over to ResumeGemini. Here, you’ll find all the tools and tips to craft a resume that gets noticed. Don’t let a weak resume hold you back from landing your dream job. Polish your resume, hit the “Build Your Resume” button, and watch your career take off! Remember, preparation is key, and ResumeGemini is your partner in interview success.
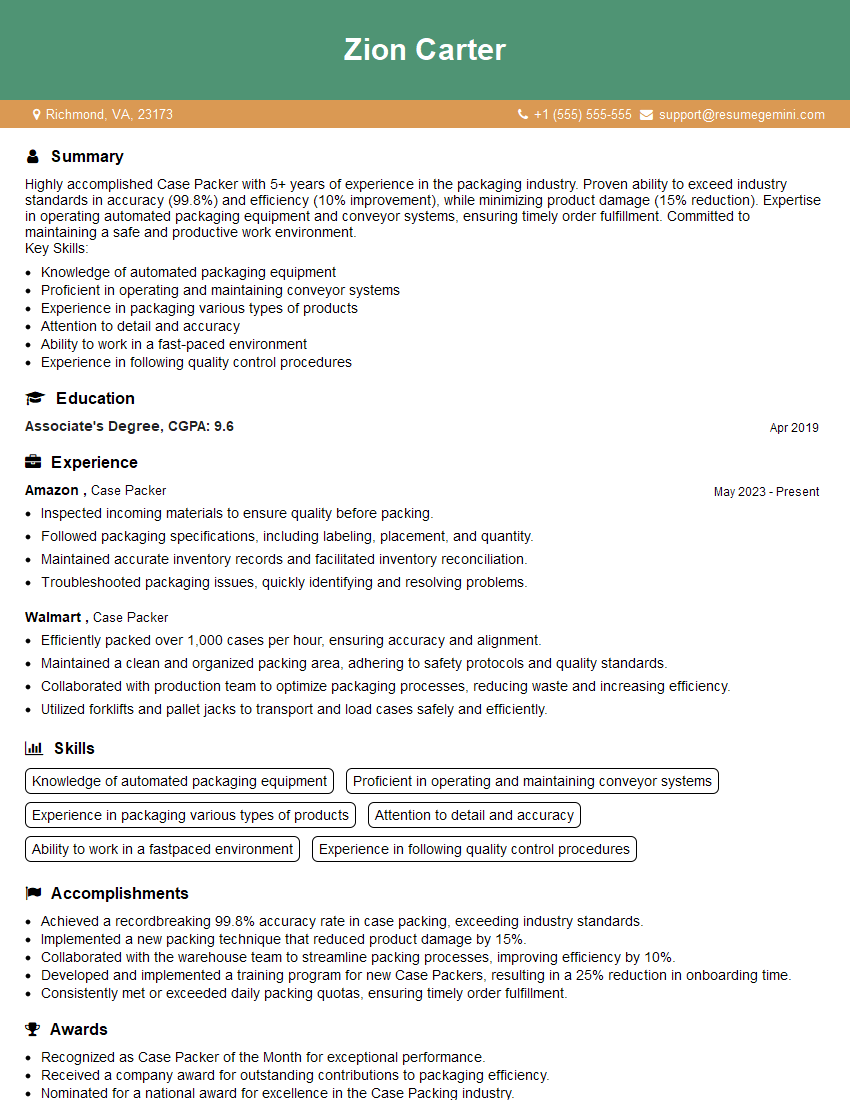