Are you gearing up for a career in Cutting Department Supervisor? Feeling nervous about the interview questions that might come your way? Don’t worry, you’re in the right place. In this blog post, we’ll dive deep into the most common interview questions for Cutting Department Supervisor and provide you with expert-backed answers. We’ll also explore the key responsibilities of this role so you can tailor your responses to showcase your perfect fit.
Acing the interview is crucial, but landing one requires a compelling resume that gets you noticed. Crafting a professional document that highlights your skills and experience is the first step toward interview success. ResumeGemini can help you build a standout resume that gets you called in for that dream job.
Essential Interview Questions For Cutting Department Supervisor
1. Describe the key responsibilities and duties of a Cutting Department Supervisor?
As a Cutting Department Supervisor, my primary responsibilities would be to:
- Plan, organize, and supervise all aspects of the cutting department’s operations, ensuring efficient and effective fabric cutting.
- Oversee the maintenance and calibration of cutting equipment, including spreaders, cutters, and inspection machines, to guarantee precision and accuracy.
- Train, develop, and motivate a team of fabric cutters, ensuring they adhere to quality standards and safety protocols.
- Implement and enforce cutting techniques to optimize fabric utilization and minimize waste, maximizing material yield.
- Coordinate with other departments, such as design, production, and quality control, to ensure seamless communication and alignment in achieving production goals.
2. How do you ensure the accuracy and precision of fabric cutting?
Supervision and Training
- Provide clear instructions and training to cutters on proper cutting techniques, equipment operation, and quality standards.
- Conduct regular inspections and audits of cutting operations to identify and correct any deviations from specified tolerances.
Equipment Maintenance and Calibration
- Establish a preventive maintenance schedule for all cutting equipment to ensure optimal performance.
- Calibrate cutting machines regularly according to manufacturer specifications to maintain accuracy and precision.
Quality Control
- Implement a quality control system to inspect cut pieces for accuracy, consistency, and compliance with design specifications.
- Provide feedback to cutters on areas for improvement and recognize exceptional performance.
3. How do you manage and optimize fabric inventory to minimize waste?
To minimize fabric waste and optimize inventory management, I would employ the following strategies:
- Implement a comprehensive inventory control system to track fabric usage, consumption, and availability.
- Collaborate with the design and production teams to optimize pattern layouts and minimize fabric waste during cutting.
- Explore innovative cutting techniques, such as automated spreading and nesting systems, to enhance fabric utilization.
- Repurpose fabric scraps and remnants for other applications, reducing waste and maximizing material yield.
- Conduct regular audits and reviews of fabric inventory to identify potential areas for improvement and cost savings.
4. How do you handle production deadlines and ensure timely delivery of cut fabrics?
To ensure timely delivery of cut fabrics and meet production deadlines, I would implement the following strategies:
- Establish a clear production schedule and communicate it effectively to the cutting team.
- Monitor progress regularly and identify potential bottlenecks or delays.
- Prioritize cutting orders based on urgency and customer requirements.
- Cross-train cutters to increase flexibility and ensure efficient workflow.
- Communicate proactively with production and other departments to anticipate and address any challenges.
5. How do you motivate and develop your team of fabric cutters?
To motivate and develop my team of fabric cutters, I would implement the following strategies:
- Create a positive and supportive work environment where cutters feel valued and respected.
- Provide regular feedback on performance, both positive and constructive, to facilitate growth and improvement.
- Offer opportunities for professional development through training, workshops, and industry events.
- Recognize and reward exceptional performance to acknowledge and motivate cutters.
- Encourage teamwork and collaboration to foster a sense of ownership and accountability.
6. How do you ensure compliance with safety regulations and maintain a safe working environment in the cutting department?
To ensure compliance with safety regulations and maintain a safe working environment in the cutting department, I would:
- Establish and enforce clear safety protocols and procedures for all cutting operations.
- Provide comprehensive safety training to cutters, emphasizing potential hazards and proper safety practices.
- Conduct regular safety inspections to identify and mitigate any potential risks.
- Ensure that all cutting equipment is properly guarded and maintained to prevent accidents.
- Foster a culture of safety awareness and encourage cutters to report any concerns or unsafe conditions promptly.
7. Describe your experience in implementing and managing lean manufacturing principles in the cutting department.
In my previous role as Cutting Department Supervisor at [Company Name], I successfully implemented and managed lean manufacturing principles to enhance efficiency and reduce waste in the cutting process. Key initiatives included:
- Value Stream Mapping: Conducted value stream mapping exercises to identify and eliminate non-value-added activities in the cutting process.
- 5S Implementation: Implemented the 5S system to organize and standardize the work environment, reducing search time and improving productivity.
- Kanban System: Introduced a Kanban system to regulate the flow of materials and optimize inventory levels.
- Continuous Improvement: Established a culture of continuous improvement by encouraging cutters to identify and suggest process enhancements.
- Results: As a result of these initiatives, we achieved a 15% reduction in cutting time and a 10% reduction in fabric waste.
8. How do you stay updated on the latest advancements in cutting technology and industry best practices?
To stay updated on the latest advancements in cutting technology and industry best practices, I engage in the following activities:
- Attend industry conferences and trade shows to learn about new technologies and innovations.
- Read trade publications and industry journals to stay informed about emerging trends and best practices.
- Participate in online forums and discussion groups to connect with other professionals and share knowledge.
- Conduct research and explore online resources to identify potential improvements to cutting processes.
- Seek opportunities for training and professional development to enhance my technical expertise.
9. Describe your approach to quality control and how you ensure that cut fabrics meet customer specifications.
My approach to quality control involves the following steps:
- Establishing clear quality standards and specifications based on customer requirements.
- Implementing a comprehensive inspection process to assess the accuracy, consistency, and quality of cut fabrics.
- Providing cutters with detailed instructions and training on inspection procedures.
- Regularly monitoring and evaluating the quality of cut fabrics to identify areas for improvement.
- Implementing corrective actions to address any quality issues and prevent their recurrence.
10. How do you manage the relationship with fabric suppliers to ensure timely delivery and quality of materials?
To manage the relationship with fabric suppliers and ensure timely delivery and quality of materials, I would:
- Establish clear communication channels and maintain regular contact with suppliers.
- Review supplier performance regularly, considering factors such as delivery time, fabric quality, and responsiveness.
- Negotiate favorable terms and conditions, including pricing, payment schedules, and delivery lead times.
- Conduct supplier audits to assess their production capabilities, quality control measures, and environmental practices.
- Foster a collaborative relationship with suppliers to identify potential improvements and address any challenges.
Interviewers often ask about specific skills and experiences. With ResumeGemini‘s customizable templates, you can tailor your resume to showcase the skills most relevant to the position, making a powerful first impression. Also check out Resume Template specially tailored for Cutting Department Supervisor.
Career Expert Tips:
- Ace those interviews! Prepare effectively by reviewing the Top 50 Most Common Interview Questions on ResumeGemini.
- Navigate your job search with confidence! Explore a wide range of Career Tips on ResumeGemini. Learn about common challenges and recommendations to overcome them.
- Craft the perfect resume! Master the Art of Resume Writing with ResumeGemini’s guide. Showcase your unique qualifications and achievements effectively.
- Great Savings With New Year Deals and Discounts! In 2025, boost your job search and build your dream resume with ResumeGemini’s ATS optimized templates.
Researching the company and tailoring your answers is essential. Once you have a clear understanding of the Cutting Department Supervisor‘s requirements, you can use ResumeGemini to adjust your resume to perfectly match the job description.
Key Job Responsibilities
The Cutting Department Supervisor oversees all aspects of the cutting department in a garment manufacturing facility. They are responsible for ensuring that the department meets production goals, quality standards, and safety regulations.
1. Production Management
The Cutting Department Supervisor plans, schedules, and coordinates the production of cut fabric. This includes determining the most efficient use of equipment and labor, as well as ensuring that all orders are completed on time and to specification.
- Determines production schedules and ensures the department meets production targets.
- Allocates resources and assigns tasks to team members based on their skills and experience.
2. Quality Control
The Cutting Department Supervisor is responsible for ensuring that all cut fabric meets the required quality standards. This includes inspecting fabric for defects, ensuring that it is cut accurately, and correcting any errors.
- Conducts regular quality checks on cut fabric to ensure it meets specifications.
- Identifies and corrects any errors or defects in the cutting process.
3. Safety Management
The Cutting Department Supervisor is responsible for ensuring that all employees follow safety procedures and that the department is a safe working environment. This includes providing safety training, conducting safety inspections, and enforcing safety regulations.
- Develops and implements safety procedures for the cutting department.
- Conducts regular safety inspections and ensures that all equipment is in good working order.
4. Team Management
The Cutting Department Supervisor leads and manages a team of cutters and other staff. This includes providing training, motivation, and feedback, as well as resolving conflicts and ensuring a positive work environment.
- Provides training and mentoring to team members to improve their skills and knowledge.
- Motivates and inspires team members to achieve high performance.
Interview Tips
To prepare for an interview for a Cutting Department Supervisor position, it is important to research the company and the position itself. You should also be prepared to answer questions about your experience, skills, and qualifications.
1. Research the Company and Position
Before the interview, take some time to research the company and the position you are applying for. This will help you understand the company’s culture, goals, and needs. It will also help you tailor your answers to the specific requirements of the position.
- Visit the company website to learn about its history, mission, and products or services.
- Read industry news and articles to understand the company’s position in the market.
2. Quantify Your Experience
When answering questions about your experience, be sure to quantify your results whenever possible. This will help the interviewer understand the impact of your work.
- For example, instead of saying “I managed a team of cutters,” you could say “I managed a team of 10 cutters and increased production by 15%.”
- Use specific numbers and metrics to demonstrate your accomplishments.
3. Highlight Your Skills and Qualifications
In addition to your experience, the interviewer will also be interested in your skills and qualifications. Be sure to highlight the skills and qualifications that are most relevant to the position you are applying for.
- Make a list of your skills and qualifications, and then tailor your answers to the specific requirements of the position.
- Be prepared to provide examples of how you have used your skills and qualifications to achieve success in your previous roles.
4. Practice Your Answers
Once you have prepared your answers to common interview questions, take some time to practice your delivery. This will help you feel more confident and prepared during the interview.
- Practice answering questions in front of a mirror or with a friend or family member.
- Time yourself to make sure you can answer questions concisely and within the allotted time.
Next Step:
Armed with this knowledge, you’re now well-equipped to tackle the Cutting Department Supervisor interview with confidence. Remember, preparation is key. So, start crafting your resume, highlighting your relevant skills and experiences. Don’t be afraid to tailor your application to each specific job posting. With the right approach and a bit of practice, you’ll be well on your way to landing your dream job. Build your resume now from scratch or optimize your existing resume with ResumeGemini. Wish you luck in your career journey!
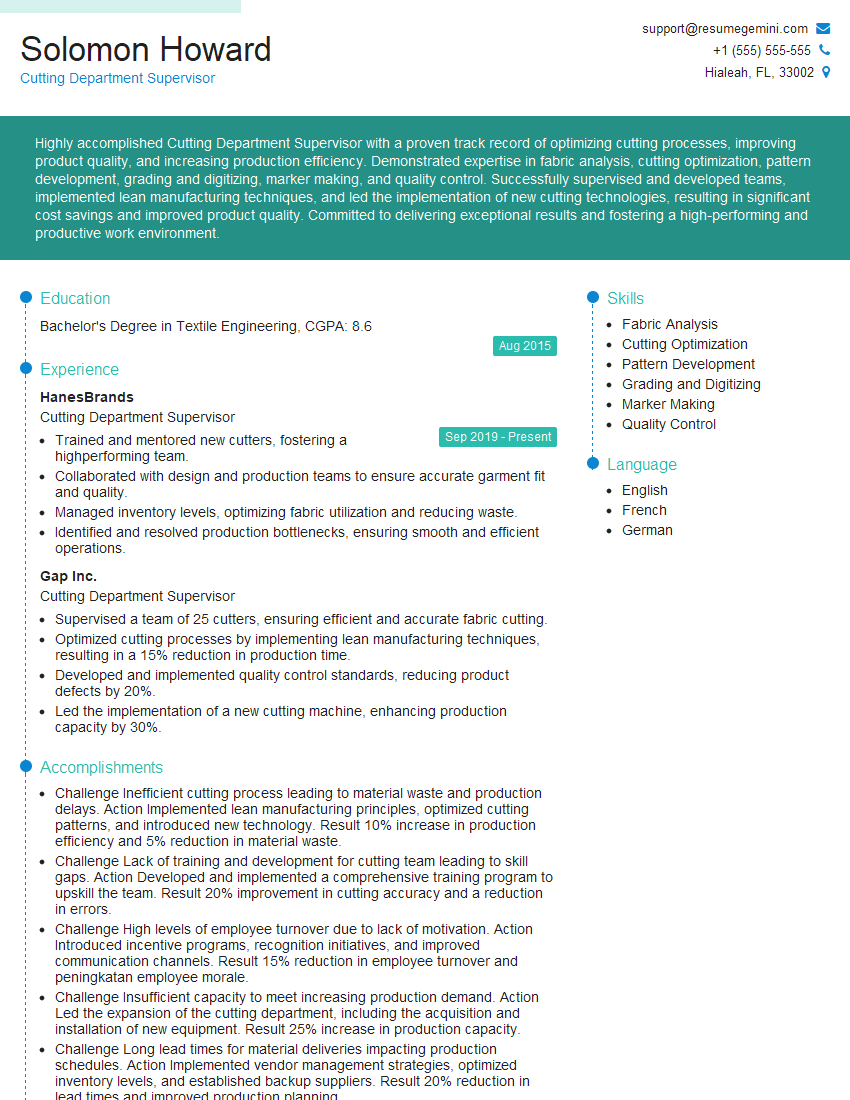