Are you gearing up for a career in Hot Dip Tinning Supervisor? Feeling nervous about the interview questions that might come your way? Don’t worry, you’re in the right place. In this blog post, we’ll dive deep into the most common interview questions for Hot Dip Tinning Supervisor and provide you with expert-backed answers. We’ll also explore the key responsibilities of this role so you can tailor your responses to showcase your perfect fit.
Acing the interview is crucial, but landing one requires a compelling resume that gets you noticed. Crafting a professional document that highlights your skills and experience is the first step toward interview success. ResumeGemini can help you build a standout resume that gets you called in for that dream job.
Essential Interview Questions For Hot Dip Tinning Supervisor
1. Describe the key responsibilities of a Hot Dip Tinning Supervisor?
As a Hot Dip Tinning Supervisor, my key responsibilities are to:
- Supervise and coordinate the activities of the hot dip tinning line, ensuring efficient and safe operations.
- Monitor and control the quality of tinned products, ensuring they meet specifications and customer requirements.
- Train and develop team members, providing guidance and support to enhance their skills and knowledge.
- Implement and maintain quality control procedures, ensuring compliance with industry standards and regulations.
- Troubleshoot and resolve technical issues related to the tinning process, minimizing downtime and product defects.
2. Explain the principles of hot dip tinning.
Metallurgical principles
- Discuss the formation of the tin-iron intermetallic layer.
- Describe the effects of different process parameters on the coating thickness and adhesion.
Chemical process
- Explain the role of flux in the tinning process.
- Discuss the importance of proper surface preparation and cleaning.
3. What are the common defects in hot dip tinning and how do you prevent them?
Common defects in hot dip tinning include:
- Dross inclusions: Caused by impurities in the molten tin bath. Prevented by maintaining bath cleanliness and using filtration systems.
- Solder balls: Formed due to localized overheating. Prevented by controlling bath temperature and immersion time.
- Uncoated areas: Result from improper surface preparation or inadequate fluxing. Prevented by ensuring proper cleaning and fluxing practices.
- Excessive coating thickness: Caused by extended immersion time or high bath temperature. Prevented by controlling process parameters.
- Warpage: Can occur due to uneven heating or cooling. Prevented by proper handling of the products during and after tinning.
4. How do you ensure the quality of the tinned products?
I ensure the quality of tinned products through various measures:
- Visual inspection: Inspecting products for defects such as dross inclusions, uncoated areas, and excessive coating thickness.
- Coating thickness testing: Using non-destructive methods (e.g., magnetic or eddy current) to measure the thickness of the tin coating.
- Adhesion testing: Conducting tests (e.g., peel test or cross-cut test) to assess the adhesion of the tin coating to the base metal.
- Salt spray testing: Evaluating the corrosion resistance of the tin coating by exposing the products to a salt spray environment.
- Ongoing monitoring and adjustment: Continuously monitoring process parameters and making adjustments as needed to ensure consistent product quality.
5. What are the safety precautions to be taken during hot dip tinning operations?
Safety precautions in hot dip tinning include:
- Proper personal protective equipment (PPE): Wearing protective clothing, gloves, and face shields to prevent exposure to molten tin and chemicals.
- Ventilation: Ensuring adequate ventilation to remove fumes and vapors generated during the process.
- Fire prevention: Implementing measures to prevent and extinguish fires, including proper storage and handling of flammable materials.
- Lockout/tagout procedures: Establishing procedures for isolating and de-energizing equipment during maintenance or repairs.
- Emergency response plan: Having a plan in place for responding to emergencies, including spills, fires, and injuries.
6. How do you optimize the tinning process for efficiency and cost-effectiveness?
Optimizing the tinning process involves:
- Equipment maintenance: Regularly inspecting and maintaining equipment to prevent breakdowns and ensure smooth operations.
- Process control: Monitoring and controlling process parameters (e.g., temperature, flux concentration) to minimize defects and ensure consistency.
- Material handling: Implementing efficient handling practices to reduce product damage and improve productivity.
- Waste reduction: Implementing measures to minimize waste generation and optimize raw material usage.
- Continuous improvement: Regularly evaluating the process and implementing improvements to enhance efficiency and cost-effectiveness.
7. Describe your experience in implementing new technologies or innovations in hot dip tinning.
In my previous role as a Hot Dip Tinning Supervisor, I was involved in the implementation of several new technologies:
- Automated coating thickness monitoring system: Implemented a system to automatically measure and control the thickness of the tin coating, ensuring consistent product quality.
- Non-destructive testing (NDT) equipment: Introduced NDT methods to evaluate the adhesion and corrosion resistance of the tin coating, improving product reliability.
- Digital data logging and reporting system: Established a system to collect and analyze process data, enabling real-time monitoring and improved decision-making.
- Environmental monitoring system: Implemented a system to monitor air quality and emissions, ensuring compliance with environmental regulations.
8. How do you manage a team of tinning line operators?
I manage my team by:
- Establishing clear roles and responsibilities: Assigning specific tasks and expectations to each team member.
- Providing regular training and support: Ensuring team members have the necessary skills and knowledge to perform their jobs effectively.
- Maintaining open communication: Fostering a collaborative environment where team members can share ideas and concerns.
- Delegating responsibilities: Empowering team members to make decisions and take ownership of their tasks.
- Recognizing and rewarding achievements: Acknowledging and appreciating team members’ contributions to motivate and maintain high performance.
9. Describe your approach to troubleshooting and problem-solving in the hot dip tinning process.
My approach to troubleshooting and problem-solving involves:
- Identifying the root cause: Analyzing the symptoms and gathering data to determine the underlying cause of the problem.
- Developing and implementing solutions: Formulating and testing solutions to address the root cause and prevent recurrence.
- Collaboration and knowledge sharing: Consulting with colleagues and experts to leverage collective knowledge and best practices.
- Continuous improvement: Learning from problem-solving experiences and implementing measures to prevent similar issues in the future.
10. How do you stay up-to-date with the latest developments and best practices in hot dip tinning?
To stay up-to-date, I:
- Attend industry conferences and workshops: Participating in events to learn about new technologies, innovations, and best practices.
- Read technical publications and journals: Staying informed about the latest research and developments in the field.
- Network with industry professionals: Connecting with colleagues, suppliers, and experts to exchange knowledge and ideas.
- Participate in professional development programs: Undertaking courses and certifications to enhance my skills and knowledge.
Interviewers often ask about specific skills and experiences. With ResumeGemini‘s customizable templates, you can tailor your resume to showcase the skills most relevant to the position, making a powerful first impression. Also check out Resume Template specially tailored for Hot Dip Tinning Supervisor.
Career Expert Tips:
- Ace those interviews! Prepare effectively by reviewing the Top 50 Most Common Interview Questions on ResumeGemini.
- Navigate your job search with confidence! Explore a wide range of Career Tips on ResumeGemini. Learn about common challenges and recommendations to overcome them.
- Craft the perfect resume! Master the Art of Resume Writing with ResumeGemini’s guide. Showcase your unique qualifications and achievements effectively.
- Great Savings With New Year Deals and Discounts! In 2025, boost your job search and build your dream resume with ResumeGemini’s ATS optimized templates.
Researching the company and tailoring your answers is essential. Once you have a clear understanding of the Hot Dip Tinning Supervisor‘s requirements, you can use ResumeGemini to adjust your resume to perfectly match the job description.
Key Job Responsibilities
The Hot Dip Tinning Supervisor is responsible for overseeing the production and quality of tinned products in a manufacturing environment. This role involves managing all aspects of the hot dip tinning process, ensuring that products meet customer specifications and industry standards.
1. Production Management
Oversees daily production operations, including scheduling, staffing, and equipment maintenance.
- Develops and implements production plans and procedures.
- Monitors production lines to ensure efficient operation and identify bottlenecks.
2. Quality Control
Ensures that tinned products meet quality standards by conducting inspections and implementing quality assurance measures.
- Establishes quality control protocols and procedures.
- Inspects finished products for defects and non-conformances.
3. Process Optimization
Continuously improves the hot dip tinning process by identifying and implementing efficiency gains.
- Conducts process audits and identifies areas for improvement.
- Develops and implements process modifications to enhance productivity.
4. Team Management
Supervises a team of employees, including operators, technicians, and quality inspectors.
- Provides training and development for team members.
- Motivates and leads the team to achieve production goals.
Interview Tips
To prepare effectively for an interview as a Hot Dip Tinning Supervisor, consider the following tips:
1. Research the Company and Industry
Learn about the company’s history, products, and industry trends. This will demonstrate your interest in the role and the company.
2. Highlight Your Experience and Skills
Emphasize your experience in hot dip tinning or a related field, as well as your technical skills and leadership abilities.
3. Prepare for Common Interview Questions
Anticipate and prepare answers to common interview questions, such as:
- Tell us about your experience in hot dip tinning.
- How do you ensure product quality in a manufacturing environment?
- Describe your approach to managing a team and motivating employees.
4. Ask Thoughtful Questions
Ask thoughtful questions about the company and the role to show your interest and engagement.
5. Follow Up and Thank the Interviewers
After the interview, send a thank-you note and reiterate your interest in the role. This will show your appreciation and leave a positive impression.
Next Step:
Now that you’re armed with interview-winning answers and a deeper understanding of the Hot Dip Tinning Supervisor role, it’s time to take action! Does your resume accurately reflect your skills and experience for this position? If not, head over to ResumeGemini. Here, you’ll find all the tools and tips to craft a resume that gets noticed. Don’t let a weak resume hold you back from landing your dream job. Polish your resume, hit the “Build Your Resume” button, and watch your career take off! Remember, preparation is key, and ResumeGemini is your partner in interview success.
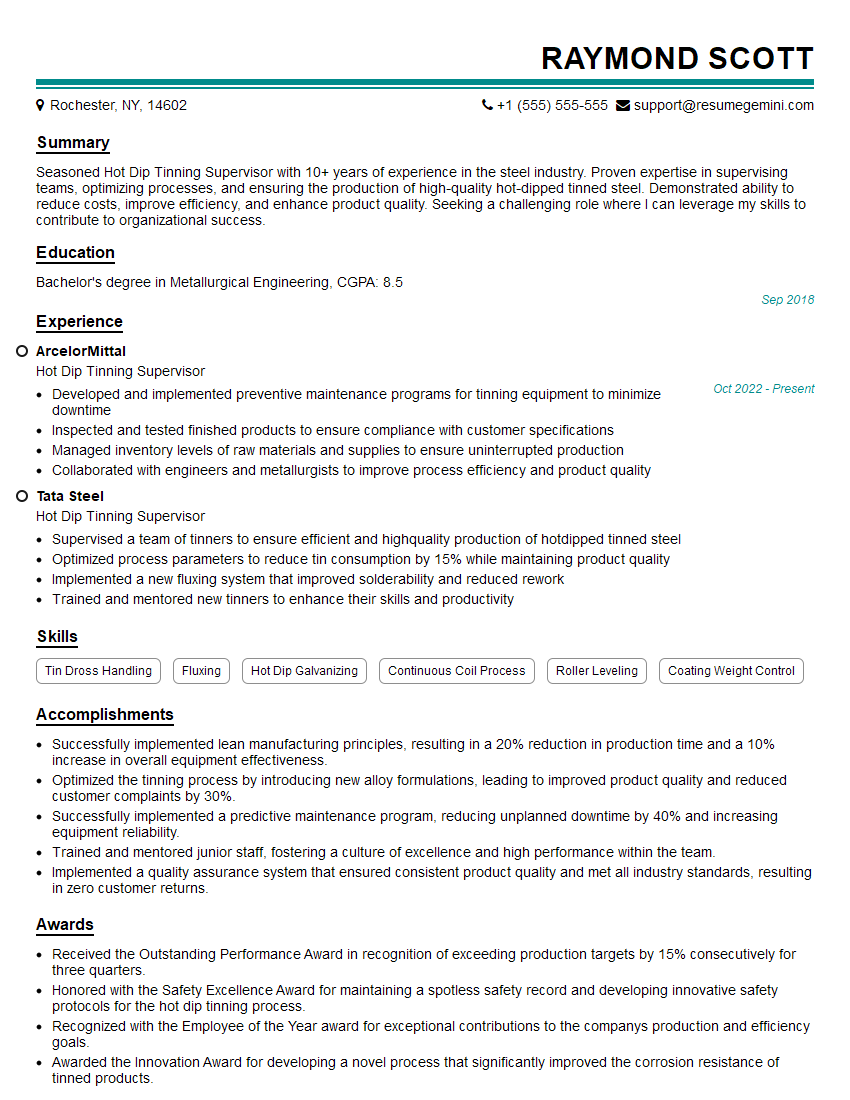