Feeling lost in a sea of interview questions? Landed that dream interview for Manufacturing Group Leader but worried you might not have the answers? You’re not alone! This blog is your guide for interview success. We’ll break down the most common Manufacturing Group Leader interview questions, providing insightful answers and tips to leave a lasting impression. Plus, we’ll delve into the key responsibilities of this exciting role, so you can walk into your interview feeling confident and prepared.
Acing the interview is crucial, but landing one requires a compelling resume that gets you noticed. Crafting a professional document that highlights your skills and experience is the first step toward interview success. ResumeGemini can help you build a standout resume that gets you called in for that dream job.
Essential Interview Questions For Manufacturing Group Leader
1. How do you ensure that the manufacturing processes are optimized and efficient?
To ensure optimized and efficient manufacturing processes, I employ a comprehensive approach that includes:
- Process Analysis: I conduct thorough assessments of existing processes to identify areas for improvement.
- Data Analysis: I leverage data and metrics to pinpoint inefficiencies and bottlenecks.
- Implementation of Lean Principles: I apply lean manufacturing techniques to eliminate waste, streamline operations, and enhance efficiency.
- Collaboration with Cross-Functional Teams: I foster collaboration with engineering, design, and other departments to optimize product design for manufacturability.
- Continuous Improvement: I establish a culture of continuous improvement by encouraging employee feedback, experimenting with new ideas, and implementing process enhancements.
2. Describe your experience in managing and motivating a manufacturing team.
- Leadership Style: I adopt a transformational leadership style, empowering my team and inspiring them to excel.
- Motivation Strategies: I utilize various motivation strategies, such as providing clear goals, recognizing achievements, and creating a positive work environment.
- Performance Management: I establish clear performance expectations and provide regular feedback to guide and support my team.
- Team Building: I foster a cohesive team environment by promoting collaboration, communication, and mutual respect.
- Skill Development: I identify and support employee development needs to enhance their capabilities and contribute to team success.
- Conflict Resolution: I proactively address conflicts and facilitate constructive discussions to resolve issues and maintain a harmonious work environment.
3. How do you handle production quality control and ensure adherence to quality standards?
- Quality Management System: I implement and maintain a robust quality management system aligned with industry standards.
- Inspection and Testing: I establish thorough inspection and testing procedures to identify and mitigate quality issues.
- Preventive Maintenance: I prioritize preventive maintenance to minimize equipment downtime and maintain optimal quality.
- Employee Training: I ensure that all team members receive comprehensive training on quality control principles and procedures.
- Continuous Improvement: I regularly review and improve quality control processes to enhance product quality and meet customer expectations.
4. How do you manage production schedules and ensure on-time delivery?
- Master Scheduling: I develop and maintain a comprehensive master schedule that aligns production activities with customer demand.
- Resource Planning: I anticipate and allocate resources effectively to avoid bottlenecks and ensure smooth production flow.
- Capacity Planning: I conduct thorough capacity planning to assess and optimize manufacturing capabilities.
- Collaboration with Suppliers: I build strong relationships with suppliers to ensure timely delivery of raw materials and components.
- Contingency Planning: I develop and implement contingency plans to mitigate potential disruptions and maintain on-time delivery.
5. Describe your experience in implementing and managing new technologies in the manufacturing process.
- Technology Assessment: I evaluate emerging technologies to identify those that align with manufacturing objectives.
- Pilot Implementation: I conduct pilot implementations to test and refine new technologies before full-scale deployment.
- Training and Support: I provide comprehensive training and support to ensure seamless adoption of new technologies by the team.
- Data Analysis: I leverage data analytics to monitor and optimize the performance of newly implemented technologies.
- Integration with Existing Systems: I ensure that new technologies are effectively integrated with existing manufacturing systems to maximize efficiency.
6. How do you measure and improve the productivity of the manufacturing process?
- Key Performance Indicators (KPIs): I establish relevant KPIs, such as output per hour, lead times, and defect rates, to measure productivity.
- Data Collection and Analysis: I collect and analyze data to identify areas for improvement.
- Process Optimization: I implement process optimization initiatives, such as reducing cycle times and eliminating waste, to enhance productivity.
- Employee Involvement: I engage team members in productivity improvement efforts to foster ownership and innovation.
- Continuous Improvement: I promote a culture of continuous improvement by regularly evaluating and refining manufacturing processes to enhance productivity.
7. How do you ensure safety and compliance in the manufacturing environment?
- Safety Protocols: I establish and implement comprehensive safety protocols to prevent accidents and ensure employee well-being.
- Risk Assessments: I conduct thorough risk assessments to identify potential hazards and develop mitigation strategies.
- Training and Education: I provide regular training and education to employees on safety procedures and compliance requirements.
- Regular Inspections: I conduct regular inspections to ensure compliance with safety regulations and identify areas for improvement.
- Emergency Preparedness: I develop and maintain emergency preparedness plans to respond effectively to incidents and minimize potential risks.
8. How do you manage inventory and ensure optimal stock levels?
- Inventory Management System: I implement an effective inventory management system to track inventory levels, optimize stock, and minimize waste.
- Demand Forecasting: I utilize demand forecasting techniques to predict future customer demand and adjust inventory levels accordingly.
- Supplier Collaboration: I establish strong relationships with suppliers to ensure timely delivery and avoid stockouts.
- Just-in-Time Inventory: I implement lean inventory practices, such as just-in-time inventory management, to reduce inventory holding costs and improve cash flow.
- Inventory Analysis: I conduct regular inventory analysis to identify slow-moving or obsolete items and optimize stock levels.
9. How do you handle customer complaints and resolve quality issues?
- Complaint Management System: I establish a structured complaint management system to effectively address customer concerns.
- Root Cause Analysis: I conduct thorough root cause analysis to identify the source of quality issues and prevent recurrence.
- Customer Communication: I maintain open and transparent communication with customers to address their concerns and provide timely updates.
- Corrective Action: I implement corrective actions to resolve quality issues and prevent customer dissatisfaction.
- Preventive Measures: I develop and implement preventive measures to minimize the likelihood of future quality issues.
10. How do you stay up-to-date with the latest manufacturing technologies and best practices?
- Industry Conferences and Events: I attend industry conferences and events to learn about emerging technologies and best practices.
- Trade Publications and Journals: I subscribe to trade publications and journals to stay informed about industry advancements.
- Continuing Education: I actively participate in continuing education programs and workshops to enhance my knowledge and skills.
- Networking: I build and maintain a network of professionals in the manufacturing industry to exchange ideas and insights.
- Vendor Collaboration: I engage with vendors and technology providers to learn about their latest offerings and advancements.
Interviewers often ask about specific skills and experiences. With ResumeGemini‘s customizable templates, you can tailor your resume to showcase the skills most relevant to the position, making a powerful first impression. Also check out Resume Template specially tailored for Manufacturing Group Leader.
Career Expert Tips:
- Ace those interviews! Prepare effectively by reviewing the Top 50 Most Common Interview Questions on ResumeGemini.
- Navigate your job search with confidence! Explore a wide range of Career Tips on ResumeGemini. Learn about common challenges and recommendations to overcome them.
- Craft the perfect resume! Master the Art of Resume Writing with ResumeGemini’s guide. Showcase your unique qualifications and achievements effectively.
- Great Savings With New Year Deals and Discounts! In 2025, boost your job search and build your dream resume with ResumeGemini’s ATS optimized templates.
Researching the company and tailoring your answers is essential. Once you have a clear understanding of the Manufacturing Group Leader‘s requirements, you can use ResumeGemini to adjust your resume to perfectly match the job description.
Key Job Responsibilities
The Manufacturing Group Leader plays a pivotal role in leading and directing a team of manufacturing professionals to achieve optimal production outputs, ensure quality standards, and drive continuous improvement initiatives.
1. Production Management
Spearheading the planning, execution, and control of production processes to optimize efficiency, minimize costs, and meet customer demands.
- Developing and implementing production schedules, allocating resources, and monitoring progress to ensure timely delivery of products.
- Identifying and resolving production bottlenecks, implementing process improvements, and optimizing resource utilization.
2. Quality Assurance
Establishing and maintaining rigorous quality control measures to ensure that products meet specifications and regulatory requirements.
- Conducting regular quality inspections, audits, and reviews to identify and address potential quality issues.
- Collaborating with design engineers and quality assurance teams to develop and implement quality management systems.
3. Team Leadership
Leading and motivating a team of manufacturing professionals to achieve shared goals and objectives.
- Providing clear direction, setting expectations, and fostering a positive and collaborative work environment.
- Mentoring and developing team members, providing training and support to enhance their skills and capabilities.
4. Continuous Improvement
Initiating and leading continuous improvement initiatives to enhance efficiency, productivity, and product quality.
- Identifying areas for improvement through data analysis, feedback collection, and industry best practices.
- Developing and implementing solutions, monitoring progress, and evaluating results to drive ongoing improvement.
Interview Tips
To ace the interview for the Manufacturing Group Leader position, consider the following tips:
1. Research the Company and Role
Thoroughly research the company, its products, and its industry to demonstrate your understanding of the business context.
- Read the company website, annual reports, and news articles to gain insights into their operations and strategy.
- Review the job description carefully to identify the key responsibilities and qualifications for the role.
2. Quantify Your Experience
Use specific metrics and data to quantify your achievements and demonstrate your impact in previous manufacturing roles.
- For example, instead of saying “I managed a team,” provide specific details such as “I led a team of 20 manufacturing professionals, resulting in a 15% increase in production output and a 20% reduction in production costs.”
- Use numbers to support your claims and show the tangible results of your work.
3. Highlight Your Leadership and Communication Skills
Emphasize your ability to lead and motivate teams, communicate effectively, and resolve conflicts.
- Provide examples of how you have successfully led teams through complex projects or challenging situations.
- Describe your approach to communication, highlighting your ability to clearly convey information, listen attentively, and build rapport with colleagues.
4. Prepare Questions for the Interviewer
Preparing thoughtful questions for the interviewer demonstrates your interest in the role and the company.
- Ask questions about the company’s manufacturing strategy, future plans, and opportunities for professional development.
- Inquire about the specific challenges and opportunities facing the manufacturing group and how you can contribute to their success.
5. Practice and Get Feedback
Practice your answers to common interview questions and get feedback from a friend, family member, or career counselor.
- This will help you refine your responses, build confidence, and reduce anxiety during the actual interview.
- Consider recording yourself to identify areas for improvement and to track your progress.
Next Step:
Armed with this knowledge, you’re now well-equipped to tackle the Manufacturing Group Leader interview with confidence. Remember, preparation is key. So, start crafting your resume, highlighting your relevant skills and experiences. Don’t be afraid to tailor your application to each specific job posting. With the right approach and a bit of practice, you’ll be well on your way to landing your dream job. Build your resume now from scratch or optimize your existing resume with ResumeGemini. Wish you luck in your career journey!
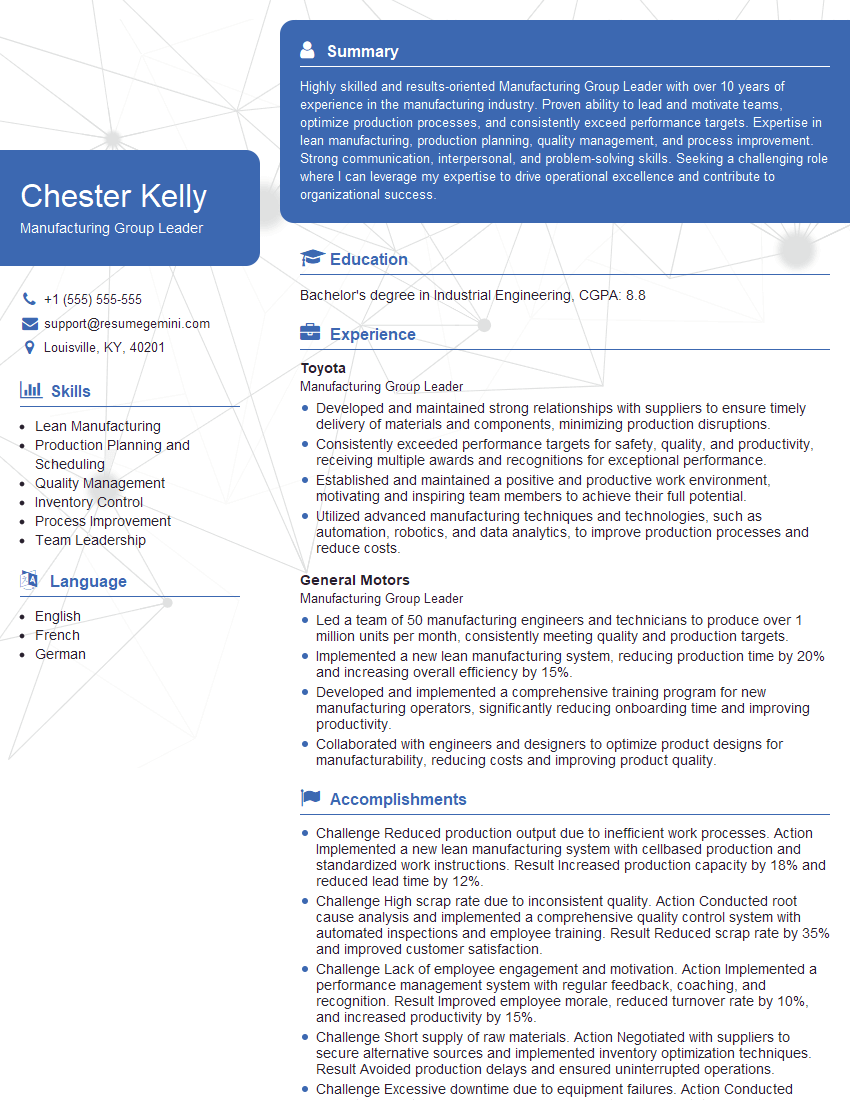