Ever felt underprepared for that crucial job interview? Or perhaps you’ve landed the interview but struggled to articulate your skills and experiences effectively? Fear not! We’ve got you covered. In this blog post, we’re diving deep into the Foundry Tender interview questions that you’re most likely to encounter. But that’s not all. We’ll also provide expert insights into the key responsibilities of a Foundry Tender so you can tailor your answers to impress potential employers.
Acing the interview is crucial, but landing one requires a compelling resume that gets you noticed. Crafting a professional document that highlights your skills and experience is the first step toward interview success. ResumeGemini can help you build a standout resume that gets you called in for that dream job.
Essential Interview Questions For Foundry Tender
1. Explain the process of preparing a mold for casting?
The process of preparing a mold for casting involves several steps:
- Pattern making: Creating a pattern or model of the desired casting using wood, metal, or plastic.
- Molding: Forming a mold cavity around the pattern using sand or other mold materials, compacted to create the desired shape.
- Pattern removal: Removing the pattern from the mold cavity, leaving behind an imprint.
- Mold finishing: Smoothing and repairing the mold cavity to ensure a good surface finish on the casting.
- Core making (if required): Creating cores to form hollow sections or internal shapes within the casting.
- Mold assembly: Joining the mold halves and securing them together to prevent molten metal leakage.
2. Describe the different types of molding processes used in foundries?
Sand casting
- Uses a sand mold to form the shape of the casting.
- Versatile process suitable for a wide range of metals and shapes.
Investment casting
- Creates a mold using a wax pattern invested in a ceramic slurry.
- Produces high-precision castings with intricate details.
Permanent mold casting
- Uses a metal mold to form the shape of the casting.
- Suitable for high-volume production of small and medium-sized castings.
Die casting
- Forces molten metal into a precision-machined die cavity.
- Produces high-quality castings with excellent dimensional accuracy.
3. What are the safety precautions that must be observed when working in a foundry?
- Wear appropriate personal protective equipment (PPE) such as gloves, safety glasses, and a foundry apron.
- Be aware of potential hazards such as molten metal, moving machinery, and falling objects.
- Handle and store molten metal with care, using proper tools and equipment.
- Maintain a clean and organized work area to minimize tripping and other accidents.
- Receive training and follow established safety procedures.
4. How do you ensure the quality of castings produced in a foundry?
- Pattern inspection: Checking the pattern for accuracy and completeness before molding.
- Mold inspection: Inspecting the mold for defects or imperfections that could affect the casting.
- Casting inspection: Examining the finished casting for dimensional accuracy, surface finish, and internal soundness.
- Destructive testing: Conducting tests such as tensile testing or radiographic inspection to assess the mechanical properties and internal structure of the casting.
- Quality control measures: Implementing statistical process control (SPC) and other quality management techniques to monitor and improve casting quality.
5. What are the common defects that can occur in castings and how can they be prevented?
- Shrinkage defects: Caused by the solidification of molten metal, leading to cavities or voids in the casting.
- Porosity: Trapped air or gas bubbles within the casting, resulting in a porous or spongy structure.
- Cold shuts: Incomplete fusion of metal at the mold interface, causing weak spots.
- Cracks: Caused by internal stresses or thermal expansion and contraction.
- Prevention strategies: Proper mold design, controlled pouring temperature, and the use of risers and chills to minimize defects.
6. Discuss the role of fluxes in the foundry process?
- Removal of impurities: Fluxes help remove oxides and other impurities from molten metal, improving its fluidity and cleanliness.
- Protection from oxidation: Fluxes cover the surface of molten metal, preventing it from oxidizing during pouring and casting.
- Enhanced fluidity: Fluxes can lower the viscosity of molten metal, allowing it to flow more easily into the mold.
- Types of fluxes: Acid fluxes (e.g., silica sand) and basic fluxes (e.g., lime) are commonly used in foundries.
7. How do you melt and control the temperature of molten metal in a foundry?
- Furnaces: Furnaces such as induction furnaces, arc furnaces, or crucible furnaces are used to melt and heat metal to the desired temperature.
- Temperature measurement: Pyrometers or thermocouples are used to measure the temperature of molten metal.
- Temperature control: Furnaces are equipped with temperature controllers and sensors to maintain the desired temperature within a specific range.
- Alloying: Alloys can be added to molten metal to modify its properties, and temperature control is crucial to ensure proper alloying.
8. Describe the different methods of pouring molten metal into a mold?
- Gravity pouring: Pouring molten metal directly into the mold using gravity as the driving force.
- Centrifugal casting: Pouring molten metal into a rotating mold, distributing it centrifugally to create a dense and uniform casting.
- Vacuum casting: Drawing molten metal into a mold under vacuum, reducing porosity and producing high-quality castings.
- Pressure casting: Pouring molten metal under pressure into a mold, resulting in dense and precise castings.
9. Explain the post-casting processes involved in finishing a casting?
- Shakeout: Removing the casting from the mold after solidification.
- Gating removal: Cutting or grinding off the gates and risers used to pour molten metal.
- Cleaning and finishing: Shot blasting, grinding, or polishing to remove any remaining mold material or imperfections.
- Heat treatment: Annealing, tempering, or quenching to enhance the mechanical properties of the casting.
- Inspection and testing: Final inspection and testing to ensure the casting meets the desired specifications.
10. Discuss the environmental regulations and safety measures related to foundry operations?
- Air pollution control: Dust and fume extraction systems to minimize air pollution.
- Wastewater treatment: Treatment facilities to manage and dispose of wastewater generated from foundry processes.
- Solid waste management: Proper disposal and recycling of spent sand, dross, and other foundry waste.
- Noise control: Measures such as enclosures or soundproofing to reduce noise levels generated by foundry equipment.
- Employee safety: Compliance with safety standards and provision of personal protective equipment (PPE).
Interviewers often ask about specific skills and experiences. With ResumeGemini‘s customizable templates, you can tailor your resume to showcase the skills most relevant to the position, making a powerful first impression. Also check out Resume Template specially tailored for Foundry Tender.
Career Expert Tips:
- Ace those interviews! Prepare effectively by reviewing the Top 50 Most Common Interview Questions on ResumeGemini.
- Navigate your job search with confidence! Explore a wide range of Career Tips on ResumeGemini. Learn about common challenges and recommendations to overcome them.
- Craft the perfect resume! Master the Art of Resume Writing with ResumeGemini’s guide. Showcase your unique qualifications and achievements effectively.
- Great Savings With New Year Deals and Discounts! In 2025, boost your job search and build your dream resume with ResumeGemini’s ATS optimized templates.
Researching the company and tailoring your answers is essential. Once you have a clear understanding of the Foundry Tender‘s requirements, you can use ResumeGemini to adjust your resume to perfectly match the job description.
Key Job Responsibilities
A Foundry Tender is responsible for running and maintaining the foundry, which is a facility where metal is melted and cast into various shapes. Some of the key job responsibilities include:Preparing and operating foundry equipment
- Setting up and operating furnaces, molding machines, and other foundry equipment.
- Adjusting and maintaining equipment to ensure optimal performance.
Melting and casting metal
- Melting metal in furnaces to the desired temperature.
- Pouring molten metal into molds to create castings.
Cleaning and finishing castings
- Removing excess metal and defects from castings.
- Polishing and finishing castings to meet customer specifications.
Maintaining a safe and clean work environment
- Ensuring that the foundry is a safe and healthy place to work.
- Cleaning up spills and debris, and disposing of hazardous materials properly.
Interview Tips
Here are some tips to help you ace your interview for a Foundry Tender position:Research the company and the position
- Visit the company’s website and learn about their products and services.
- Read the job description carefully and identify the key requirements.
Practice answering common interview questions
- Prepare for questions about your experience, skills, and qualifications.
- Be able to explain why you are interested in the position and how you can add value to the company.
Dress professionally and arrive on time for your interview
- Make a good first impression by dressing appropriately and arriving on time for your interview.
- Be polite and respectful to the interviewer, and answer their questions clearly and concisely.
Follow up after your interview
- Send a thank-you note to the interviewer within 24 hours of the interview.
- Follow up with the interviewer a week later to check on the status of your application.
Next Step:
Now that you’re armed with interview-winning answers and a deeper understanding of the Foundry Tender role, it’s time to take action! Does your resume accurately reflect your skills and experience for this position? If not, head over to ResumeGemini. Here, you’ll find all the tools and tips to craft a resume that gets noticed. Don’t let a weak resume hold you back from landing your dream job. Polish your resume, hit the “Build Your Resume” button, and watch your career take off! Remember, preparation is key, and ResumeGemini is your partner in interview success.
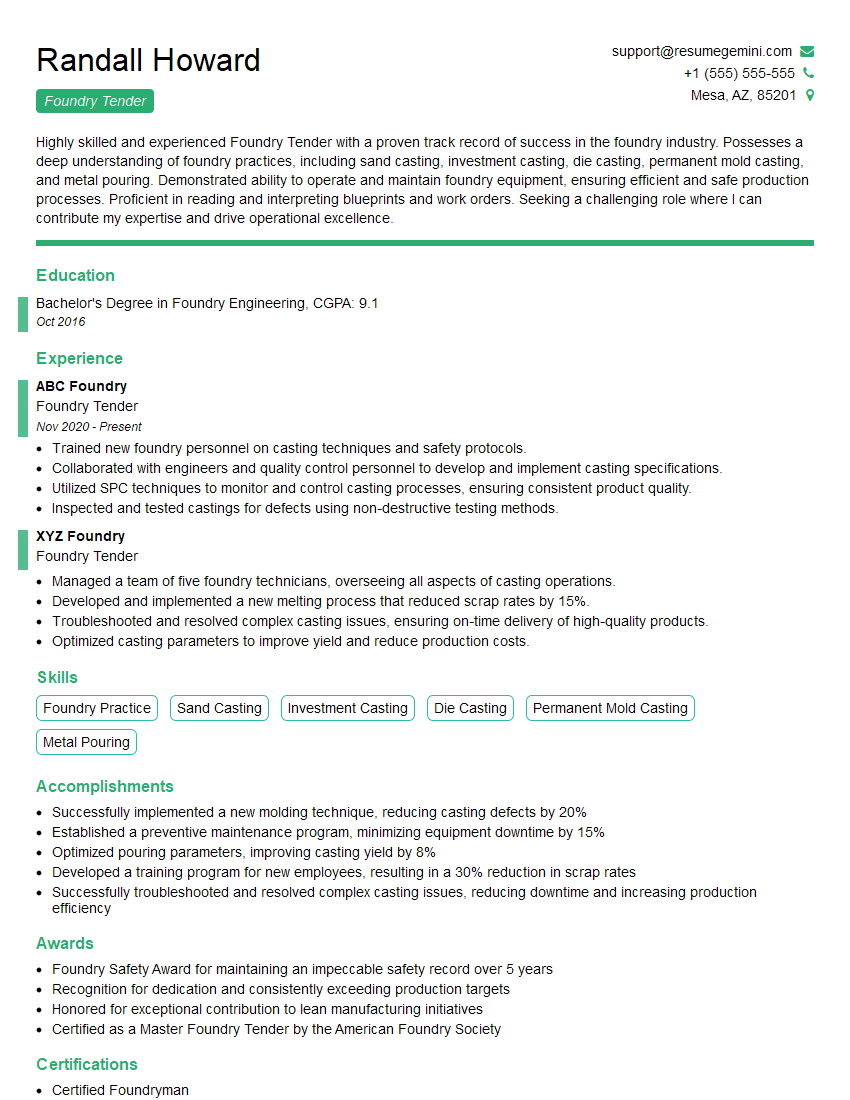