Ever felt underprepared for that crucial job interview? Or perhaps you’ve landed the interview but struggled to articulate your skills and experiences effectively? Fear not! We’ve got you covered. In this blog post, we’re diving deep into the Tube Coater interview questions that you’re most likely to encounter. But that’s not all. We’ll also provide expert insights into the key responsibilities of a Tube Coater so you can tailor your answers to impress potential employers.
Acing the interview is crucial, but landing one requires a compelling resume that gets you noticed. Crafting a professional document that highlights your skills and experience is the first step toward interview success. ResumeGemini can help you build a standout resume that gets you called in for that dream job.
Essential Interview Questions For Tube Coater
1. What are the different types of tube coating materials and their applications?
The different types of tube coating materials include:
- Epoxy: Provides excellent chemical and abrasion resistance, making it suitable for harsh environments.
- Polyurethane: Offers high flexibility and wear resistance, ideal for applications with vibration and movement.
- FBE (Fusion Bonded Epoxy): A powder coating that adheres strongly to metal surfaces, providing excellent corrosion protection.
- PE (Polyethylene): A thermoplastic material that offers insulation and resistance to moisture and chemicals.
2. Describe the process of applying a coating to a tube using an electrostatic spray system.
Pre-Treatment:
- Cleaning and degreasing the tube surface to remove contaminants.
- Abrasive blasting or chemical etching to create a rough surface for better adhesion.
Coating Application:
- The coating material is electrically charged and sprayed onto the tube using a spray gun.
- The charged particles are attracted to the tube surface, ensuring uniform coverage.
Curing:
- The coated tube is baked in an oven to cure the coating, creating a strong and durable finish.
3. What are the factors that affect the thickness of a coating applied using a dip coating method?
- Viscosity of the coating: Thicker coatings are obtained with higher viscosities.
- Withdrawal speed: Slower withdrawal speeds result in thicker coatings.
- Temperature of the coating and substrate: Higher temperatures generally lead to thinner coatings.
- Surface tension of the coating: Coatings with lower surface tension produce thinner films.
4. How do you ensure the quality and consistency of coatings applied on tubes?
- Standard Operating Procedures (SOPs): Establish clear and detailed instructions for all coating processes.
- Quality Control Measures: Implement inspections before, during, and after coating to check for defects.
- Calibration and Maintenance: Ensure equipment is regularly calibrated and maintained to operate accurately.
- Operator Training: Provide thorough training to operators on proper coating techniques and quality standards.
5. What are the challenges associated with coating small-diameter tubes?
- Uniform Coverage: Ensuring complete and even coating on small surfaces.
- Adhesion: Maintaining strong adhesion between the coating and the tube, especially on curved surfaces.
- Curing: Achieving proper curing of coatings on small-diameter tubes without overheating or damaging them.
6. Describe the different methods used for drying coatings on tubes.
- Air Drying: Exposing coated tubes to ambient air for evaporation of solvents.
- Oven Drying: Baking coated tubes in an oven at a controlled temperature to accelerate curing.
- Infrared Drying: Using infrared radiation to heat and cure coatings rapidly.
7. What are the common defects encountered in tube coating and how can they be prevented?
- Pinholing: Small holes in the coating, preventable by ensuring proper surface cleaning and avoiding over-spraying.
- Blistering: Bubbles in the coating, caused by moisture or trapped air, preventable by proper pre-treatment and drying.
- Wrinkling: Uneven or wrinkled coating, caused by applying too thick of a layer, preventable by controlling coating thickness.
8. How do you determine the appropriate coating thickness for a specific application?
- Environmental Conditions: Consider the corrosive environment and protection required.
- Tube Material: Different metals require different coating thicknesses for optimal protection.
- Application Standards: Refer to industry standards or manufacturer’s recommendations.
- Coating Type: Different coatings have different thickness ranges and properties.
9. What are the safety precautions to be taken when working with tube coating materials?
- Proper Ventilation: Ensure adequate ventilation to avoid inhalation of fumes.
- Personal Protective Equipment (PPE): Wear appropriate gloves, respirators, and protective clothing.
- Spill Containment: Have spill kits readily available to contain and clean up any spills.
- Training: Provide workers with comprehensive training on handling and safety procedures.
10. Describe the importance of surface preparation before tube coating.
- Removes Contaminants: Cleaning and degreasing eliminate dirt, oil, and other substances that can interfere with adhesion.
- Enhances Adhesion: Abrasive blasting or chemical etching creates a rougher surface, providing a stronger bond for the coating.
- Promotes Uniform Coverage: Proper surface preparation ensures the coating adheres evenly and covers the entire surface.
Interviewers often ask about specific skills and experiences. With ResumeGemini‘s customizable templates, you can tailor your resume to showcase the skills most relevant to the position, making a powerful first impression. Also check out Resume Template specially tailored for Tube Coater.
Career Expert Tips:
- Ace those interviews! Prepare effectively by reviewing the Top 50 Most Common Interview Questions on ResumeGemini.
- Navigate your job search with confidence! Explore a wide range of Career Tips on ResumeGemini. Learn about common challenges and recommendations to overcome them.
- Craft the perfect resume! Master the Art of Resume Writing with ResumeGemini’s guide. Showcase your unique qualifications and achievements effectively.
- Great Savings With New Year Deals and Discounts! In 2025, boost your job search and build your dream resume with ResumeGemini’s ATS optimized templates.
Researching the company and tailoring your answers is essential. Once you have a clear understanding of the Tube Coater‘s requirements, you can use ResumeGemini to adjust your resume to perfectly match the job description.
Key Job Responsibilities of a Tube Coater
Tube Coaters are responsible for applying a protective coating to the interior and exterior surfaces of tubes. This coating helps to prevent corrosion, wear, and other damage to the tubes. The key job responsibilities of a Tube Coater include:
1. Preparing Tubes for Coating
This involves cleaning the tubes to remove any dirt, grease, or other contaminants. The tubes may also need to be sanded or blasted to create a rough surface that will help the coating to adhere.
2. Applying the Coating
This can be done using a variety of methods, including dipping, spraying, or brushing. The coating is typically applied in multiple layers to ensure complete coverage.
3. Inspecting the Coating
Once the coating has been applied, it must be inspected to ensure that it meets the required specifications. This may involve checking the coating for thickness, smoothness, and adhesion.
4. Troubleshooting
If any problems are found with the coating, the Tube Coater must be able to troubleshoot and correct the issue. This may involve adjusting the coating process or replacing the coating material.
Interview Tips for Tube Coaters
To ace an interview for a Tube Coater position, it is important to be prepared to answer questions about your experience, skills, and knowledge. Here are some tips:
1. Research the Company
Before the interview, take some time to research the company you are applying to. This will help you to understand their business, their values, and their culture. This will also help you to tailor your answers to the specific needs of the company.
2. Practice Answering Common Interview Questions
There are some common interview questions that you are likely to be asked, such as “Tell me about yourself” and “Why are you interested in this position?” It is helpful to practice answering these questions in advance so that you can deliver your answers confidently and concisely.
3. Be Prepared to Discuss Your Experience
The interviewer will want to know about your experience as a Tube Coater. Be prepared to discuss your responsibilities, your accomplishments, and the challenges you have faced.
4. Highlight Your Skills and Knowledge
In addition to your experience, the interviewer will also want to know about your skills and knowledge. Be sure to highlight your skills in tube coating, as well as any other relevant skills, such as problem-solving, troubleshooting, and quality control.
5. Be Enthusiastic and Positive
Attire bright and lively. Employers want a candidate who is enthusiastic about the job. Be positive and upbeat throughout the interview. This will make a good impression on the interviewer and show that you are interested in the position.
Next Step:
Armed with this knowledge, you’re now well-equipped to tackle the Tube Coater interview with confidence. Remember, preparation is key. So, start crafting your resume, highlighting your relevant skills and experiences. Don’t be afraid to tailor your application to each specific job posting. With the right approach and a bit of practice, you’ll be well on your way to landing your dream job. Build your resume now from scratch or optimize your existing resume with ResumeGemini. Wish you luck in your career journey!
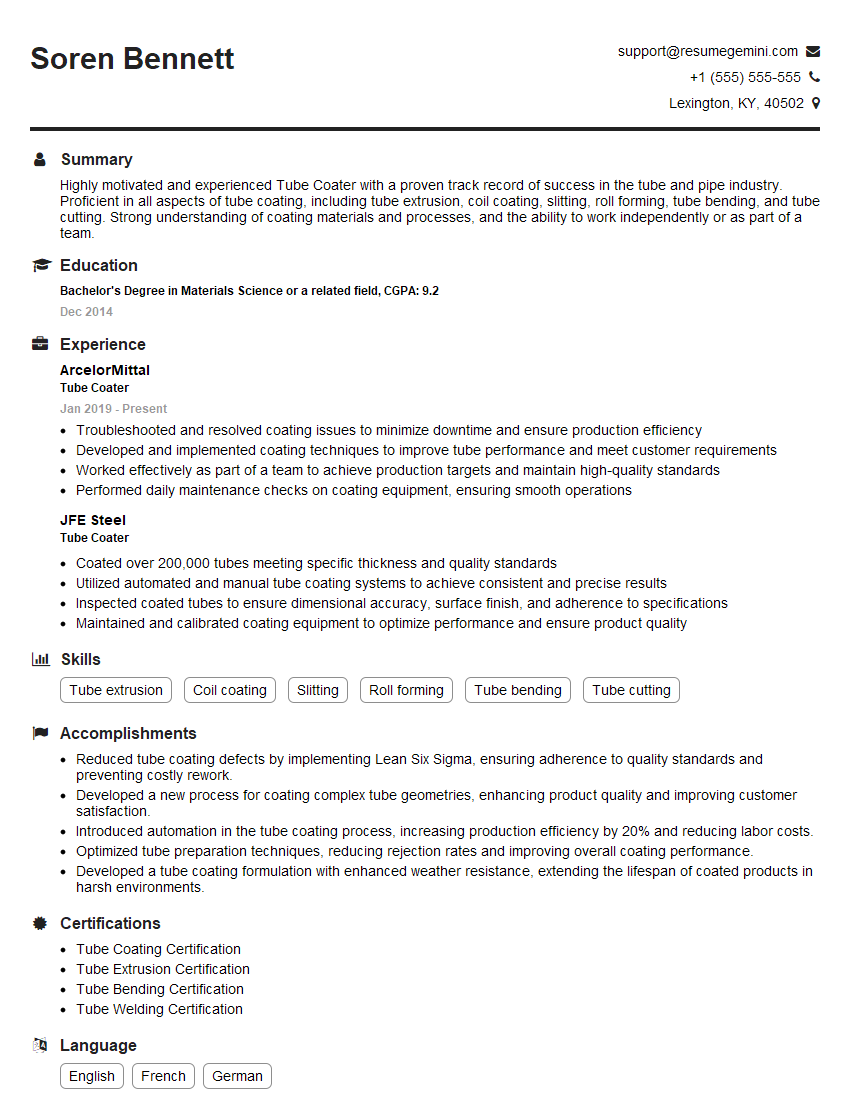