Feeling lost in a sea of interview questions? Landed that dream interview for Tubular Riveter but worried you might not have the answers? You’re not alone! This blog is your guide for interview success. We’ll break down the most common Tubular Riveter interview questions, providing insightful answers and tips to leave a lasting impression. Plus, we’ll delve into the key responsibilities of this exciting role, so you can walk into your interview feeling confident and prepared.
Acing the interview is crucial, but landing one requires a compelling resume that gets you noticed. Crafting a professional document that highlights your skills and experience is the first step toward interview success. ResumeGemini can help you build a standout resume that gets you called in for that dream job.
Essential Interview Questions For Tubular Riveter
1. Explain the process of installing a tubular rivet?
- Prepare the hole: Ensure the hole is clean, free of burrs, and the correct diameter for the rivet.
- Insert the rivet: Place the rivet into the hole, ensuring the flanged end is facing the desired side.
- Set the rivet: Use a rivet gun or pneumatic hammer to apply force to the rivet head, expanding the shank within the hole.
- Form the head: Continue applying force until the head is fully formed, creating a tight and secure joint.
- Inspect the joint: Visually check the joint to ensure the rivet is properly installed, the head is formed correctly, and there is no damage to the surrounding material.
2. What factors should be considered when selecting a tubular rivet?
Durability and Strength:
- Material: Choose a rivet material that can withstand the expected loads and environmental conditions.
- Diameter and Length: Select a rivet with a diameter and length appropriate for the thickness of the materials being joined.
Head Style:
- Flat Head: Provides a flush finish, suitable for applications where aesthetics or space constraints are important.
- Domed Head: Offers increased strength, suitable for high-stress applications.
- Countersunk Head: Sits below the surface of the material, providing a seamless finish.
Material Compatibility:
- Ensure compatibility between the rivet material and the materials being joined to avoid galvanic corrosion.
- Consider using dissimilar materials to prevent dissimilar metal corrosion.
3. Describe the different types of tubular rivet setting tools?
- Manual Rivet Gun: A handheld tool that requires manual force to squeeze the handles and set the rivet.
- Pneumatic Rivet Gun: Powered by compressed air, allowing for faster and more consistent riveting.
- Hydraulic Rivet Gun: Uses hydraulic pressure to set rivets, providing high force for heavy-duty applications.
- Automatic Riveting Machine: Automated machines that can set rivets at high speeds, suitable for large-scale production.
4. What safety precautions should be taken when working with tubular rivets?
- Wear appropriate safety gear: Safety glasses, gloves, and hearing protection.
- Securely clamp the materials: Ensure the materials are held firmly in place to prevent movement during riveting.
- Inspect the rivet gun: Regularly check the rivet gun for proper functioning and any signs of damage.
- Use the correct rivet size: Avoid using rivets that are too large or too small for the hole.
- Dispose of rivets properly: Discard used rivets in designated containers to prevent injuries.
5. Explain the advantages of using tubular rivets over other types of fasteners?
- High Strength: Tubular rivets provide strong and permanent joints, capable of withstanding significant loads.
- Wide Material Compatibility: Tubular rivets can be used with various materials, including metals, plastics, and composites.
- Versatility: Available in different sizes, materials, and head styles, allowing for customization according to specific application requirements.
- Low Cost: Tubular rivets are a cost-effective solution compared to other types of fasteners.
- Ease of Installation: Tubular rivets can be installed quickly and easily with minimal specialized equipment.
6. What are the common materials used for tubular rivets?
- Aluminum: Lightweight and corrosion-resistant, suitable for general-purpose applications.
- Steel: Strong and durable, used in high-load applications.
- Stainless Steel: Resistant to corrosion and oxidation, ideal for harsh environments.
- Copper: Provides good electrical conductivity, used in electrical applications.
- Brass: Durable and corrosion-resistant, used in marine and decorative applications.
7. Describe the different head styles of tubular rivets?
- Flat Head: Flush finish, suitable for aesthetic applications.
- Domed Head: Increased strength, used in high-stress applications.
- Countersunk Head: Sits below the surface, providing a seamless finish.
- Large Flange Head: Provides a wider bearing surface, used in thin materials.
- Peel Head: Can be bent or peeled over, used for sealing or tamper-proofing.
8. What are the key factors to consider when designing a riveted joint?
- Load Requirements: Determine the loads that the joint will be subjected to.
- Material Thickness: Ensure the rivet diameter and length are appropriate for the thickness of the materials being joined.
- Hole Size: Select a hole size that allows for proper expansion of the rivet shank.
- Spacing and Pitch: Determine the optimal spacing and pitch of the rivets to achieve desired strength and load distribution.
- Accessibility: Consider the accessibility of the joint for riveting.
9. Explain the process of quality control for tubular riveting?
- Visual Inspection: Check for proper rivet head formation, flushness, and absence of cracks or defects.
- Pull Test: Apply force to the rivet head to test the strength of the joint.
- Dimensional Verification: Measure the rivet diameter, length, and head dimensions to ensure conformance to specifications.
- Non-Destructive Testing: Use techniques like ultrasonic or X-ray inspection to detect internal defects or voids.
- Statistical Process Control: Monitor and analyze process parameters to identify areas for improvement and maintain consistent quality.
10. Describe the role of adhesives in tubular riveting?
- Enhanced Strength: Adhesives can supplement the mechanical strength of the rivet joint, providing additional load-bearing capacity.
- Improved Vibration Resistance: Adhesives can dampen vibrations and prevent loosening of the rivet joint over time.
- Sealing: Adhesives can seal the joint, preventing the ingress of moisture and contaminants.
- Stress Distribution: Adhesives can distribute stresses more evenly, reducing the risk of fatigue failure.
- Enhanced Corrosion Resistance: Adhesives can act as a barrier, protecting the rivet and surrounding materials from corrosion.
Interviewers often ask about specific skills and experiences. With ResumeGemini‘s customizable templates, you can tailor your resume to showcase the skills most relevant to the position, making a powerful first impression. Also check out Resume Template specially tailored for Tubular Riveter.
Career Expert Tips:
- Ace those interviews! Prepare effectively by reviewing the Top 50 Most Common Interview Questions on ResumeGemini.
- Navigate your job search with confidence! Explore a wide range of Career Tips on ResumeGemini. Learn about common challenges and recommendations to overcome them.
- Craft the perfect resume! Master the Art of Resume Writing with ResumeGemini’s guide. Showcase your unique qualifications and achievements effectively.
- Great Savings With New Year Deals and Discounts! In 2025, boost your job search and build your dream resume with ResumeGemini’s ATS optimized templates.
Researching the company and tailoring your answers is essential. Once you have a clear understanding of the Tubular Riveter‘s requirements, you can use ResumeGemini to adjust your resume to perfectly match the job description.
Key Job Responsibilities
Tubular Riveters are responsible for assembling and joining metal components using tubular rivets. They operate specialized riveting machines to insert and set tubular rivets, ensuring secure and durable connections. Key job responsibilities include:
1. Preparing Materials
Gathering and preparing metal components, tubular rivets, and necessary tools for riveting operations.
- Verifying component dimensions and rivet specifications.
- Selecting and installing appropriate dies and tooling into the riveting machine.
2. Operating Riveting Machine
Setting up and operating riveting machines to insert and set tubular rivets accurately.
- Positioning components and inserting rivets into designated holes.
- Applying pressure to set rivets, ensuring proper deformation and secure joints.
- Adjusting machine settings and troubleshooting minor operational issues.
3. Inspecting Joints
Assessing the quality of riveted joints to ensure they meet specifications and standards.
- Visually inspecting joints for proper rivet deformation and alignment.
- Conducting pull tests or other non-destructive tests to verify joint strength.
- Documenting inspection results and reporting any defects or non-conformances.
4. Maintaining Equipment
Keeping riveting machines and tooling in good working condition to optimize performance.
- Performing routine maintenance tasks such as cleaning, lubrication, and calibration.
- Identifying and reporting major repairs or equipment upgrades.
- Following established safety protocols and using proper personal protective equipment (PPE).
Interview Tips
To ace the interview for a Tubular Riveter position, consider the following preparation tips:
1. Research the Industry and Company
Demonstrate your understanding of the industry, company, and specific job requirements. Research the company’s products, services, and market position. Learn about the company’s culture and values, as well as the specific role you are applying for.
2. Highlight Relevant Experience and Skills
Emphasize your experience in operating riveting machines, setting tubular rivets, and inspecting joints. Provide specific examples of your work history and quantify your accomplishments whenever possible. Highlight any certifications or training you have received in riveting techniques.
3. Practice Common Interview Questions
Prepare for common interview questions by practicing your responses. Anticipate questions about your experience, skills, and motivation. Consider the STAR method (Situation, Task, Action, Result) to structure your answers and provide concrete examples.
4. Ask Thoughtful Questions
Asking informed questions at the end of the interview shows genuine interest in the position and company. Prepare questions about the company’s growth plans, safety protocols, or opportunities for professional development. This demonstrates your enthusiasm and engagement.
Next Step:
Now that you’re armed with the knowledge of Tubular Riveter interview questions and responsibilities, it’s time to take the next step. Build or refine your resume to highlight your skills and experiences that align with this role. Don’t be afraid to tailor your resume to each specific job application. Finally, start applying for Tubular Riveter positions with confidence. Remember, preparation is key, and with the right approach, you’ll be well on your way to landing your dream job. Build an amazing resume with ResumeGemini
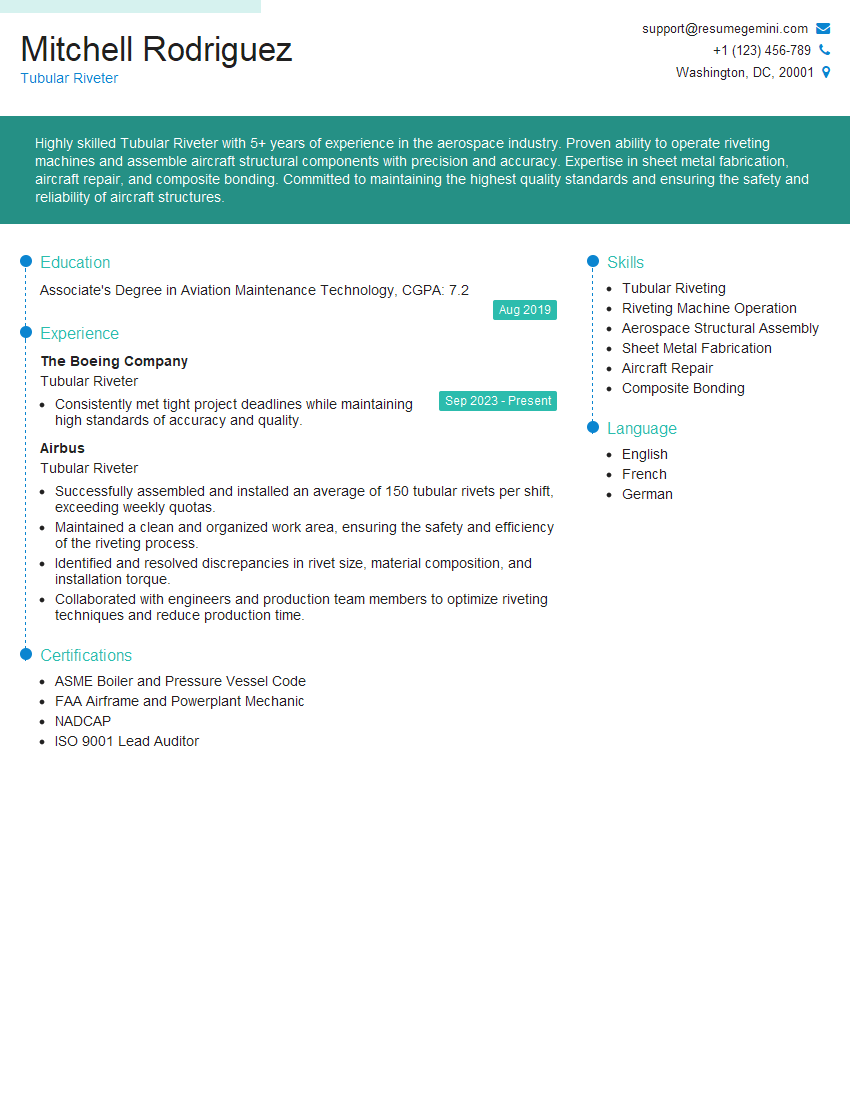