Are you gearing up for a career in Assembly Line Supervisor? Feeling nervous about the interview questions that might come your way? Don’t worry, you’re in the right place. In this blog post, we’ll dive deep into the most common interview questions for Assembly Line Supervisor and provide you with expert-backed answers. We’ll also explore the key responsibilities of this role so you can tailor your responses to showcase your perfect fit.
Acing the interview is crucial, but landing one requires a compelling resume that gets you noticed. Crafting a professional document that highlights your skills and experience is the first step toward interview success. ResumeGemini can help you build a standout resume that gets you called in for that dream job.
Essential Interview Questions For Assembly Line Supervisor
1. Describe the key responsibilities of an Assembly Line Supervisor?
As an Assembly Line Supervisor, my primary responsibilities include:
- Supervising and managing a team of assembly line operators
- Ensuring that all production goals are met
- Monitoring product quality and identifying areas for improvement
- Training and developing new employees
- Working with other departments to coordinate production
- Enforcing safety regulations and ensuring a safe work environment
2. How would you improve efficiency and productivity on an assembly line?
Kaizen and Lean Manufacturing Principles
- Implement Kaizen and Lean manufacturing principles to identify and eliminate waste
- Conduct regular time and motion studies to optimize work processes
- Provide continuous training to operators to enhance their skills
Automation and Technology
- Explore automation opportunities to streamline tasks and reduce labor costs
- Implement technology such as real-time data collection and analysis to monitor performance and make informed decisions
Cross-Training and Collaboration
- Cross-train employees to increase flexibility and coverage
- Promote collaboration between operators and supervisors to foster a sense of ownership and responsibility
3. How would you handle a situation where multiple operators are not meeting production targets?
When faced with such a situation, I would take the following steps:
- Identify the root cause: Conduct observations and gather data to determine the reasons behind the underperformance.
- Communicate with operators: Discuss the issue openly with the affected operators, seeking their input and feedback.
- Provide support and training: Offer additional training, coaching, or resources to help operators improve their skills and knowledge.
- Set achievable goals: Collaborate with operators to establish realistic and achievable production targets.
- Monitor progress and provide feedback: Track performance regularly and provide constructive feedback to motivate operators and encourage improvement.
4. What techniques do you use to ensure product quality?
To maintain product quality, I employ the following techniques:
- Establishing clear quality standards: Collaborate with quality control department to define and communicate quality expectations.
- Regular inspections: Conduct routine inspections at various stages of production to identify and address potential defects.
- Statistical process control: Use statistical tools and techniques to monitor production processes and identify areas for improvement.
- Employee training: Provide comprehensive training to operators on quality standards and best practices.
- Continuous improvement: Implement quality improvement programs to identify and eliminate root causes of defects.
5. How do you maintain a safe and healthy work environment on the assembly line?
Ensuring a safe and healthy work environment is of utmost importance to me. I take the following measures:
- Enforcing safety regulations: Establish clear safety guidelines and ensure adherence to all applicable regulations.
- Training and awareness: Provide comprehensive safety training to employees and conduct regular safety drills.
- Hazard identification and risk assessment: Regularly identify potential hazards and implement measures to mitigate risks.
- Ergonomic considerations: Evaluate workstations and tasks to ensure they are ergonomically designed to prevent injuries.
- Emergency preparedness: Develop and implement emergency response plans and train employees on evacuation procedures.
6. How do you manage multiple projects and priorities on the assembly line?
To effectively manage multiple projects and priorities, I follow these strategies:
- Prioritization: Determine the most critical projects and tasks and assign them appropriate priority.
- Effective planning: Create realistic timelines and schedules, considering dependencies and resource availability.
- Delegation: Delegate tasks to competent team members, providing clear instructions and support.
- Regular monitoring: Track project progress regularly, identify potential roadblocks, and take corrective actions as needed.
- Communication: Keep stakeholders informed about project status, challenges, and any changes in priorities.
7. How do you motivate and engage your team to achieve high performance?
Motivating and engaging my team to achieve high performance is essential. I utilize the following approaches:
- Recognition and rewards: Acknowledge and reward employees for their contributions and successes.
- Empowerment: Provide employees with autonomy and decision-making authority within their roles.
- Feedback and coaching: Offer regular feedback to employees, focusing on both strengths and areas for improvement.
- Team building: Foster a collaborative and supportive work environment through team-building activities.
- Communication: Keep employees informed about company goals, progress, and any changes that may impact their work.
8. How do you handle conflicts or disagreements among team members?
When conflicts or disagreements arise among team members, I take the following steps:
- Facilitate open communication: Encourage team members to express their perspectives and concerns in a respectful manner.
- Identify the root cause: Explore the underlying causes of the conflict and avoid focusing solely on symptoms.
- Find mutually acceptable solutions: Collaborate with team members to find solutions that address the concerns of all parties involved.
- Set clear expectations: Establish clear guidelines and expectations regarding behavior and conflict resolution.
- Follow up and monitor: Check in with team members after conflicts are resolved to ensure that solutions are working effectively.
9. How do you stay up-to-date with the latest technologies and best practices in assembly line management?
- Attend industry conferences and workshops.
- Read trade publications and online resources.
- Network with other professionals in the field.
- Take online courses and certifications.
- Implement pilot programs to test new technologies and approaches.
10. Why are you interested in this Assembly Line Supervisor position?
I am eager to join your organization as an Assembly Line Supervisor because I am confident that my skills and experience would be a valuable asset to your team. I am passionate about manufacturing and have a proven track record of success in improving efficiency, maintaining quality, and motivating teams. I am also a proactive and results-oriented individual with a strong commitment to safety and continuous improvement.
Interviewers often ask about specific skills and experiences. With ResumeGemini‘s customizable templates, you can tailor your resume to showcase the skills most relevant to the position, making a powerful first impression. Also check out Resume Template specially tailored for Assembly Line Supervisor.
Career Expert Tips:
- Ace those interviews! Prepare effectively by reviewing the Top 50 Most Common Interview Questions on ResumeGemini.
- Navigate your job search with confidence! Explore a wide range of Career Tips on ResumeGemini. Learn about common challenges and recommendations to overcome them.
- Craft the perfect resume! Master the Art of Resume Writing with ResumeGemini’s guide. Showcase your unique qualifications and achievements effectively.
- Great Savings With New Year Deals and Discounts! In 2025, boost your job search and build your dream resume with ResumeGemini’s ATS optimized templates.
Researching the company and tailoring your answers is essential. Once you have a clear understanding of the Assembly Line Supervisor‘s requirements, you can use ResumeGemini to adjust your resume to perfectly match the job description.
Key Job Responsibilities
An Assembly Line Supervisor is responsible for overseeing the production process on an assembly line, ensuring that products are manufactured efficiently and according to quality standards.
1. Oversee Production
Directly supervise and monitor assembly line workers to ensure they follow established procedures and safety protocols.
2. Quality Control
Inspect products to ensure they meet quality standards and specifications.
3. Production Optimization
Analyze production processes to identify inefficiencies and implement improvements to enhance productivity and reduce costs.
4. Team Management
Motivate and lead a team of assembly line workers, providing guidance and support.
Resolve conflicts and maintain a positive work environment.
Interview Tips
To excel in an Assembly Line Supervisor interview, it’s crucial to highlight your leadership abilities, technical knowledge, and experience in managing teams and optimizing production processes.
1. Research the Company and Industry
Familiarize yourself with the company’s products, industry trends, and the specific role you’re applying for.
2. Quantify Your Experience
Use specific metrics and examples to demonstrate your accomplishments in previous roles.
For instance, highlight how you improved production efficiency by implementing a new process, which resulted in a 10% increase in output.
3. Prepare for Technical Questions
Familiarize yourself with common assembly line practices, quality control measures, and production optimization techniques.
4. Demonstrate Leadership Skills
Share examples of how you have effectively motivated and led teams, managed conflict, and fostered a positive work environment.
Emphasize your ability to inspire others and achieve results through collaboration.
5. Showcase Your Attention to Detail
Highlight your strong attention to detail and commitment to ensuring product quality.
Discuss how you have implemented quality control measures and resolved production issues efficiently.
Next Step:
Now that you’re armed with a solid understanding of what it takes to succeed as a Assembly Line Supervisor, it’s time to turn that knowledge into action. Take a moment to revisit your resume, ensuring it highlights your relevant skills and experiences. Tailor it to reflect the insights you’ve gained from this blog and make it shine with your unique qualifications. Don’t wait for opportunities to come to you—start applying for Assembly Line Supervisor positions today and take the first step towards your next career milestone. Your dream job is within reach, and with a polished resume and targeted applications, you’ll be well on your way to achieving your career goals! Build your resume now with ResumeGemini.
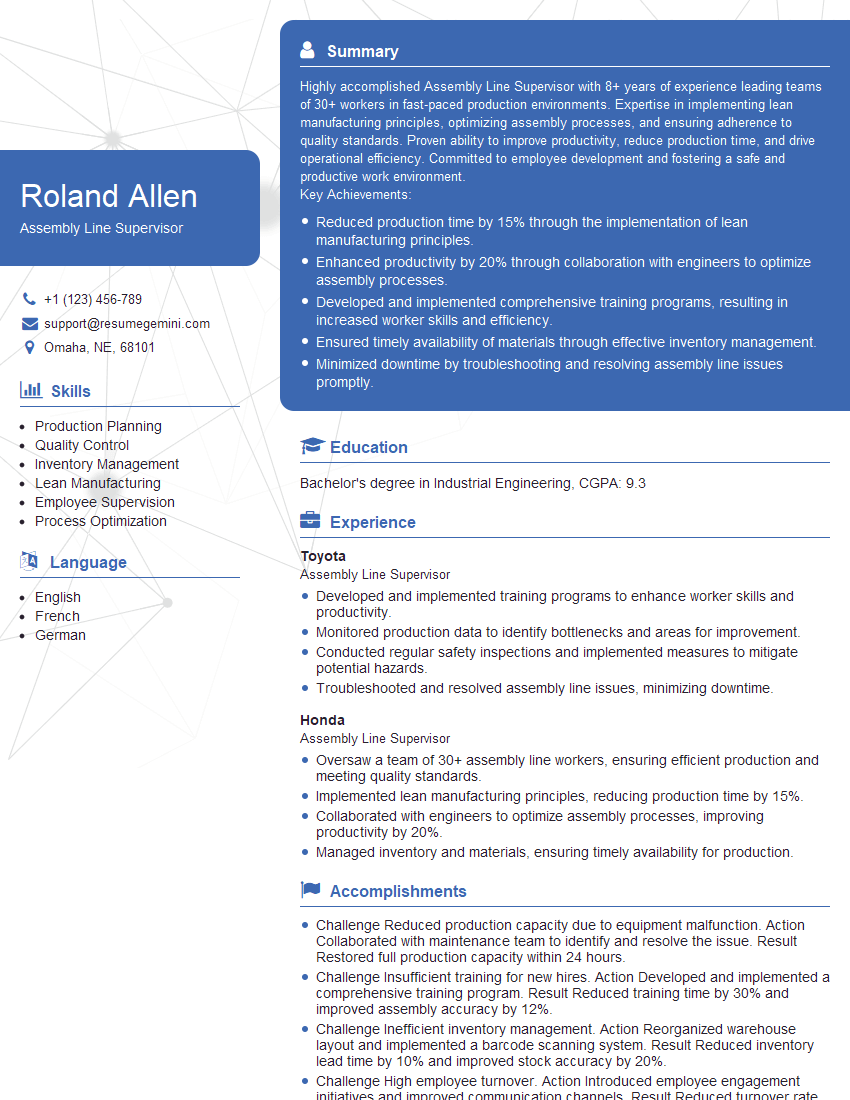