Are you gearing up for a career shift or aiming to ace your next interview? Look no further! We’ve curated a comprehensive guide to help you crack the interview for the coveted Basin Finish Operator-Tig Welder position. From understanding the key responsibilities to mastering the most commonly asked questions, this blog has you covered. So, buckle up and let’s embark on this journey together
Acing the interview is crucial, but landing one requires a compelling resume that gets you noticed. Crafting a professional document that highlights your skills and experience is the first step toward interview success. ResumeGemini can help you build a standout resume that gets you called in for that dream job.
Essential Interview Questions For Basin Finish Operator-Tig Welder
1. What is the proper way to prepare the workpiece for welding?
To properly prepare the workpiece for welding, I would:
- Inspect the workpiece for any damage or imperfections.
- Clean the workpiece thoroughly to remove any dirt, oil, or debris.
- Edge or bevel the workpiece if necessary, to create a proper joint for welding.
- Clamp or secure the workpiece in place to ensure stability during welding.
2. What are the different types of welding processes you are familiar with, which one is the best and why?
Gas Tungsten Arc Welding (GTAW)
- GTAW, also known as TIG welding, produces high-quality welds with minimal spatter and a narrow heat-affected zone.
- It is often used for welding thin metals, stainless steel, and precision components.
Gas Metal Arc Welding (GMAW)
- GMAW, also known as MIG welding, is a versatile process suitable for various metals and thicknesses.
- It offers high deposition rates and good weld penetration.
Plasma Arc Welding (PAW)
- PAW is a high-temperature welding process that uses a plasma arc to melt the metal.
- It produces clean, precise welds with minimal distortion and is commonly used in aerospace and automotive industries.
3. What are the essential characteristics of a good weld?
A good weld should possess the following characteristics:
- Penetration: The weld should penetrate deeply enough to create a strong joint.
- Fusion: The weld metal should fuse completely with the base metal.
- Strength: The weld should have sufficient strength to withstand the applied loads.
- Ductility: The weld should be ductile enough to resist cracking.
- Visual Appearance: The weld should be free of defects and have a smooth, consistent surface.
4. How do you ensure the quality of your welds?
I ensure the quality of my welds by:
- Following established welding procedures and specifications.
- Using proper welding techniques and equipment.
- Inspecting welds visually and using non-destructive testing methods.
- Continuously monitoring and adjusting welding parameters to optimize weld quality.
- Maintaining a clean and organized work area to minimize contamination.
5. What are the common defects in welding and how do you prevent them?
Porosity:
- Caused by entrapped gases in the weld metal.
- Preventable by using clean materials, shielding gases, and proper welding techniques.
Cracking:
- Caused by excessive stress or improper welding techniques.
- Preventable by preheating and post-heating the workpiece, using the correct welding parameters, and avoiding abrupt changes in direction.
Undercut:
- Caused by excessive heat input or incorrect welding angle.
- Preventable by using the correct welding parameters and maintaining a proper welding technique.
6. How do you handle complex welding tasks that require precision and accuracy?
When faced with complex welding tasks, I employ the following strategies:
- Planning and Preparation: I carefully review drawings, specifications, and procedures to fully understand the requirements.
- Equipment Selection: I choose the appropriate welding equipment and consumables based on the material, joint design, and desired outcome.
- Test Welds: I perform test welds to determine the optimal welding parameters and techniques.
- Controlled Environment: I maintain a clean and stable work environment to minimize external factors that could affect weld quality.
- Precision Measurement: I use precision measuring tools and techniques to ensure accurate joint alignment and weld dimensions.
7. What is your experience in welding different types of metals and alloys?
I have extensive experience welding various metals and alloys, including:
- Carbon Steels: Mild steel, high-strength steel, stainless steel
- Aluminum Alloys: 6061, 7075
- Nickel Alloys: Inconel, Hastelloy
- Titanium Alloys: Grade 2, Grade 5
- Copper Alloys: Copper, brass, bronze
I am familiar with the unique properties and welding characteristics of each metal, enabling me to adjust my techniques and parameters accordingly.
8. How do you stay updated on the latest welding techniques and technologies?
To stay current with the latest welding techniques and technologies, I engage in the following activities:
- Industry Events and Conferences: I attend industry events and conferences to learn about new developments and network with professionals.
- Technical Publications and Journals: I subscribe to welding journals and magazines to stay informed about the latest research and best practices.
- Online Resources and Webinars: I utilize online resources, including webinars and online forums, to access up-to-date information and connect with other welders.
- Training and Certification: I participate in additional training programs and certifications to enhance my skills and knowledge.
9. Describe your experience in troubleshooting welding problems and implementing corrective actions.
Troubleshooting welding problems and implementing corrective actions is a critical aspect of my work. Here’s how I approach this:
- Problem Identification: I carefully observe the weld and workpiece to identify any visible defects or irregularities.
- Root Cause Analysis: I analyze the welding parameters, equipment, and materials used to determine the potential cause of the problem.
- Corrective Actions: Based on my analysis, I implement appropriate corrective actions, such as adjusting welding parameters, replacing faulty equipment, or using different welding consumables.
- Verification and Documentation: I verify the effectiveness of the corrective actions by conducting test welds and documenting the results.
10. How do you ensure safety in the welding workplace?
Safety is paramount in the welding workplace. I adhere to the following practices to ensure a safe environment:
- Protective Gear: I always wear appropriate protective gear, including a welding helmet, gloves, and fire-resistant clothing.
- Workplace Ventilation: I ensure adequate ventilation to minimize exposure to welding fumes and gases.
- Fire Prevention: I keep the work area clean and free of flammable materials to prevent fires.
- Electrical Safety: I follow proper electrical safety procedures and ensure that all equipment is grounded and in good working order.
- Training and Compliance: I regularly participate in safety training and comply with all applicable safety regulations and standards.
Interviewers often ask about specific skills and experiences. With ResumeGemini‘s customizable templates, you can tailor your resume to showcase the skills most relevant to the position, making a powerful first impression. Also check out Resume Template specially tailored for Basin Finish Operator-Tig Welder.
Career Expert Tips:
- Ace those interviews! Prepare effectively by reviewing the Top 50 Most Common Interview Questions on ResumeGemini.
- Navigate your job search with confidence! Explore a wide range of Career Tips on ResumeGemini. Learn about common challenges and recommendations to overcome them.
- Craft the perfect resume! Master the Art of Resume Writing with ResumeGemini’s guide. Showcase your unique qualifications and achievements effectively.
- Great Savings With New Year Deals and Discounts! In 2025, boost your job search and build your dream resume with ResumeGemini’s ATS optimized templates.
Researching the company and tailoring your answers is essential. Once you have a clear understanding of the Basin Finish Operator-Tig Welder‘s requirements, you can use ResumeGemini to adjust your resume to perfectly match the job description.
Key Job Responsibilities
Basin Finish Operators-TIG Welders are responsible for the finishing and welding of basins in accordance with established quality standards and specifications.
1. Finishing Operations
intro paragraph
- Grind, sand, buff, and polish basin surfaces to achieve desired finish.
- Inspect finished basins for defects and ensure compliance with quality standards.
2. Welding Operations
intro paragraph
- Use TIG welding techniques to join and repair basins.
- Set up and operate welding equipment to ensure optimal performance.
3. Quality Control
intro paragraph
- Monitor welding processes to ensure adherence to specifications.
- Perform quality inspections on finished products to verify compliance with standards.
4. Maintenance and Safety
intro paragraph
- Maintain and calibrate welding equipment to ensure optimal operation.
- Adhere to safety regulations and follow established safety procedures.
Interview Tips
Preparing for an interview can significantly increase your chances of success. Here are some tips to help you ace your interview for a Basin Finish Operator-TIG Welder position:
1. Research the Company and Position
Take the time to learn about the company’s history, mission, and values. Understanding the company’s culture and the specific requirements of the position will help you tailor your answers to the interviewer’s questions.
- For example, if the company emphasizes sustainability, you could highlight your experience in eco-friendly welding practices.
- If the position requires proficiency in a particular welding technique, ensure you emphasize your skills in that area.
2. Practice Your Answers
Before the interview, take some time to practice answering common interview questions. Prepare concise, well-structured responses that highlight your relevant skills and experience.
- For instance, you could practice describing your experience with different welding methods or explaining your understanding of welding standards.
- Avoid simply memorizing answers; focus on understanding the underlying concepts and providing genuine examples from your work.
3. Showcase Your Technical Expertise
As a Basin Finish Operator-TIG Welder, technical expertise is crucial. During the interview, be prepared to discuss your proficiency in welding techniques, knowledge of welding equipment, and understanding of quality control processes.
- Consider bringing a portfolio of your work or examples of projects you have completed.
- Be ready to explain the different welding techniques you have mastered and how you ensure the quality of your work.
4. Emphasize Your Safety Mindset
Safety is paramount in the welding industry. Emphasize your commitment to following safety regulations and implementing proper welding practices.
- Share experiences where you have identified and mitigated safety risks on the job.
- Explain how you stay up-to-date with the latest safety standards and best practices.
5. Be Enthusiastic and Confident
Show your enthusiasm for the field and demonstrate your confidence in your abilities. A positive and motivated attitude can make a lasting impression on the interviewer.
- Share your passion for welding and explain why you believe you are well-suited for the role.
- Express your eagerness to learn and contribute to the company’s success.
Next Step:
Now that you’re armed with interview-winning answers and a deeper understanding of the Basin Finish Operator-Tig Welder role, it’s time to take action! Does your resume accurately reflect your skills and experience for this position? If not, head over to ResumeGemini. Here, you’ll find all the tools and tips to craft a resume that gets noticed. Don’t let a weak resume hold you back from landing your dream job. Polish your resume, hit the “Build Your Resume” button, and watch your career take off! Remember, preparation is key, and ResumeGemini is your partner in interview success.
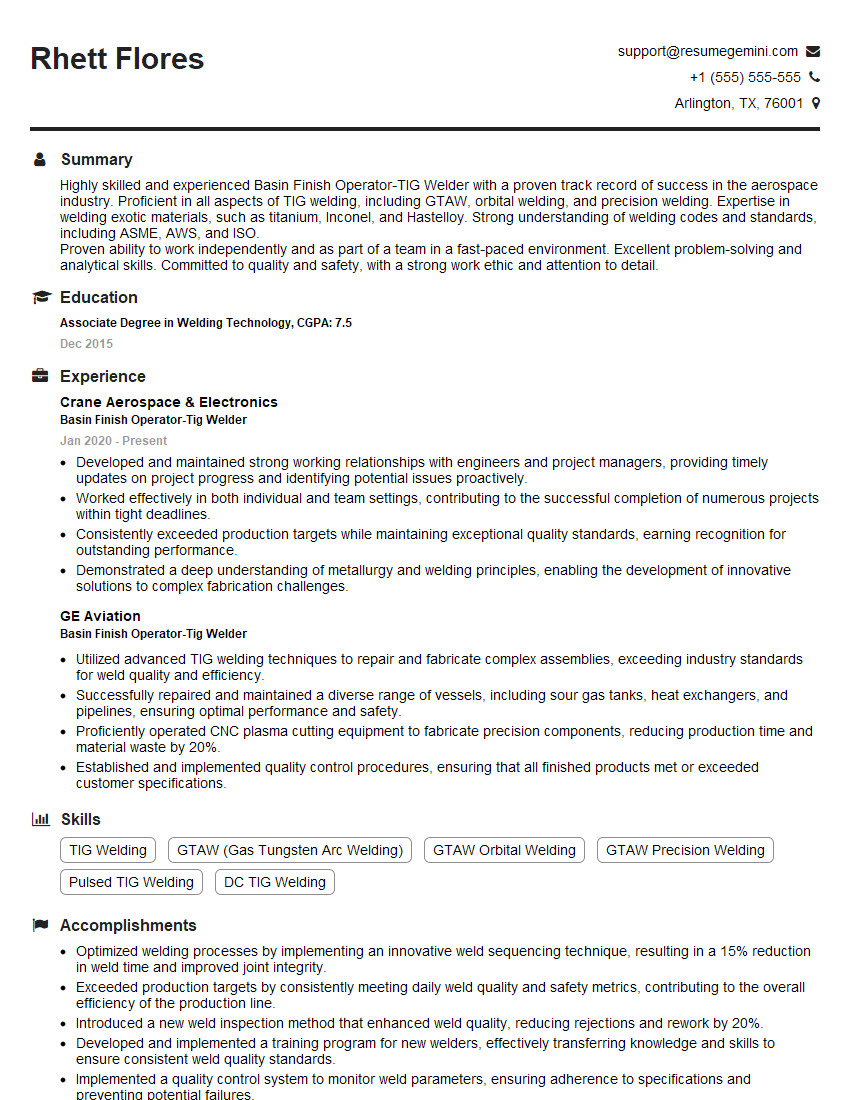