Are you gearing up for a career shift or aiming to ace your next interview? Look no further! We’ve curated a comprehensive guide to help you crack the interview for the coveted Bevel Mill Operator position. From understanding the key responsibilities to mastering the most commonly asked questions, this blog has you covered. So, buckle up and let’s embark on this journey together.
Acing the interview is crucial, but landing one requires a compelling resume that gets you noticed. Crafting a professional document that highlights your skills and experience is the first step toward interview success. ResumeGemini can help you build a standout resume that gets you called in for that dream job.
Essential Interview Questions For Bevel Mill Operator
1. Explain the different types of bevel cutting processes?
There are primarily two types of bevel cutting processes:
- Cold cutting: This method utilizes a cutting tool to shear the material, resulting in a clean and precise cut. It is often used for thinner materials and requires less force compared to hot cutting.
- Hot cutting: This method uses a high-temperature flame or plasma to melt and cut the material. It is suitable for thicker materials and can produce complex shapes. However, it can generate sparks and fumes, requiring proper ventilation.
2. What are the key factors to consider when setting up a bevel mill machine?
Material characteristics:
- Thickness and type of material
- Hardness and strength
Bevel angle requirements:
- Desired angle of the bevel
- Accuracy and tolerance required
Machine capabilities:
- Maximum beveling angle
- Spindle speed and feed rate
- Type of cutting tool used
3. How do you ensure the accuracy and precision of bevel cuts?
Accuracy and precision are critical in bevel cutting. Here are some methods to ensure them:
- Proper machine calibration: Regularly calibrate the machine to ensure its accuracy and repeatability.
- Sharp cutting tools: Use sharp and properly maintained cutting tools to achieve clean and precise cuts.
- Material fixturing: Secure the material firmly to prevent movement during cutting, which can result in inaccuracies.
- Accurate measurement and alignment: Use precision measuring tools and verify the alignment of the material and cutting tool to ensure the desired bevel angle.
- Quality control: Implement quality control measures to check the accuracy and precision of bevel cuts against specifications and standards.
4. What safety precautions should be followed when operating a bevel mill machine?
Safety is paramount when operating a bevel mill machine. Key precautions include:
- Personal protective equipment: Wear appropriate PPE, such as safety glasses, gloves, and ear protection.
- Machine guarding: Ensure all machine guards and safety devices are in place and functional.
- Proper handling of materials: Use proper lifting techniques and equipment to handle heavy materials.
- Fire safety: Have fire extinguishers readily available and follow proper fire safety protocols.
- Electrical safety: Ensure proper grounding and electrical connections to prevent electrical hazards.
5. Describe the different types of cutting tools used in bevel milling and their applications?
Bevel milling employs various cutting tools depending on the material and application:
- Face mills: These tools have multiple cutting edges and are used for roughing operations to remove large amounts of material.
- End mills: They have a single cutting edge and are suitable for precise cuts, profiling, and slotting.
- Helical mills: These tools have multiple cutting edges arranged in a helical pattern, providing a smooth surface finish and reduced cutting forces.
- Slitting saws: Thin, circular saws used for cutting grooves and slots in the material.
- Inserted tooth cutters: Tools with replaceable cutting inserts, allowing for versatility and cost-effectiveness.
6. How do you troubleshoot common problems encountered in bevel milling?
Troubleshooting common bevel milling problems is essential for efficient operation:
- Inaccurate cuts: Check machine calibration, cutting tool sharpness, material fixturing, and alignment.
- Excessive vibration: Inspect the machine for loose components, ensure the material is securely clamped, and consider using a vibration dampener.
- Poor surface finish: Use a sharper cutting tool, adjust the feed rate or spindle speed, and check for material defects.
- Tool breakage: Inspect the tool for damage, verify proper mounting, and ensure the cutting parameters are appropriate for the material.
- Electrical faults: Check for loose connections, blown fuses, or faulty electrical components.
7. What maintenance procedures are essential for a bevel mill machine?
Regular maintenance ensures optimal performance and longevity of the bevel mill machine:
- Cleaning: Remove chips, debris, and coolant from the machine to prevent accumulation and potential damage.
- Lubrication: Follow the manufacturer’s recommendations for lubrication to reduce friction and wear on moving parts.
- Spindle inspection: Periodically inspect the spindle for any signs of damage or wear, and adjust or replace as needed.
- Calibration: Regularly calibrate the machine to maintain accuracy and repeatability.
- Safety checks: Ensure all safety devices, such as guards and interlocks, are in good working condition.
8. Explain the role of coolant in bevel milling and its benefits?
Coolant plays a crucial role in bevel milling:
- Cooling: Coolant reduces heat generated during cutting, which extends tool life and improves surface finish.
- Lubrication: It lubricates the cutting tool and workpiece, reducing friction and improving tool performance.
- Chip removal: Coolant helps flush away chips from the cutting zone, preventing them from accumulating and affecting the cut quality.
- Corrosion prevention: Coolant can contain additives to prevent corrosion of the workpiece and cutting tool.
9. What factors influence the selection of spindle speed and feed rate in bevel milling?
Spindle speed and feed rate are critical parameters in bevel milling:
- Material properties: Harder materials typically require lower spindle speeds and feed rates.
- Tool type: Different cutting tools have specific recommended operating ranges.
- Desired surface finish: Higher spindle speeds and lower feed rates generally result in a better surface finish.
- Machine capabilities: The machine’s maximum spindle speed and feed rate capabilities must be considered.
- Cycle time: Adjusting spindle speed and feed rate can optimize production time and efficiency.
10. Discuss the advantages of using Computer Numerical Control (CNC) in bevel milling?
CNC technology offers several advantages in bevel milling:
- Precision and accuracy: CNC machines provide high levels of precision and accuracy, ensuring consistent and repeatable bevel cuts.
- Complex cuts: CNC machines can execute complex bevel cuts with ease, eliminating the need for manual setup and reducing production time.
- Increased productivity: Automation with CNC allows for faster production rates and reduced labor costs.
- Reduced scrap: The precision of CNC machines minimizes errors and reduces scrap rates, leading to cost savings.
- Operator safety: CNC machines automate the cutting process, reducing the risk of operator injury.
Interviewers often ask about specific skills and experiences. With ResumeGemini‘s customizable templates, you can tailor your resume to showcase the skills most relevant to the position, making a powerful first impression. Also check out Resume Template specially tailored for Bevel Mill Operator.
Career Expert Tips:
- Ace those interviews! Prepare effectively by reviewing the Top 50 Most Common Interview Questions on ResumeGemini.
- Navigate your job search with confidence! Explore a wide range of Career Tips on ResumeGemini. Learn about common challenges and recommendations to overcome them.
- Craft the perfect resume! Master the Art of Resume Writing with ResumeGemini’s guide. Showcase your unique qualifications and achievements effectively.
- Great Savings With New Year Deals and Discounts! In 2025, boost your job search and build your dream resume with ResumeGemini’s ATS optimized templates.
Researching the company and tailoring your answers is essential. Once you have a clear understanding of the Bevel Mill Operator‘s requirements, you can use ResumeGemini to adjust your resume to perfectly match the job description.
Key Job Responsibilities
Bevel Mill Operators are responsible for operating bevel milling machines to cut and shape metal workpieces. Their key responsibilities include:
1. Machine Operation
Operate bevel milling machines to cut and shape metal workpieces according to specifications.
- Set up machines with appropriate tooling and fixtures.
- Load and unload workpieces safely following safety protocols.
2. Quality Control
Inspect workpieces for accuracy and quality, ensuring they meet specifications.
- Use measuring tools and gauges to verify dimensions.
- Identify and correct any defects or inconsistencies.
3. Machine Maintenance
Perform basic maintenance and troubleshooting on bevel milling machines.
- Clean and lubricate machines regularly.
- Identify and resolve minor issues.
4. Safety Compliance
Follow all safety regulations and wear appropriate safety gear while operating machines.
- Maintain a clean and organized work area.
- Report any safety concerns or hazards immediately.
Interview Tips
Preparing for a Bevel Mill Operator interview requires a combination of technical knowledge and an understanding of the industry. Here are some tips to help you ace your interview:
1. Research the Company
Take the time to research the company you are interviewing with. This will give you a better understanding of their products, services, and culture. It will also help you tailor your answers to the specific needs of the company.
2. Practice Your Technical Skills
Be prepared to discuss your technical skills and experience in detail. The interviewer will likely ask you about your experience with bevel milling machines, as well as your knowledge of different types of metalworking techniques. Practice answering questions about your experience and how it relates to the job requirements.
3. Highlight Your Safety Knowledge
Safety is a top priority in any manufacturing environment. Be prepared to discuss your knowledge of safety regulations and your experience with following safety protocols. The interviewer will want to know that you are aware of the potential hazards associated with operating bevel milling machines and that you take safety seriously.
4. Ask Questions
Asking questions at the end of the interview shows that you are interested in the position and that you are taking the interview seriously. Prepare a few questions to ask the interviewer about the company, the position, and the industry. This will help you get a better understanding of the opportunity and will also make a good impression on the interviewer.
Next Step:
Armed with this knowledge, you’re now well-equipped to tackle the Bevel Mill Operator interview with confidence. Remember, preparation is key. So, start crafting your resume, highlighting your relevant skills and experiences. Don’t be afraid to tailor your application to each specific job posting. With the right approach and a bit of practice, you’ll be well on your way to landing your dream job. Build your resume now from scratch or optimize your existing resume with ResumeGemini. Wish you luck in your career journey!
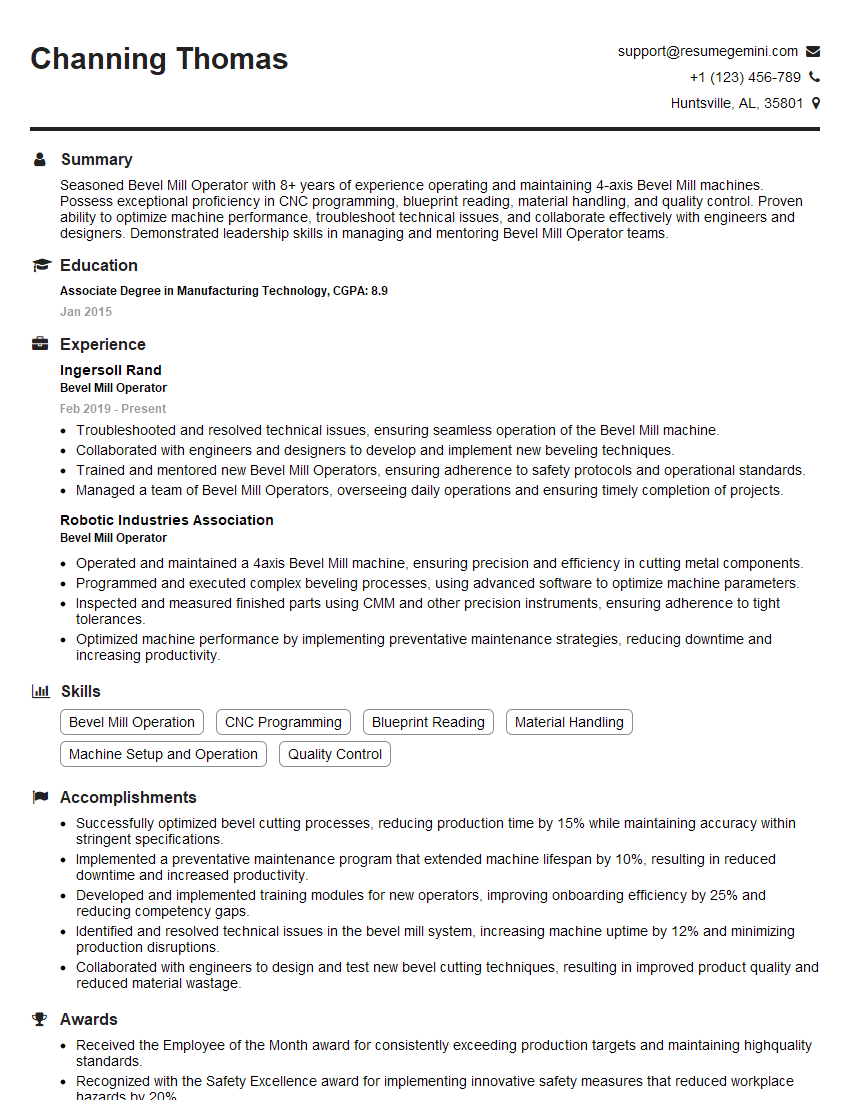