Are you gearing up for a career shift or aiming to ace your next interview? Look no further! We’ve curated a comprehensive guide to help you crack the interview for the coveted Call Box Wirer position. From understanding the key responsibilities to mastering the most commonly asked questions, this blog has you covered. So, buckle up and let’s embark on this journey together.
Acing the interview is crucial, but landing one requires a compelling resume that gets you noticed. Crafting a professional document that highlights your skills and experience is the first step toward interview success. ResumeGemini can help you build a standout resume that gets you called in for that dream job.
Essential Interview Questions For Call Box Wirer
1. Describe the process of wiring a call box?
The process of wiring a call box involves several steps to ensure proper functionality and adherence to safety regulations:
- Identify the location of the call box and determine the appropriate wiring route.
- Select the necessary wires and cables based on the call box specifications and the distance to the control panel.
- Prepare the wires by stripping the insulation and tinning the ends to prevent fraying.
- Connect the wires to the terminals on the call box according to the wiring diagram.
- Secure the wires using wire nuts or terminal blocks and insulate the connections with electrical tape.
- Run the wires through conduits or raceways to protect them from damage and maintain a neat installation.
- Terminate the wires at the control panel and connect them to the appropriate terminals.
- Test the call box thoroughly to ensure it is functioning correctly and complies with safety standards.
2. How do you troubleshoot a faulty call box?
Testing the Call Box
- Verify if the call box is receiving power by checking the indicator light or using a multimeter.
- Test the buttons to ensure they are making proper contact and sending signals.
- Inspect the wiring for any loose connections, damage, or corrosion.
Checking the Control Panel
- Examine the control panel to identify any error messages or indications.
- Review the wiring connections at the panel to ensure they are secure and match the call box wiring.
- Test the communication path between the call box and the control panel using a loop tester.
3. Explain the importance of proper grounding in call box wiring?
Proper grounding is crucial in call box wiring for several reasons:
- Safety: Grounding provides a safe path for electrical current to flow in case of a fault or surge, preventing electrical shocks and equipment damage.
- Signal Integrity: A proper ground reference ensures that the call box signals are transmitted and received correctly, minimizing noise and interference.
- Code Compliance: Electrical codes require proper grounding for call box systems to meet safety and functionality standards.
- Lightning Protection: A grounded call box system helps protect against lightning strikes by providing a path for the surge to safely dissipate.
4. How do you determine the correct wire gauge for call box wiring?
The correct wire gauge for call box wiring is determined based on several factors:
- Current Draw: Calculate the current draw of the call box and refer to wire gauge tables to determine the appropriate size.
- Distance: The length of the wire run affects the voltage drop, so larger gauge wires are used for longer distances to maintain signal strength.
- Voltage Drop: The acceptable voltage drop for call box systems is typically 5%, so wire gauge is selected to minimize voltage loss over the distance.
- Code Requirements: Electrical codes specify minimum wire gauges based on the type of insulation and installation method.
5. Describe the different types of call box enclosures?
There are several types of call box enclosures designed for various applications and environments:
- Weatherproof Enclosures: Protect the call box from rain, snow, and other outdoor elements.
- Vandal-Resistant Enclosures: Constructed with durable materials and anti-tamper features to withstand vandalism and theft.
- Flush-Mounted Enclosures: Recessed into the wall for a seamless and unobtrusive appearance.
- Surface-Mounted Enclosures: Installed on the surface of a wall or pole, providing easy access for maintenance.
- Pedestal Enclosures: Mounted on a pedestal or stand for visibility and accessibility in public areas.
6. What are the common safety considerations when working with call box wiring?
Safety is paramount when working with call box wiring:
- De-energize the System: Before starting work, ensure the call box system is powered down to prevent electrical shocks.
- Use Proper Tools: Utilize insulated tools and safety gear, such as gloves and safety glasses, to protect against electrical hazards.
- Test for Voltage: Use a voltage tester to verify that the wires are not live before touching them.
- Wear Protective Clothing: Wear appropriate clothing, including long sleeves and non-conductive footwear, to minimize the risk of injury.
- Follow Electrical Codes: Adhere to electrical codes and industry best practices to ensure safety and compliance.
7. Explain the role of a call box relay in the system?
A call box relay plays a vital role in the call box system:
- Isolation: The relay isolates the call box from the control panel, preventing feedback and ensuring signal integrity.
- Signal Amplification: The relay amplifies the signal from the call box, making it strong enough to travel over long distances.
- Multiple Call Box Support: One relay can handle signals from multiple call boxes, reducing the need for individual wiring.
- Fault Detection: The relay can detect faults in the call box wiring or the call box itself, providing early warning for maintenance.
8. How do you splice and terminate call box wires?
Splicing and terminating call box wires require careful attention to detail:
- Strip and Tin Wires: Strip the insulation from the wires and tin the ends using solder to prevent fraying and improve conductivity.
- Twist and Solder: Twist the wires together and solder them to create a secure and permanent connection.
- Insulate the Splice: Cover the soldered connection with heat shrink tubing or electrical tape to provide insulation and protection.
- Use Terminal Blocks: For multiple wire connections, use terminal blocks to provide a neat and organized termination point.
- Label the Wires: Clearly label the wires to facilitate future troubleshooting and maintenance.
9. What are the different types of call box activation mechanisms?
Call boxes utilize various activation mechanisms to initiate communication:
- Push Button: The most common type, activated by pressing a large button.
- Rotary Dial: Used in older systems, requires the user to dial a specific number.
- Touch Screen: Modern call boxes feature touch screens for user-friendly operation.
- Keypad: Similar to a telephone keypad, used for entering codes or numbers.
- Pull Cord: Found in emergency situations, activates the call box by pulling a cord.
10. How do you maintain and inspect call box systems?
Regular maintenance and inspection are crucial for optimal call box performance:
- Visual Inspection: Regularly check the call box enclosure for damage, corrosion, or vandalism.
- Button and Dial Testing: Test all buttons and dials to ensure they are functioning correctly.
- Communication Testing: Verify that the call box can communicate with the control panel and transmit signals clearly.
- Battery Replacement: Replace batteries regularly to ensure continuous operation during power outages.
- Wiring Inspection: Inspect the wiring for any damage, loose connections, or corrosion, and repair or replace as needed.
Interviewers often ask about specific skills and experiences. With ResumeGemini‘s customizable templates, you can tailor your resume to showcase the skills most relevant to the position, making a powerful first impression. Also check out Resume Template specially tailored for Call Box Wirer.
Career Expert Tips:
- Ace those interviews! Prepare effectively by reviewing the Top 50 Most Common Interview Questions on ResumeGemini.
- Navigate your job search with confidence! Explore a wide range of Career Tips on ResumeGemini. Learn about common challenges and recommendations to overcome them.
- Craft the perfect resume! Master the Art of Resume Writing with ResumeGemini’s guide. Showcase your unique qualifications and achievements effectively.
- Great Savings With New Year Deals and Discounts! In 2025, boost your job search and build your dream resume with ResumeGemini’s ATS optimized templates.
Researching the company and tailoring your answers is essential. Once you have a clear understanding of the Call Box Wirer‘s requirements, you can use ResumeGemini to adjust your resume to perfectly match the job description.
Key Job Responsibilities
Call Box Wirers are responsible for the installation, maintenance and repair of call boxes, which are used to summon help in emergency situations. They must have a strong understanding of electrical wiring and be able to work independently and as part of a team.
1. Installing Call Boxes
Call Box Wirers typically work with blueprints or schematics to determine the location of call boxes. They then install the boxes, making sure that they are securely mounted and properly wired. They also test the boxes to ensure that they are working properly.
2. Maintaining Call Boxes
Call Box Wirers perform regular maintenance on call boxes to ensure that they are in good working condition. They may inspect the boxes for damage, replace batteries, or clean contacts. They also test the boxes to make sure that they are still functioning properly.
3. Repairing Call Boxes
If a call box is damaged or malfunctioning, Call Box Wirers are responsible for repairing it. They may need to replace wires, switches, or other components. They also test the box to make sure that it is working properly after the repair.
4. Working with Others
Call Box Wirers often work with other tradespeople, such as electricians and construction workers. They may also work with law enforcement and emergency responders to ensure that call boxes are properly installed and maintained.
Interview Tips
Here are some tips for interviewing for a Call Box Wirer position:
1. Be Prepared to Answer Questions About Your Experience
Be prepared to answer questions about your experience installing, maintaining, and repairing call boxes. You should also be able to discuss your knowledge of electrical wiring and safety procedures.
2. Be Able to Demonstrate Your Skills
The interviewer may ask you to demonstrate your skills by wiring a call box or performing a repair. Be prepared to show the interviewer that you have the skills and knowledge necessary to do the job.
3. Be Professional and Courteous
Dress professionally for the interview and be polite and respectful to the interviewer. This will show the interviewer that you are serious about the job and that you are a good fit for the company.
4. Ask Questions about the Position
At the end of the interview, be sure to ask the interviewer questions about the position and the company. This will show the interviewer that you are interested in the job and that you are taking the interview seriously.
Next Step:
Armed with this knowledge, you’re now well-equipped to tackle the Call Box Wirer interview with confidence. Remember, a well-crafted resume is your first impression. Take the time to tailor your resume to highlight your relevant skills and experiences. And don’t forget to practice your answers to common interview questions. With a little preparation, you’ll be on your way to landing your dream job. So what are you waiting for? Start building your resume and start applying! Build an amazing resume with ResumeGemini.
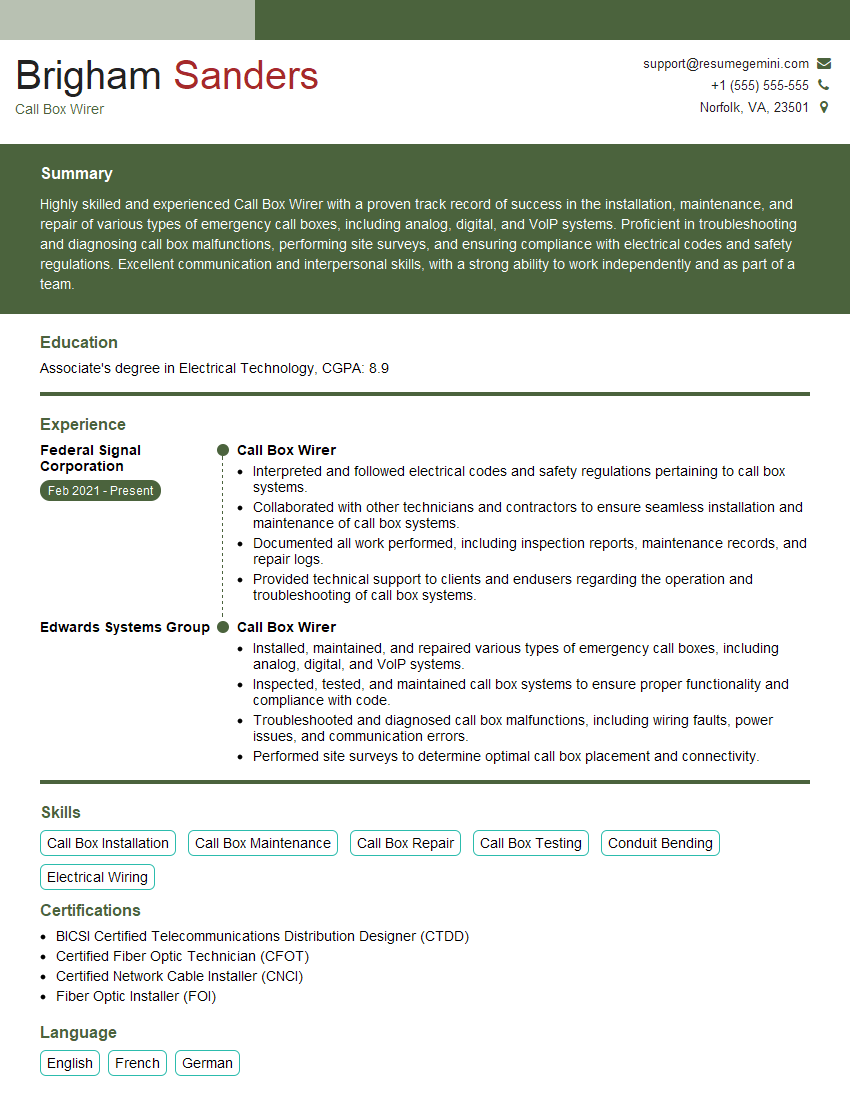