Are you gearing up for an interview for a Carding Supervisor position? Whether you’re a seasoned professional or just stepping into the role, understanding what’s expected can make all the difference. In this blog, we dive deep into the essential interview questions for Carding Supervisor and break down the key responsibilities of the role. By exploring these insights, you’ll gain a clearer picture of what employers are looking for and how you can stand out. Read on to equip yourself with the knowledge and confidence needed to ace your next interview and land your dream job!
Acing the interview is crucial, but landing one requires a compelling resume that gets you noticed. Crafting a professional document that highlights your skills and experience is the first step toward interview success. ResumeGemini can help you build a standout resume that gets you called in for that dream job.
Essential Interview Questions For Carding Supervisor
1. What are the main responsibilities of a Carding Supervisor?
As a Carding Supervisor, I will be responsible for overseeing the carding operation, ensuring that the machines are running smoothly and producing quality sliver. I will be leading a team of operators and ensuring that they are trained and supervised effectively. Additionally, I will be responsible for maintaining the carding machines, conducting regular inspections, and troubleshooting any issues that may arise.
2. What are the quality parameters for card sliver and how do you ensure they are met?
Maintaining Fiber Length
- Regularly monitor the card settings and make adjustments as needed to maintain the desired fiber length.
- Inspect the sliver for any signs of excessive fiber breakage or neps, and take corrective actions.
Ensuring Uniformity
- Check the sliver for any variations in thickness or density, and adjust the card settings accordingly.
- Monitor the sliver weight and make adjustments to the feed rate or other parameters to ensure consistency.
Minimizing Contamination
- Maintain a clean work environment and regularly clean the carding machines to prevent contamination.
- Inspect the sliver for any foreign particles or impurities, and remove them promptly.
3. How do you optimize the carding process for different fiber types and blends?
To optimize the carding process for different fiber types and blends, I follow these steps:
- Identify the characteristics of the fiber, such as staple length, strength, and fineness.
- Adjust the carding machine settings, such as cylinder speed, licker-in speed, and doffer speed, to suit the specific fiber properties.
- Monitor the carding process closely and make adjustments as needed to ensure optimal fiber opening, blending, and parallelization.
- Conduct regular tests on the sliver to assess its quality and make further adjustments to the carding process if necessary.
4. How do you troubleshoot and resolve common carding problems, such as uneven sliver, neps, or fiber breakage?
To troubleshoot and resolve common carding problems, I follow a systematic approach:
- Identify the problem and its potential causes by observing the sliver and inspecting the carding machine.
- Check the card settings, such as cylinder speed, licker-in speed, and doffer speed, and adjust them if necessary.
- Inspect the card clothing for any damage or wear, and replace or repair it as needed.
- Clean the carding machine thoroughly to remove any accumulated fiber or debris that may be causing problems.
- Monitor the carding process closely after making adjustments or repairs, and make further changes as needed to resolve the issue.
5. How do you ensure the safety of your team while working on carding machines?
Ensuring the safety of my team while working on carding machines is a top priority for me. I implement the following measures:
- Provide comprehensive safety training to all team members, covering topics such as machine operation, lockout/tagout procedures, and emergency response.
- Regularly inspect the carding machines for any potential hazards and take immediate action to устранить them.
- Enforce strict adherence to safety protocols, such as wearing appropriate personal protective equipment and maintaining a clean and organized work environment.
- Conduct regular safety audits to identify any areas for improvement and implement necessary changes.
- Empower team members to report any safety concerns or near misses, and promptly investigate and address them.
6. How do you motivate and develop your team to achieve high performance?
To motivate and develop my team to achieve high performance, I employ the following strategies:
- Set clear performance goals and expectations, and provide regular feedback to help team members track their progress.
- Recognize and reward team members for their achievements and contributions.
- Create a positive and supportive work environment where team members feel valued and respected.
- Provide opportunities for professional development and growth, such as training programs and mentorship opportunities.
- Encourage open communication and collaboration, and empower team members to share ideas and contribute to decision-making.
7. How do you measure and evaluate the performance of your team and the carding operation?
To measure and evaluate the performance of my team and the carding operation, I use the following metrics:
- Sliver quality: I regularly monitor the quality of the sliver produced, assessing parameters such as fiber length, uniformity, and contamination.
- Production efficiency: I track the amount of sliver produced per hour and compare it to targets to ensure optimal productivity.
- Machine uptime: I monitor the uptime of the carding machines and identify any areas for improvement in maintenance or операционные процедуры.
- Team performance: I evaluate the effectiveness of my team by assessing their adherence to safety protocols, their ability to troubleshoot and resolve problems, and their overall productivity.
8. How do you stay up-to-date with the latest advancements in carding technology and best practices?
To stay up-to-date with the latest advancements in carding technology and best practices, I engage in the following activities:
- Attend industry conferences and exhibitions to learn about new technologies and innovations.
- Read technical journals and articles to stay informed about the latest research and developments.
- Network with other carding professionals and share knowledge and experiences.
- Participate in training programs and workshops to enhance my skills and knowledge.
9. How do you handle production challenges, such as meeting tight deadlines or dealing with unexpected equipment failures?
When faced with production challenges, such as meeting tight deadlines or dealing with unexpected equipment failures, I employ the following strategies:
- Prioritize tasks and allocate resources effectively to ensure that critical deadlines are met.
- Communicate openly with my team and stakeholders to manage expectations and coordinate efforts.
- Troubleshoot and resolve equipment failures promptly to minimize downtime and maintain production efficiency.
- Explore alternative solutions and contingency plans to mitigate the impact of challenges and ensure business continuity.
10. Describe your experience in implementing lean manufacturing principles to improve the carding operation.
In my previous role as Carding Supervisor, I successfully implemented lean manufacturing principles to improve the carding operation. I focused on the following areas:
- Waste reduction: I identified and eliminated waste in the carding process by streamlining workflows, reducing setup times, and optimizing material handling.
- Process flow improvement: I analyzed the carding process and identified bottlenecks. I then implemented changes to improve the flow of materials and reduce lead times.
- Standardization: I established standardized work instructions and procedures for all carding operations to ensure consistency and improve efficiency.
- Employee involvement: I engaged my team in the lean implementation process and empowered them to identify and address areas for improvement.
As a result of these efforts, we achieved significant improvements in production efficiency, reduced waste, and enhanced the overall performance of the carding operation.
Interviewers often ask about specific skills and experiences. With ResumeGemini‘s customizable templates, you can tailor your resume to showcase the skills most relevant to the position, making a powerful first impression. Also check out Resume Template specially tailored for Carding Supervisor.
Career Expert Tips:
- Ace those interviews! Prepare effectively by reviewing the Top 50 Most Common Interview Questions on ResumeGemini.
- Navigate your job search with confidence! Explore a wide range of Career Tips on ResumeGemini. Learn about common challenges and recommendations to overcome them.
- Craft the perfect resume! Master the Art of Resume Writing with ResumeGemini’s guide. Showcase your unique qualifications and achievements effectively.
- Great Savings With New Year Deals and Discounts! In 2025, boost your job search and build your dream resume with ResumeGemini’s ATS optimized templates.
Researching the company and tailoring your answers is essential. Once you have a clear understanding of the Carding Supervisor‘s requirements, you can use ResumeGemini to adjust your resume to perfectly match the job description.
Key Job Responsibilities
Carding Supervisors play a crucial role in ensuring the efficient operation of carding machines in textile mills. Their responsibilities encompass a wide range of tasks related to machine operation, maintenance, and quality control.
1. Machine Operation and Monitoring
Supervising and coordinating the operation of carding machines to ensure optimal production.
- Monitoring machine settings and performance to identify any deviations from standards.
- Adjusting and calibrating machines to maintain desired quality and production targets.
2. Maintenance and Repair
Performing routine maintenance and repairs on carding machines to prevent breakdowns and ensure smooth functioning.
- Identifying and diagnosing mechanical or electrical issues in machines.
- Replacing worn or damaged parts and conducting necessary repairs.
- Coordinating with maintenance personnel for major repairs or overhauls.
3. Quality Control
Ensuring the quality of carded fibers by monitoring and controlling process parameters.
- Conducting regular inspections of carded fibers to assess quality and adherence to specifications.
- Identifying and addressing deviations in fiber quality, such as contamination or unevenness.
- Implementing corrective actions to maintain desired quality standards.
4. Production Planning and Scheduling
Coordinating production schedules and ensuring adherence to production targets.
- Planning and organizing work schedules for carding operators and other staff involved in the carding process.
- Monitoring production progress and identifying bottlenecks or areas for improvement.
- Collaborating with other departments, such as spinning and weaving, to ensure smooth production flow.
5. Training and Supervision
Training and supervising carding operators and other staff to ensure safe and efficient operations.
- Providing on-the-job training and guidance to new or inexperienced operators.
- Monitoring operator performance and providing feedback to improve skills and efficiency.
- Ensuring that all staff adheres to safety protocols and regulations.
Interview Tips
To prepare for an interview for a Carding Supervisor position, it’s essential to have a thorough understanding of the key responsibilities and industry best practices. Here are some tips to help you ace the interview:
1. Research the Company and Industry
Familiarize yourself with the company’s history, products, and competitive landscape. Research the textile industry and stay up-to-date on trends and technologies related to carding.
2. Practice Answering Common Interview Questions
Prepare for questions related to your experience in carding operations, quality control, production planning, and team management. Practice answering using the STAR method (Situation, Task, Action, Result) to highlight your skills and achievements.
- Example question: Describe a situation where you identified and resolved a quality issue in the carding process.
- Example answer: [Using the STAR method, provide a detailed account of the situation, the specific actions you took, and the positive results achieved].
3. Showcase Your Technical Expertise
Highlight your knowledge of carding machine operation, maintenance, and quality control techniques. Describe your experience in diagnosing and troubleshooting mechanical or electrical issues.
- Example question: What are the key factors that affect the quality of carded fibers?
- Example answer: [Explain the factors such as fiber type, machine settings, and operator skills, providing examples of how they impact fiber quality].
4. Emphasize Your Leadership and Management Skills
Discuss your experience in supervising and motivating teams, setting performance goals, and providing constructive feedback. Highlight your ability to maintain a safe and productive work environment.
- Example question: How do you ensure that your team meets production targets and maintains quality standards?
- Example answer: [Describe your approach to team management, including setting clear expectations, providing training, and monitoring performance].
5. Be Prepared to Discuss Your Career Goals
Articulate your career goals and how the Carding Supervisor position aligns with your aspirations. Explain how your skills and experience can contribute to the company’s success.
- Example question: Where do you see yourself in five years?
- Example answer: [State your professional goals and how they align with the company’s objectives, demonstrating your commitment to growth and development].
Next Step:
Now that you’re armed with the knowledge of Carding Supervisor interview questions and responsibilities, it’s time to take the next step. Build or refine your resume to highlight your skills and experiences that align with this role. Don’t be afraid to tailor your resume to each specific job application. Finally, start applying for Carding Supervisor positions with confidence. Remember, preparation is key, and with the right approach, you’ll be well on your way to landing your dream job. Build an amazing resume with ResumeGemini
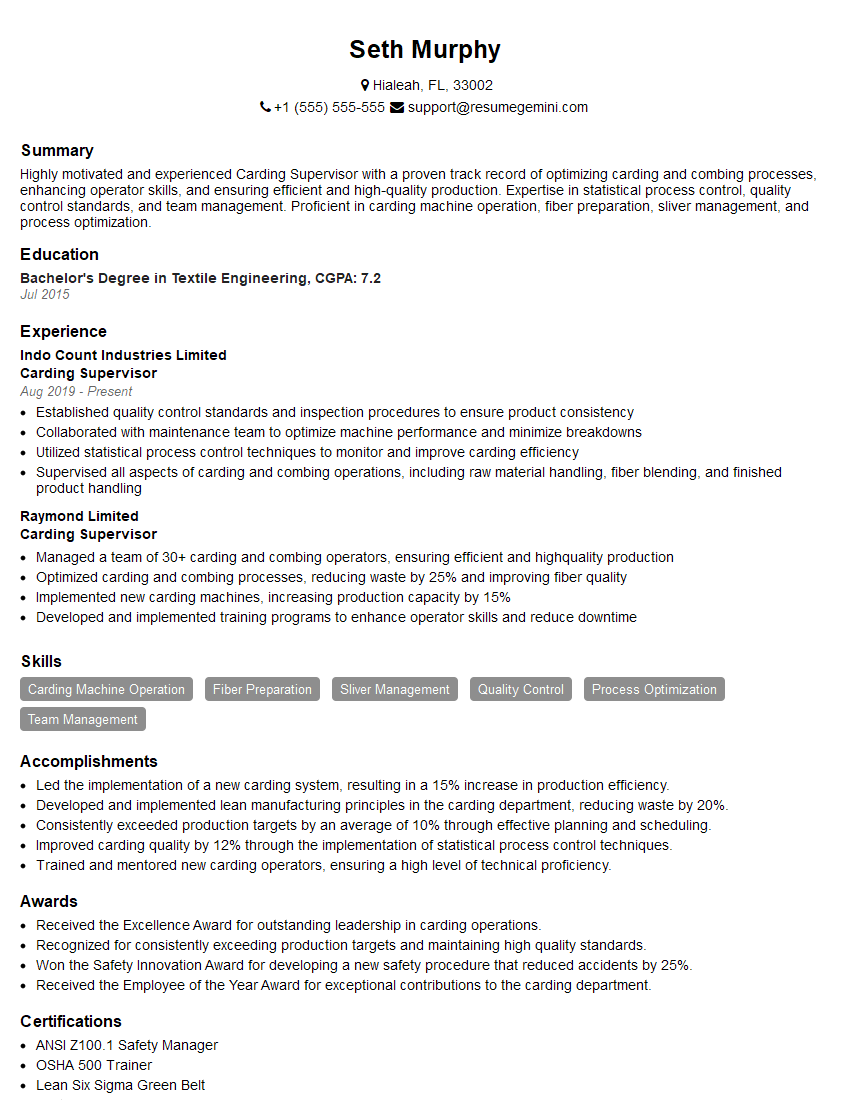