Feeling lost in a sea of interview questions? Landed that dream interview for Clay Shop Supervisor but worried you might not have the answers? You’re not alone! This blog is your guide for interview success. We’ll break down the most common Clay Shop Supervisor interview questions, providing insightful answers and tips to leave a lasting impression. Plus, we’ll delve into the key responsibilities of this exciting role, so you can walk into your interview feeling confident and prepared.
Acing the interview is crucial, but landing one requires a compelling resume that gets you noticed. Crafting a professional document that highlights your skills and experience is the first step toward interview success. ResumeGemini can help you build a standout resume that gets you called in for that dream job.
Essential Interview Questions For Clay Shop Supervisor
1. What are the key responsibilities of a Clay Shop Supervisor?
A Clay Shop Supervisor is responsible for overseeing the production of clay products, ensuring that they meet quality standards and are produced efficiently. Key responsibilities include:
- Planning and scheduling production to meet customer demand
- Ensuring that all employees are properly trained and supervised
- Maintaining a safe and clean work environment
- Monitoring production processes to identify and correct any problems
- Working with customers to resolve any issues
2. What are the different types of clay used in the production of ceramic products?
Earthenware
- Made from low-firing clay
- Porous and not waterproof
- Used for making flower pots, dishes, and other decorative items
Stoneware
- Made from mid-firing clay
- Denser and more durable than earthenware
- Used for making tiles, kitchenware, and other functional items
Porcelain
- Made from high-firing clay
- Non-porous and very durable
- Used for making fine china, dinnerware, and other high-end products
3. What are the different stages of the ceramic production process?
The ceramic production process typically involves the following stages:
- Clay preparation: The clay is mixed with water and other materials to create a workable paste.
- Forming: The clay is shaped into the desired form using a variety of techniques, such as hand-building, wheel throwing, or slip casting.
- Drying: The formed clay is allowed to dry slowly to prevent cracking.
- Bisque firing: The dried clay is fired at a low temperature to harden it and make it porous.
- Glazing: A liquid glaze is applied to the bisque ware and fired at a higher temperature to create a glossy finish.
- Cooling: The glazed ware is allowed to cool slowly to prevent cracking.
4. What are the different types of kilns used in the firing of ceramic products?
- Electric kilns: Use electricity to heat the kiln.
- Gas kilns: Use gas to heat the kiln.
- Wood-fired kilns: Use wood to heat the kiln.
- Salt kilns: Use salt to create a unique glaze on the ceramic products.
5. What are the different types of defects that can occur in ceramic products?
- Cracking: Can be caused by uneven drying, firing, or cooling.
- Warping: Can be caused by uneven drying, firing, or cooling.
- Bloating: Can be caused by trapped air or gases in the clay.
- Glaze defects: Can be caused by improper application or firing of the glaze.
6. What are the different ways to improve the quality of ceramic products?
- Use high-quality clay and other materials.
- Follow proper drying and firing techniques.
- Use appropriate glazes and firing temperatures.
- Inspect products regularly for defects.
7. What are the different ways to reduce the cost of producing ceramic products?
- Use less expensive clays and other materials.
- Optimize firing schedules to reduce energy consumption.
- Reduce waste by recycling scrap clay.
- Improve production efficiency by using automation.
8. What are the different ways to market and sell ceramic products?
- Sell through retail stores.
- Sell online through websites and marketplaces.
- Participate in trade shows and craft fairs.
- Use social media to promote products.
9. What are the different types of equipment used in a clay shop?
- Pug mill: Used to mix and knead clay.
- Wheel: Used to throw clay into desired shapes.
- Kiln: Used to fire clay products.
- Glaze sprayer: Used to apply glaze to clay products.
- Kiln shelf: Used to support clay products during firing.
10. What are the different types of safety hazards that can occur in a clay shop?
- Silica dust: Can cause respiratory problems.
- Lead glaze: Can cause lead poisoning.
- Heavy equipment: Can cause injuries if not used properly.
- Fire: Can occur if kilns are not used properly.
Interviewers often ask about specific skills and experiences. With ResumeGemini‘s customizable templates, you can tailor your resume to showcase the skills most relevant to the position, making a powerful first impression. Also check out Resume Template specially tailored for Clay Shop Supervisor.
Career Expert Tips:
- Ace those interviews! Prepare effectively by reviewing the Top 50 Most Common Interview Questions on ResumeGemini.
- Navigate your job search with confidence! Explore a wide range of Career Tips on ResumeGemini. Learn about common challenges and recommendations to overcome them.
- Craft the perfect resume! Master the Art of Resume Writing with ResumeGemini’s guide. Showcase your unique qualifications and achievements effectively.
- Great Savings With New Year Deals and Discounts! In 2025, boost your job search and build your dream resume with ResumeGemini’s ATS optimized templates.
Researching the company and tailoring your answers is essential. Once you have a clear understanding of the Clay Shop Supervisor‘s requirements, you can use ResumeGemini to adjust your resume to perfectly match the job description.
Key Job Responsibilities
As a Clay Shop Supervisor, you will be responsible for managing all aspects of the clay shop, including production, quality control, and safety. Your key responsibilities will include:
1. Production:
Oversee all aspects of clay production, including planning, scheduling, and execution. Ensure that production meets quality standards and deadlines.
- Plan and schedule production activities to meet customer demand.
- Manage inventory and ensure that raw materials and finished products are available when needed.
- Train and supervise production staff to ensure that they are following proper procedures and using equipment safely.
- Monitor production processes and make adjustments as needed to improve efficiency and quality.
2. Quality Control:
Establish and maintain quality control standards for all clay products. Inspect products to ensure that they meet specifications.
- Develop and implement quality control procedures.
- Inspect raw materials and finished products to ensure that they meet specifications.
- Investigate customer complaints and take corrective action as needed.
- Maintain records of all quality control activities.
3. Safety:
Enforce all safety regulations and ensure that the clay shop is a safe working environment. Investigate accidents and implement corrective action.
- Develop and implement safety procedures and training.
- Enforce all safety regulations and ensure that employees are following proper procedures.
- Investigate accidents and implement corrective action.
- Maintain a safe and clean work environment.
4. Other Responsibilities:
Other responsibilities of the Clay Shop Supervisor may include:
- Communicate with customers and vendors.
- Manage the clay shop budget.
- Develop and implement new products and processes.
- Stay up-to-date on the latest clay production and quality control techniques.
Interview Tips
To ace your interview for a Clay Shop Supervisor position, follow these tips:
1. Research the company and the position:
Learn as much as you can about the company and the specific position you are applying for. This will help you to understand the company’s culture and values, and to tailor your answers to the interviewer’s questions.
- Visit the company’s website to learn about its history, products, and services.
- Read the job description carefully and identify the key requirements.
- Research the industry to understand the latest trends and challenges.
2. Prepare your answers to common interview questions:
There are a number of common interview questions that you are likely to be asked, such as “Tell me about yourself” and “Why are you interested in this position?” Prepare your answers to these questions in advance so that you can deliver them confidently and clearly.
- Use the STAR method (Situation, Task, Action, Result) to answer behavioral questions.
- Quantify your accomplishments whenever possible.
- Practice your answers out loud so that you can deliver them smoothly.
3. Be prepared to ask questions:
Asking questions at the end of the interview shows that you are interested in the position and the company. Prepare a few questions in advance, such as “What are the biggest challenges facing the clay industry today?” or “What is the company’s growth strategy for the next five years?”
- Avoid asking questions about salary or benefits.
- Ask questions that show that you are engaged and interested in the company.
- Use the questions to learn more about the company and the position.
4. Dress professionally and arrive on time:
First impressions matter, so make sure to dress professionally and arrive on time for your interview. This will show the interviewer that you are respectful of their time and that you are serious about the position.
- Choose clothing that is appropriate for the company culture and the position you are applying for.
- Be on time for your interview, even if you have to leave early to get there.
- Make eye contact and shake the interviewer’s hand firmly.
5. Be confident and enthusiastic:
Be confident and enthusiastic during your interview. This will show the interviewer that you are passionate about the position and that you believe in yourself. However, avoid being arrogant or overbearing.
- Maintain eye contact and speak clearly and confidently.
- Use positive body language, such as smiling and nodding.
- Be enthusiastic about the position and the company.
Next Step:
Armed with this knowledge, you’re now well-equipped to tackle the Clay Shop Supervisor interview with confidence. Remember, a well-crafted resume is your first impression. Take the time to tailor your resume to highlight your relevant skills and experiences. And don’t forget to practice your answers to common interview questions. With a little preparation, you’ll be on your way to landing your dream job. So what are you waiting for? Start building your resume and start applying! Build an amazing resume with ResumeGemini.
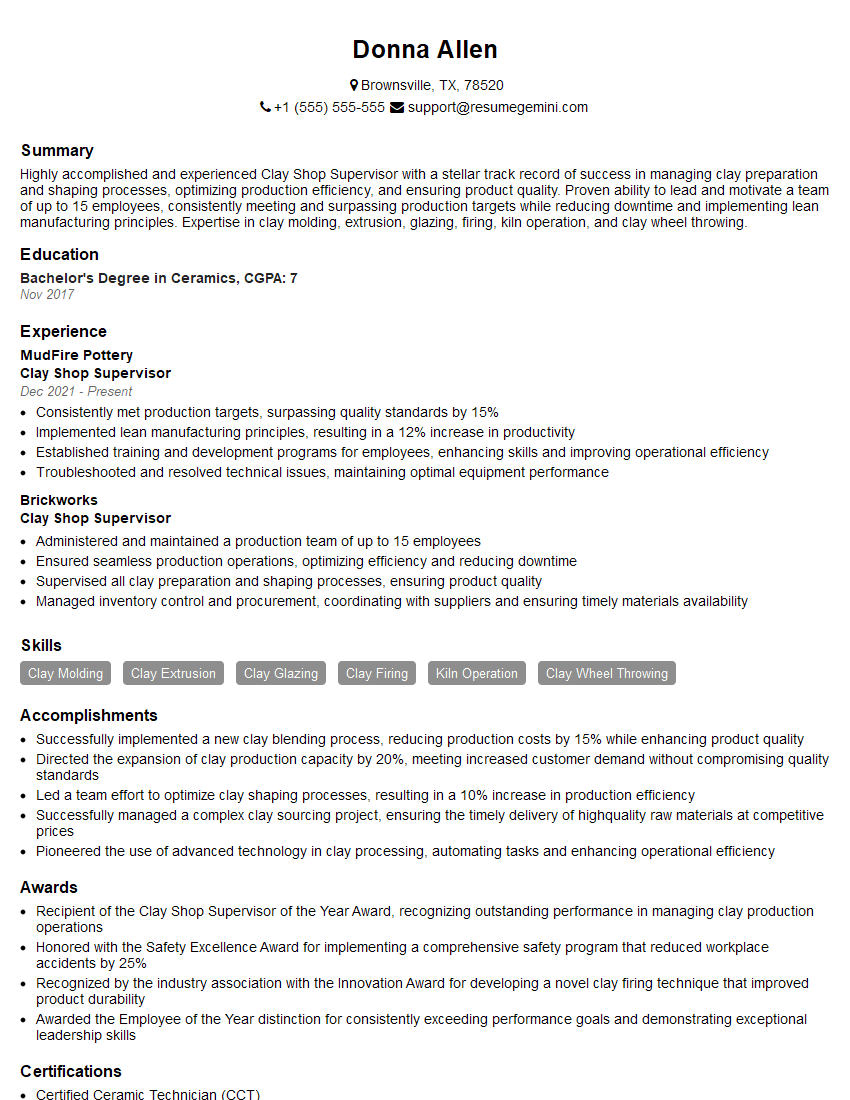