Are you gearing up for a career shift or aiming to ace your next interview? Look no further! We’ve curated a comprehensive guide to help you crack the interview for the coveted Coil Connector position. From understanding the key responsibilities to mastering the most commonly asked questions, this blog has you covered. So, buckle up and let’s embark on this journey together
Acing the interview is crucial, but landing one requires a compelling resume that gets you noticed. Crafting a professional document that highlights your skills and experience is the first step toward interview success. ResumeGemini can help you build a standout resume that gets you called in for that dream job.
Essential Interview Questions For Coil Connector
1. What are the main types of coil connectors and their applications?
Coil connectors are primarily classified into three main types based on their design and application:
- Axial Lead Coil Connectors: Designed with leads extending axially from the coil body, suitable for through-hole mounting on printed circuit boards (PCBs).
- Radial Lead Coil Connectors: Feature leads extending radially from the coil body, often used for surface mount applications on PCBs.
- Pin-Through-Hole Coil Connectors: Combine axial and radial leads, providing flexibility in mounting options and enabling secure connections in high-vibration environments.
2. Explain the factors that influence the inductance of a coil connector.
Number of Turns
- Inductance is directly proportional to the number of turns in the coil.
Core Material
- Ferrite and iron cores increase inductance compared to air cores.
Coil Geometry
- Larger coil diameters and shorter coil lengths increase inductance.
Spacing between Turns
- Closer spacing between turns increases inductance.
3. How do you ensure proper electrical contact between the coil connector and the mating component?
Ensuring proper electrical contact is crucial:
- Proper Insertion: Connectors should be fully inserted and engagement mechanisms engaged.
- Clean Contacts: Contacts should be free of dirt, corrosion, or debris.
- Adequate Contact Force: Sufficient force should be applied to maintain contact pressure.
- Vibration Resistance: Connectors should be designed to withstand vibrations and maintain contact.
4. What testing methods are used to evaluate the performance of coil connectors?
Coil connectors undergo rigorous testing to ensure reliability and performance:
- Inductance Measurement: Verifies the electrical inductance of the coil.
- Resistance Measurement: Tests the electrical resistance of the leads and contacts.
- Insulation Resistance Test: Evaluates the electrical insulation between conductors.
- High-Voltage/Dielectric Withstand Test: Assesses the ability to withstand high voltages without breakdown.
- Vibration and Shock Tests: Simulate real-world conditions and ensure durability.
5. Describe the different materials used in the construction of coil connectors.
Coil connectors utilize various materials based on their performance requirements:
- Conductive Materials: Copper, brass, or beryllium copper for leads and contacts.
- Insulating Materials: Nylon, PBT, or PPS for coil bobbins and insulators.
- Magnetic Core Materials: Ferrite or iron for increasing inductance.
- Jacketing Materials: PVC, rubber, or silicone for protection and flexibility.
6. How do you calculate the current-carrying capacity of a coil connector?
The current-carrying capacity depends on several factors:
- Wire Gauge: Larger wire sizes can carry higher currents.
- Conductor Material: Copper has a higher current-carrying capacity than aluminum.
- Temperature Rating: Insulation materials have temperature limits that affect current capacity.
- Ambient Temperature: Higher ambient temperatures reduce current capacity.
- Connector Design: Connector geometry and ventilation affect heat dissipation.
7. What are the potential failure modes of coil connectors and how can they be mitigated?
Coil connectors can experience various failure modes:
- Open Circuits: Broken wires or loose connections can cause interruptions in current flow.
- Short Circuits: Contact between adjacent conductors can create unwanted current paths.
- Insulation Breakdown: Excessive voltage or heat can damage insulation and lead to short circuits.
- Contact Wear: Repeated mating and unmating can cause contact surfaces to wear.
Mitigation strategies include:
- Using high-quality materials and manufacturing processes
- Proper connector selection and application
- Adequate environmental protection
- Regular maintenance and inspection
8. Can you explain the concept of insertion loss in coil connectors?
Insertion loss refers to the signal power loss that occurs when a coil connector is inserted into a circuit:
- Reflection Loss: Mismatch between connector impedance and circuit impedance causes signal reflections.
- Ohmic Loss: Resistance in the connector materials and contacts attenuates the signal.
- Dielectric Loss: Energy lost due to interactions with the connector’s insulating materials.
9. Describe the importance of shielding in coil connectors and its applications.
Shielding is crucial for:
- EMI/RFI Suppression: Prevents interference from external electromagnetic fields.
- Cross-Talk Reduction: Minimizes signal interference between adjacent connectors.
- Grounding: Provides a low-impedance path for current to flow, reducing noise.
Shielding is used in applications such as:
- Medical equipment
- Communication systems
- Industrial control
10. Discuss the role of quality control in coil connector manufacturing.
Quality control ensures:
- Product Conformance: Connectors meet design specifications and performance requirements.
- Process Consistency: Manufacturing processes are standardized and controlled to maintain quality.
- Defect Prevention: Proactive measures are taken to identify and eliminate potential defects.
- Continuous Improvement: Feedback and analysis are used to enhance product quality and processes.
Interviewers often ask about specific skills and experiences. With ResumeGemini‘s customizable templates, you can tailor your resume to showcase the skills most relevant to the position, making a powerful first impression. Also check out Resume Template specially tailored for Coil Connector.
Career Expert Tips:
- Ace those interviews! Prepare effectively by reviewing the Top 50 Most Common Interview Questions on ResumeGemini.
- Navigate your job search with confidence! Explore a wide range of Career Tips on ResumeGemini. Learn about common challenges and recommendations to overcome them.
- Craft the perfect resume! Master the Art of Resume Writing with ResumeGemini’s guide. Showcase your unique qualifications and achievements effectively.
- Great Savings With New Year Deals and Discounts! In 2025, boost your job search and build your dream resume with ResumeGemini’s ATS optimized templates.
Researching the company and tailoring your answers is essential. Once you have a clear understanding of the Coil Connector‘s requirements, you can use ResumeGemini to adjust your resume to perfectly match the job description.
Key Job Responsibilities
Coil Connectors are responsible for manufacturing and installing coil systems in industrial and commercial settings. They work closely with electricians and other tradespeople to ensure that the systems are installed correctly and meet safety standards.
1. Manufacturing Coil Systems
Coil Connectors manufacture coils using various materials, such as copper, aluminum, and steel. They use specialized equipment to form the coils into the desired shape and size. They also install electrical components, such as transformers and capacitors, into the coils.
2. Installing Coil Systems
Coil Connectors install coil systems in a variety of settings, including power plants, factories, and commercial buildings. They work with electricians to connect the coils to the electrical grid and ensure that the systems are operating properly.
3. Maintaining Coil Systems
Coil Connectors perform regular maintenance on coil systems to ensure that they are operating safely and efficiently. They inspect the coils for damage and wear, and they replace any components that are not functioning properly.
4. Troubleshooting Coil Systems
Coil Connectors troubleshoot coil systems when they experience problems. They use their knowledge of the systems to diagnose the problem and make repairs.
Interview Tips
Preparing for an interview for a Coil Connector position can be daunting, but by following these tips, you can increase your chances of success.
1. Research the Company and the Position
Before the interview, take some time to research the company and the position. This will help you to understand the company’s culture and the specific responsibilities of the Coil Connector role.
2. Practice Your Answers to Common Interview Questions
There are a number of common interview questions that you are likely to be asked, such as “Tell me about yourself” and “Why are you interested in this position?” Practice your answers to these questions so that you can deliver them confidently and concisely.
3. Be Prepared to Talk About Your Experience
The interviewer will want to know about your experience as a Coil Connector. Be prepared to talk about your skills and experience in manufacturing, installing, and maintaining coil systems.
4. Be Enthusiastic and Positive
The interviewer will be looking for someone who is enthusiastic and positive about the Coil Connector position. Show your interest in the position and the company by asking questions and engaging in conversation.
Next Step:
Now that you’re armed with interview-winning answers and a deeper understanding of the Coil Connector role, it’s time to take action! Does your resume accurately reflect your skills and experience for this position? If not, head over to ResumeGemini. Here, you’ll find all the tools and tips to craft a resume that gets noticed. Don’t let a weak resume hold you back from landing your dream job. Polish your resume, hit the “Build Your Resume” button, and watch your career take off! Remember, preparation is key, and ResumeGemini is your partner in interview success.
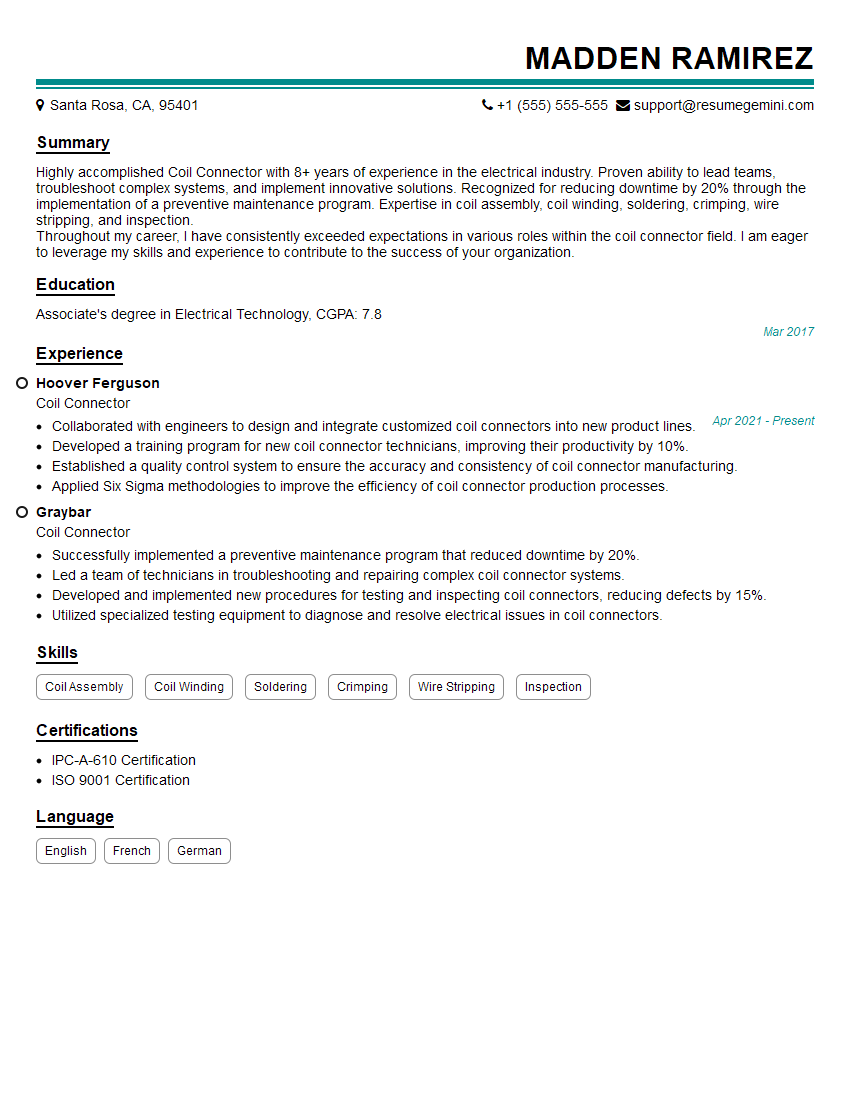