Are you gearing up for an interview for a Drum Maker position? Whether you’re a seasoned professional or just stepping into the role, understanding what’s expected can make all the difference. In this blog, we dive deep into the essential interview questions for Drum Maker and break down the key responsibilities of the role. By exploring these insights, you’ll gain a clearer picture of what employers are looking for and how you can stand out. Read on to equip yourself with the knowledge and confidence needed to ace your next interview and land your dream job!
Acing the interview is crucial, but landing one requires a compelling resume that gets you noticed. Crafting a professional document that highlights your skills and experience is the first step toward interview success. ResumeGemini can help you build a standout resume that gets you called in for that dream job.
Essential Interview Questions For Drum Maker
1. Explain the different types of wood used in drum making and their properties?
- Hardwoods: Maple, Oak, Birch, Mahogany – These woods are dense and durable, making them ideal for use in drum shells. They produce a bright, clear sound with a lot of attack.
- Softwoods: Pine, Fir, Spruce – These woods are less dense than hardwoods, making them more resonant. They produce a warmer, rounder sound with less attack.
- Exotic woods: Rosewood, Ebony, Teak – These woods are often used for their unique appearance and sound characteristics. They can be very dense, producing a bright, crisp sound, or they can be softer, producing a warmer, more resonant sound.
2. Describe the process of making a drum shell?
Tools
- Wood lathe
- Drum hoop bender
- Drum sander
- Drum press
- Drum drilling machine
Process
- Cut the wood to the desired length and width.
- Mount the wood on the wood lathe and shape it into a drum shell.
- Bend the drum hoop around the shell and secure it with screws.
- Sand the shell to smooth it out.
- Press the shell to give it its final shape.
- Drill holes in the shell for the lugs, vents, and other hardware.
3. How do you select the right drum head for a particular drum?
- Size: The drum head must be the correct size for the drum shell.
- Thickness: The thickness of the drum head will affect the sound of the drum. Thicker heads produce a lower pitch, while thinner heads produce a higher pitch.
- Material: Drum heads are made from a variety of materials, such as Mylar, Kevlar, and animal skin. Each material has its own unique sound characteristics.
- Coating: Drum heads can be coated with a variety of materials, such as lacquer, enamel, and oil. Coatings can affect the sound of the drum, making it brighter, warmer, or more resonant.
4. Explain the importance of drum hardware?
- Lugs: Lugs hold the drum head in place and allow it to be tuned.
- Hoops: Hoops provide support for the drum head and help to keep it in place.
- Throw-off: The throw-off allows the snare drum to be played with or without the snare wires engaged.
- Cymbal stands: Cymbal stands hold cymbals in place and allow them to be adjusted to the desired height and angle.
- Drum thrones: Drum thrones provide a comfortable place for the drummer to sit while playing.
5. How do you maintain a drum set?
- Clean the drums regularly. This will help to remove dirt, dust, and moisture, which can damage the drums.
- Lubricate the hardware regularly. This will help to keep the hardware moving smoothly and prevent it from rusting.
- Replace the drum heads as needed. Drum heads will eventually wear out and need to be replaced. Replace them as soon as you notice any signs of wear or damage.
- Store the drums in a cool, dry place. This will help to prevent the drums from warping or cracking.
6. What are the most important qualities of a good drum maker?
- Attention to detail: A good drum maker must pay close attention to detail in order to create drums that are both beautiful and functional.
- Craftsmanship: A good drum maker must have excellent craftsmanship skills in order to create drums that are durable and well-made.
- Knowledge of materials: A good drum maker must have a good understanding of the different materials used in drum making in order to select the right materials for each drum.
- Creativity: A good drum maker must be creative in order to design drums that are both unique and beautiful.
7. What is the most challenging aspect of drum making?
- Selecting the right materials: The choice of materials can have a significant impact on the sound and quality of the drum.
- Shaping the drum shell: Shaping the drum shell requires precision and skill in order to create a shell that is both beautiful and functional.
- Assembling the drum: Assembling the drum requires careful attention to detail in order to ensure that the drum is properly put together.
8. What is the most rewarding aspect of drum making?
- Seeing your creation come to life: There is nothing quite like seeing a drum that you have created come to life and being played by a musician.
- Hearing your drums being played: The sound of a well-made drum is truly something special.
- Knowing that you have crafted a piece of art: A drum is not just a musical instrument, it is also a work of art.
9. What are your favorite types of drums to make?
- Snare drums: I love the challenge of creating a snare drum that has a great sound and is also visually appealing.
- Bass drums: I enjoy making bass drums because they are such a powerful and versatile instrument.
- Tom-toms: Tom-toms are a great way to add depth and complexity to a drum set.
10. What are your long-term goals as a drum maker?
- To continue to improve my skills as a drum maker: I want to learn new techniques and experiment with new materials in order to create even better drums.
- To build a reputation for making high-quality drums: I want my drums to be known for their excellent sound, craftsmanship, and beauty.
- To inspire other drum makers: I want to share my knowledge and experience with other drum makers so that they can also create great drums.
Interviewers often ask about specific skills and experiences. With ResumeGemini‘s customizable templates, you can tailor your resume to showcase the skills most relevant to the position, making a powerful first impression. Also check out Resume Template specially tailored for Drum Maker.
Career Expert Tips:
- Ace those interviews! Prepare effectively by reviewing the Top 50 Most Common Interview Questions on ResumeGemini.
- Navigate your job search with confidence! Explore a wide range of Career Tips on ResumeGemini. Learn about common challenges and recommendations to overcome them.
- Craft the perfect resume! Master the Art of Resume Writing with ResumeGemini’s guide. Showcase your unique qualifications and achievements effectively.
- Great Savings With New Year Deals and Discounts! In 2025, boost your job search and build your dream resume with ResumeGemini’s ATS optimized templates.
Researching the company and tailoring your answers is essential. Once you have a clear understanding of the Drum Maker‘s requirements, you can use ResumeGemini to adjust your resume to perfectly match the job description.
Key Job Responsibilities
Drum makers play a pivotal role in the creation of musical drums, instruments essential for any percussionist or drummer. Their responsibilities encompass a wide range of tasks, each contributing to the production of high-quality drums.
1. Crafting Drum Shells
Drum makers possess the expertise to construct drum shells, the fundamental component of a drum. They meticulously select the appropriate wood, ensuring its tonal qualities and durability, and shape it using specialized machinery, including lathes and sanding equipment.
- Precisely cut and shape wood to create drum shells of various sizes and depths.
- Steam and bend wood to form the distinctive curves of drum shells.
2. Installing Hardware
Drum makers are responsible for installing hardware onto the drum shells. This includes attaching hoops, lugs, tension rods, and other components that enable the drum to be tuned and played. They ensure that the hardware is securely fastened and aligned correctly for optimal performance.
- Mount hoops onto the drum shells and tighten them evenly.
- Install tension rods and lugs, ensuring proper tension and tuning capabilities.
3. Applying Finishes
Drum makers apply a range of finishes to the drum shells, enhancing their appearance and protecting the wood. They may use stains, lacquers, or other materials to achieve desired colors and textures. They also apply protective coatings to safeguard the drums from wear and tear.
- Apply stains and lacquers to enhance the aesthetic appeal of the drums.
- Use polyurethane or other protective coatings to shield the drums from moisture and scratches.
4. Quality Control
Drum makers strictly adhere to quality control measures throughout the production process. They inspect each drum component for defects and ensure that the finished product meets specifications. They also conduct sound tests to verify the tonal qualities and resonance of the drums.
- Inspect wood for imperfections and ensure proper grain orientation.
- Conduct sound tests to assess the pitch, volume, and sustain of the drums.
Interview Tips
Ace the interview by following these expert interview preparation tips:
1. Research the Company and Position
Thoroughly research the company you are applying to and the specific role you are seeking. This will demonstrate your genuine interest and commitment to the opportunity. Familiarize yourself with their history, products or services, company culture, and mission statement.
- Visit the company’s website and social media pages for insights.
- Read articles and news about the company to stay informed.
2. Practice Your Answers
Prepare thoughtful answers to potential interview questions by practicing in advance. Consider questions related to your skills, experience, motivations, and why you are interested in the position. Practice delivering your answers confidently and concisely.
- Anticipate questions about your drum-making techniques and knowledge.
- Prepare examples to showcase your craftsmanship and attention to detail.
3. Dress Professionally and Be Punctual
First impressions matter, so dress professionally and arrive on time for your interview. Your appearance and punctuality convey respect for the interviewer and the company.
- Choose attire that is appropriate for the company culture.
- Plan your route and transportation in advance to avoid any delays.
4. Show Enthusiasm and Ask Questions
Express your enthusiasm for the position and the company. Ask thoughtful questions about the role, the team, and the company’s goals. This demonstrates your genuine interest and eagerness to learn more.
- Inquire about the company’s commitment to sustainability in drum-making.
- Ask about opportunities for professional development and growth within the role.
Next Step:
Now that you’re armed with a solid understanding of what it takes to succeed as a Drum Maker, it’s time to turn that knowledge into action. Take a moment to revisit your resume, ensuring it highlights your relevant skills and experiences. Tailor it to reflect the insights you’ve gained from this blog and make it shine with your unique qualifications. Don’t wait for opportunities to come to you—start applying for Drum Maker positions today and take the first step towards your next career milestone. Your dream job is within reach, and with a polished resume and targeted applications, you’ll be well on your way to achieving your career goals! Build your resume now with ResumeGemini.
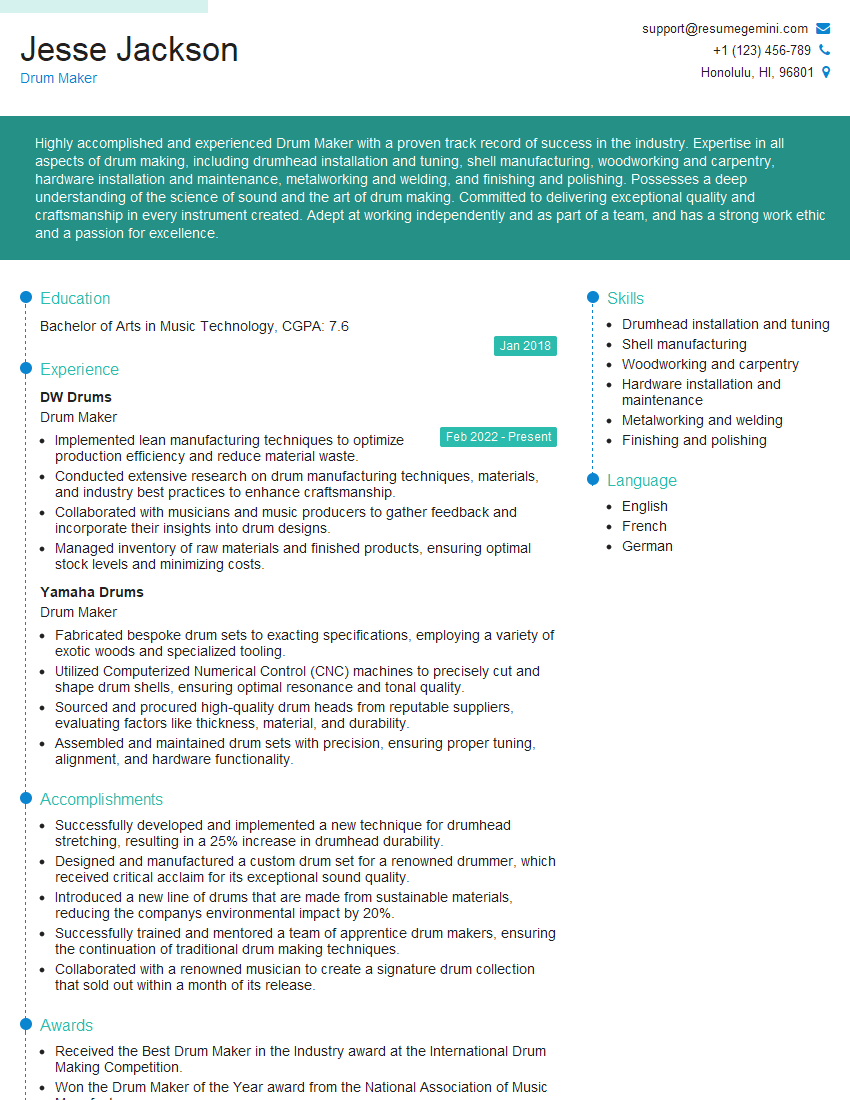