Are you gearing up for a career in Electric Spot Welder? Feeling nervous about the interview questions that might come your way? Don’t worry, you’re in the right place. In this blog post, we’ll dive deep into the most common interview questions for Electric Spot Welder and provide you with expert-backed answers. We’ll also explore the key responsibilities of this role so you can tailor your responses to showcase your perfect fit.
Acing the interview is crucial, but landing one requires a compelling resume that gets you noticed. Crafting a professional document that highlights your skills and experience is the first step toward interview success. ResumeGemini can help you build a standout resume that gets you called in for that dream job.
Essential Interview Questions For Electric Spot Welder
1. What are the different types of electric spot welders and what are their advantages and disadvantages?
There are different types of electric spot welders, each with its advantages and disadvantages:
- AC spot welders: Uses alternating current (AC) to create welds. Advantages of AC welders are lower cost and less maintenance. Disadvantages include less precise welds and more spatter.
- DC spot welders: Uses direct current (DC) to create welds. Advantages of DC welders are more precise welds, less spatter, and better weld quality. Disadvantages include higher cost and more maintenance.
- Inverter spot welders: Uses advanced technology to convert AC power to DC power. Advantages of inverter welders are lightweight, portable, and energy-efficient. Disadvantages include higher cost and more complexity.
- Capacitor discharge (CD) spot welders: Stores energy in capacitors and releases it to create welds. Advantages of CD welders are fast welding speed and high power. Disadvantages include high cost and limited weld size.
2. What are the key parameters to consider when setting up an electric spot welder?
Weld current:
- Determines the amount of heat generated during the welding process.
- Higher currents result in stronger welds but can also cause excessive heat and damage to the materials being welded.
Weld time:
- Determines the duration of the welding current flow.
- Longer weld times result in stronger welds but can also cause excessive heat and damage to the materials being welded.
Electrode force:
- Determines the amount of pressure applied to the materials being welded.
- Higher electrode forces result in stronger welds but can also cause distortion or damage to the materials being welded.
Material thickness:
- Determines the amount of current, time, and force required to create a strong weld.
- Thicker materials require higher settings to achieve a good weld.
3. What are the common problems encountered in electric spot welding and how do you troubleshoot them?
Some common problems encountered in electric spot welding include:
- Porosity: Occurs when gas pockets are trapped in the weld. Can be caused by insufficient electrode force, improper weld time, or dirty materials.
- Spatter: Occurs when molten metal is ejected from the weld area. Can be caused by excessive weld current, improper electrode force, or dirty materials.
- Weld cracking: Occurs when the weld metal cracks. Can be caused by excessive heat, improper weld time, or brittle materials.
- Weld distortion: Occurs when the materials being welded are distorted by the heat of the weld. Can be caused by uneven heating, excessive heat, or improper electrode force.
Troubleshooting involves identifying the root cause of the problem and adjusting the welding parameters accordingly.
4. What are the safety precautions that should be taken when operating an electric spot welder?
To ensure safety when operating an electric spot welder, it is important to:
- Wear appropriate personal protective equipment (PPE), including gloves, safety glasses, and earplugs.
- Ensure the work area is well-ventilated to avoid inhalation of harmful fumes.
- Inspect the welder and cables regularly for any damage.
- Keep flammable materials away from the welding area.
- Never operate the welder if it is damaged or malfunctioning.
5. Describe the process of setting up and operating an electric spot welder.
Setting up and operating an electric spot welder typically involves the following steps:
- Mount the welder to a stable work surface.
- Connect the welder to a power source.
- Adjust the welding parameters (current, time, force) based on the materials being welded.
- Place the materials to be welded between the electrodes.
- Activate the welding cycle.
- Inspect the weld to ensure it meets the desired specifications.
6. How do you maintain an electric spot welder to ensure optimal performance?
To maintain an electric spot welder for optimal performance, it is important to:
- Regularly clean the electrodes to remove any dirt or debris.
- Inspect the cables and connections for any damage.
- Lubricate the moving parts of the welder as per the manufacturer’s instructions.
- Calibrate the welder regularly to ensure accurate welding parameters.
7. What are the different types of electrodes used in electric spot welding and what are their applications?
Different types of electrodes used in electric spot welding include:
- Copper: High electrical and thermal conductivity, good weld quality. Used for welding a wide range of materials.
- Copper alloys: Improved strength and wear resistance compared to pure copper. Used for welding thicker materials and materials with high surface hardness.
- Tungsten: High melting point, good wear resistance. Used for welding materials with high melting points, such as stainless steel and titanium.
- Zirconium: High electrical and thermal conductivity, good weld quality. Used for welding thin materials and materials with low surface hardness.
8. How do you determine the appropriate electrode size and shape for a specific welding application?
To determine the appropriate electrode size and shape for a specific welding application, consider the following factors:
- Material thickness: Thicker materials require larger electrodes.
- Material type: Different materials have different electrical and thermal properties, which can affect the electrode size and shape.
- Weld strength requirements: Stronger welds require larger electrodes.
- Electrode wear: Electrodes wear over time, so it is important to consider the electrode size and shape in relation to the desired weld life.
9. What are the quality control measures used in electric spot welding to ensure weld quality?
Quality control measures used in electric spot welding to ensure weld quality include:
- Weld strength testing: Destructive or non-destructive testing methods to verify the strength of the weld.
- Weld appearance inspection: Visual inspection to check for any defects, such as porosity, spatter, or cracks.
- Microstructure analysis: Microscopic examination of the weld to check for proper grain structure and any defects.
- Process monitoring: Continuous monitoring of welding parameters, such as current, time, and force, to ensure they are within the desired range.
10. How do you stay up-to-date with the latest advancements and best practices in electric spot welding?
To stay up-to-date with the latest advancements and best practices in electric spot welding, it is important to:
- Attend industry conferences and exhibitions.
- Read technical journals and articles.
- Participate in online forums and discussion groups.
- Consult with experts in the field.
Interviewers often ask about specific skills and experiences. With ResumeGemini‘s customizable templates, you can tailor your resume to showcase the skills most relevant to the position, making a powerful first impression. Also check out Resume Template specially tailored for Electric Spot Welder.
Career Expert Tips:
- Ace those interviews! Prepare effectively by reviewing the Top 50 Most Common Interview Questions on ResumeGemini.
- Navigate your job search with confidence! Explore a wide range of Career Tips on ResumeGemini. Learn about common challenges and recommendations to overcome them.
- Craft the perfect resume! Master the Art of Resume Writing with ResumeGemini’s guide. Showcase your unique qualifications and achievements effectively.
- Great Savings With New Year Deals and Discounts! In 2025, boost your job search and build your dream resume with ResumeGemini’s ATS optimized templates.
Researching the company and tailoring your answers is essential. Once you have a clear understanding of the Electric Spot Welder‘s requirements, you can use ResumeGemini to adjust your resume to perfectly match the job description.
Key Job Responsibilities
Electric Spot Welders are responsible for joining metal parts together using electric spot welding machines. Their primary duties include:
1. Equipment Setup and Maintenance
Electric spot welders are responsible for setting up and maintaining electric spot welding machines. This includes tasks such as:
- Inspecting and adjusting welding equipment to ensure proper operation
- Replacing electrodes and other welding consumables
- Troubleshooting and repairing welding equipment
2. Welding Process
Electric spot welders perform the actual welding process. This involves:
- Positioning the metal parts to be welded
- Applying pressure to the parts to hold them in place
- Activating the welding machine to create an electrical arc that welds the parts together
3. Quality Control
Electric spot welders are responsible for ensuring the quality of the welds they produce. This involves tasks such as:
- Visually inspecting welds for defects
- Performing destructive and non-destructive tests to verify weld quality
- Maintaining records of weld quality
4. Safety
Electric spot welders must follow safety procedures to prevent accidents. This includes tasks such as:
- Wearing appropriate safety gear, such as gloves, eye protection, and ear protection
- Following lockout/tagout procedures to prevent accidental machine activation
- Maintaining a clean and organized work area
Interview Tips
Preparing for an interview for an Electric Spot Welder position requires a combination of technical knowledge, industry experience, and effective communication skills. Here are some tips to help you ace the interview:
1. Research the Company and Position
Before the interview, take the time to research the company and the specific position you are applying for. This will help you understand the company’s culture, values, and the specific requirements of the role.
- Visit the company’s website to learn about its products, services, and mission statement.
- Read industry publications and articles to stay up-to-date on the latest welding technologies and best practices.
- Prepare questions to ask the interviewer about the company, the position, and the industry.
2. Highlight Your Skills and Experience
During the interview, be sure to highlight your relevant skills and experience. Employers will be interested in candidates who have a strong understanding of electric spot welding processes and safety procedures.
- Quantify your accomplishments whenever possible. For example, instead of saying “I performed welding tasks,” you could say “I welded over 10,000 parts with a 99% success rate.”
- Be prepared to discuss your experience with different types of welding equipment and materials.
- Emphasize your commitment to safety and quality.
3. Be Enthusiastic and Professional
First impressions matter, so be sure to arrive at the interview on time, dressed professionally, and with a positive attitude. Throughout the interview, maintain eye contact, speak clearly, and be respectful of the interviewer’s time.
- Show your enthusiasm for the position and the company by asking thoughtful questions and listening attentively to the interviewer’s responses.
- Be honest and transparent about your skills and experience. Employers can tell when candidates are being disingenuous.
- Thank the interviewer for their time and consideration at the end of the interview.
4. Practice and Preparation
Practice makes perfect, so take the time to practice answering common interview questions. This will help you feel more confident and prepared during the actual interview.
- Prepare answers to questions about your experience, skills, and why you are interested in the position.
- Practice answering questions about safety procedures and quality control.
- Come prepared with questions to ask the interviewer.
Next Step:
Now that you’re armed with a solid understanding of what it takes to succeed as a Electric Spot Welder, it’s time to turn that knowledge into action. Take a moment to revisit your resume, ensuring it highlights your relevant skills and experiences. Tailor it to reflect the insights you’ve gained from this blog and make it shine with your unique qualifications. Don’t wait for opportunities to come to you—start applying for Electric Spot Welder positions today and take the first step towards your next career milestone. Your dream job is within reach, and with a polished resume and targeted applications, you’ll be well on your way to achieving your career goals! Build your resume now with ResumeGemini.
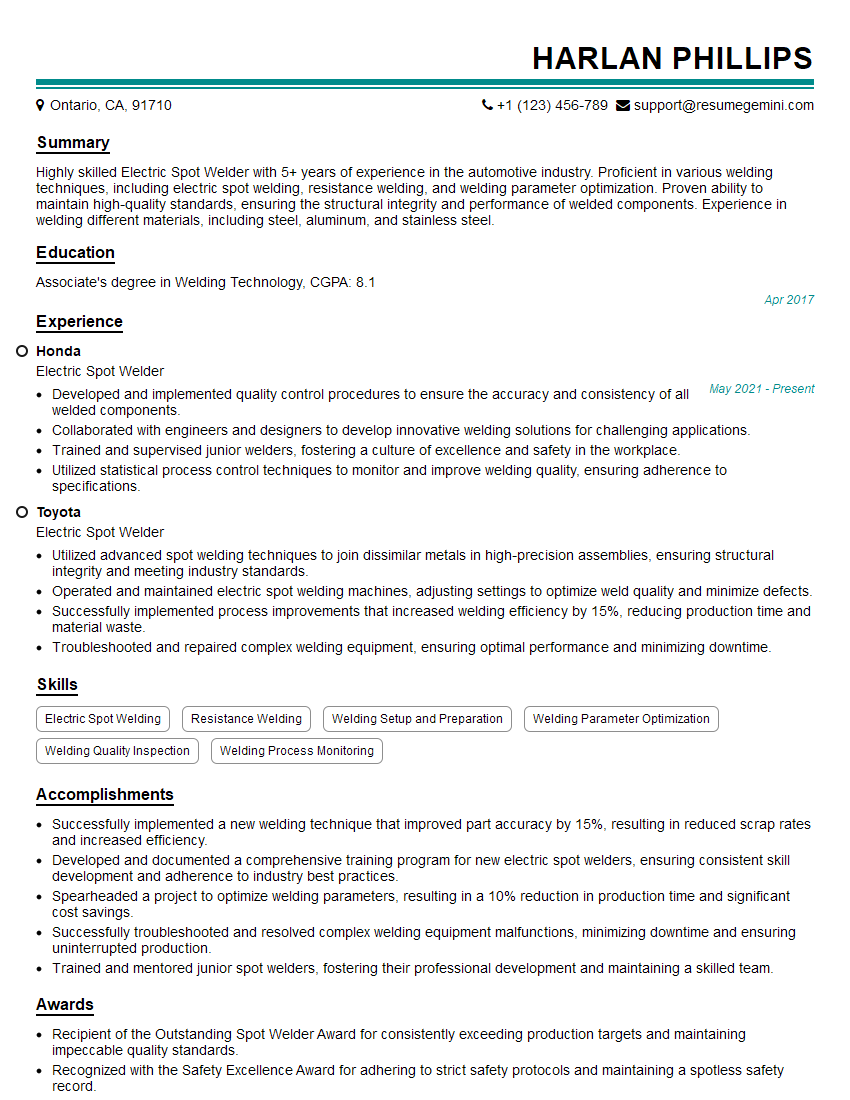