Are you gearing up for a career shift or aiming to ace your next interview? Look no further! We’ve curated a comprehensive guide to help you crack the interview for the coveted Final Assembly and Packing Supervisor position. From understanding the key responsibilities to mastering the most commonly asked questions, this blog has you covered. So, buckle up and let’s embark on this journey together
Acing the interview is crucial, but landing one requires a compelling resume that gets you noticed. Crafting a professional document that highlights your skills and experience is the first step toward interview success. ResumeGemini can help you build a standout resume that gets you called in for that dream job.
Essential Interview Questions For Final Assembly and Packing Supervisor
1. What are the key responsibilities of a Final Assembly and Packing Supervisor?
The key responsibilities of a Final Assembly and Packing Supervisor include:
- Managing and supervising all aspects of final assembly and packing operations, including raw materials storage, line operations, packaging, and shipping
- Ensuring that all products meet quality standards and customer specifications
- Optimizing production processes to improve efficiency and minimize waste
- Training and supervising team members, providing guidance and support
- Monitoring production schedules and ensuring timely delivery of products
2. How do you ensure that products meet quality standards and customer specifications?
To ensure that products meet quality standards and customer specifications, I implement the following measures:
Establish Clear Quality Standards
- Develop and communicate detailed quality standards for all products
- Ensure that all team members are trained on these standards
Implement Quality Control Processes
- Establish regular quality checks at various stages of the assembly and packing process
- Use inspection tools and techniques to identify any defects or non-conformances
Monitor and Improve Quality
- Regularly review quality data and identify areas for improvement
- Implement corrective actions to address quality issues and prevent their recurrence
3. What steps do you take to optimize production processes and improve efficiency?
To optimize production processes and improve efficiency, I take the following steps:
- Analyze existing processes to identify inefficiencies and bottlenecks
- Develop and implement process improvements, such as streamlining workflows and reducing waste
- Introduce automation and technology to enhance productivity and accuracy
- Train and empower team members to continuously seek opportunities for improvement
- Monitor production data and make adjustments as needed to maintain efficiency
4. How do you train and supervise your team effectively?
To train and supervise my team effectively, I follow these principles:
- Provide comprehensive training on all aspects of the job, including product knowledge, assembly procedures, and quality standards
- Establish clear performance expectations and provide regular feedback
- Foster a supportive and collaborative work environment
- Delegate tasks and empower team members to take ownership of their responsibilities
- Monitor team performance and provide coaching and mentoring to help them improve
5. How do you manage production schedules and ensure timely delivery of products?
To manage production schedules and ensure timely delivery of products, I follow these practices:
- Develop realistic production schedules based on customer requirements and available resources
- Monitor production progress closely and make adjustments as needed
- Communicate schedule updates to all stakeholders, including customers, production team, and suppliers
- Identify potential risks and develop contingency plans to mitigate delays
- Collaborate with other departments, such as procurement and logistics, to ensure smooth coordination
6. What experience do you have in lean manufacturing and continuous improvement?
I have extensive experience in lean manufacturing and continuous improvement, and I have implemented these principles successfully in previous roles. Some examples include:
- Developing and implementing a 5S program to improve workplace organization and efficiency
- Using Six Sigma tools to identify and eliminate defects in production processes
- Implementing Kanban systems to optimize inventory management and reduce waste
- Facilitating kaizen events to involve team members in continuous improvement initiatives
- Establishing a culture of continuous improvement where all employees are encouraged to identify and address inefficiencies
7. How do you manage and resolve quality issues effectively?
To manage and resolve quality issues effectively, I follow these steps:
- Identify and investigate quality issues promptly
- Determine the root cause of the issue and develop corrective actions
- Implement corrective actions and monitor their effectiveness
- Communicate quality issues and corrective actions to the appropriate stakeholders
- Use data analysis and quality reports to identify trends and make informed decisions
8. How do you ensure that products are packaged and shipped in accordance with customer requirements and industry standards?
To ensure that products are packaged and shipped in accordance with customer requirements and industry standards, I implement the following measures:
- Develop and maintain packaging specifications that meet customer requirements and industry regulations
- Inspect incoming packaging materials to verify their quality and compliance
- Train and supervise packaging team members on proper packaging techniques
- Monitor packaging operations to ensure that products are packaged correctly and securely
- Coordinate with shipping carriers to ensure proper handling and delivery of products
9. How do you handle production emergencies and unexpected events?
In the event of production emergencies or unexpected events, I follow these steps:
- Assess the situation promptly and identify potential risks
- Communicate with the appropriate stakeholders, including management, team members, and customers
- Develop and implement contingency plans to minimize the impact of the event
- Monitor the situation closely and make adjustments as needed
- Follow up after the event to evaluate the response and identify areas for improvement
10. What is your approach to safety in the workplace?
I prioritize safety in the workplace by:
- Establishing and enforcing clear safety policies and procedures
- Providing comprehensive safety training to all team members
- Conducting regular safety inspections and audits
- Encouraging employees to report any potential hazards or concerns
- Investigating and addressing all safety incidents promptly
Interviewers often ask about specific skills and experiences. With ResumeGemini‘s customizable templates, you can tailor your resume to showcase the skills most relevant to the position, making a powerful first impression. Also check out Resume Template specially tailored for Final Assembly and Packing Supervisor.
Career Expert Tips:
- Ace those interviews! Prepare effectively by reviewing the Top 50 Most Common Interview Questions on ResumeGemini.
- Navigate your job search with confidence! Explore a wide range of Career Tips on ResumeGemini. Learn about common challenges and recommendations to overcome them.
- Craft the perfect resume! Master the Art of Resume Writing with ResumeGemini’s guide. Showcase your unique qualifications and achievements effectively.
- Great Savings With New Year Deals and Discounts! In 2025, boost your job search and build your dream resume with ResumeGemini’s ATS optimized templates.
Researching the company and tailoring your answers is essential. Once you have a clear understanding of the Final Assembly and Packing Supervisor‘s requirements, you can use ResumeGemini to adjust your resume to perfectly match the job description.
Key Job Responsibilities
A Final Assembly and Packing Supervisor is responsible for overseeing and managing the final assembly and packing operations within a manufacturing or distribution environment. They play a crucial role in ensuring the timely and efficient production and distribution of finished goods, while adhering to quality and safety standards.
1. Production Management
Supervising and coordinating the final assembly process, including the allocation of tasks, monitoring progress, and identifying and resolving bottlenecks.
- Developing and implementing production schedules to optimize efficiency and meet deadlines.
- Ensuring that all assembly operations are performed in accordance with established procedures and quality standards.
2. Quality Control
Maintaining and enforcing quality standards throughout the final assembly and packing process.
- Conducting regular inspections and audits to ensure that assembled products meet specifications.
- Identifying and addressing non-conformances and implementing corrective actions.
3. Team Management
Leading and motivating a team of assembly and packing personnel.
- Providing clear instructions and guidance to team members.
- Monitoring performance, providing feedback, and recognizing achievements.
4. Inventory Management
Monitoring and managing inventory levels of raw materials, components, and finished goods.
- Coordinating with suppliers to ensure timely delivery of materials.
- Implementing inventory control systems to prevent shortages or overstocking.
Interview Tips
Preparing thoroughly for an interview can significantly increase your chances of success. Here are some tips and tricks to help you ace your interview for a Final Assembly and Packing Supervisor position:
1. Research the Company and Position
Take the time to research the company and the specific role you are applying for. Familiarize yourself with their products or services, industry standing, and company culture. This will demonstrate your interest in the opportunity and help you tailor your answers to the company’s needs.
2. Highlight Relevant Experience
Emphasize your relevant experience and skills that align with the job requirements. Quantify your accomplishments whenever possible, using specific examples and metrics to demonstrate your impact. Showcase your ability to manage teams, optimize processes, and ensure quality.
3. Practice Common Interview Questions
Prepare for common interview questions by rehearsing your answers. Anticipate questions about your experience, qualifications, and how you would approach various scenarios in the role. Practice answering questions confidently and succinctly.
4. Be Enthusiastic and Professional
Throughout the interview, maintain a positive and enthusiastic attitude. Show that you are genuinely interested in the position and the company. Dress professionally and arrive on time for your interview to convey a sense of respect and commitment.
5. Ask Thoughtful Questions
At the end of the interview, ask thoughtful questions about the role, the company, and the industry. This demonstrates your engagement and interest in the opportunity. It also provides you with an opportunity to clarify any details or gain additional insights.
Next Step:
Now that you’re armed with the knowledge of Final Assembly and Packing Supervisor interview questions and responsibilities, it’s time to take the next step. Build or refine your resume to highlight your skills and experiences that align with this role. Don’t be afraid to tailor your resume to each specific job application. Finally, start applying for Final Assembly and Packing Supervisor positions with confidence. Remember, preparation is key, and with the right approach, you’ll be well on your way to landing your dream job. Build an amazing resume with ResumeGemini
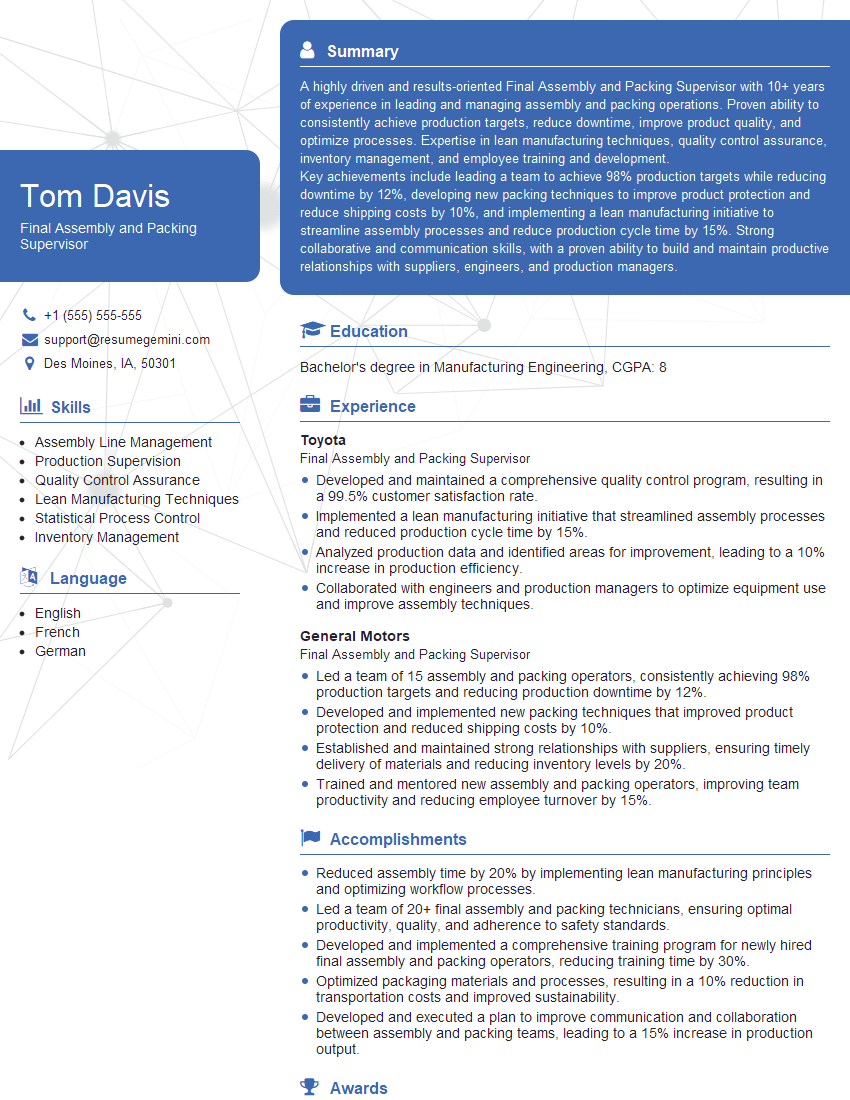