Ever felt underprepared for that crucial job interview? Or perhaps you’ve landed the interview but struggled to articulate your skills and experiences effectively? Fear not! We’ve got you covered. In this blog post, we’re diving deep into the Flat Machine Cutter interview questions that you’re most likely to encounter. But that’s not all. We’ll also provide expert insights into the key responsibilities of a Flat Machine Cutter so you can tailor your answers to impress potential employers.
Acing the interview is crucial, but landing one requires a compelling resume that gets you noticed. Crafting a professional document that highlights your skills and experience is the first step toward interview success. ResumeGemini can help you build a standout resume that gets you called in for that dream job.
Essential Interview Questions For Flat Machine Cutter
1. Describe the process of setting up a flat machine cutter, including the different types of materials that can be cut and the factors to consider when selecting a blade.
The process of setting up a flat machine cutter involves several steps:
- Mounting the material: The material to be cut is placed on the cutting table and secured using clamps or a vacuum system.
- Positioning the blade: The blade is positioned over the material, and its height and angle are adjusted to suit the material’s thickness and the desired cut quality.
- Selecting the cutting parameters: The cutting speed, feed rate, and other parameters are set based on the material’s properties and the desired cut quality.
Different types of materials that can be cut with a flat machine cutter include:
- Paper and cardboard: These materials are commonly cut for packaging, printing, and signage applications.
- Textiles and fabrics: These materials are cut for clothing, upholstery, and other textile products.
- Plastics and composite materials: These materials are used in various industries, including automotive, aerospace, and construction.
When selecting a blade for a flat machine cutter, several factors should be considered:
- Material thickness: The blade’s thickness should be appropriate for the thickness of the material being cut.
- Material hardness: Harder materials require blades with a sharper cutting edge.
- Cut quality: The blade’s sharpness and geometry affect the quality of the cut, including the smoothness and precision.
2. How do you ensure the accuracy and precision of cuts made with a flat machine cutter?
Calibration and maintenance
- Regularly calibrate the machine to ensure its accuracy and minimize errors.
- Maintain the machine’s components, including the blade, cutting table, and drive system, to prevent wear and ensure optimal performance.
Material handling
- Handle materials carefully to avoid deformation or damage that could affect cut accuracy.
- Secure materials firmly on the cutting table to prevent movement during cutting.
Cutting parameters
- Select the appropriate cutting speed, feed rate, and other parameters based on the material being cut.
- Use sharp blades and replace them regularly to maintain cutting accuracy.
3. What techniques can be used to minimize waste and optimize material utilization when cutting with a flat machine cutter?
- Nesting: Arrange the cutting patterns on the material in a way that minimizes wasted space.
- Common-line cutting: Cut multiple layers of material simultaneously along common lines to reduce material waste.
- Remnant utilization: Use leftover material from previous cuts for smaller parts or other applications.
- Material optimization software: Utilize software tools to automatically optimize cutting patterns and minimize waste.
4. How do you troubleshoot common problems that occur when operating a flat machine cutter, such as blade breakage or material tearing?
- Blade breakage: Check the blade for damage or dullness, and replace it if necessary. Ensure the blade is properly installed and tightened.
- Material tearing: Adjust the cutting speed and feed rate to suit the material’s properties. Use a sharp blade and ensure the material is securely held in place.
- Other problems: Consult the machine’s manual or contact the manufacturer for assistance in troubleshooting and resolving specific issues.
5. Describe the safety precautions that must be taken when operating a flat machine cutter.
- Wear appropriate safety gear, including gloves, safety glasses, and ear protection.
- Keep hands and other body parts away from the cutting blade.
- Ensure the machine is properly grounded and the electrical connections are secure.
- Follow the manufacturer’s instructions for safe operation and maintenance.
- Be aware of the machine’s potential hazards, such as sharp edges and moving parts.
6. How do you maintain a flat machine cutter to ensure its longevity and optimal performance?
- Regular cleaning: Remove dust, debris, and material residue from the machine’s components.
- Blade maintenance: Sharpen or replace the blade as needed to maintain cutting accuracy.
- Lubrication: Lubricate moving parts according to the manufacturer’s recommendations.
- Electrical maintenance: Inspect electrical connections and wiring for damage or loose contacts.
- Preventive maintenance: Perform regular inspections and maintenance tasks to prevent potential problems.
7. Explain the different types of cutting tools used in a flat machine cutter and their applications.
- Straight blades: Used for straight cuts and can be adjusted for different cutting depths.
- Circular blades: Used for cutting curves and circles, with various diameters available.
- Oscillating knives: Used for cutting intricate shapes and can follow complex contours.
- Drag knives: Used for cutting thick materials, providing a clean and precise cut.
- Laser cutting heads: Used for non-contact cutting of various materials, offering high precision and speed.
8. Describe the process of creating and optimizing cutting patterns for a flat machine cutter.
- Design: Use CAD software to create the cutting patterns, ensuring they meet the required specifications.
- Nesting: Optimize the placement of patterns on the material to minimize waste and maximize material utilization.
- Tool selection: Choose the appropriate cutting tool based on the material and the desired cut quality.
- Parameter optimization: Adjust cutting parameters such as speed and pressure to achieve the best results for the specific material.
- Testing and refinement: Cut sample pieces to evaluate the patterns and make any necessary adjustments for accuracy and efficiency.
9. How do you ensure the quality of cuts made with a flat machine cutter and assess the accuracy of the finished products?
- Visual inspection: Examine the cut edges for smoothness, precision, and absence of defects.
- Dimensional measurement: Use measuring tools such as calipers or a CMM (Coordinate Measuring Machine) to verify the dimensions of the cut pieces.
- Functional testing: Test the finished products to ensure they meet the required specifications and perform as intended.
- Process monitoring: Regularly check the machine’s performance and adjust parameters as needed to maintain consistent cutting quality.
- Quality control procedures: Implement quality control measures to identify and address potential issues before they affect production.
10. Explain how you would troubleshoot and resolve common issues that arise during the operation of a flat machine cutter.
- Blade problems: Dull or damaged blades can affect cut quality. Replace or sharpen the blades as needed.
- Material handling issues: Improper material handling can lead to inaccurate cuts. Ensure the material is securely held in place and adjust the cutting parameters accordingly.
- Machine malfunctions: Electrical or mechanical issues can cause the machine to malfunction. Check for loose connections, damaged components, or software errors.
- Software problems: Cutting patterns or parameter settings can cause cutting errors. Verify the software settings and make any necessary adjustments.
- Environmental factors: Temperature and humidity can affect the cutting process. Adjust the machine settings or consider using materials that are less sensitive to environmental conditions.
Interviewers often ask about specific skills and experiences. With ResumeGemini‘s customizable templates, you can tailor your resume to showcase the skills most relevant to the position, making a powerful first impression. Also check out Resume Template specially tailored for Flat Machine Cutter.
Career Expert Tips:
- Ace those interviews! Prepare effectively by reviewing the Top 50 Most Common Interview Questions on ResumeGemini.
- Navigate your job search with confidence! Explore a wide range of Career Tips on ResumeGemini. Learn about common challenges and recommendations to overcome them.
- Craft the perfect resume! Master the Art of Resume Writing with ResumeGemini’s guide. Showcase your unique qualifications and achievements effectively.
- Great Savings With New Year Deals and Discounts! In 2025, boost your job search and build your dream resume with ResumeGemini’s ATS optimized templates.
Researching the company and tailoring your answers is essential. Once you have a clear understanding of the Flat Machine Cutter‘s requirements, you can use ResumeGemini to adjust your resume to perfectly match the job description.
Key Job Responsibilities
The Flat Machine Cutter is an integral part of the manufacturing process, operating large cutting machines to cut various materials into specific shapes and sizes. Their precision and attention to detail are crucial for ensuring the accuracy and quality of finished products.
1. Machine Operation and Calibration
Expertly operate flat cutting machines to efficiently cut materials like fabrics, leather, foam, and other substrates.
- Execute cutting plans and specifications, meticulously following instructions to produce precise cuts.
- Monitor and calibrate cutting machines to maintain optimal performance, minimizing downtime and ensuring consistent quality.
2. Material Handling and Preparation
Handle and prepare materials with care to achieve desired cutting results.
- Prepare materials by spreading, aligning, and securing them on the cutting bed, ensuring proper positioning and stability.
- Inspect materials for defects or imperfections before cutting to prevent errors and maintain product quality.
3. Quality Control and Inspection
Thoroughly inspect cut materials to ensure they meet specifications and quality standards.
- Measure and verify dimensions, shapes, and details of cut pieces, using measuring tools and templates.
- Identify and rectify any discrepancies or defects in cut materials, maintaining consistent product quality and minimizing waste.
4. Production Optimization and Efficiency
Continuously seek ways to improve production efficiency and optimize machine performance.
- Collaborate with team members to identify bottlenecks and develop solutions for smoother workflow.
- Stay updated on industry advancements and cutting techniques to enhance productivity and quality.
Interview Tips
To ace your Flat Machine Cutter interview, thorough preparation is key. Here are some tips to help you stand out:
1. Research the Role and Company
Take the time to thoroughly research the job description and the company’s background, values, and industry standing.
- Identify the specific skills and responsibilities required for the role and tailor your answers accordingly.
- Showcase your knowledge of the company’s products, services, and industry reputation.
2. Practice Your Answers
Prepare your answers to common interview questions, especially those related to your technical skills, experience, and problem-solving abilities.
- Use the STAR method (Situation, Task, Action, Result) to structure your answers, providing specific examples that highlight your capabilities.
- Practice your answers out loud or with a friend or family member to gain confidence and fluency.
3. Emphasize Your Attention to Detail
Accuracy and precision are crucial for Flat Machine Cutters. Clearly communicate your meticulous nature and unwavering focus on quality.
- Highlight your ability to follow instructions precisely and execute cutting tasks with utmost precision.
- Share examples of how you have maintained high levels of accuracy and consistency in previous roles.
4. Showcase Your Problem-Solving Skills
Unexpected situations can arise in manufacturing, so demonstrating your problem-solving abilities is essential.
- Describe instances where you encountered challenges or machine malfunctions and how you effectively resolved them.
- Emphasize your logical thinking, analytical skills, and ability to find innovative solutions.
5. Prepare Relevant Questions
Asking thoughtful questions at the end of the interview shows your engagement and interest in the position.
- Prepare questions about the company’s growth plans, industry trends, or opportunities for professional development.
- These questions demonstrate your enthusiasm and commitment to the role and the organization.
Next Step:
Armed with this knowledge, you’re now well-equipped to tackle the Flat Machine Cutter interview with confidence. Remember, preparation is key. So, start crafting your resume, highlighting your relevant skills and experiences. Don’t be afraid to tailor your application to each specific job posting. With the right approach and a bit of practice, you’ll be well on your way to landing your dream job. Build your resume now from scratch or optimize your existing resume with ResumeGemini. Wish you luck in your career journey!
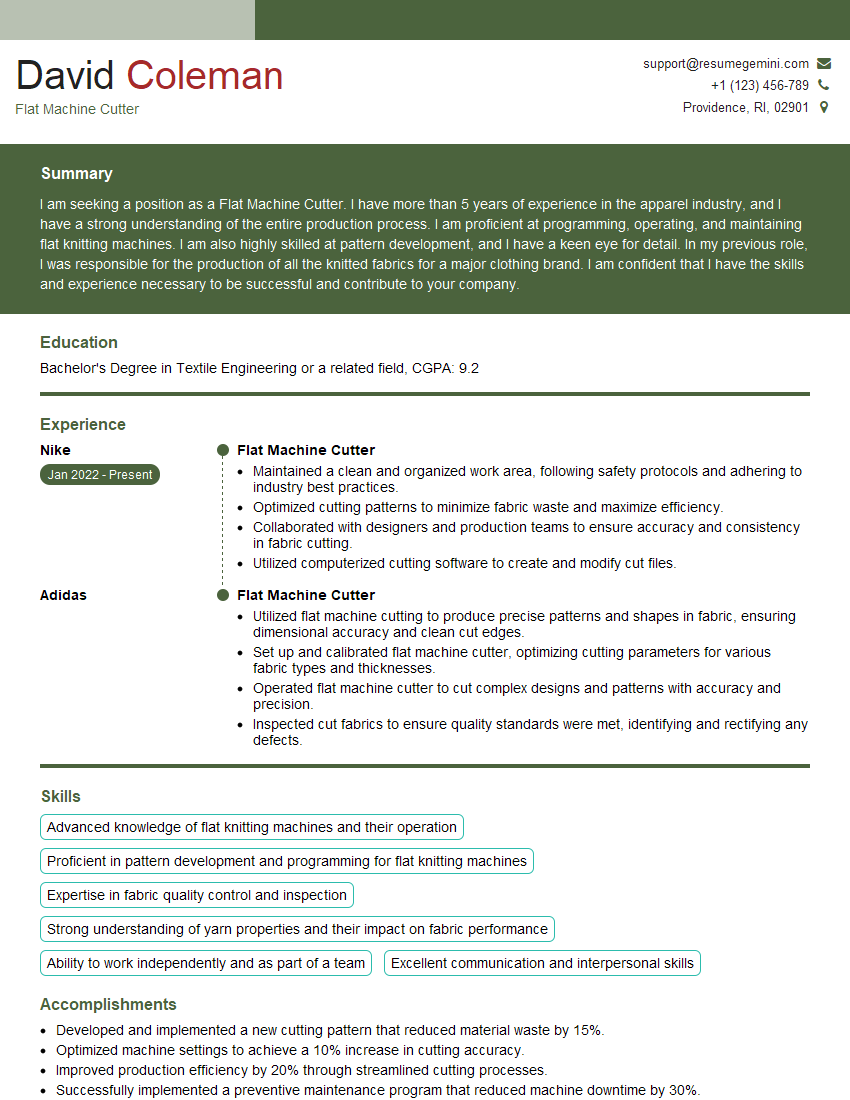