Are you gearing up for a career in Foundry Molder? Feeling nervous about the interview questions that might come your way? Don’t worry, you’re in the right place. In this blog post, we’ll dive deep into the most common interview questions for Foundry Molder and provide you with expert-backed answers. We’ll also explore the key responsibilities of this role so you can tailor your responses to showcase your perfect fit.
Acing the interview is crucial, but landing one requires a compelling resume that gets you noticed. Crafting a professional document that highlights your skills and experience is the first step toward interview success. ResumeGemini can help you build a standout resume that gets you called in for that dream job.
Essential Interview Questions For Foundry Molder
1. What are the key steps involved in the sand casting process?
- Pattern making: Creating a replica of the desired object from wood, metal, plastic, or other materials.
- Mold making: Preparing the sand by mixing it with water and binders to create a mold that will hold the molten metal.
- Pouring: Filling the mold with molten metal.
- Solidification: Allowing the metal to cool and solidify within the mold.
- Shakeout: Removing the solidified casting from the sand mold.
- Finishing: Cleaning and finishing the casting to remove any excess material or imperfections.
2. Describe the different types of sand used in foundry molding.
Green sand
- Mixture of silica sand, clay, and water.
- Strong and durable, holds its shape well.
- Used for large and heavy castings.
Dry sand
- Silica sand without clay or water.
- Weak and less durable than green sand.
- Used for small and delicate castings.
Chemical sand
- Silica sand bonded with chemical binders.
- Very strong and durable, can withstand high temperatures.
- Used for castings that require dimensional accuracy.
3. Explain the purpose and operation of a gating system in sand casting.
- To provide a controlled flow of molten metal into the mold cavity.
- Consists of a sprue, runners, and gates.
- Sprue connects the pouring basin to the runners.
- Runners distribute the metal to the gates.
- Gates allow the metal to enter the mold cavity.
4. What are the common defects that can occur in sand castings and how can they be prevented?
- Blowholes: Caused by trapped air or gas in the mold. Prevented by venting the mold and using vacuum degassing techniques.
- Cold shuts: Incomplete fusion of metal surfaces. Prevented by ensuring sufficient metal fluidity and mold preheating.
- Cracks: Fractures in the casting. Prevented by using proper gating and risering techniques, and avoiding sudden cooling.
- Dimensional inaccuracies: Deviations from desired dimensions. Prevented by using precision patterns, molds, and casting techniques.
- Shrinkage cavities: Voids caused by metal contraction during cooling. Prevented by using risers or chillers to promote directional solidification.
5. Describe the role of risers in sand casting.
- Reservoirs of molten metal that feed metal to the casting as it solidifies and shrinks.
- Prevent the formation of shrinkage cavities.
- Located in areas where solidification occurs last.
- Properly sized and positioned to ensure adequate feeding of metal.
6. What are the techniques used to produce investment castings?
Lost-wax casting
- Creating a wax pattern of the desired object.
- Investing the wax pattern in a ceramic slurry.
- Melting and removing the wax, leaving a ceramic mold.
- Pouring molten metal into the ceramic mold.
Shell molding
- Creating a metal pattern of the desired object.
- Coating the pattern with a refractory material.
- Heating the coated pattern, causing the refractory material to harden into a shell mold.
- Pouring molten metal into the shell mold.
7. Explain the difference between permanent mold casting and die casting.
Permanent mold casting
- Uses reusable metal molds.
- Molten metal is poured into the mold.
- Lower pressure and slower cooling than die casting.
- Produces castings with good surface finish and dimensional accuracy.
Die casting
- Uses permanent metal dies that are forced together under high pressure.
- Molten metal is injected into the dies.
- Rapid cooling and high pressure result in castings with excellent surface finish and dimensional accuracy.
- Suitable for high-volume production of small and intricate parts.
8. What safety precautions are essential in a foundry environment?
- Wearing appropriate personal protective equipment (PPE), such as gloves, safety glasses, and respirators.
- Handling molten metal with caution, using tongs or other protective tools.
- Ventilating the foundry to avoid exposure to fumes and gases.
- Maintaining a clean and organized work area.
- Following established safety procedures and protocols.
9. Describe the different types of melting furnaces used in foundries.
Electric arc furnace
- Uses an electric arc to generate heat.
- Can melt various metals, including ferrous and non-ferrous.
- Provides precise temperature control.
Induction furnace
- Uses electromagnetic induction to generate heat.
- Can melt ferrous metals.
- Provides fast melting and precise temperature control.
Cupola furnace
- Burns coke to generate heat.
- Used to melt ferrous metals, primarily iron.
- Continuous melting process.
10. Explain the role of slag in the foundry process.
- Flux added to the molten metal to form a floating layer on top.
- Protects the molten metal from oxidation and contamination.
- Promotes the removal of impurities and gases from the metal.
- Helps regulate metal temperature.
Interviewers often ask about specific skills and experiences. With ResumeGemini‘s customizable templates, you can tailor your resume to showcase the skills most relevant to the position, making a powerful first impression. Also check out Resume Template specially tailored for Foundry Molder.
Career Expert Tips:
- Ace those interviews! Prepare effectively by reviewing the Top 50 Most Common Interview Questions on ResumeGemini.
- Navigate your job search with confidence! Explore a wide range of Career Tips on ResumeGemini. Learn about common challenges and recommendations to overcome them.
- Craft the perfect resume! Master the Art of Resume Writing with ResumeGemini’s guide. Showcase your unique qualifications and achievements effectively.
- Great Savings With New Year Deals and Discounts! In 2025, boost your job search and build your dream resume with ResumeGemini’s ATS optimized templates.
Researching the company and tailoring your answers is essential. Once you have a clear understanding of the Foundry Molder‘s requirements, you can use ResumeGemini to adjust your resume to perfectly match the job description.
Key Job Responsibilities
Foundry Molders are skilled individuals who play a vital role in the production process of metal castings. They are responsible for setting up and operating molding machines, and ensuring the proper quality of the molds produced.
Key job responsibilities of a Foundry Molder include:
1. Mold Making
Molders create molds by packing sand around a pattern, or model, of the desired casting. They must ensure that the sand is packed tightly and evenly to prevent defects in the final casting. Once the mold is complete, it is removed from the pattern and prepared for casting.
- Create molds using a variety of materials, including sand, metal, and plaster.
- Operate molding machines to pack sand around patterns.
- Inspect molds for defects and make necessary repairs.
2. Casting
Molders pour molten metal into the mold and allow it to cool and solidify. They must carefully control the temperature of the metal and the cooling process to ensure that the casting is of the desired quality.
- Pour molten metal into molds.
- Control the temperature of the metal and the cooling process.
- Remove castings from molds.
3. Finishing
Molders remove the castings from the molds and perform finishing operations, such as grinding, polishing, and painting. They must inspect the castings for defects and make any necessary repairs.
- Grind, polish, and paint castings.
- Inspect castings for defects.
- Make necessary repairs to castings.
4. Maintenance
Molders are responsible for maintaining their equipment and work area. They must keep their machines clean and in good working order, and ensure that the work area is safe and free of hazards.
- Maintain equipment and work area.
- Keep machines clean and in good working order.
- Ensure that the work area is safe and free of hazards.
Interview Tips
Interviewing for a Foundry Molder position can be a daunting task, but with the right preparation, you can increase your chances of success. Here are some interview tips and hacks to help you ace the interview:
1. Research the Company
Before you go on an interview, it is important to research the company. This will help you understand the company’s culture, values, and goals. You can learn about the company by visiting their website, reading their press releases, and talking to people who work there.
- Visit the company’s website.
- Read the company’s press releases.
- Talk to people who work at the company.
2. Practice Your Answers
Once you have researched the company, you should practice your answers to common interview questions. This will help you feel more confident and prepared during the interview.
- Practice answering common interview questions.
- Use the STAR method to answer behavioral questions.
- Be prepared to talk about your skills and experience.
3. Dress Professionally
First impressions matter, so it is important to dress professionally for your interview. This means wearing a suit or business casual attire.
4. Be Yourself
It is important to be yourself during the interview. The interviewer wants to get to know the real you, so don’t try to be someone you’re not.
5. Ask Questions
At the end of the interview, be sure to ask the interviewer questions. This shows that you are interested in the position and that you have taken the interview seriously. Here are some good questions to ask:
- What are the biggest challenges facing the company right now?
- What are the company’s goals for the next year?
- What is the company culture like?
- What is the next step in the hiring process?
Next Step:
Now that you’re armed with interview-winning answers and a deeper understanding of the Foundry Molder role, it’s time to take action! Does your resume accurately reflect your skills and experience for this position? If not, head over to ResumeGemini. Here, you’ll find all the tools and tips to craft a resume that gets noticed. Don’t let a weak resume hold you back from landing your dream job. Polish your resume, hit the “Build Your Resume” button, and watch your career take off! Remember, preparation is key, and ResumeGemini is your partner in interview success.
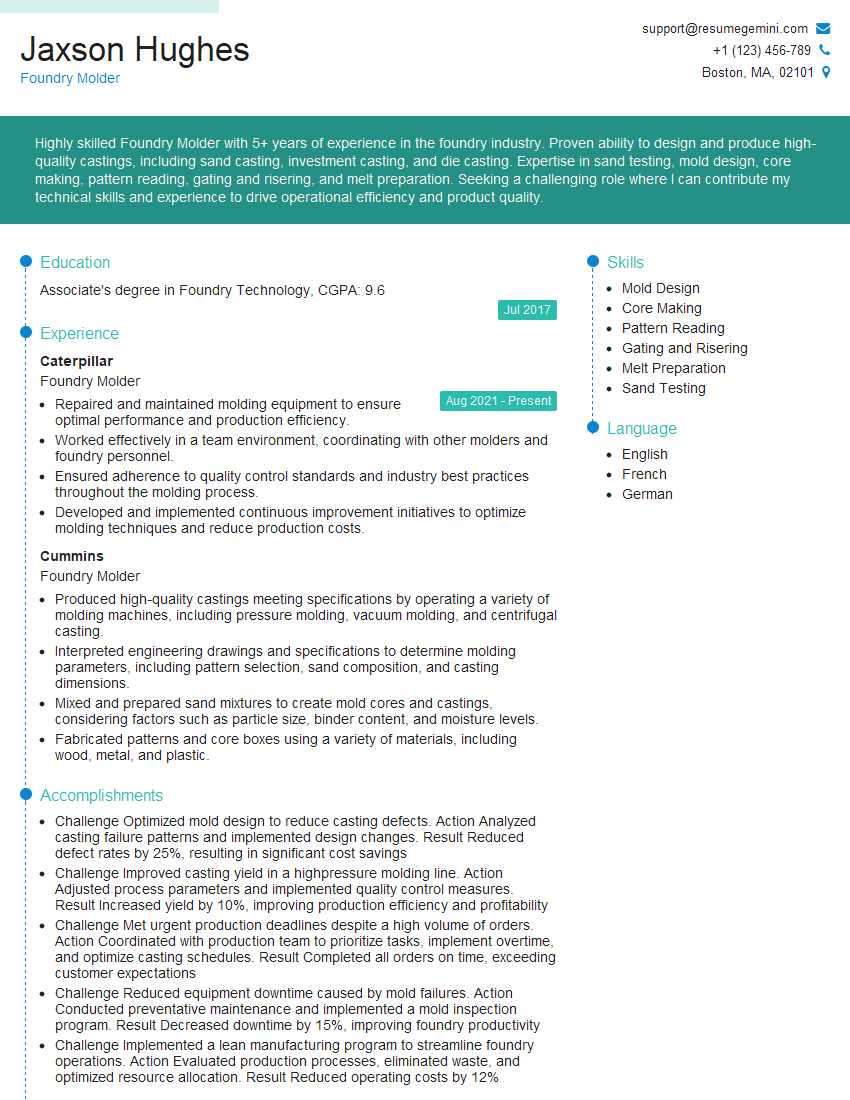