Feeling lost in a sea of interview questions? Landed that dream interview for Gear Milling Machine Set-Up Operator but worried you might not have the answers? You’re not alone! This blog is your guide for interview success. We’ll break down the most common Gear Milling Machine Set-Up Operator interview questions, providing insightful answers and tips to leave a lasting impression. Plus, we’ll delve into the key responsibilities of this exciting role, so you can walk into your interview feeling confident and prepared.
Acing the interview is crucial, but landing one requires a compelling resume that gets you noticed. Crafting a professional document that highlights your skills and experience is the first step toward interview success. ResumeGemini can help you build a standout resume that gets you called in for that dream job.
Essential Interview Questions For Gear Milling Machine Set-Up Operator
1. Explain the process of setting up a gear milling machine?
The process of setting up a gear milling machine involves several steps:
- Mount the workpiece: Secure the workpiece to the machine table using clamps or a fixture.
- Select and install the cutter: Choose the appropriate cutter based on the desired gear specifications and mount it on the machine spindle.
- Set the machine parameters: Enter the necessary parameters into the machine’s control system, including spindle speed, feed rate, and depth of cut.
- Calibrate the machine: Check the machine’s accuracy by running a test cut and making any necessary adjustments.
- Load the program: Transfer the CNC program containing the gear cutting instructions into the machine’s control system.
2. What are the different types of gear milling cutters, and when should each type be used?
Types of Gear Milling Cutters:
- Involute Gear Cutters: Most common type, used for cutting spur and helical gears.
- Straight-sided Gear Cutters: Used for cutting gears with straight-sided teeth, such as racks and pinions.
- Hobbing Cutters: Used for cutting gears by a single-point cutting action, suitable for high-volume production.
- Shaper Cutters: Used for cutting gears with complex tooth profiles or for gear repair.
When to Use Each Type:
- Involute Gear Cutters: General purpose, suitable for most gear cutting applications.
- Straight-sided Gear Cutters: For gears with straight teeth, such as in rack-and-pinion systems.
- Hobbing Cutters: For high-volume production of precision gears.
- Shaper Cutters: For specialized gear profiles or gear repair.
3. How do you ensure the accuracy of the gears produced on a gear milling machine?
Ensuring accuracy in gear milling involves several key practices:
- Proper Machine Setup: Calibrating the machine and verifying its accuracy before cutting.
- Precision Cutting Tools: Using high-quality cutters with sharp cutting edges.
- Accurate Part Fixturing: Securing the workpiece securely to prevent movement during cutting.
- Optimal Cutting Conditions: Setting appropriate spindle speeds, feed rates, and depths of cut.
- Regular Inspection and Measurement: Checking the gears during and after cutting using precision measuring instruments.
- Temperature Control: Maintaining stable temperature conditions to prevent thermal expansion and contraction.
4. Describe the different types of gear inspection methods and their applications?
- Involute Profile Inspection: Using a coordinate measuring machine (CMM) or gear measuring machine to verify the tooth profile.
- Lead and Helix Inspection: Measuring the lead and helix angles of the teeth using specialized gauges or CMMs.
- Runout Inspection: Checking the concentricity and parallelism of the gear teeth using a runout gauge.
- Composite Inspection: Combining multiple inspection methods to provide a comprehensive analysis of the gear’s accuracy.
5. What are the common problems encountered when operating a gear milling machine, and how do you troubleshoot them?
Common Problems:
- Chattering: Excessive vibration due to improper machine setup or dull cutters.
- Tool Breakage: Overloading the machine or using worn-out cutters.
- Inaccurate Gear Profiles: Incorrect cutter selection, improper machine calibration, or thermal expansion.
- Poor Surface Finish: Dull cutters, incorrect cutting parameters, or vibration.
Troubleshooting:
- Chattering: Check machine setup, cutter sharpness, and cutting parameters.
- Tool Breakage: Replace worn cutters, adjust cutting parameters, and check for workpiece stability.
- Inaccurate Gear Profiles: Verify cutter selection, machine calibration, and temperature stability.
- Poor Surface Finish: Replace dull cutters, adjust cutting parameters, and minimize vibration.
6. Explain the importance of coolant in gear milling operations?
Coolant in gear milling serves several critical purposes:
- Lubrication: Reduces friction between the cutter and workpiece, preventing overheating and premature tool wear.
- Cooling: Dissipates heat generated during cutting, preventing thermal distortion and ensuring accuracy.
- Chip Removal: Flushes away chips from the cutting zone, improving surface finish and preventing tool clogging.
- Corrosion Protection: Protects the workpiece and machine components from corrosion.
7. How do you calculate the cutting speed and feed rate for gear milling?
Cutting Speed:
- V = (π × D × N) / 1000
- Where:
- V = Cutting speed (m/min)
- D = Cutter diameter (mm)
- N = Spindle speed (rpm)
Feed Rate:
- F = (Z × N × P) / 1000
- Where:
- F = Feed rate (mm/min)
- Z = Number of teeth on the cutter
- N = Spindle speed (rpm)
- P = Pitch of the gear teeth (mm)
8. Describe the different types of gear materials and their applications?
- Steel: Common material for gears due to its strength, durability, and wear resistance.
- Stainless Steel: Used in corrosive environments or for applications requiring high resistance to rust.
- Bronze: Suitable for low-load applications where wear resistance and noise reduction are important.
- Aluminum: Lightweight material used in applications where weight reduction is crucial.
- Plastic: Used for gears in low-torque applications, such as toys or consumer electronics.
9. Explain the safety protocols associated with operating a gear milling machine?
- Wear appropriate safety gear: Including safety glasses, gloves, and hearing protection.
- Keep the work area clean and organized: To prevent tripping hazards.
- Inspect the machine and tools before use: To ensure they are in good working order.
- Secure the workpiece properly: To prevent it from becoming loose during cutting.
- Never operate the machine while under the influence of drugs or alcohol: To maintain alertness and safety.
10. How do you stay updated on the latest advancements in gear milling technology?
- Attend industry conferences and exhibitions: To learn about new products and techniques.
- Subscribe to industry publications and newsletters: To stay informed about the latest advancements.
- Network with other professionals in the field: To share knowledge and experiences.
- Participate in training and certification programs: To enhance skills and keep up with industry best practices.
Interviewers often ask about specific skills and experiences. With ResumeGemini‘s customizable templates, you can tailor your resume to showcase the skills most relevant to the position, making a powerful first impression. Also check out Resume Template specially tailored for Gear Milling Machine Set-Up Operator.
Career Expert Tips:
- Ace those interviews! Prepare effectively by reviewing the Top 50 Most Common Interview Questions on ResumeGemini.
- Navigate your job search with confidence! Explore a wide range of Career Tips on ResumeGemini. Learn about common challenges and recommendations to overcome them.
- Craft the perfect resume! Master the Art of Resume Writing with ResumeGemini’s guide. Showcase your unique qualifications and achievements effectively.
- Great Savings With New Year Deals and Discounts! In 2025, boost your job search and build your dream resume with ResumeGemini’s ATS optimized templates.
Researching the company and tailoring your answers is essential. Once you have a clear understanding of the Gear Milling Machine Set-Up Operator‘s requirements, you can use ResumeGemini to adjust your resume to perfectly match the job description.
Key Job Responsibilities
Gear Milling Machine Set-Up Operators play a crucial role in the manufacturing industry, ensuring the smooth operation and accuracy of gear milling machines. Their key responsibilities encompass:
1. Machine Set-Up and Calibration
Setting up and calibrating gear milling machines according to specifications, including tool selection, spindle speed, and feed rates.
2. Tool Inspection and Maintenance
Inspecting and maintaining cutting tools, ensuring they are sharp and in proper working condition to achieve precise gear profiles.
3. Fixture Design and Installation
Designing and installing fixtures to hold workpieces securely during the milling process, ensuring accurate positioning and stability.
4. Workpiece Measurement and Inspection
Measuring and inspecting workpieces using precision instruments, such as calipers and micrometers, to verify conformance to specifications.
5. Troubleshooting and Maintenance
Identifying and resolving machine malfunctions, performing routine maintenance tasks, and adhering to safety protocols to minimize downtime.
Interview Tips
To ace an interview for a Gear Milling Machine Set-Up Operator position, candidates can leverage the following tips:
1. Research the Company and Position
Thoroughly research the company, its industry, and the specific role to demonstrate a genuine interest and understanding of the organization’s objectives.
2. Highlight Relevant Skills and Experience
Emphasize your technical expertise in gear milling, including knowledge of machine operation, tool selection, and precision measurement techniques. Showcase previous experience in similar roles or any relevant training.
3. Prepare for Technical Questions
Anticipate technical questions related to gear milling principles, machine components, and troubleshooting procedures. Practice answering these questions clearly and concisely.
4. Practice Your Communication Skills
Articulate your ideas effectively and demonstrate strong communication skills, as you will be interacting with engineers, technicians, and other team members.
5. Dress Professionally
First impressions matter. Dress professionally to show respect for the interviewer and the company. Consider wearing business attire or clothing that is suitable for a manufacturing environment.
6. Be Punctual
Arrive on time for the interview. Punctuality demonstrates respect for the interviewer’s schedule and professionalism.
7. Be Confident and Enthusiastic
Project a positive and enthusiastic attitude throughout the interview. Confidence in your abilities and a passion for gear milling will make a lasting impression.
8. Ask Insightful Questions
At the end of the interview, prepare thoughtful questions to ask the interviewer. This shows your interest in the position and the company’s goals.
Next Step:
Armed with this knowledge, you’re now well-equipped to tackle the Gear Milling Machine Set-Up Operator interview with confidence. Remember, a well-crafted resume is your first impression. Take the time to tailor your resume to highlight your relevant skills and experiences. And don’t forget to practice your answers to common interview questions. With a little preparation, you’ll be on your way to landing your dream job. So what are you waiting for? Start building your resume and start applying! Build an amazing resume with ResumeGemini.
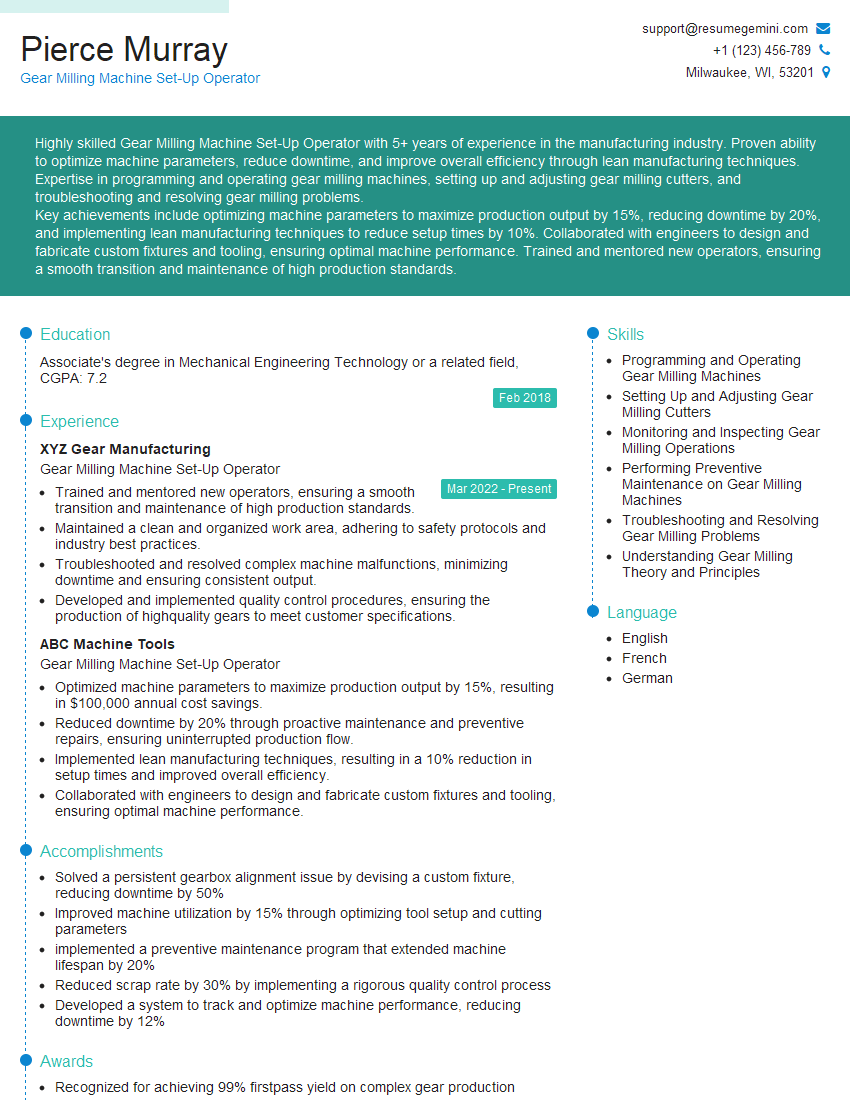