Feeling lost in a sea of interview questions? Landed that dream interview for Industrial Hygiene Technician but worried you might not have the answers? You’re not alone! This blog is your guide for interview success. We’ll break down the most common Industrial Hygiene Technician interview questions, providing insightful answers and tips to leave a lasting impression. Plus, we’ll delve into the key responsibilities of this exciting role, so you can walk into your interview feeling confident and prepared.
Acing the interview is crucial, but landing one requires a compelling resume that gets you noticed. Crafting a professional document that highlights your skills and experience is the first step toward interview success. ResumeGemini can help you build a standout resume that gets you called in for that dream job.
Essential Interview Questions For Industrial Hygiene Technician
1. Explain the hierarchy of controls for hazard mitigation.
- Elimination: Removing the hazard at the source.
- Substitution: Replacing the hazard with a less hazardous alternative.
- Engineering Controls: Isolating workers from the hazard, such as ventilation or machine guarding.
- Administrative Controls: Changing work practices or procedures to reduce exposure, such as job rotation or work schedules.
- Personal Protective Equipment (PPE): Providing workers with protective gear, such as respirators or gloves.
2. What are the key components of an industrial hygiene monitoring plan?
- Hazard Identification: Identifying potential hazards in the workplace.
- Exposure Assessment: Measuring the levels of exposure to hazardous substances.
- Health Effects Evaluation: Assessing the health effects associated with exposure to hazardous substances.
- Control Measures: Implementing measures to reduce or eliminate exposure to hazardous substances.
- Monitoring and Evaluation: Regularly monitoring the effectiveness of control measures and evaluating the health of exposed workers.
3. Describe the different types of air sampling methods and their applications.
- Personal Sampling: Collecting samples from the breathing zone of workers to assess their personal exposure.
- Area Sampling: Collecting samples from a fixed location in the workplace to assess the general exposure levels.
- Grab Sampling: Collecting a single sample over a short period to determine the instantaneous exposure level.
- Passive Sampling: Using a passive sampling device that absorbs or adsorbs the analyte over time to determine the average exposure level.
4. How do you interpret the results of an industrial hygiene survey?
- Compare the results to established occupational exposure limits (OELs).
- Identify any trends or patterns in the data.
- Assess the potential health risks associated with the exposure levels.
- Recommend appropriate control measures to reduce or eliminate exposure.
- Monitor the effectiveness of implemented control measures.
5. What are the common health hazards associated with welding operations?
- Fumes and Gases: Exposure to welding fumes and gases, such as carbon monoxide, nitrogen oxides, and ozone, can cause respiratory irritation, lung damage, and systemic effects.
- Ultraviolet Radiation: Exposure to ultraviolet radiation from the welding arc can cause skin burns and eye damage.
- Noise: Welding operations can produce high levels of noise, which can lead to hearing loss and other health effects.
- Heavy Metals: Welders may be exposed to heavy metals, such as lead and cadmium, which can have toxic effects on the nervous system and other organs.
6. How do you develop and implement a respiratory protection program?
- Hazard Assessment: Identify the hazards and assess the potential for respiratory exposure.
- Respirator Selection: Select the appropriate respirators based on the hazards and exposure levels.
- Training and Fit Testing: Train workers on the proper use and maintenance of respirators and conduct fit testing to ensure proper fit.
- Medical Evaluation: Evaluate workers to ensure they are physically able to wear and use respirators.
- Program Monitoring and Evaluation: Regularly monitor the effectiveness of the program and make adjustments as needed.
7. Describe the different types of noise measurements and their applications.
- Sound Pressure Level (SPL): Used to measure the instantaneous sound pressure at a specific point.
- Equivalent Sound Level (Leq): Used to measure the average sound level over a period of time.
- Dose: Used to measure the total sound energy exposure over a period of time and compare it to permissible exposure levels.
- Impulse Noise: Used to measure sudden, high-impact noise events.
8. How do you investigate and control noise hazards in the workplace?
- Noise Source Identification: Identify the sources of noise and assess their contribution to the overall noise levels.
- Control Measures: Implement control measures such as noise enclosures, vibration isolation, and sound-absorbing materials.
- Hearing Conservation Program: Implement a hearing conservation program that includes noise monitoring, audiometric testing, and provision of hearing protection.
- Employee Education and Training: Train employees on the hazards of noise and the importance of using hearing protection.
9. What are the key steps in conducting a workplace ergonomic assessment?
- Job Analysis: Observe and analyze the work activities to identify potential ergonomic hazards.
- Employee Interviews: Interview employees to gather their input on ergonomic issues and symptoms.
- Physical Measurements: Take body measurements and evaluate posture to assess the fit between the worker and the workstation.
- Recommendations: Develop recommendations for ergonomic improvements, such as workstation adjustments, equipment modifications, or changes in work practices.
10. Describe the different types of heat stress and their potential health effects.
- Heat Cramps: Muscle pain and spasms caused by electrolyte loss due to excessive sweating.
- Heat Exhaustion: Fatigue, weakness, dizziness, and nausea caused by dehydration and electrolyte imbalance.
- Heat Stroke: A life-threatening condition characterized by high body temperature, confusion, seizures, and coma.
Interviewers often ask about specific skills and experiences. With ResumeGemini‘s customizable templates, you can tailor your resume to showcase the skills most relevant to the position, making a powerful first impression. Also check out Resume Template specially tailored for Industrial Hygiene Technician.
Career Expert Tips:
- Ace those interviews! Prepare effectively by reviewing the Top 50 Most Common Interview Questions on ResumeGemini.
- Navigate your job search with confidence! Explore a wide range of Career Tips on ResumeGemini. Learn about common challenges and recommendations to overcome them.
- Craft the perfect resume! Master the Art of Resume Writing with ResumeGemini’s guide. Showcase your unique qualifications and achievements effectively.
- Great Savings With New Year Deals and Discounts! In 2025, boost your job search and build your dream resume with ResumeGemini’s ATS optimized templates.
Researching the company and tailoring your answers is essential. Once you have a clear understanding of the Industrial Hygiene Technician‘s requirements, you can use ResumeGemini to adjust your resume to perfectly match the job description.
Key Job Responsibilities
Industrial Hygiene Technicians play a pivotal role in ensuring the health and safety of employees in various workplaces. Their key responsibilities encompass:
1. Monitoring and Evaluating Occupational Exposures
Technicians conduct comprehensive workplace assessments and monitor environmental conditions to identify potential hazards, such as chemical fumes, dust, noise, and radiation.
- Collect air and surface samples for laboratory analysis to quantify hazardous substances and determine compliance with regulations.
- Utilize specialized equipment like gas detectors, noise dosimeters, and radiation monitors to assess exposure levels.
2. Developing and Implementing Control Measures
Industrial Hygiene Technicians devise and implement strategies to minimize or eliminate occupational exposures.
- Design and install ventilation systems, personal protective equipment (PPE), and engineering controls to reduce exposure levels.
- Develop written protocols and procedures to ensure proper handling, storage, and use of hazardous substances.
3. Conducting Employee Training and Education
Technicians provide training and guidance to employees on potential hazards, safe work practices, and the use of PPE.
- Develop and deliver educational programs on topics such as chemical handling, noise reduction techniques, and ergonomic principles.
- Train employees on the proper use, maintenance, and inspection of PPE, including respirators and protective clothing.
4. Maintaining Records and Reporting
Industrial Hygiene Technicians ensure accurate documentation and reporting of occupational exposure data.
- Maintain detailed records of monitoring results, employee training, and control measures implemented.
- Prepare reports and summaries to inform management, employees, and regulatory agencies about workplace hazards and mitigation strategies.
Interview Tips
Preparing thoroughly for an Industrial Hygiene Technician interview is crucial to showcasing your skills and demonstrating your suitability for the role:
1. Research the Company and Role
Familiarize yourself with the company’s industry, its health and safety practices, and the specific responsibilities of the Industrial Hygiene Technician position.
- Visit the company website and review its safety policies, mission statement, and recent news articles.
- Review the job description thoroughly and identify the key skills and experience required.
2. Highlight Your Technical Expertise
Emphasize your technical proficiency in occupational exposure monitoring, control measures, and employee training.
- Provide specific examples of projects where you successfully evaluated and controlled hazardous exposures.
- Showcase your knowledge of industry standards, regulations, and equipment calibration techniques.
3. Show Your Communication and Interpersonal Skills
Industrial Hygiene Technicians must effectively communicate with a diverse audience, including employees, management, and regulatory agencies.
- Describe your experience in developing and delivering training programs that engage employees.
- Provide examples of how you have successfully communicated complex technical concepts to non-technical audiences.
4. Prepare for Case Studies or Hypothetical Scenarios
Interviewers may ask you to discuss hypothetical scenarios or case studies related to occupational safety and health.
- Prepare by brainstorming potential scenarios you may encounter and how you would approach them.
- Use the STAR method (Situation, Task, Action, Result) to structure your answers and provide specific examples of your problem-solving skills.
Next Step:
Armed with this knowledge, you’re now well-equipped to tackle the Industrial Hygiene Technician interview with confidence. Remember, preparation is key. So, start crafting your resume, highlighting your relevant skills and experiences. Don’t be afraid to tailor your application to each specific job posting. With the right approach and a bit of practice, you’ll be well on your way to landing your dream job. Build your resume now from scratch or optimize your existing resume with ResumeGemini. Wish you luck in your career journey!
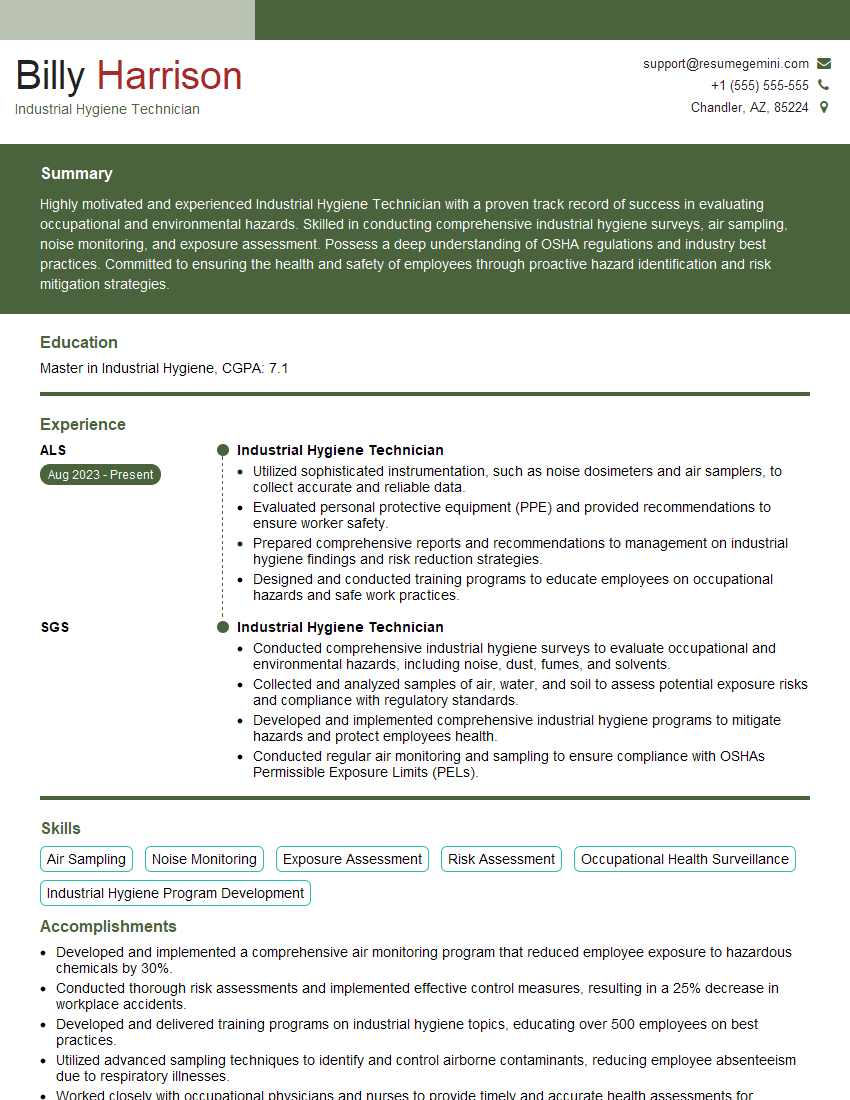