Are you gearing up for a career shift or aiming to ace your next interview? Look no further! We’ve curated a comprehensive guide to help you crack the interview for the coveted Metal Riveter position. From understanding the key responsibilities to mastering the most commonly asked questions, this blog has you covered. So, buckle up and let’s embark on this journey together
Acing the interview is crucial, but landing one requires a compelling resume that gets you noticed. Crafting a professional document that highlights your skills and experience is the first step toward interview success. ResumeGemini can help you build a standout resume that gets you called in for that dream job.
Essential Interview Questions For Metal Riveter
1. What are the key qualities of a successful Metal Riveter?
As a Metal Riveter, I believe key qualities for success include:
- Technical expertise: Proficiency in operating riveting machines, understanding riveting techniques, and troubleshooting equipment issues.
- Physical fitness: Ability to withstand physically demanding work, involving repetitive motions and handling heavy materials.
- Attention to detail: Ensuring accuracy and precision in riveting operations, adhering to safety regulations and quality standards.
- Teamwork: Collaborating effectively with other team members, understanding work processes, and contributing to overall productivity.
- Safety consciousness: Prioritizing safety measures, wearing appropriate personal protective equipment, and adhering to established safety protocols.
2. Describe the types of riveting processes and their applications.
Riveting Processes
- Solid Riveting: Permanent joint created by inserting a solid rivet into pre-drilled holes, hammering or pressing it into place.
- Blind Riveting: Used for inaccessible or one-sided applications, where rivets are installed with a specialized tool.
- Explosive Riveting: Creates high-strength joints using explosive charges to expand the rivet shank.
Applications
- Solid Riveting: Aircraft frames, bridges, structural steelworks
- Blind Riveting: Automotive panels, HVAC systems, electronic enclosures
- Explosive Riveting: Aerospace applications, military equipment
3. What are the common types of rivets used in metalworking?
Common rivet types in metalworking include:
- Solid Rivets: Round, cylindrical rods with a head on one end, used in solid riveting.
- Blind Rivets: Tubular rivets with a mandrel inserted, used in blind riveting.
- Pop Rivets: Blind rivets with a pre-assembled mandrel, designed for easy installation.
- Countersunk Rivets: Solid or blind rivets with a countersunk head, for flush installation.
- Cherrymax Rivets: High-strength blind rivets with a larger head, providing maximum bearing area.
4. Explain the factors that affect the strength of a riveted joint.
Key factors influencing the strength of a riveted joint include:
- Material properties: Strength and thickness of the metals being joined.
- Rivet type and size: Diameter, length, and material of the rivet.
- Riveting process: Proper hole preparation, rivet selection, and installation techniques.
- Joint design: Number of rivets, spacing, and edge distance.
- Loading conditions: Types of forces applied to the joint (tensile, shear, bending).
5. Describe the maintenance procedures for riveting equipment.
Regular maintenance of riveting equipment is crucial for optimal performance and safety:
- Daily: Inspecting air lines, oiling moving parts, and cleaning equipment.
- Weekly: Checking hoses, nozzles, and fittings for wear or damage.
- Monthly: Lubricating major components, replacing worn gaskets, and calibrating equipment.
- Annually: Performing comprehensive inspections, including electrical testing and pressure testing.
- As needed: Troubleshooting and repairing any equipment malfunctions.
6. How do you troubleshoot common riveting problems, such as loose rivets or misaligned holes?
Troubleshooting common riveting problems involves:
- Loose Rivets: Checking rivet selection, hole size, and installation process; ensuring proper hole preparation and rivet driving techniques.
- Misaligned Holes: Verifying template accuracy, ensuring proper hole alignment before riveting, and using specialized tools for precise hole alignment.
- Deformed Rivets: Inspecting riveting tools for damage, using proper rivet sizes, and applying appropriate pressure during installation.
- Broken Rivets: Examining rivet material and installation techniques, ensuring compatibility with the application and load requirements.
- Equipment Malfunctions: Diagnosing and addressing any issues with riveting machines, including air pressure, hydraulic systems, or electrical components.
7. What safety precautions should be taken when operating riveting machines?
To ensure safety while operating riveting machines, it’s crucial to:
- Wear appropriate personal protective equipment (PPE) including eye protection, earplugs, and gloves.
- Inspect equipment regularly for any damage or malfunctions, and report any issues promptly.
- Follow established safety protocols and guidelines provided by the manufacturer.
- Ensure the workpiece is properly secured to prevent movement during riveting.
- Maintain a clean and organized work area to minimize tripping or slipping hazards.
8. Describe the quality control procedures you follow to ensure the accuracy and reliability of riveted joints.
Quality control in riveting involves:
- Pre-Inspection: Verifying material specifications, rivet selection, and hole preparation.
- In-Process Inspection: Monitoring riveting parameters, such as pressure, force, and timing.
- Post-Riveting Inspection: Examining joints for proper head formation, clearances, and alignment.
- Testing: Conducting destructive or non-destructive testing to assess joint strength, such as tensile testing or ultrasonic testing.
- Documentation: Maintaining records of inspection results and any corrective actions taken.
9. What are the advantages and disadvantages of using automation in riveting processes?
Advantages
- Increased Productivity: Automated systems can perform riveting operations faster and with greater accuracy.
- Improved Quality: Automation helps maintain consistent riveting parameters, reducing human error and ensuring high-quality joints.
- Reduced Labor Costs: Automated systems can replace manual labor, reducing overall production costs.
- Safety Enhancement: Automation can remove workers from hazardous areas, reducing the risk of injuries.
Disadvantages
- High Initial Investment: Automated riveting systems can be expensive to purchase and implement.
- Limited Flexibility: Automated systems may not be suitable for all types of riveting tasks or materials.
- Maintenance Requirements: Automated systems require regular maintenance and technical expertise to operate efficiently.
10. What are the emerging trends in the field of riveting technology?
Emerging trends in riveting technology include:
- Advanced Materials: Development of stronger and lighter materials for rivets and metal sheets.
- Innovative Riveting Processes: Novel techniques such as ultrasonic riveting and laser riveting.
- Data Analytics: Utilizing sensors and data analysis to optimize riveting processes and improve quality control.
- Automation and Robotics: Increased adoption of automated riveting systems and robotic arms for enhanced efficiency and precision.
- Sustainable Riveting: Focus on environmentally friendly practices, such as using recyclable or biodegradable rivets.
Interviewers often ask about specific skills and experiences. With ResumeGemini‘s customizable templates, you can tailor your resume to showcase the skills most relevant to the position, making a powerful first impression. Also check out Resume Template specially tailored for Metal Riveter.
Career Expert Tips:
- Ace those interviews! Prepare effectively by reviewing the Top 50 Most Common Interview Questions on ResumeGemini.
- Navigate your job search with confidence! Explore a wide range of Career Tips on ResumeGemini. Learn about common challenges and recommendations to overcome them.
- Craft the perfect resume! Master the Art of Resume Writing with ResumeGemini’s guide. Showcase your unique qualifications and achievements effectively.
- Great Savings With New Year Deals and Discounts! In 2025, boost your job search and build your dream resume with ResumeGemini’s ATS optimized templates.
Researching the company and tailoring your answers is essential. Once you have a clear understanding of the Metal Riveter‘s requirements, you can use ResumeGemini to adjust your resume to perfectly match the job description.
Key Job Responsibilities
A Metal Riveter is a skilled tradesperson who specializes in joining metal components using rivets, a type of fastener that permanently connects two pieces of metal.
1. Riveting and Assembly
The primary responsibility of a Metal Riveter is to fasten metal components together using rivets. Riveting involves drilling holes into the metal pieces, inserting the rivet, and hammering or pressing it into place to create a secure connection. Metal Riveters ensure that the rivets are properly sized and installed according to specifications.
2. Preparation and Layout
Before riveting, Metal Riveters prepare the metal components by marking and drilling holes. They determine the appropriate rivet size and type based on the thickness and material of the metal. They also ensure that the components are correctly aligned and positioned before riveting.
3. Equipment Operation
Metal Riveters operate various tools and equipment, including rivet guns, hammers, drills, and presses. They maintain and calibrate these tools to ensure their accuracy and efficiency. They also wear appropriate safety gear, including gloves, eye protection, and hearing protection, while working.
4. Quality Inspection
After riveting, Metal Riveters inspect the connections to ensure that they meet quality standards. They check the rivet heads for proper formation and secure attachment. They also inspect the surrounding metal for any damage or defects.
Interview Tips
To ace an interview for a Metal Riveter position, candidates should be well-prepared and demonstrate their skills and knowledge of the trade. Here are some tips for successful interview preparation:
1. Research the Company and Position
Candidates should thoroughly research the company and the specific Metal Riveter position they are applying for. Understanding the company’s culture, values, and industry will help candidates tailor their answers to the interviewer’s questions.
2. Practice Common Interview Questions
Candidates should anticipate common interview questions and prepare thoughtful responses. They should practice answering questions about their experience, skills, and qualifications. Examples of common questions include:
- Tell me about your experience in metal riveting.
- Describe the types of riveting techniques you are familiar with.
- How do you ensure the quality of your riveting work?
3. Showcase Relevant Skills and Experience
Candidates should highlight their relevant skills and experience that align with the job requirements. They should provide specific examples to demonstrate their abilities in riveting, preparation, equipment operation, and quality inspection.
4. Prepare Questions for the Interviewer
Asking well-informed questions at the end of the interview shows candidates are engaged and interested in the position. Questions about the company’s projects, safety protocols, or training opportunities demonstrate a genuine desire to learn more about the role and the organization.
Next Step:
Now that you’re armed with a solid understanding of what it takes to succeed as a Metal Riveter, it’s time to turn that knowledge into action. Take a moment to revisit your resume, ensuring it highlights your relevant skills and experiences. Tailor it to reflect the insights you’ve gained from this blog and make it shine with your unique qualifications. Don’t wait for opportunities to come to you—start applying for Metal Riveter positions today and take the first step towards your next career milestone. Your dream job is within reach, and with a polished resume and targeted applications, you’ll be well on your way to achieving your career goals! Build your resume now with ResumeGemini.
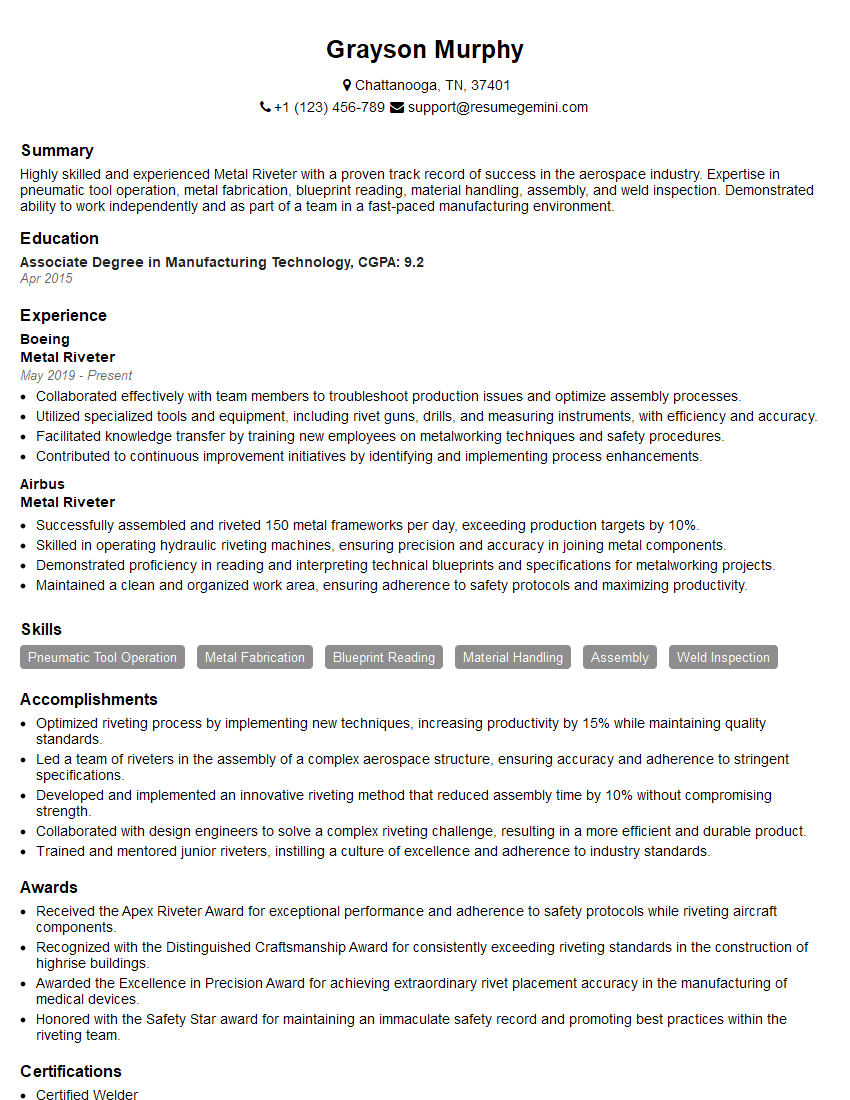