Ever felt underprepared for that crucial job interview? Or perhaps you’ve landed the interview but struggled to articulate your skills and experiences effectively? Fear not! We’ve got you covered. In this blog post, we’re diving deep into the Microfabrication Engineer Manager interview questions that you’re most likely to encounter. But that’s not all. We’ll also provide expert insights into the key responsibilities of a Microfabrication Engineer Manager so you can tailor your answers to impress potential employers.
Acing the interview is crucial, but landing one requires a compelling resume that gets you noticed. Crafting a professional document that highlights your skills and experience is the first step toward interview success. ResumeGemini can help you build a standout resume that gets you called in for that dream job.
Essential Interview Questions For Microfabrication Engineer Manager
1. What are the key challenges in managing a microfabrication engineering team?
- Coordinating a diverse team of engineers with specialized skills, including mechanical, electrical, and chemical engineering.
- Meeting tight deadlines and delivering high-quality products while adhering to strict quality standards.
- Staying abreast of rapidly evolving technologies and implementing them effectively within the team.
- Managing budgets and resources efficiently to ensure optimal team performance.
- Creating and fostering a positive and collaborative work environment that promotes innovation and productivity.
2. How do you stay updated with the latest advancements in microfabrication technology?
Conferences and workshops
- Attending industry conferences, workshops, and seminars to gain insights into new techniques and applications.
- Networking with experts and peers to exchange knowledge and stay informed about emerging trends.
Research papers and industry publications
- Regularly reading peer-reviewed journals, technical reports, and industry publications to stay abreast of the latest research and developments.
- Subscribing to industry newsletters and following thought leaders on social media to stay informed about the latest advancements.
Collaboration with academia and industry partners
- Partnering with universities and research institutions to gain access to cutting-edge research and collaborate on innovative projects.
- Working closely with industry partners to understand their specific needs and explore potential applications for new technologies.
3. Describe your experience in managing a team of engineers with diverse skill sets?
- Effectively leading and motivating a team of mechanical, electrical, and chemical engineers.
- Clearly defining roles and responsibilities to ensure seamless collaboration and minimize overlaps.
- Encouraging open communication, fostering teamwork, and recognizing individual contributions.
- Providing regular feedback and support to help each team member grow and develop their skills.
- Creating a positive and inclusive work environment that values diversity and encourages innovation.
4. How do you ensure the quality of products produced by your team?
- Implementing and maintaining a comprehensive quality management system that encompasses all aspects of the production process.
- Establishing clear quality standards and specifications, and ensuring that all team members are trained and certified to meet them.
- Conducting regular inspections and audits to monitor product quality and identify areas for improvement.
- Empowering team members to take ownership of quality and report any deviations or non-conformances.
- Working closely with customers to understand their specific requirements and ensure that products meet their expectations.
5. Describe your experience in managing budgets and resources for a microfabrication engineering team?
- Effectively managing and controlling budgets for equipment, materials, and labor.
- Prioritizing projects and allocating resources based on strategic objectives and customer demands.
- Negotiating contracts with vendors to secure the best possible deals on materials and services.
- Optimizing resource utilization to minimize waste and increase efficiency.
- Regularly reviewing and analyzing financial performance to identify areas for improvement.
6. How do you motivate and inspire your team to achieve peak performance?
- Setting clear goals and expectations, and providing regular feedback and recognition.
- Creating a culture of innovation and continuous improvement, where ideas are valued and rewarded.
- Providing opportunities for professional development and growth, including training, workshops, and conferences.
- Encouraging a sense of ownership and accountability among team members.
- Celebrating successes and acknowledging the contributions of each individual.
7. How do you handle conflicts within your team?
- Addressing conflicts promptly and openly, and creating a safe space for team members to express their concerns.
- Facilitating discussions and encouraging active listening to understand different perspectives.
- Mediating conflicts fairly and impartially, and finding solutions that are acceptable to all parties involved.
- Learning from conflicts and implementing strategies to prevent similar issues in the future.
8. How do you ensure that your team is aligned with the company’s strategic goals?
- Regularly communicating the company’s strategic goals and objectives to the team.
- Translating strategic goals into clear and actionable tasks for the team to work towards.
- Monitoring team progress and providing feedback to ensure alignment with strategic objectives.
- Involving the team in strategic planning and decision-making to foster buy-in and commitment.
9. How do you measure the success of your team?
- Establishing clear performance metrics that align with the company’s strategic goals.
- Tracking key performance indicators (KPIs) to monitor progress towards objectives.
- Conducting regular performance reviews to evaluate individual and team contributions.
- Gathering feedback from customers and stakeholders to assess the impact of the team’s work.
10. What are your strengths and weaknesses as a Microfabrication Engineer Manager?
- Proven leadership skills and ability to inspire and motivate teams to achieve exceptional results.
- Deep understanding of microfabrication principles, techniques, and materials.
- Experience in managing complex projects, budgets, and timelines.
- Strong communication and interpersonal skills, with the ability to effectively interact with engineers, scientists, and business leaders.
- Commitment to quality and continuous improvement.
- I am always eager to take on new challenges, which can sometimes lead me to overextend myself.
- I have a tendency to be perfectionistic, which can occasionally slow down the team’s progress.
- I am actively working on delegating more effectively to avoid these weaknesses.
Strengths:
Weaknesses:
Interviewers often ask about specific skills and experiences. With ResumeGemini‘s customizable templates, you can tailor your resume to showcase the skills most relevant to the position, making a powerful first impression. Also check out Resume Template specially tailored for Microfabrication Engineer Manager.
Career Expert Tips:
- Ace those interviews! Prepare effectively by reviewing the Top 50 Most Common Interview Questions on ResumeGemini.
- Navigate your job search with confidence! Explore a wide range of Career Tips on ResumeGemini. Learn about common challenges and recommendations to overcome them.
- Craft the perfect resume! Master the Art of Resume Writing with ResumeGemini’s guide. Showcase your unique qualifications and achievements effectively.
- Great Savings With New Year Deals and Discounts! In 2025, boost your job search and build your dream resume with ResumeGemini’s ATS optimized templates.
Researching the company and tailoring your answers is essential. Once you have a clear understanding of the Microfabrication Engineer Manager‘s requirements, you can use ResumeGemini to adjust your resume to perfectly match the job description.
Key Job Responsibilities
Microfabrication Engineer Managers oversee all aspects of microfabrication within an organization. This includes developing and implementing manufacturing processes, managing staff, and ensuring that the company’s products meet quality standards.
1. Process Development
Microfabrication Engineer Managers are responsible for developing and implementing new manufacturing processes. This includes researching new technologies, designing experiments, and optimizing process parameters.
- Conduct research to identify new and improved microfabrication techniques.
- Develop and implement new microfabrication processes to improve product quality and yield.
2. Equipment Maintenance
Microfabrication Engineer Managers are responsible for maintaining the company’s microfabrication equipment. This includes performing preventive maintenance, troubleshooting problems, and repairing equipment.
- Maintain and repair microfabrication equipment to ensure optimal performance.
- Develop and implement preventive maintenance programs to minimize downtime.
3. Quality Control
Microfabrication Engineer Managers are responsible for ensuring that the company’s products meet quality standards. This includes developing and implementing quality control procedures, inspecting products, and identifying and correcting defects.
- Develop and implement quality control procedures to ensure product quality.
- Inspect products to identify defects and non-conformances.
4. Staff Management
Microfabrication Engineer Managers are responsible for managing staff. This includes hiring, training, and evaluating employees.
- Hire, train, and evaluate staff to ensure a skilled and motivated workforce.
- Provide leadership and guidance to staff to achieve organizational goals.
Interview Tips
Preparing for an interview for a Microfabrication Engineer Manager position requires a combination of technical knowledge and interview skills. Here are some tips to help you ace the interview:
1. Research the Company and the Position
Before the interview, research the company and the specific position you are applying for. This will help you understand the company’s culture and the specific requirements of the role.
- Visit the company’s website to learn about their products, services, and values.
- Read industry publications and news articles to stay up-to-date on the latest trends in microfabrication.
2. Prepare for Technical Questions
Be prepared to answer technical questions about microfabrication processes, equipment, and quality control. These questions may be specific to the company’s products or processes, so it is important to research the company and the specific position you are applying for.
- Review your knowledge of microfabrication processes, equipment, and quality control procedures.
- Practice answering technical questions in a clear and concise manner.
3. Highlight Your Management Skills
In addition to technical skills, Microfabrication Engineer Managers need strong management skills. Be prepared to answer questions about your experience in hiring, training, and evaluating staff.
- Highlight your experience in managing staff, including your ability to motivate and develop employees.
- Provide examples of how you have successfully implemented new processes or resolved problems.
4. Be Enthusiastic and Professional
First impressions matter, so be sure to dress professionally and arrive on time for your interview. Be enthusiastic and positive about the position and the company. Show the interviewer that you are eager to learn and contribute to the team.
- Dress professionally and arrive on time for your interview.
- Be enthusiastic and positive about the position and the company.
Next Step:
Now that you’re armed with interview-winning answers and a deeper understanding of the Microfabrication Engineer Manager role, it’s time to take action! Does your resume accurately reflect your skills and experience for this position? If not, head over to ResumeGemini. Here, you’ll find all the tools and tips to craft a resume that gets noticed. Don’t let a weak resume hold you back from landing your dream job. Polish your resume, hit the “Build Your Resume” button, and watch your career take off! Remember, preparation is key, and ResumeGemini is your partner in interview success.
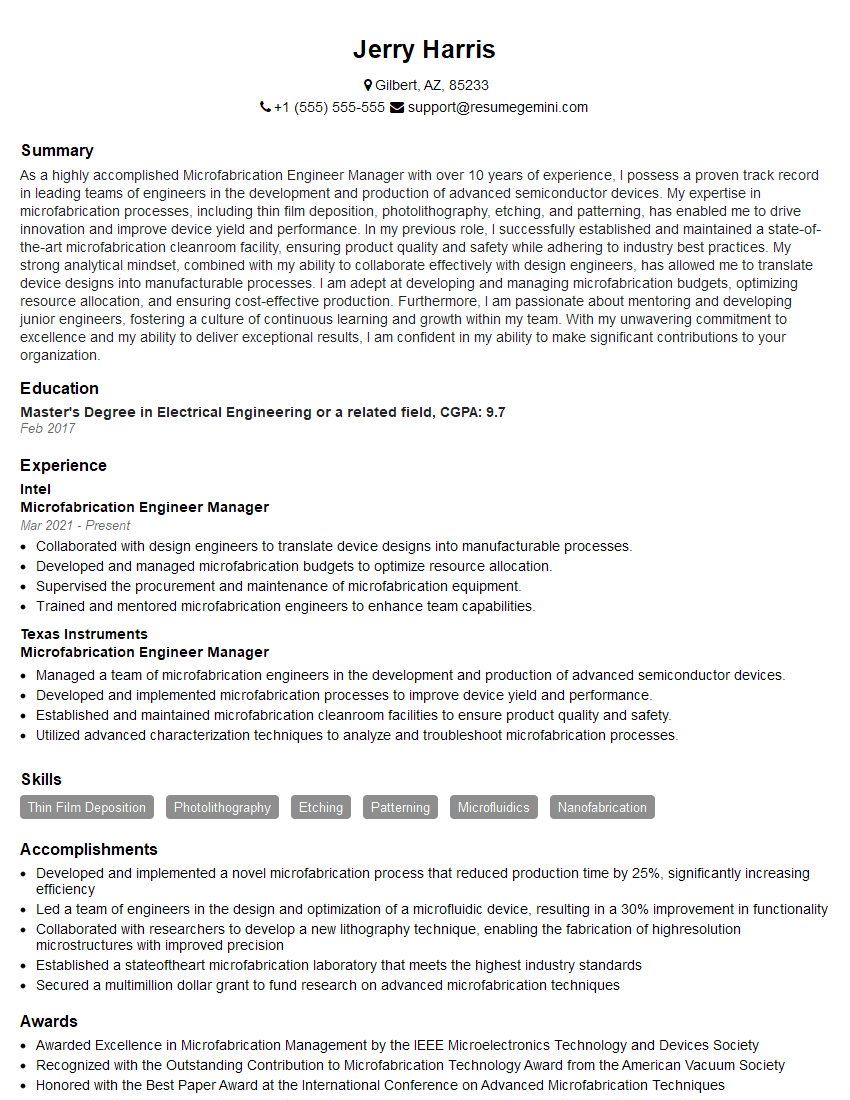