Ever felt underprepared for that crucial job interview? Or perhaps you’ve landed the interview but struggled to articulate your skills and experiences effectively? Fear not! We’ve got you covered. In this blog post, we’re diving deep into the Production Manager interview questions that you’re most likely to encounter. But that’s not all. We’ll also provide expert insights into the key responsibilities of a Production Manager so you can tailor your answers to impress potential employers.
Acing the interview is crucial, but landing one requires a compelling resume that gets you noticed. Crafting a professional document that highlights your skills and experience is the first step toward interview success. ResumeGemini can help you build a standout resume that gets you called in for that dream job.
Essential Interview Questions For Production Manager
1. How do you ensure product quality meets customer expectations?
To ensure product quality meets customer expectations, I implement a comprehensive quality management system that includes the following steps:
- Establish clear quality standards: Define specific, measurable, achievable, relevant, and time-bound quality criteria.
- Conduct thorough inspections: Regularly inspect raw materials, work-in-progress, and finished products to identify and address defects.
- Implement statistical process control: Monitor production processes using statistical tools to identify and eliminate sources of variation.
- Empower employees: Train and empower employees to take ownership of product quality and report any concerns.
- Continuously improve: Analyze quality data and implement corrective actions to improve processes and reduce defects.
2. How do you optimize production schedules to maximize efficiency and minimize waste?
Capacity Planning
- Assess production capacity: Determine the maximum output potential of equipment and resources.
- Forecast demand: Analyze historical data and market trends to predict future product demand.
- Balance workload: Distribute workload evenly across production lines and shifts to avoid bottlenecks and maximize utilization.
Scheduling Techniques
- First-In-First-Out (FIFO): Process orders in the sequence they are received.
- Shortest Job First (SJF): Prioritize orders based on shortest processing time.
- Critical Path Method (CPM): Identify critical activities and schedule them accordingly to minimize project duration.
Waste Reduction
- Eliminate bottlenecks: Identify and address production constraints that slow down operations.
- Reduce setup times: Implement lean manufacturing techniques to minimize downtime between production runs.
- Optimize inventory levels: Maintain appropriate inventory levels to avoid overstocking and waste.
3. What are the key performance indicators (KPIs) you track to monitor production performance?
The following KPIs are essential for monitoring production performance:
- Overall Equipment Effectiveness (OEE): Measures the efficiency, availability, and quality of production equipment.
- Production Output: Tracks the quantity of products produced in a given period.
- Throughput: Measures the rate at which products move through the production process.
- Lead Time: Monitors the time it takes from order placement to product delivery.
- Yield: Calculates the percentage of defect-free products produced in relation to total output.
- Inventory Turnover: Assesses the efficiency of inventory management practices.
4. How do you ensure adherence to safety regulations and maintain a safe work environment?
To ensure adherence to safety regulations and maintain a safe work environment, I implement the following measures:
- Establish clear safety policies and procedures: Communicate expectations and guidelines to all employees.
- Conduct regular safety training and drills: Educate employees on hazards and emergency procedures.
- Regularly inspect equipment and facilities: Identify and address potential hazards and maintain a clean and organized workplace.
- Provide personal protective equipment (PPE): Ensure employees have access to appropriate PPE and enforce its use.
- Empower employees to report safety concerns: Encourage employees to identify and report any safety issues without fear of retaliation.
- Monitor and evaluate safety performance: Track safety incidents and conduct regular audits to identify areas for improvement.
5. What are your strategies for minimizing production costs while maintaining product quality?
To minimize production costs while maintaining product quality, I employ the following strategies:
- Value stream mapping: Identify and eliminate waste and inefficiencies in production processes.
- Supplier management: Negotiate competitive prices and establish long-term relationships with suppliers.
- Lean manufacturing techniques: Implement continuous improvement practices to reduce waste and increase efficiency.
- Process optimization: Analyze production processes to identify and eliminate bottlenecks and improve flow.
- Automation: Implement automation technologies to reduce labor costs and increase productivity.
- Employee training: Provide training to employees to enhance skills and reduce errors and rework.
6. How do you handle production challenges and resolve unexpected issues?
When faced with production challenges and unexpected issues, I follow a structured problem-solving approach:
- Identify the problem: Clearly define the issue and its potential impact.
- Gather data: Collect relevant data and information to understand the root cause.
- Generate solutions: Brainstorm and evaluate potential solutions to address the problem.
- Implement the solution: Execute the chosen solution and monitor its effectiveness.
- Evaluate and adjust: Track the results of the solution and make necessary adjustments to ensure optimal performance.
7. How do you stay updated on industry best practices and emerging technologies?
To stay updated on industry best practices and emerging technologies, I engage in the following activities:
- Attend industry conferences and workshops: Network with experts and learn about the latest advancements.
- Read industry publications and journals: Keep abreast of research and developments in the field.
- Participate in online forums and communities: Engage with peers and share knowledge.
- Collaborate with technology vendors: Explore new technologies and their potential applications.
- Conduct internal research and development: Experiment with innovative ideas and develop new solutions.
8. What are your strengths and weaknesses as a Production Manager?
Strengths:
- Strong technical understanding of production processes.
- Proven ability to optimize production schedules and minimize waste.
- Excellent communication and interpersonal skills for effective team leadership.
- Commitment to safety and maintaining a safe work environment.
- Ability to handle production challenges and resolve unexpected issues effectively.
Weaknesses:
- Limited experience in a highly automated production environment.
- Still developing knowledge in the latest manufacturing technologies.
9. How do you plan to contribute to our organization as a Production Manager?
If selected as Production Manager, I plan to contribute to your organization by:
- Optimizing production processes to increase efficiency and reduce costs.
- Implementing innovative technologies to enhance productivity and quality.
- Leading and motivating a team of production professionals to achieve exceptional results.
- Ensuring adherence to safety regulations and maintaining a safe work environment.
- Collaborating with cross-functional teams to drive operational excellence.
10. What are your salary expectations for this role?
My salary expectations are commensurate with my experience and qualifications. I am confident that my skills and contributions will bring significant value to your organization. I am open to discussing a compensation package that is competitive and aligned with industry benchmarks.
Interviewers often ask about specific skills and experiences. With ResumeGemini‘s customizable templates, you can tailor your resume to showcase the skills most relevant to the position, making a powerful first impression. Also check out Resume Template specially tailored for Production Manager.
Career Expert Tips:
- Ace those interviews! Prepare effectively by reviewing the Top 50 Most Common Interview Questions on ResumeGemini.
- Navigate your job search with confidence! Explore a wide range of Career Tips on ResumeGemini. Learn about common challenges and recommendations to overcome them.
- Craft the perfect resume! Master the Art of Resume Writing with ResumeGemini’s guide. Showcase your unique qualifications and achievements effectively.
- Great Savings With New Year Deals and Discounts! In 2025, boost your job search and build your dream resume with ResumeGemini’s ATS optimized templates.
Researching the company and tailoring your answers is essential. Once you have a clear understanding of the Production Manager‘s requirements, you can use ResumeGemini to adjust your resume to perfectly match the job description.
Key Job Responsibilities
As a Production Manager, you will be responsible for:
1. Planning and Scheduling Production
Oversee the planning and scheduling of production activities, including setting production goals, determining resource allocation, and ensuring efficient use of equipment and materials
- Develop and implement production plans that optimize efficiency and minimize costs
- Allocate resources effectively to meet production demands
2. Supervising and Managing Production Team
Manage and supervise a team of production operators, ensuring adherence to safety regulations and quality standards
- Train and develop production staff to enhance productivity
- Maintain a positive and productive work environment
3. Monitoring Production Progress
Monitor production progress and identify bottlenecks to address and improve efficiency
- Use production tracking systems to monitor progress
- Identify areas for improvement and implement solutions
4. Ensuring Quality Standards
Establish and maintain quality standards for products and ensure compliance throughout the production process
- Implement quality control measures to prevent defects
- Conduct regular inspections to ensure product quality
Interview Tips
To ace your Production Manager interview, consider the following tips:
1. Research the Company and Position
Thoroughly research the company’s industry, products, and culture to demonstrate your interest and understanding of the role
- Visit the company’s website and social media pages
- Read industry news and articles to stay informed
2. Practice Your Answers
Prepare for common interview questions by practicing your answers out loud. Consider using our Example Outline below to structure your responses
- Explain your experience in production planning and scheduling
- Discuss your strategies for motivating and managing a team
3. Highlight Your Skills and Experience
Tailor your resume and cover letter to highlight skills and experiences that are relevant to the job requirements
- Quantify your accomplishments with concrete metrics
- Use action verbs to describe your responsibilities
4. Be Enthusiastic and Confident
Project enthusiasm and confidence during the interview. This will show the interviewer that you are genuinely interested in the position and believe in your abilities
- Smile and make eye contact with the interviewer
- Speak clearly and concisely
Next Step:
Armed with this knowledge, you’re now well-equipped to tackle the Production Manager interview with confidence. Remember, preparation is key. So, start crafting your resume, highlighting your relevant skills and experiences. Don’t be afraid to tailor your application to each specific job posting. With the right approach and a bit of practice, you’ll be well on your way to landing your dream job. Build your resume now from scratch or optimize your existing resume with ResumeGemini. Wish you luck in your career journey!
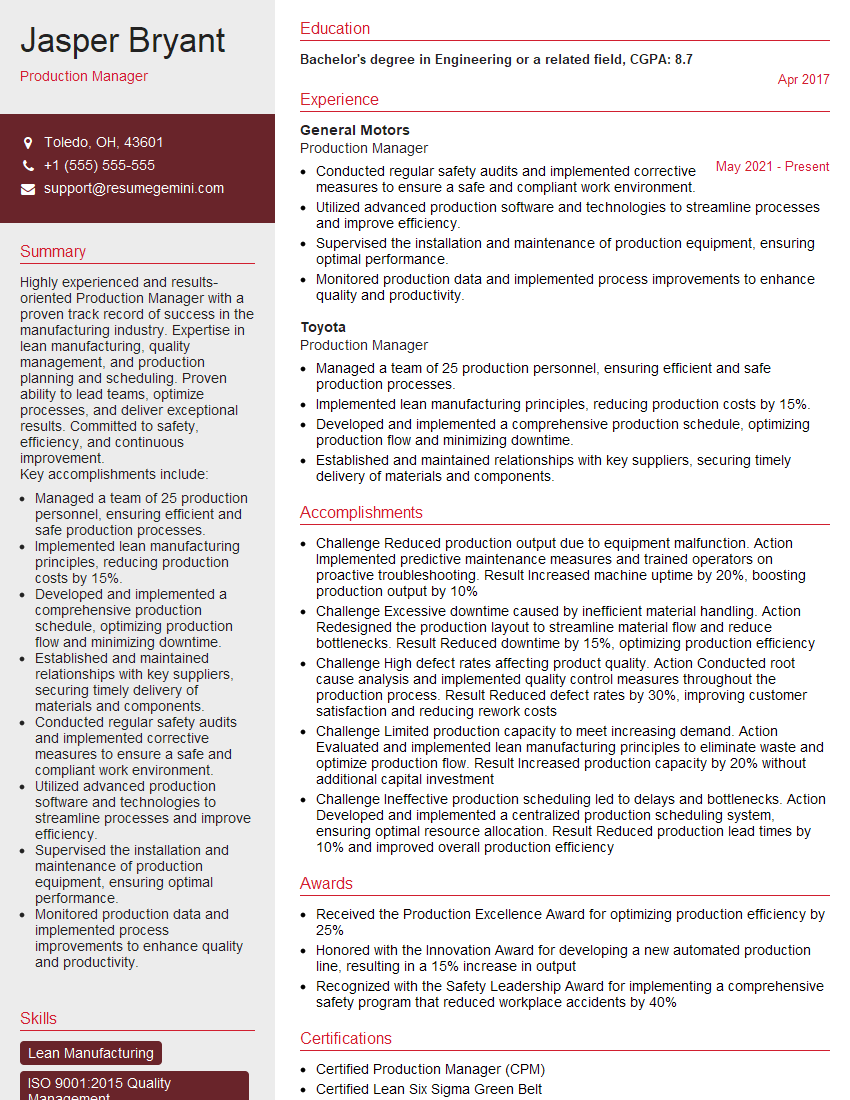