Are you gearing up for an interview for a Pump Service Supervisor position? Whether you’re a seasoned professional or just stepping into the role, understanding what’s expected can make all the difference. In this blog, we dive deep into the essential interview questions for Pump Service Supervisor and break down the key responsibilities of the role. By exploring these insights, you’ll gain a clearer picture of what employers are looking for and how you can stand out. Read on to equip yourself with the knowledge and confidence needed to ace your next interview and land your dream job!
Acing the interview is crucial, but landing one requires a compelling resume that gets you noticed. Crafting a professional document that highlights your skills and experience is the first step toward interview success. ResumeGemini can help you build a standout resume that gets you called in for that dream job.
Essential Interview Questions For Pump Service Supervisor
1. What are the key components of a centrifugal pump and explain their functions?
- Impeller: The impeller is a rotating disk with blades that imparts kinetic energy to the fluid.
- Casing: The casing surrounds the impeller and directs the flow of fluid.
- Shaft: The shaft connects the impeller to the motor and transmits power.
- Bearings: The bearings support the shaft and reduce friction.
- Seals: The seals prevent fluid leakage along the shaft.
2. Describe the different types of pump seals and their applications.
Mechanical Seals
- Used in high-pressure applications.
- Consist of two rotating faces that seal against each other.
Gland Packing
- Used in low-pressure applications.
- Consists of a packing material that is compressed around the shaft.
Lip Seals
- Used in low-pressure applications where the shaft rotates at high speeds.
- Consist of a flexible lip that seals against the shaft.
3. How do you troubleshoot a pump that is not priming?
- Check the suction line for leaks or blockages.
- Check the impeller for wear or damage.
- Check the foot valve for proper operation.
- Check the prime source for sufficient flow.
- Check the pump speed and voltage.
4. Explain the importance of suction lift and how it affects pump performance.
- Suction lift is the vertical distance between the fluid level and the pump inlet.
- Suction lift affects pump performance because it increases the pressure drop on the suction side of the pump.
- A high suction lift can lead to cavitation, which can damage the pump.
5. How do you calculate the efficiency of a pump?
- Pump efficiency = (Actual flow rate x Actual head) / (Theoretical flow rate x Theoretical head)
- Theoretical flow rate and head are calculated based on the pump design data.
- Actual flow rate and head are measured during pump operation.
6. What are the different types of pump cavitation and how do you prevent them?
- Suction cavitation: Occurs when the pressure on the suction side of the pump drops below the vapor pressure of the fluid.
- Discharge cavitation: Occurs when the pressure on the discharge side of the pump drops below the vapor pressure of the fluid.
- Prevention: Reduce suction lift, increase pump speed, or change the fluid viscosity.
7. How do you plan and execute a pump maintenance program?
- Planning: Identify maintenance tasks, intervals, and resources.
- Execution: Schedule maintenance, perform inspections, and replace worn parts.
- Record-keeping: Document maintenance activities and track pump performance.
8. Explain the difference between parallel and series pump operation.
- Parallel operation: Pumps are connected in parallel to increase flow rate.
- Series operation: Pumps are connected in series to increase head.
9. Describe the safety procedures you follow when working with pumps.
- Lock out and tag out equipment before servicing.
- Wear appropriate PPE (e.g., safety glasses, gloves, hard hat).
- Never work alone on a pump.
- Be aware of potential hazards (e.g., electrical shock, fluid leaks).
10. How do you stay up-to-date on new technologies and industry best practices related to pump service?
- Attend industry conferences and training programs.
- Read technical articles and journals.
- Network with other pump professionals.
- Get certified in pump maintenance and repair.
Interviewers often ask about specific skills and experiences. With ResumeGemini‘s customizable templates, you can tailor your resume to showcase the skills most relevant to the position, making a powerful first impression. Also check out Resume Template specially tailored for Pump Service Supervisor.
Career Expert Tips:
- Ace those interviews! Prepare effectively by reviewing the Top 50 Most Common Interview Questions on ResumeGemini.
- Navigate your job search with confidence! Explore a wide range of Career Tips on ResumeGemini. Learn about common challenges and recommendations to overcome them.
- Craft the perfect resume! Master the Art of Resume Writing with ResumeGemini’s guide. Showcase your unique qualifications and achievements effectively.
- Great Savings With New Year Deals and Discounts! In 2025, boost your job search and build your dream resume with ResumeGemini’s ATS optimized templates.
Researching the company and tailoring your answers is essential. Once you have a clear understanding of the Pump Service Supervisor‘s requirements, you can use ResumeGemini to adjust your resume to perfectly match the job description.
Key Job Responsibilities
The Pump Service Supervisor is responsible for overseeing the maintenance, repair, and installation of pumps and related equipment.
1. Management and Supervision
Directs and supervises a team of pump service technicians, including assigning work, monitoring performance, and providing training.
- Develops and implements policies and procedures for the pump service department.
- Ensures that all work is completed safely and efficiently.
2. Technical Expertise
Possesses a deep understanding of pump systems, including principles of operation, maintenance, and troubleshooting.
- Diagnoses and repairs pump problems, including mechanical, electrical, and hydraulic issues.
- Performs preventive maintenance and inspections to ensure optimal pump performance.
3. Customer Relations
Interacts with customers to understand their needs and provide excellent service.
- Responds to customer inquiries and resolves any issues or concerns.
- Builds and maintains strong customer relationships.
4. Budget and Resource Management
Manages the pump service department’s budget and resources, including personnel, equipment, and supplies.
- Prepares and tracks budgets for the department.
- Acquires and manages necessary equipment and supplies.
Interview Tips
Preparing for an interview for a Pump Service Supervisor position requires a combination of technical knowledge, industry experience, and strong communication skills. Here are some tips to help you ace your interview:
1. Research the Company and Position
Thoroughly research the company and the specific role you are applying for. This will give you a deeper understanding of their business, industry, and the challenges and opportunities associated with the position.
- Visit the company’s website to learn about their products, services, values, and culture.
- Read industry publications and articles to stay up-to-date on current trends and best practices.
2. Highlight Your Technical Expertise
In your interview, be prepared to discuss your technical knowledge and experience in detail. This may include:
- Your understanding of different types of pumps and their applications.
- Your experience in troubleshooting and repairing pumps.
- Your ability to perform preventive maintenance and inspections.
3. Emphasize Customer Service Skills
Since you will be interacting with customers in this role, it’s essential to highlight your customer service skills. Explain how you build and maintain relationships with clients and resolve any concerns they may have.
- Provide examples of how you have gone above and beyond to meet customer expectations.
- Discuss your ability to communicate effectively and professionally with customers.
4. Showcase Your Leadership and Management Abilities
The Pump Service Supervisor is a leadership position, so be prepared to discuss your supervisory skills. Highlight your experience in motivating and directing a team, as well as your ability to handle performance issues and resolve conflicts.
- Describe your approach to employee development and training.
- Share examples of how you have successfully managed and completed projects.
5. Prepare Questions
At the end of the interview, you will likely be given the opportunity to ask questions. This is a great way to show your interest in the position and the company. Prepare thoughtful questions that demonstrate your curiosity and enthusiasm for the role.
- Ask about the company’s future plans and growth prospects.
- Inquire about opportunities for professional development and advancement.
Next Step:
Now that you’re armed with a solid understanding of what it takes to succeed as a Pump Service Supervisor, it’s time to turn that knowledge into action. Take a moment to revisit your resume, ensuring it highlights your relevant skills and experiences. Tailor it to reflect the insights you’ve gained from this blog and make it shine with your unique qualifications. Don’t wait for opportunities to come to you—start applying for Pump Service Supervisor positions today and take the first step towards your next career milestone. Your dream job is within reach, and with a polished resume and targeted applications, you’ll be well on your way to achieving your career goals! Build your resume now with ResumeGemini.
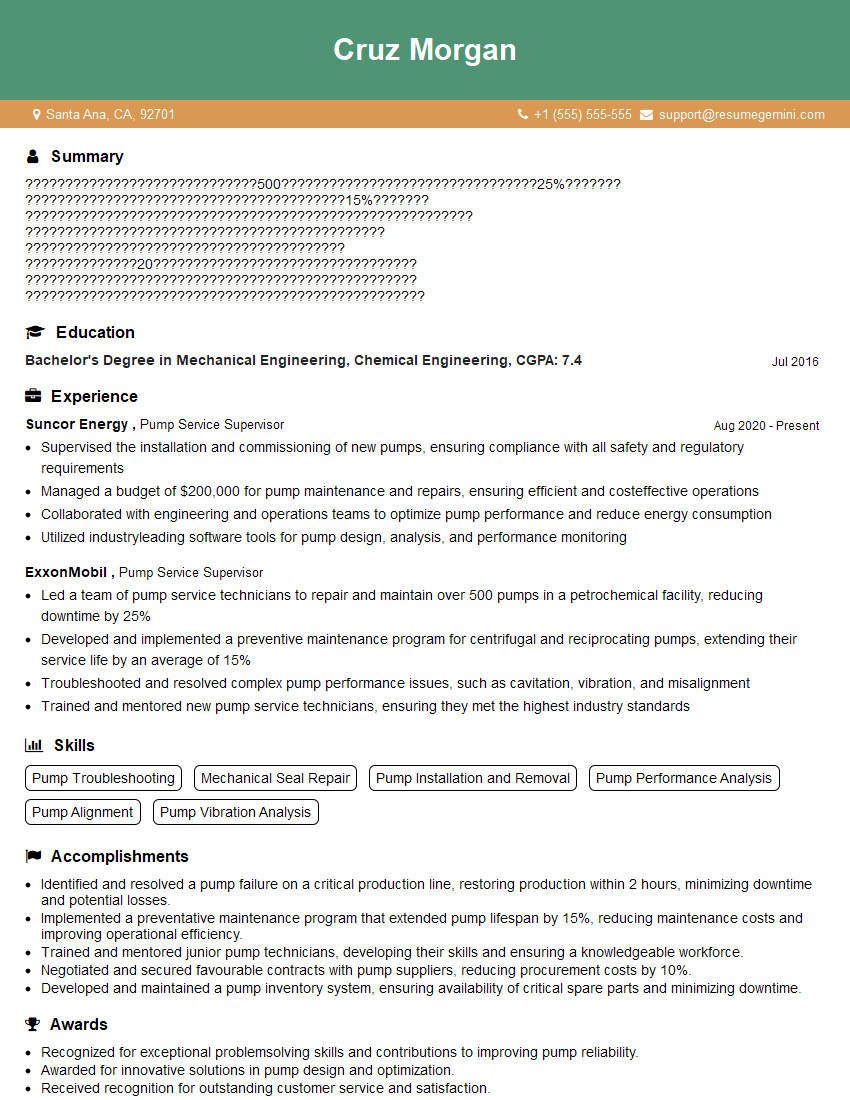