Are you gearing up for an interview for a Quality Control Inspector (QC Inspector) position? Whether you’re a seasoned professional or just stepping into the role, understanding what’s expected can make all the difference. In this blog, we dive deep into the essential interview questions for Quality Control Inspector (QC Inspector) and break down the key responsibilities of the role. By exploring these insights, you’ll gain a clearer picture of what employers are looking for and how you can stand out. Read on to equip yourself with the knowledge and confidence needed to ace your next interview and land your dream job!
Acing the interview is crucial, but landing one requires a compelling resume that gets you noticed. Crafting a professional document that highlights your skills and experience is the first step toward interview success. ResumeGemini can help you build a standout resume that gets you called in for that dream job.
Essential Interview Questions For Quality Control Inspector (QC Inspector)
1. What are the key responsibilities of a Quality Control Inspector (QC Inspector)?
As a Quality Control Inspector, my responsibilities would encompass:
- Inspecting and testing raw materials, finished products, and components to ensure they meet specifications and quality standards.
- Conducting visual inspections, dimensional measurements, and functional testing to identify any defects or deviations.
2. How do you maintain accurate and detailed inspection records?
Using Inspection Tools and Techniques
- Employing the appropriate inspection tools and techniques, such as gauges, calipers, and specialized testing equipment.
- Following established procedures and checklists to ensure consistent and thorough inspections.
Documenting Inspection Findings
- Accurately recording inspection results and any identified defects or deviations in inspection reports.
- Maintaining organized and easily accessible documentation for future reference and traceability.
3. What statistical process control (SPC) tools are you familiar with?
I am familiar with various statistical process control (SPC) tools, including:
- Control charts (e.g., X-bar, R-chart, p-chart, c-chart): Used to monitor process stability and identify trends and variations.
- Histograms: Depicting the distribution of data to analyze process capability and identify potential areas of improvement.
- Sampling techniques: Utilizing random or stratified sampling methods to ensure representative samples for inspection and data analysis.
4. How do you ensure the traceability of inspected products?
To ensure the traceability of inspected products, I utilize various methods, such as:
- Implementing clear labeling and marking systems to identify products and inspection status.
- Maintaining comprehensive records of inspection results, including product identification, inspection dates, and any identified defects.
- Establishing procedures for tracking and managing non-conforming products to prevent their release.
5. What are the different types of inspection reports you have experience with?
I have experience in generating and reviewing various types of inspection reports, including:
- Inspection Certificates: Formal documents certifying the compliance of inspected products with specified standards.
- Non-Conformance Reports (NCRs): Detailed reports documenting identified defects, their root causes, and corrective actions.
- Inspection Logs: Daily or periodic records summarizing inspection activities, findings, and actions taken.
6. How do you handle and manage non-conforming products?
Upon identifying non-conforming products, I follow established procedures to ensure their proper handling and management:
- Segregating and clearly labeling non-conforming products to prevent their inadvertent use.
- Initiating investigations to determine the root cause of non-conformances and identify corrective actions.
- Collaborating with relevant departments, such as production and engineering, to implement corrective measures.
7. What software applications are you proficient in for quality control purposes?
My proficiency extends to various quality control software applications, including:
- Inspection Management Systems: Software tools for managing inspection plans, scheduling inspections, and recording inspection results.
- Statistical Analysis Software: Applications for analyzing inspection data, creating control charts, and conducting statistical tests.
- Computer-Aided Inspection (CAI) Systems: Advanced software utilized for automated inspections using image recognition and other technologies.
8. How do you contribute to continuous quality improvement (CQI) initiatives?
I actively contribute to CQI initiatives through:
- Participating in process reviews and audits to identify areas for improvement.
- Analyzing inspection data to identify trends and patterns that could indicate potential quality issues.
- Collaborating with cross-functional teams to develop and implement solutions to improve product quality and efficiency.
9. What are the ethical considerations in quality control inspections?
Ethical considerations are paramount in quality control inspections:
- Maintaining objectivity and impartiality during inspections, avoiding any personal biases or conflicts of interest.
- Accurately reporting inspection findings and adhering to established standards, even if the results may be unfavorable.
- Protecting confidential information, such as trade secrets or proprietary data, encountered during inspections.
10. How do you stay updated with the latest advancements in quality control techniques and industry best practices?
I continuously seek professional development opportunities to stay abreast of advancements in quality control:
- Attending industry conferences and workshops to learn from experts and gain insights into emerging trends.
- Subscribing to technical journals and industry publications to stay informed about new inspection technologies and methodologies.
- Participating in online courses and certifications to expand my knowledge and skills in quality control.
Interviewers often ask about specific skills and experiences. With ResumeGemini‘s customizable templates, you can tailor your resume to showcase the skills most relevant to the position, making a powerful first impression. Also check out Resume Template specially tailored for Quality Control Inspector (QC Inspector).
Career Expert Tips:
- Ace those interviews! Prepare effectively by reviewing the Top 50 Most Common Interview Questions on ResumeGemini.
- Navigate your job search with confidence! Explore a wide range of Career Tips on ResumeGemini. Learn about common challenges and recommendations to overcome them.
- Craft the perfect resume! Master the Art of Resume Writing with ResumeGemini’s guide. Showcase your unique qualifications and achievements effectively.
- Great Savings With New Year Deals and Discounts! In 2025, boost your job search and build your dream resume with ResumeGemini’s ATS optimized templates.
Researching the company and tailoring your answers is essential. Once you have a clear understanding of the Quality Control Inspector (QC Inspector)‘s requirements, you can use ResumeGemini to adjust your resume to perfectly match the job description.
Key Job Responsibilities
QC Inspectors play a crucial role in ensuring the quality of products or services, safeguarding the reputation of businesses, and meeting customer expectations. Their key job responsibilities include:
1. Inspection and Testing
Conduct rigorous examinations of products, materials, and processes to assess their conformance to established specifications and standards.
2. Quality Control Documentation
Maintain accurate and detailed records of inspections, test results, and any nonconformities identified to facilitate traceability and accountability.
3. Nonconformity Management
Identify and document quality issues or deviations from standards, initiate corrective actions, and monitor their effectiveness to ensure timely resolution.
4. Quality Improvement Initiatives
Participate in quality improvement programs, provide feedback on production processes, and suggest enhancements to improve overall quality.
Interview Tips
To ace the QC Inspector interview, candidates should prepare diligently by understanding the key responsibilities, researching the industry, and practicing their answers. Here are some tips:
1. Research the Company and Role
Thoroughly review the company’s website, LinkedIn profile, and job description to gain insights into their culture, values, and specific requirements for the QC Inspector role.
2. Highlight Relevant Skills and Experience
Focus on showcasing your technical expertise in quality control techniques, proficiency in industry-specific standards, and a strong attention to detail.
3. Prepare for Common Interview Questions
Anticipate questions about your understanding of quality control principles, experience with inspection equipment, and ability to handle nonconformities.
4. Showcase Problem-Solving Abilities
Share examples from your past experience where you successfully identified and resolved quality issues, demonstrating your analytical and problem-solving skills.
5. Emphasize Communication and Teamwork
Highlight your ability to communicate effectively with production staff, engineers, and management to ensure clarity and cooperation in quality control efforts.
Next Step:
Now that you’re armed with interview-winning answers and a deeper understanding of the Quality Control Inspector (QC Inspector) role, it’s time to take action! Does your resume accurately reflect your skills and experience for this position? If not, head over to ResumeGemini. Here, you’ll find all the tools and tips to craft a resume that gets noticed. Don’t let a weak resume hold you back from landing your dream job. Polish your resume, hit the “Build Your Resume” button, and watch your career take off! Remember, preparation is key, and ResumeGemini is your partner in interview success.
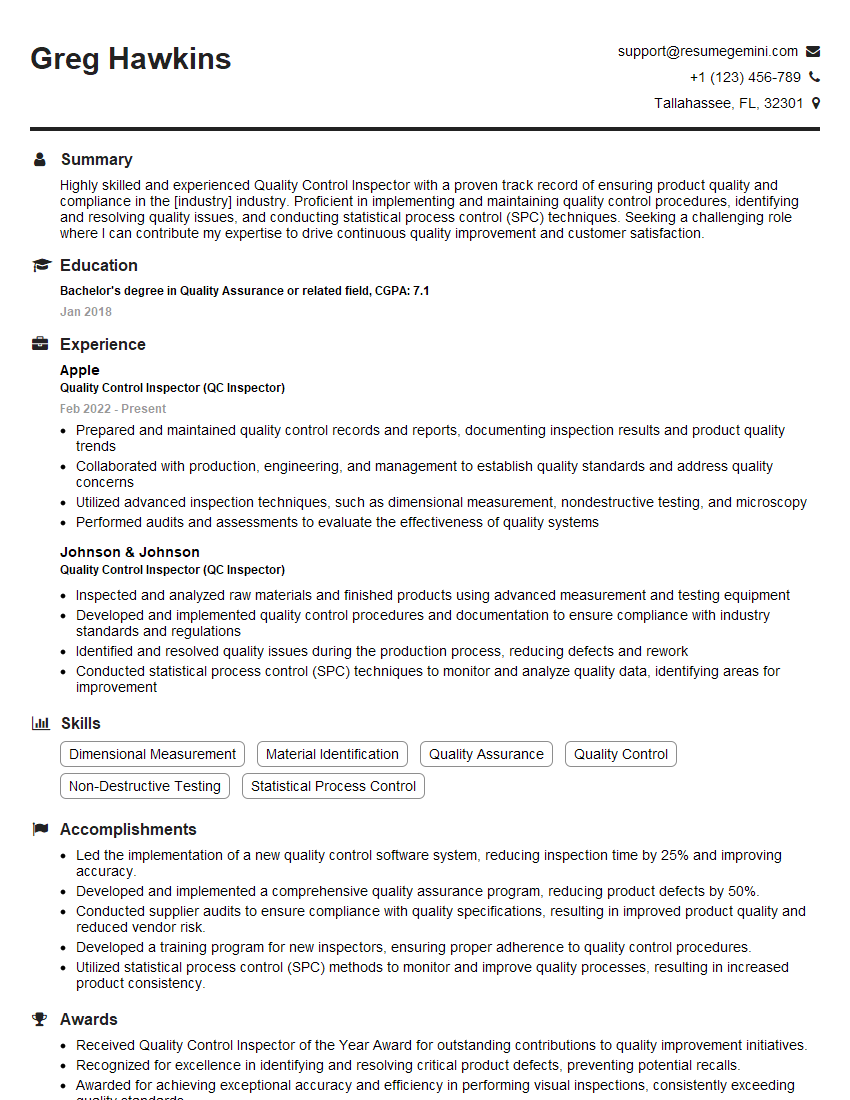