Are you gearing up for a career shift or aiming to ace your next interview? Look no further! We’ve curated a comprehensive guide to help you crack the interview for the coveted Safety Professional, Industrial Hygiene Consultant position. From understanding the key responsibilities to mastering the most commonly asked questions, this blog has you covered. So, buckle up and let’s embark on this journey together.
Acing the interview is crucial, but landing one requires a compelling resume that gets you noticed. Crafting a professional document that highlights your skills and experience is the first step toward interview success. ResumeGemini can help you build a standout resume that gets you called in for that dream job.
Essential Interview Questions For Safety Professional, Industrial Hygiene Consultant
1. Describe the key components of a comprehensive safety management system?
A comprehensive safety management system (SMS) should include the following key components
- Leadership and management commitment
- Hazard identification and risk assessment
- Risk control and mitigation
- Emergency preparedness and response
- Monitoring, evaluation, and improvement
2. What are the principles of industrial hygiene and how do they apply to your work?
Principles of Industrial Hygiene
- Anticipation
- Recognition
- Evaluation
- Control
Application to my work
- I use these principles to identify and assess workplace hazards, and to develop and implement control measures to protect workers.
- For example, I might use an exposure assessment to identify workers who are exposed to hazardous chemicals, and then develop and implement a ventilation system to reduce their exposure.
3. Explain the hierarchy of controls and how it can be used to eliminate or reduce workplace hazards?
The hierarchy of controls is a system for prioritizing the use of different types of control measures to eliminate or reduce workplace hazards.
- Elimination: This is the most effective way to control a hazard, and it involves removing the hazard from the workplace.
- Substitution: This involves replacing a hazardous substance or process with a less hazardous one.
- Engineering controls: These controls involve changing the physical environment of the workplace to reduce exposure to hazards.
- Administrative controls: These controls involve changing the way work is performed to reduce exposure to hazards.
- Personal protective equipment (PPE): This is the least effective way to control a hazard, and it involves providing workers with protective clothing or equipment to reduce their exposure to hazards.
4. What are the different types of air sampling methods and when should each be used?
- Grab sampling: This is a simple and inexpensive method that involves collecting a single sample of air over a short period of time.
- Integrated sampling: This method involves collecting a sample of air over a longer period of time, and it is used to measure the average exposure of workers to a hazard.
- Passive sampling: This method involves using a device that collects a sample of air over a long period of time, and it is used to measure the time-weighted average exposure of workers to a hazard.
5. What are the different types of noise hazards and how can they be controlled?
- Impact noise: This is caused by the sudden release of energy, such as a hammer hitting a nail.
- Continuous noise: This is caused by a continuous source of noise, such as a running machine.
- Intermittent noise: This is caused by a noise that occurs at regular intervals, such as a jackhammer.
- Noise hazards can be controlled using a variety of methods, such as
- Engineering controls: These involve changing the physical environment of the workplace to reduce noise exposure.
- Administrative controls: These involve changing the way work is performed to reduce noise exposure.
- Personal protective equipment (PPE): This involves providing workers with hearing protection to reduce their exposure to noise.
6. What are the different types of chemical hazards and how can they be controlled?
- Acute hazards: These are chemicals that can cause immediate harm, such as skin burns or eye irritation.
- Chronic hazards: These are chemicals that can cause harm over a long period of time, such as cancer or respiratory disease.
- Chemical hazards can be controlled using a variety of methods, such as
- Engineering controls: These involve changing the physical environment of the workplace to reduce exposure to chemicals.
- Administrative controls: These involve changing the way work is performed to reduce exposure to chemicals.
- Personal protective equipment (PPE): This involves providing workers with protective clothing or equipment to reduce their exposure to chemicals.
7. What are the different types of biological hazards and how can they be controlled?
- Bacteria: These are single-celled organisms that can cause a variety of infections.
- Viruses: These are smaller than bacteria and can also cause a variety of infections.
- Fungi: These are organisms that include molds and yeasts, and they can cause a variety of infections.
- Parasites: These are organisms that live on or in other organisms, and they can cause a variety of diseases.
- Biological hazards can be controlled using a variety of methods, such as
- Engineering controls: These involve changing the physical environment of the workplace to reduce exposure to biological hazards.
- Administrative controls: These involve changing the way work is performed to reduce exposure to biological hazards.
- Personal protective equipment (PPE): This involves providing workers with protective clothing or equipment to reduce their exposure to biological hazards.
8. What are the different types of physical hazards and how can they be controlled?
- Ergonomic hazards: These are hazards that can cause discomfort or injury to the musculoskeletal system.
- Electrical hazards: These are hazards that can cause electrical shock or burns.
- Fire hazards: These are hazards that can cause a fire.
- Machine hazards: These are hazards that can cause injury if a person comes into contact with a machine.
- Physical hazards can be controlled using a variety of methods, such as
- Engineering controls: These involve changing the physical environment of the workplace to reduce exposure to physical hazards.
- Administrative controls: These involve changing the way work is performed to reduce exposure to physical hazards.
- Personal protective equipment (PPE): This involves providing workers with protective clothing or equipment to reduce their exposure to physical hazards.
9. What are the different types of safety training and when should each be used?
- General safety training: This training is provided to all employees and covers basic safety topics, such as hazard recognition, risk assessment, and emergency procedures.
- Job-specific safety training: This training is provided to employees who work in specific jobs that have unique safety hazards.
- Supervisor safety training: This training is provided to supervisors who are responsible for the safety of their employees.
- Refresher safety training: This training is provided to employees on a regular basis to refresh their knowledge of safety topics.
10. What are the key elements of an effective safety culture?
- Leadership: Safety leadership is essential for creating and maintaining a positive safety culture.
- Communication: Open and effective communication is essential for ensuring that everyone in the organization is aware of safety hazards and risks.
- Employee involvement: Employees should be involved in all aspects of safety, including hazard identification, risk assessment, and control measures.
- Training: Employees should receive regular safety training to ensure that they are aware of safety hazards and risks.
- Accountability: Everyone in the organization should be held accountable for safety.
Interviewers often ask about specific skills and experiences. With ResumeGemini‘s customizable templates, you can tailor your resume to showcase the skills most relevant to the position, making a powerful first impression. Also check out Resume Template specially tailored for Safety Professional, Industrial Hygiene Consultant.
Career Expert Tips:
- Ace those interviews! Prepare effectively by reviewing the Top 50 Most Common Interview Questions on ResumeGemini.
- Navigate your job search with confidence! Explore a wide range of Career Tips on ResumeGemini. Learn about common challenges and recommendations to overcome them.
- Craft the perfect resume! Master the Art of Resume Writing with ResumeGemini’s guide. Showcase your unique qualifications and achievements effectively.
- Great Savings With New Year Deals and Discounts! In 2025, boost your job search and build your dream resume with ResumeGemini’s ATS optimized templates.
Researching the company and tailoring your answers is essential. Once you have a clear understanding of the Safety Professional, Industrial Hygiene Consultant‘s requirements, you can use ResumeGemini to adjust your resume to perfectly match the job description.
Key Job Responsibilities
Safety Professionals and Industrial Hygiene Consultants play crucial roles in ensuring the safety and health of individuals in various work environments. Their key responsibilities include:
1. Assessing and Identifying Hazards
Conduct thorough inspections of workplaces to identify potential hazards that can cause injuries, illnesses, or property damage. Assess risks associated with machinery, chemicals, processes, and work practices.
- Use specialized tools and equipment to measure and evaluate environmental conditions.
- Stay up-to-date on industry standards, regulations, and best practices.
2. Developing and Implementing Safety Programs
Create and implement comprehensive safety programs that are tailored to the specific needs of the organization. Conduct employee safety training, provide resources, and promote a culture of safety.
- Establish procedures for incident reporting, investigation, and follow-up.
- Collaborate with management and employees to ensure program implementation and compliance.
3. Monitoring and Evaluating Safety Performance
Regularly monitor and evaluate the effectiveness of safety programs. Conduct audits and inspections to ensure compliance and identify areas for improvement. Analyze accident and incident data to identify trends and make data-driven recommendations.
- Use metrics and key performance indicators (KPIs) to measure safety performance.
- Identify and implement corrective actions to prevent future incidents.
4. Consulting and Providing Expertise
Provide expert advice on occupational safety and health matters. Consult with clients to assess risks, develop strategies, and implement solutions. Conduct training sessions and workshops to educate and raise awareness.
- Serve as a resource for employees, managers, and other stakeholders.
- Collaborate with external organizations, such as insurance companies and regulatory agencies.
Interview Tips
Preparing for an interview as a Safety Professional or Industrial Hygiene Consultant requires thorough knowledge of the industry and key competencies. Here are some essential tips to help you ace the interview:
1. Research the Company and Position
Thoroughly research the company, its industry, and the specific position you are applying for. This will give you a strong understanding of the organization’s culture, values, and safety priorities.
- Visit the company’s website and social media pages.
- Read industry news and articles to stay informed about current trends and regulations.
2. Highlight Your Expertise and Experience
Emphasize your skills and experience in hazard identification, risk assessment, program development, and safety consulting. Provide specific examples of your accomplishments and how you have made a positive impact in previous roles.
- Quantify your achievements using concrete data, such as the number of hazards identified, incidents reduced, or safety programs implemented.
- Demonstrate your ability to work independently and as part of a team.
3. Prepare for Technical Questions
Be prepared to answer technical questions related to industrial hygiene, occupational safety, and risk management. Review fundamental principles and concepts, such as toxicology, ergonomics, and fire safety.
- Practice answering common interview questions about safety regulations, hazard analysis techniques, and incident investigation procedures.
- Bring a portfolio or examples of your previous work to showcase your technical proficiency.
4. Articulate Your Passion for Safety
Express your genuine passion for occupational safety and health. Explain how you have been involved in safety initiatives beyond your professional roles, such as volunteering or participating in industry organizations.
- Share examples of how your passion has motivated you to drive safety improvements.
- Explain how you plan to contribute to the safety culture of the organization.
Next Step:
Armed with this knowledge, you’re now well-equipped to tackle the Safety Professional, Industrial Hygiene Consultant interview with confidence. Remember, preparation is key. So, start crafting your resume, highlighting your relevant skills and experiences. Don’t be afraid to tailor your application to each specific job posting. With the right approach and a bit of practice, you’ll be well on your way to landing your dream job. Build your resume now from scratch or optimize your existing resume with ResumeGemini. Wish you luck in your career journey!
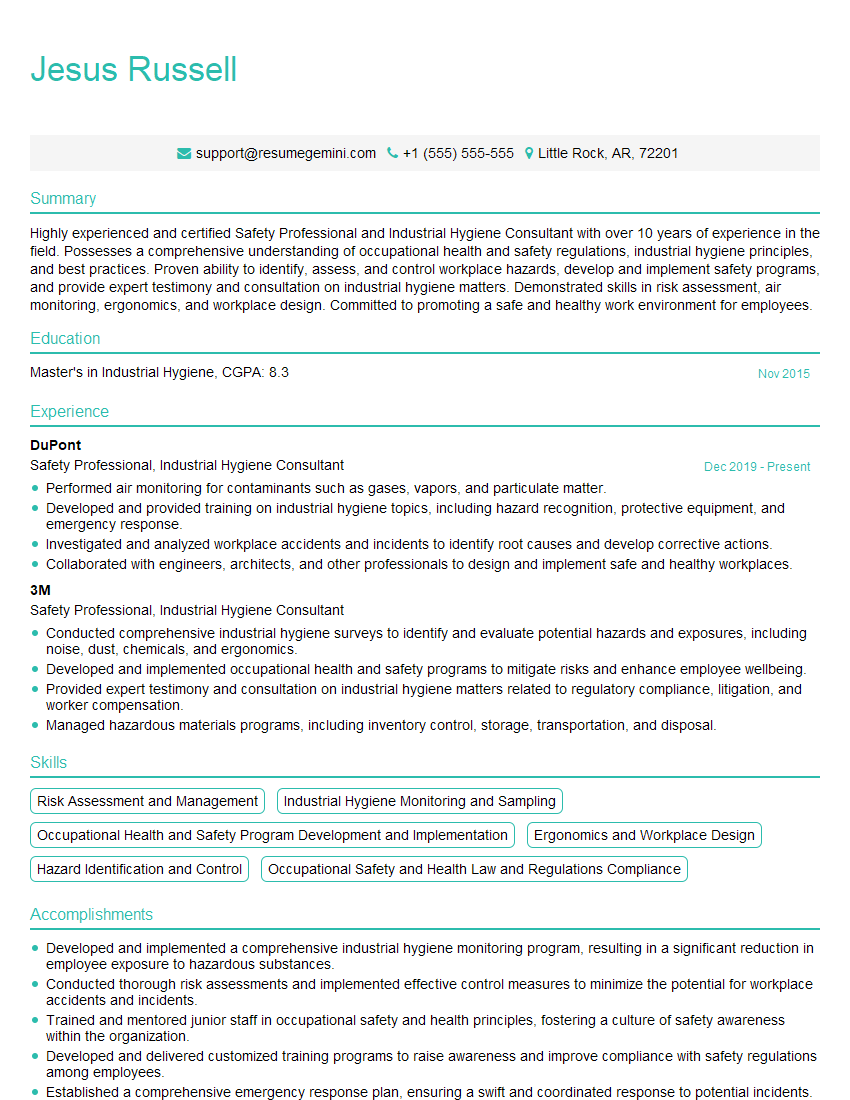