Are you gearing up for a career shift or aiming to ace your next interview? Look no further! We’ve curated a comprehensive guide to help you crack the interview for the coveted Sawmill Supervisor position. From understanding the key responsibilities to mastering the most commonly asked questions, this blog has you covered. So, buckle up and let’s embark on this journey together
Acing the interview is crucial, but landing one requires a compelling resume that gets you noticed. Crafting a professional document that highlights your skills and experience is the first step toward interview success. ResumeGemini can help you build a standout resume that gets you called in for that dream job.
Essential Interview Questions For Sawmill Supervisor
1. Describe the key performance indicators (KPIs) you would track and how you would use them to measure the success of the sawmill operation?
- Production volume: Measure the amount of lumber produced per shift or day to ensure we meet production targets.
- Lumber quality: Monitor the percentage of lumber that meets our quality standards to identify areas for improvement in sawing and handling practices.
- Machine efficiency: Track the uptime and utilization rates of sawmill equipment to optimize maintenance schedules and minimize downtime.
- Labor productivity: Measure the output per employee to assess staffing levels, training needs, and ergonomic considerations.
- Safety performance: Monitor incident rates and near-misses to ensure a safe working environment and compliance with regulations.
2. How would you optimize the breakdown and sawing processes to minimize waste and maximize lumber yield?
Breakdown Process Optimization
- Analyze log characteristics to determine optimal breakdown patterns that maximize value recovery.
- Use specialized equipment for precision cutting, such as log scanners and optimized saws, to reduce waste.
- Implement proper log handling techniques to minimize damage and maintain log integrity.
Sawing Process Optimization
- Set and maintain accurate saw blade settings to ensure precise cuts and minimize sawdust loss.
- Adjust sawing speed and feed rates based on wood species and log size to optimize yield.
- Implement proper blade maintenance and replacement schedules to ensure optimal cutting performance.
3. Explain the importance of log yard management and how you would ensure proper inventory control and log quality?
- Establish a systematic log inventory system to track incoming and outgoing logs, ensuring accurate records for production planning and accounting.
- Implement quality control measures at the log yard to segregate logs based on species, grade, and size, ensuring proper utilization.
- Regularly inspect logs for defects, damage, or decay to identify potential issues and prevent them from affecting production.
4. How would you manage and train your team of sawyers and mill operators to maintain a high level of productivity and safety?
- Establish clear job roles and responsibilities to ensure everyone understands their tasks and contributes effectively.
- Provide comprehensive training on sawmill equipment, safety protocols, and production techniques.
- Conduct regular performance evaluations and provide feedback to help employees identify areas for improvement.
- Foster a positive and collaborative work environment where employees feel valued and motivated to excel.
- Encourage a culture of continuous improvement by seeking suggestions from employees and implementing practical solutions.
5. What are the key safety precautions you would implement in the sawmill operation, and how would you ensure compliance?
- Conduct regular safety inspections and risk assessments to identify and mitigate potential hazards.
- Enforce the use of appropriate personal protective equipment (PPE) such as hard hats, safety glasses, and earplugs.
- Establish clear safety protocols for machine operation, log handling, and maintenance procedures.
- Provide ongoing safety training and refresher courses to keep employees informed and up-to-date on best practices.
- Conduct regular safety audits and involve employees in the process to promote accountability and ownership.
6. How would you maintain and troubleshoot sawmill equipment to minimize downtime and ensure efficient operation?
- Implement a preventative maintenance schedule based on manufacturer recommendations and equipment usage.
- Establish a system for regular inspections and condition monitoring to identify potential issues early on.
- Maintain an inventory of spare parts and consumables to minimize downtime in case of breakdowns.
- Train staff on basic troubleshooting techniques and empower them to resolve minor issues promptly.
- Collaborate with equipment manufacturers or service providers for complex repairs and upgrades.
7. Describe the quality control procedures you would implement to ensure the production of high-quality lumber that meets customer specifications.
- Establish clear lumber grading standards and quality specifications based on industry regulations and customer requirements.
- Conduct regular lumber inspections throughout the production process to identify and remove defective pieces.
- Use calibrated measuring and grading equipment to ensure accuracy and consistency.
- Implement a system for customer feedback and complaint handling to address quality concerns promptly.
- Continuously monitor and improve quality control processes based on data analysis and customer feedback.
8. How would you manage production schedules and coordinate with other departments, such as log procurement and sales, to ensure smooth operation and timely delivery to customers?
- Develop and maintain a master production schedule that aligns with sales commitments and log availability.
- Coordinate with log procurement to ensure a steady supply of logs that meet production requirements.
- Communicate production progress and potential delays to sales and logistics departments to manage customer expectations.
- Establish clear communication channels and regular meetings to facilitate coordination and resolve any issues promptly.
9. How do you stay up-to-date on the latest technologies and best practices in the sawmill industry?
- Attend industry conferences, seminars, and trade shows to learn about new technologies and trends.
- Read industry publications and subscribe to newsletters to stay informed about advancements in sawmill equipment, techniques, and regulations.
- Network with other sawmill professionals and exchange ideas and experiences to identify areas for improvement.
- Explore research and development initiatives within the industry to gain insights into emerging technologies and practices.
10. How would you handle a situation where there is a conflict or disagreement between employees or departments?
- Facilitate open and respectful communication between the parties involved to understand their perspectives.
- Identify the root cause of the conflict and work towards a solution that addresses the underlying issues.
- Seek input and collaborate with other relevant stakeholders, such as supervisors or HR, as needed.
- Establish clear guidelines and expectations to prevent similar conflicts from occurring in the future.
- Maintain a positive and professional demeanor throughout the process, even in challenging situations.
Interviewers often ask about specific skills and experiences. With ResumeGemini‘s customizable templates, you can tailor your resume to showcase the skills most relevant to the position, making a powerful first impression. Also check out Resume Template specially tailored for Sawmill Supervisor.
Career Expert Tips:
- Ace those interviews! Prepare effectively by reviewing the Top 50 Most Common Interview Questions on ResumeGemini.
- Navigate your job search with confidence! Explore a wide range of Career Tips on ResumeGemini. Learn about common challenges and recommendations to overcome them.
- Craft the perfect resume! Master the Art of Resume Writing with ResumeGemini’s guide. Showcase your unique qualifications and achievements effectively.
- Great Savings With New Year Deals and Discounts! In 2025, boost your job search and build your dream resume with ResumeGemini’s ATS optimized templates.
Researching the company and tailoring your answers is essential. Once you have a clear understanding of the Sawmill Supervisor‘s requirements, you can use ResumeGemini to adjust your resume to perfectly match the job description.
Key Job Responsibilities
Sawmill Supervisors oversee all aspects of sawmill operations, ensuring efficient and safe production of lumber and other wood products. Their primary responsibilities include:
1. Production Management
Supervise and coordinate production activities to meet targets for quantity, quality, and delivery.
- Monitor production schedules and adjust operations to optimize efficiency.
- Identify and address production bottlenecks and inefficiencies.
2. Quality Control
Implement and maintain quality control standards for lumber and wood products.
- Inspect raw materials and finished products to ensure they meet specifications.
- Resolve quality issues and implement corrective actions to prevent defects.
3. Equipment Management
Oversee the maintenance and operation of sawmill equipment, including saws, kilns, and conveyors.
- Schedule and coordinate equipment maintenance and repairs.
- Ensure equipment is operating safely and efficiently.
4. Safety Management
Implement and enforce safety policies and procedures to prevent accidents and injuries.
- Conduct safety inspections and identify potential hazards.
- Provide training to employees on safety protocols.
5. Employee Management
Lead and motivate a team of employees, including sawyers, graders, and equipment operators.
- Hire, train, and evaluate employees.
- Resolve employee issues and maintain a positive work environment.
Interview Tips
To ace an interview for a Sawmill Supervisor position, candidates should highlight their skills in production management, quality control, equipment maintenance, safety management, and employee leadership. Here are some tips to prepare:
1. Research the Company and Position
Thoroughly research the sawmill industry and the specific company you are applying to. Familiarize yourself with their products, production methods, and safety standards.
- Visit the company website and social media pages.
- Read industry publications and reports.
2. Highlight Relevant Skills and Experience
During the interview, emphasize your experience in supervising sawmill operations, managing production, maintaining equipment, and ensuring safety. Quantify your accomplishments whenever possible.
- Provide specific examples of how you improved production efficiency or reduced waste.
- Describe your role in implementing or improving safety protocols.
3. Demonstrate Leadership Abilities
Sawmill Supervisors are responsible for leading and motivating a team. Showcase your leadership skills by highlighting your experience in managing, training, and evaluating employees. Provide examples of how you created a positive work environment and resolved conflicts.
- Emphasize your communication and interpersonal skills.
- Describe how you motivate and inspire your team to achieve goals.
4. Prepare Thoughtful Questions
Asking thoughtful questions at the end of the interview shows that you are engaged and interested in the position. Prepare questions that demonstrate your knowledge of the industry and your commitment to safety and sustainability.
- Ask about the company’s environmental policies and initiatives.
- Inquire about opportunities for professional development and advancement.
Next Step:
Now that you’re armed with interview-winning answers and a deeper understanding of the Sawmill Supervisor role, it’s time to take action! Does your resume accurately reflect your skills and experience for this position? If not, head over to ResumeGemini. Here, you’ll find all the tools and tips to craft a resume that gets noticed. Don’t let a weak resume hold you back from landing your dream job. Polish your resume, hit the “Build Your Resume” button, and watch your career take off! Remember, preparation is key, and ResumeGemini is your partner in interview success.
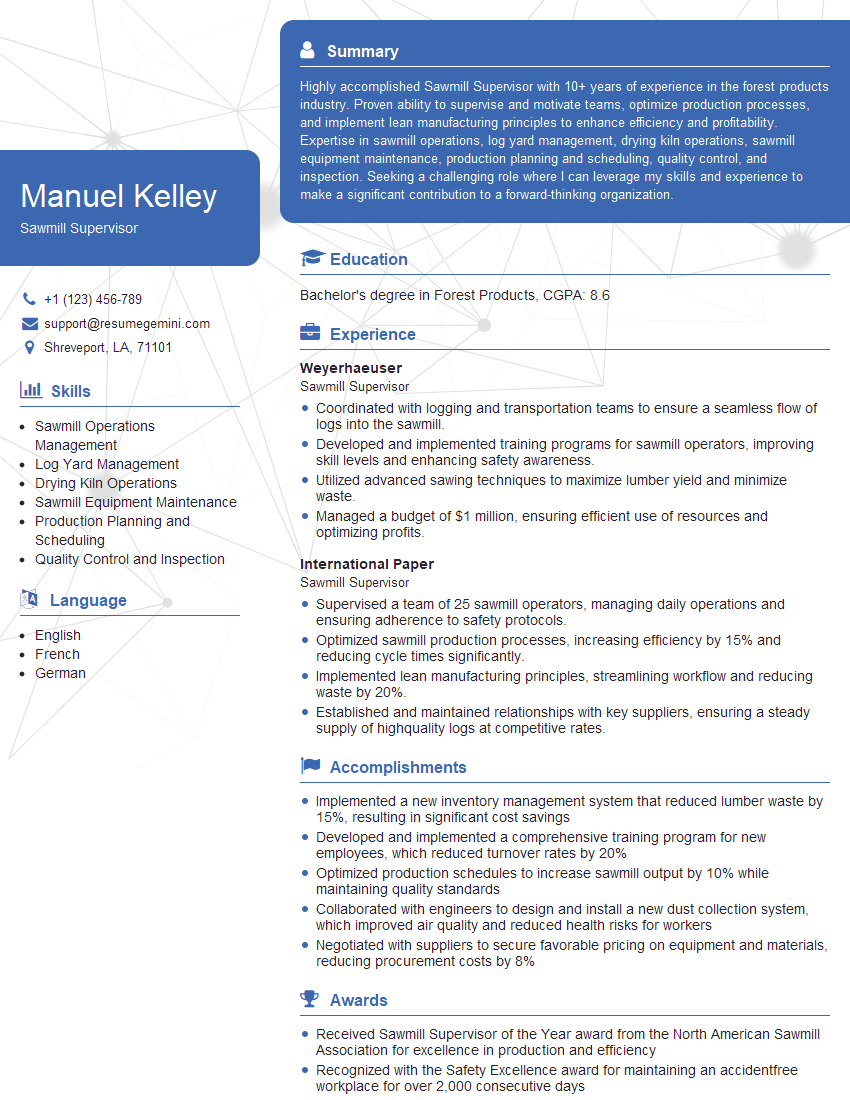