Are you gearing up for a career in Sheet Metal Worker? Feeling nervous about the interview questions that might come your way? Don’t worry, you’re in the right place. In this blog post, we’ll dive deep into the most common interview questions for Sheet Metal Worker and provide you with expert-backed answers. We’ll also explore the key responsibilities of this role so you can tailor your responses to showcase your perfect fit.
Acing the interview is crucial, but landing one requires a compelling resume that gets you noticed. Crafting a professional document that highlights your skills and experience is the first step toward interview success. ResumeGemini can help you build a standout resume that gets you called in for that dream job.
Essential Interview Questions For Sheet Metal Worker
1. Describe the process of fabricating a sheet metal duct.
The process of fabricating a sheet metal duct involves several steps:
- Design and layout: The design specifications are reviewed, and the sheet metal is marked and cut to the desired dimensions.
- Forming: The sheet metal is formed into the required shape using a variety of techniques, such as bending, rolling, or stamping.
- Assembly: The formed pieces are assembled and joined together using techniques such as welding, soldering, or riveting.
- Finishing: The duct is finished with a protective coating, such as paint or galvanizing, to prevent corrosion and enhance durability.
2. What is the difference between galvanized steel and stainless steel?
Corrosion resistance:
- Galvanized steel has a zinc coating that protects the steel from corrosion.
- Stainless steel has a chromium oxide layer that provides excellent corrosion resistance.
Strength:
- Galvanized steel is weaker than stainless steel due to the zinc coating.
- Stainless steel is stronger and more durable.
Cost:
- Galvanized steel is less expensive than stainless steel.
3. What are the different types of sheet metal fabrication techniques?
Various sheet metal fabrication techniques are used to create different shapes and components. These include:
- Bending: Used to create angles and curves.
- Rolling: Used to form cylindrical or conical shapes.
- Stamping: Used to create complex shapes by pressing the sheet metal into a mold.
- Welding: Used to join pieces of sheet metal together.
- Soldering: Used to join pieces of sheet metal together using a molten metal alloy.
- Riveting: Used to join pieces of sheet metal together using rivets.
4. What are the advantages of using sheet metal for ductwork?
Sheet metal is a popular material for ductwork due to its several advantages:
- Lightweight: Sheet metal is lightweight, making it easy to handle and install.
- Durable: Sheet metal is durable and can withstand harsh conditions.
- Versatile: Sheet metal can be formed into a variety of shapes and sizes.
- Cost-effective: Sheet metal is a relatively inexpensive material.
5. What are the safety precautions to consider when working with sheet metal?
Working with sheet metal requires adherence to safety precautions to minimize risks:
- Wear appropriate protective gear: Wear safety glasses, gloves, and protective clothing to prevent injuries from sharp edges and flying debris.
- Use sharp tools and equipment: Dull tools can slip and cause accidents. Keep tools and equipment sharp and in good working condition.
- Be aware of your surroundings: Pay attention to your surroundings and be mindful of potential hazards, such as tripping hazards or moving machinery.
- Follow established procedures: Follow established safety protocols and procedures to minimize risks.
6. What is the purpose of using a slip roll machine?
A slip roll machine is a specialized tool used in sheet metal fabrication to create cylindrical shapes, such as tubes or pipes, from flat sheet metal.
- Versatile: It allows for the production of cylinders of various diameters and lengths.
- Precise: The machine ensures accurate and consistent bending, resulting in uniform cylindrical shapes.
- Efficient: Slip roll machines offer a fast and efficient method of forming cylindrical shapes compared to manual bending.
7. Describe the process of soldering sheet metal.
Soldering involves joining two pieces of sheet metal using a molten metal alloy, known as solder, that has a lower melting point than the sheet metal.
- Surface preparation: The surfaces to be joined are cleaned and fluxed to enhance adhesion.
- Heat application: A soldering iron or torch is used to heat the joint area.
- Solder application: Solder is applied to the joint, melting and flowing between the sheet metal surfaces.
- Cooling: The joint is allowed to cool, solidifying the solder and creating a strong bond.
8. What are the different types of welding processes used in sheet metal fabrication?
Various welding processes are employed in sheet metal fabrication, each with its unique characteristics:
- MIG (Metal Inert Gas) Welding: Uses a continuously fed wire electrode and an inert gas to protect the weld pool.
- TIG (Tungsten Inert Gas) Welding: Uses a non-consumable tungsten electrode and an inert gas to create a high-quality weld.
- Spot Welding: Involves using two copper electrodes to apply pressure and heat to specific points on the sheet metal, creating localized welds.
- Arc Welding: Uses an electric arc to generate heat and create a weld joint between the sheet metal pieces.
9. What tools and equipment are essential for sheet metal fabrication?
Sheet metal fabrication requires a range of specialized tools and equipment:
- Sheet metal shears: Used to cut straight lines in sheet metal.
- Nibbler: A handheld tool for cutting irregular shapes and curves.
- Brake: Used to bend sheet metal into angles and shapes.
- Roll forming machine: Forms sheet metal into cylindrical or conical shapes.
- Welding equipment: MIG, TIG, or spot welders for joining sheet metal pieces.
10. How do you ensure the accuracy and quality of sheet metal products?
Ensuring accuracy and quality in sheet metal products involves several practices:
- Precise measurements: Using accurate measuring tools and techniques to ensure correct dimensions.
- Proper layout: Creating detailed layouts to guide the fabrication process and minimize errors.
- Quality materials: Selecting high-quality sheet metal and materials to meet the required specifications.
- Skilled craftsmanship: Employing experienced and skilled sheet metal workers to execute the fabrication process.
- Quality control: Implementing quality control measures throughout the fabrication process to identify and correct any errors.
Interviewers often ask about specific skills and experiences. With ResumeGemini‘s customizable templates, you can tailor your resume to showcase the skills most relevant to the position, making a powerful first impression. Also check out Resume Template specially tailored for Sheet Metal Worker.
Career Expert Tips:
- Ace those interviews! Prepare effectively by reviewing the Top 50 Most Common Interview Questions on ResumeGemini.
- Navigate your job search with confidence! Explore a wide range of Career Tips on ResumeGemini. Learn about common challenges and recommendations to overcome them.
- Craft the perfect resume! Master the Art of Resume Writing with ResumeGemini’s guide. Showcase your unique qualifications and achievements effectively.
- Great Savings With New Year Deals and Discounts! In 2025, boost your job search and build your dream resume with ResumeGemini’s ATS optimized templates.
Researching the company and tailoring your answers is essential. Once you have a clear understanding of the Sheet Metal Worker‘s requirements, you can use ResumeGemini to adjust your resume to perfectly match the job description.
Key Job Responsibilities
Sheet metal workers are skilled tradespeople who work with sheet metal to create various products and structures. Their responsibilities include planning, layout, fabrication, installation, and repair of sheet metal components and systems.
1. Planning and Layout
Sheet metal workers read and interpret blueprints and drawings to determine the shape, size, and location of the sheet metal components they need to fabricate.
- Lay out the work area and determine the most efficient way to cut and shape the sheet metal.
- Select and use appropriate tools and equipment, such as shears, brakes, and welding machines.
2. Fabrication
Sheet metal workers use a variety of tools and techniques to fabricate sheet metal components.
- Cut, bend, and shape sheet metal to create the desired shape and size.
- Weld, solder, or rivet sheet metal components together to create a strong and durable joint.
3. Installation
Sheet metal workers install sheet metal components and systems in a variety of applications.
- Install ductwork for heating, ventilation, and air conditioning systems.
- Install roofing and siding on buildings.
- Install gutters and downspouts to direct water away from buildings.
4. Repair
Sheet metal workers also repair and maintain sheet metal components and systems.
- Repair or replace damaged ductwork, roofing, siding, gutters, and downspouts.
- Inspect sheet metal components and systems for signs of wear and tear.
- Clean and maintain sheet metal components and systems to ensure they are functioning properly.
Interview Tips
Preparing for a sheet metal worker interview can help you make a great impression on the hiring manager and increase your chances of getting the job. Here are some tips to help you prepare.
1. Research the Company and the Position
Take some time to learn about the company you’re applying to and the specific position you’re interested in. This will help you understand the company’s culture, values, and goals.
- Visit the company’s website and social media pages.
- Read articles and news stories about the company.
- Talk to people you know who work for the company.
2. Practice Your Answers to Common Interview Questions
There are a few common interview questions that you’re likely to be asked, such as “Tell me about yourself” and “Why are you interested in this position?” Practice answering these questions in a clear and concise way.
- Use the STAR method to answer behavioral questions.
- Tailor your answers to the specific position you’re applying for.
- Practice answering questions out loud so that you can become more comfortable speaking in front of others.
3. Bring a Portfolio of Your Work
If you have a portfolio of your work, bring it with you to the interview. This will give the hiring manager a chance to see your skills and experience firsthand.
- Include examples of your best work.
- Label each piece with a brief description of the project.
- Be prepared to talk about your portfolio in detail.
4. Dress Professionally
First impressions matter, so make sure you dress professionally for your interview. This means wearing clean, pressed clothes and shoes.
- Avoid wearing casual clothing, such as jeans and t-shirts.
- Consider wearing a suit or dress pants and a button-down shirt.
- Make sure your clothes are clean and pressed.
Next Step:
Now that you’re armed with interview-winning answers and a deeper understanding of the Sheet Metal Worker role, it’s time to take action! Does your resume accurately reflect your skills and experience for this position? If not, head over to ResumeGemini. Here, you’ll find all the tools and tips to craft a resume that gets noticed. Don’t let a weak resume hold you back from landing your dream job. Polish your resume, hit the “Build Your Resume” button, and watch your career take off! Remember, preparation is key, and ResumeGemini is your partner in interview success.
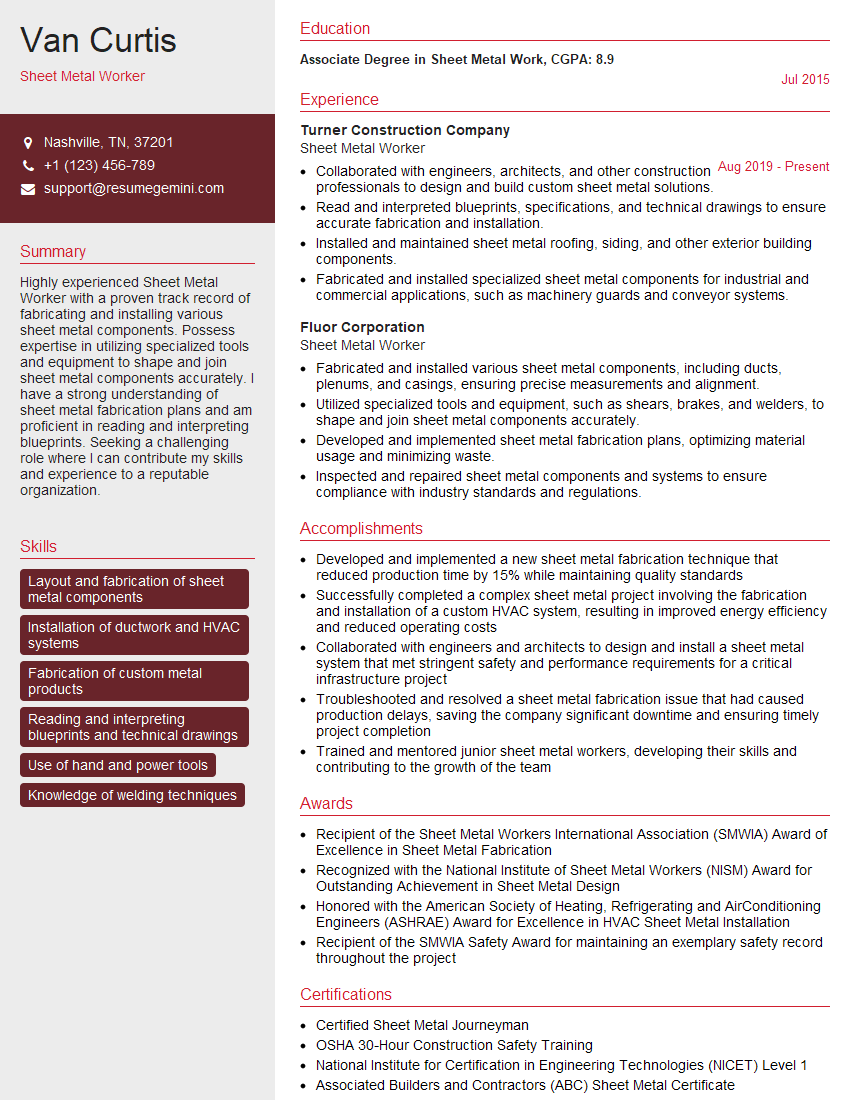