Are you gearing up for an interview for a Tubing Assembler position? Whether you’re a seasoned professional or just stepping into the role, understanding what’s expected can make all the difference. In this blog, we dive deep into the essential interview questions for Tubing Assembler and break down the key responsibilities of the role. By exploring these insights, you’ll gain a clearer picture of what employers are looking for and how you can stand out. Read on to equip yourself with the knowledge and confidence needed to ace your next interview and land your dream job!
Acing the interview is crucial, but landing one requires a compelling resume that gets you noticed. Crafting a professional document that highlights your skills and experience is the first step toward interview success. ResumeGemini can help you build a standout resume that gets you called in for that dream job.
Essential Interview Questions For Tubing Assembler
1. Describe the process of cutting and preparing tubing for assembly.
The process of cutting and preparing tubing for assembly involves:
- Selecting the correct tubing size and material based on the assembly requirements.
- Measuring and marking the tubing to the required length using measuring tape and markers.
- Cutting the tubing using a tube cutter or bandsaw, ensuring clean and perpendicular cuts.
- Deburring the cut edges to remove any sharp edges using a file or deburring tool.
- Cleaning the tubing to remove any dirt, oil, or debris that may affect the assembly process.
2. Explain the various types of tubing connections used in assembly and their respective advantages and disadvantages.
Compression Fittings
- Advantages: Simple to assemble and disassemble, no welding or soldering required.
- Disadvantages: Can leak if not tightened properly, not suitable for high-pressure applications.
Flare Fittings
- Advantages: Secure and leak-proof, can withstand high pressures.
- Disadvantages: Requires specialized tools and skills to assemble, more time-consuming.
Soldered Joints
- Advantages: Strong and permanent, suitable for high-pressure and high-temperature applications.
- Disadvantages: Requires specialized equipment and skills, cannot be disassembled easily.
3. How do you ensure the accuracy and quality of assembled tubing systems?
I ensure the accuracy and quality of assembled tubing systems through the following methods:
- Following precise measurements and specifications during cutting and assembly.
- Using calibrated measuring equipment and tools to ensure accuracy.
- Inspecting connections for proper fit, alignment, and tightness.
- Conducting pressure and leak tests to verify the integrity of the assembled system.
- Adhering to established quality standards and procedures.
4. Discuss the importance of material compatibility when selecting tubing and fittings.
Material compatibility is crucial when selecting tubing and fittings to ensure the proper functioning and longevity of the assembled system.
- Incompatibility can lead to corrosion, leaks, or premature failure.
- Selecting materials with similar thermal expansion coefficients minimizes stress and maintains seal integrity.
- Considering the chemical compatibility of the tubing and fittings with the fluids being conveyed prevents degradation or contamination.
- Adhering to industry standards and guidelines helps ensure material compatibility.
5. Describe the safety precautions you observe while working with tubing systems.
I prioritize safety while working with tubing systems by:
- Wearing appropriate personal protective equipment (PPE), including safety glasses, gloves, and earplugs.
- Inspecting tubing and fittings for damage or defects before assembly.
- Using proper cutting and assembly techniques to prevent injuries.
- Handling high-pressure systems with caution, following established procedures.
- Being aware of potential hazards, such as leaks, spills, or electrical risks.
6. Explain the role of bending machines in tubing assembly and the different types available.
Role of Bending Machines
- Create precise bends in tubing without kinking or flattening.
- Maintain the integrity and flow characteristics of the tubing.
Types of Bending Machines
- Mandrel Benders: Use a mandrel to support the inside of the tubing during bending, preventing deformation.
- Rotary Draw Benders: Draw the tubing through a series of rollers, producing smooth and consistent bends.
- Compression Benders: Bend tubing by compressing it between two dies, suitable for smaller diameters.
7. How do you troubleshoot common problems encountered during tubing assembly?
When encountering problems during tubing assembly, I follow these troubleshooting steps:
- Inspect the tubing and fittings for defects or damage.
- Verify that the correct tools and techniques are being used.
- Check the accuracy of measurements and dimensions.
- Tighten connections properly, but avoid overtightening.
- Conduct pressure and leak tests to identify potential issues.
- Refer to technical manuals and industry standards for guidance.
8. Describe the maintenance and inspection procedures for tubing systems.
To ensure the optimal performance and longevity of tubing systems, I perform regular maintenance and inspection procedures:
- Visually inspect tubing and fittings for leaks, damage, or corrosion.
- Tighten connections periodically to prevent loosening.
- Conduct pressure tests to verify system integrity.
- Clean and lubricate moving parts, if applicable.
- Document inspection and maintenance activities for future reference.
9. How do you stay updated with the latest industry standards and advancements in tubing assembly techniques?
To stay abreast of industry advancements, I engage in the following practices:
- Attend industry conferences and workshops.
- Read technical articles and journals.
- Participate in online forums and discussion groups.
- Obtain certifications or licenses related to tubing assembly.
- Consult with experienced professionals and experts.
10. Describe your experience in working with different materials and sizes of tubing.
Throughout my career as a Tubing Assembler, I have gained experience working with a diverse range of materials and sizes of tubing, including:
- Copper
- Stainless Steel
- Aluminum
- Plastic
- Diameters ranging from 1/4 inch to 2 inches
- Wall thicknesses varying from thin-walled to heavy-duty
This experience has equipped me with the skills and knowledge to handle and assemble tubing effectively, ensuring the integrity and performance of the final product.
Interviewers often ask about specific skills and experiences. With ResumeGemini‘s customizable templates, you can tailor your resume to showcase the skills most relevant to the position, making a powerful first impression. Also check out Resume Template specially tailored for Tubing Assembler.
Career Expert Tips:
- Ace those interviews! Prepare effectively by reviewing the Top 50 Most Common Interview Questions on ResumeGemini.
- Navigate your job search with confidence! Explore a wide range of Career Tips on ResumeGemini. Learn about common challenges and recommendations to overcome them.
- Craft the perfect resume! Master the Art of Resume Writing with ResumeGemini’s guide. Showcase your unique qualifications and achievements effectively.
- Great Savings With New Year Deals and Discounts! In 2025, boost your job search and build your dream resume with ResumeGemini’s ATS optimized templates.
Researching the company and tailoring your answers is essential. Once you have a clear understanding of the Tubing Assembler‘s requirements, you can use ResumeGemini to adjust your resume to perfectly match the job description.
Key Job Responsibilities
Tubing Assemblers are responsible for assembling and inspecting tubing used in various industries, including automotive, medical, and construction. Their primary duties involve ensuring the accuracy and quality of the assembled tubing products.
1. Assembly of Tubing Components
Tubing Assemblers utilize specialized tools and equipment to join different tubing components, such as fittings, connectors, and valves. They follow detailed specifications and drawings to ensure proper assembly and leak-proof connections.
2. Inspection and Testing
To guarantee the integrity and performance of the assembled tubing, Tubing Assemblers conduct thorough inspections and tests. They check for leaks, ensure proper dimensions and tolerances, and verify the functionality of the assembled products.
3. Quality Control and Documentation
Tubing Assemblers maintain strict quality control standards to ensure the highest level of accuracy and precision. They record assembly and inspection data, maintaining detailed documentation for traceability and compliance.
4. Operation of Specialized Machinery
Tubing Assemblers are often required to operate specialized machinery, such as bending machines, cutting tools, and welding equipment. They must be proficient in these operations to ensure efficient and accurate assembly processes.
Interview Tips
To ace an interview for a Tubing Assembler position, candidates should focus on highlighting their relevant skills, experience, and attention to detail. Here are some key tips:
1. Emphasize Precision and Accuracy
Tubing Assemblers must be meticulous and detail-oriented. Candidates should emphasize their ability to follow instructions precisely, maintain tight tolerances, and produce high-quality work.
2. Highlight Hands-on Experience
Prior experience in tubing assembly or related fields is highly valued. Candidates should discuss specific projects they have worked on, showcasing their proficiency in using specialized equipment and following assembly protocols.
3. Demonstrate Knowledge of Quality Standards
Inquire about the company’s quality standards and regulations. Candidates should demonstrate their understanding of industry best practices and their commitment to meeting or exceeding quality expectations.
4. Practice Interview Questions
Prepare for common interview questions tailored to the Tubing Assembler role. These may include questions about experience with specific machinery, inspection techniques, and quality control procedures.
5. Dress Professionally and Arrive On Time
First impressions matter. Dress professionally for the interview and arrive on time to show respect for the employer’s time. A positive and enthusiastic demeanor can also make a significant impact.
By effectively highlighting their relevant skills and experience, and by demonstrating their commitment to precision, quality, and attention to detail, candidates can increase their chances of success in a Tubing Assembler interview.Next Step:
Now that you’re armed with a solid understanding of what it takes to succeed as a Tubing Assembler, it’s time to turn that knowledge into action. Take a moment to revisit your resume, ensuring it highlights your relevant skills and experiences. Tailor it to reflect the insights you’ve gained from this blog and make it shine with your unique qualifications. Don’t wait for opportunities to come to you—start applying for Tubing Assembler positions today and take the first step towards your next career milestone. Your dream job is within reach, and with a polished resume and targeted applications, you’ll be well on your way to achieving your career goals! Build your resume now with ResumeGemini.
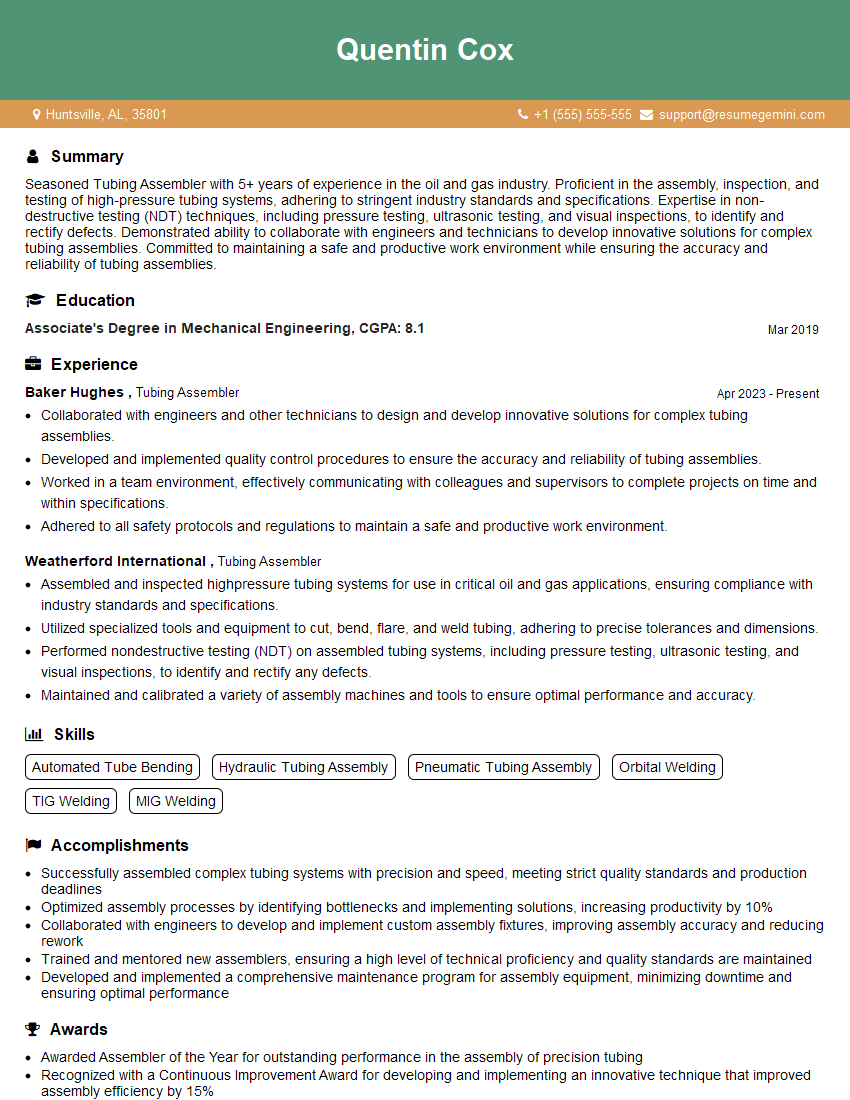