Are you gearing up for an interview for a Welt Maker position? Whether you’re a seasoned professional or just stepping into the role, understanding what’s expected can make all the difference. In this blog, we dive deep into the essential interview questions for Welt Maker and break down the key responsibilities of the role. By exploring these insights, you’ll gain a clearer picture of what employers are looking for and how you can stand out. Read on to equip yourself with the knowledge and confidence needed to ace your next interview and land your dream job!
Acing the interview is crucial, but landing one requires a compelling resume that gets you noticed. Crafting a professional document that highlights your skills and experience is the first step toward interview success. ResumeGemini can help you build a standout resume that gets you called in for that dream job.
Essential Interview Questions For Welt Maker
1. Can you describe the process of creating a 3D model in a digital sculpting program?
In digital sculpting, I typically follow these steps to create a 3D model:
- Blocking out the basic shape: Using primitives or spheres, I define the overall form and proportions of the model.
- Refining the shape: I sculpt and refine the model’s details using brushes that mimic real-world sculpting tools like clay or wax.
- Adding textures: I apply color and surface details to the model using brushes or texture maps.
- Rigging and animation: If necessary, I create a bone structure and set up animations to bring the model to life.
- Rendering: Finally, I render the model to generate high-quality images or animations for use in various applications.
2. What are the common types of 3D printing technologies and their respective strengths and limitations?
Fused Deposition Modeling (FDM)
- Strengths: Affordable, widely accessible, produces strong parts.
- Limitations: Limited resolution, visible layer lines on printed surfaces.
Stereolithography (SLA)
- Strengths: High accuracy, smooth surface finish.
- Limitations: Requires post-processing (washing, curing), can be expensive.
Selective Laser Sintering (SLS)
- Strengths: Produces durable, complex parts, good for functional applications.
- Limitations: Can be more expensive, sometimes requires post-processing (de-powdering).
3. How do you approach optimizing a 3D model for 3D printing, and what are some key considerations?
To optimize a 3D model for 3D printing, I consider the following:
- Geometry: Ensuring the model is watertight, has no self-intersections, and meets minimum wall thickness requirements.
- Resolution: Adjusting the model’s resolution to balance detail with printability.
- Orientation: Positioning the model for optimal printing to minimize support material and ensure structural integrity.
- Slicing settings: Choosing the appropriate layer height, infill density, and other slicer settings for the desired print quality and strength.
- Post-processing: Considering any necessary post-processing steps, such as support removal, sanding, or painting.
4. What are the key factors that affect the quality of a 3D printed part, and how can you control them?
Factors affecting 3D print quality include:
- Printer calibration: Ensuring the printer is properly calibrated to maintain accuracy and precision.
- Material selection: Choosing the appropriate material for the desired properties (strength, flexibility, color).
- Slicing settings: Optimizing print settings for the specific material and model.
- Environmental conditions: Controlling temperature and humidity during printing to prevent warping or layer separation.
- Maintenance and troubleshooting: Regularly cleaning and inspecting the printer, and addressing any issues promptly.
5. How do you handle the design and iteration process when developing a new 3D model, and how do you incorporate feedback from stakeholders?
My design and iteration process involves:
- Initial concept: Generating ideas and brainstorming with stakeholders.
- Digital sculpting: Creating a rough 3D model to explore the form and functionality.
- Feedback and refinement: Gathering feedback from stakeholders and incorporating it to improve the model.
- Prototyping: 3D printing or rapid prototyping to test the model’s physical properties and user experience.
- Finalization: Refining the model based on prototyping results and feedback.
6. How do you stay up-to-date with the latest technologies and trends in 3D modeling and 3D printing?
I keep updated on the latest technologies and trends through:
- Industry events and conferences: Attending workshops, seminars, and exhibitions.
- Online resources: Reading industry blogs, magazines, and technical articles.
- Online communities: Engaging in online forums and discussion groups.
- Collaboration with experts: Connecting with other professionals and learning from their experiences.
- Hands-on experimentation: Continuously testing new techniques and technologies in my own projects.
7. What are some of the challenges you have faced in your career as a Welt Maker, and how did you overcome them?
One challenge I encountered was creating a highly detailed and complex 3D model for a medical device. To overcome this, I used a combination of digital sculpting and 3D scanning techniques to capture intricate anatomical features and ensure accuracy.
Another challenge was optimizing a 3D model for large-scale 3D printing. I collaborated with an engineer to analyze the model’s structure and modify it for efficient printing while maintaining its functionality.
8. Can you describe your workflow for creating a realistic 3D character model?
Concept and Reference Gathering
- Develop a concept for the character’s appearance, personality, and backstory.
- Collect reference images and materials for inspiration and anatomical accuracy.
Modeling and Sculpting
- Start with a rough base mesh to define the character’s proportions and body shape.
- Use digital sculpting tools to refine the model, adding details, textures, and expressions.
Texturing and Shading
- Create color maps, normal maps, and other textures to give the model realistic surface details.
- Set up lighting and materials to enhance the model’s appearance.
Rigging and Animation
- Create a bone structure to control the character’s movement.
- Animate the character using various techniques, such as keyframing, motion capture, or inverse kinematics.
9. What are your favorite software tools for 3D modeling and why?
My preferred software tools for 3D modeling include:
- ZBrush: For its powerful sculpting capabilities and intuitive brush system.
- Maya: For its comprehensive toolset for modeling, rigging, and animation.
- Substance Painter: For creating realistic textures and materials.
- Marmoset Toolbag: For real-time rendering and presentation.
10. How do you ensure the quality and accuracy of your 3D models?
I follow these guidelines to ensure the quality and accuracy of my 3D models:
- Attention to detail: Paying close attention to every aspect of the model, from proportions to textures.
- Reference usage: Relying on high-quality reference materials to ensure anatomical accuracy and realism.
- Feedback gathering: Seeking feedback from peers and colleagues to identify and address areas for improvement.
- Software proficiency: Mastering the software tools used to create the models and leveraging their capabilities effectively.
- Constant refinement: Iteratively refining the models based on feedback and observations to achieve the desired level of quality.
Interviewers often ask about specific skills and experiences. With ResumeGemini‘s customizable templates, you can tailor your resume to showcase the skills most relevant to the position, making a powerful first impression. Also check out Resume Template specially tailored for Welt Maker.
Career Expert Tips:
- Ace those interviews! Prepare effectively by reviewing the Top 50 Most Common Interview Questions on ResumeGemini.
- Navigate your job search with confidence! Explore a wide range of Career Tips on ResumeGemini. Learn about common challenges and recommendations to overcome them.
- Craft the perfect resume! Master the Art of Resume Writing with ResumeGemini’s guide. Showcase your unique qualifications and achievements effectively.
- Great Savings With New Year Deals and Discounts! In 2025, boost your job search and build your dream resume with ResumeGemini’s ATS optimized templates.
Researching the company and tailoring your answers is essential. Once you have a clear understanding of the Welt Maker‘s requirements, you can use ResumeGemini to adjust your resume to perfectly match the job description.
Key Job Responsibilities
Welt Makers are responsible for creating and maintaining the welts of shoes. Welts are the strips of leather that run around the perimeter of the shoe’s sole, and they play a vital role in keeping the shoe together. Welt Makers must have a strong understanding of leatherworking techniques, and they must be able to work with precision and accuracy.
1. Cutting and Preparing the Welt
The first step in making a welt is to cut a strip of leather to the correct size and shape. Welt Makers use a variety of tools to cut leather, including knives, scissors, and punches. Once the welt has been cut, it must be prepared for sewing. This involves thinning the edges of the welt and applying a sealant to help keep it from fraying.
2. Sewing the Welt
Once the welt has been prepared, it is sewn to the shoe’s upper. Welt Makers use a specialized sewing machine to sew the welt, and they must be able to control the stitch length and tension to ensure that the welt is secure and durable.
3. Trimming and Finishing the Welt
After the welt has been sewn, it must be trimmed and finished. Welt Makers use a variety of tools to trim the welt, including knives, scissors, and sandpaper. Once the welt has been trimmed, it is buffed and polished to give it a smooth and finished appearance.
4. Other Duties
In addition to their primary responsibilities, Welt Makers may also be responsible for other tasks, such as:
- Inspecting shoes for defects
- Packing and shipping shoes
- Cleaning and maintaining equipment
Interview Tips
Preparing for an interview for a Welt Maker position can be daunting, but there are a few things you can do to increase your chances of success.
1. Research the Company and Position
Before you go to your interview, take some time to research the company and the position you are applying for. This will help you understand the company’s culture and values, as well as the specific requirements of the job. You can find information about the company on their website, social media pages, and Glassdoor.
2. Practice Your Answers to Common Interview Questions
There are a few common interview questions that you are likely to be asked, such as “Tell me about yourself” and “Why are you interested in this position?”. It is helpful to practice your answers to these questions in advance so that you can deliver them confidently and clearly.
3. Be Prepared to Talk About Your Skills and Experience
The interviewer will want to know about your skills and experience as a Welt Maker. Be prepared to talk about your experience in cutting, preparing, and sewing welts, as well as any other relevant skills or experience you have.
4. Be Enthusiastic and Professional
It is important to be enthusiastic and professional during your interview. This will show the interviewer that you are interested in the position and that you are a hard worker.
5. Dress Appropriately
First impressions matter, so it is important to dress appropriately for your interview. This means wearing clean, pressed clothes that are appropriate for a professional setting.
Next Step:
Now that you’re armed with a solid understanding of what it takes to succeed as a Welt Maker, it’s time to turn that knowledge into action. Take a moment to revisit your resume, ensuring it highlights your relevant skills and experiences. Tailor it to reflect the insights you’ve gained from this blog and make it shine with your unique qualifications. Don’t wait for opportunities to come to you—start applying for Welt Maker positions today and take the first step towards your next career milestone. Your dream job is within reach, and with a polished resume and targeted applications, you’ll be well on your way to achieving your career goals! Build your resume now with ResumeGemini.
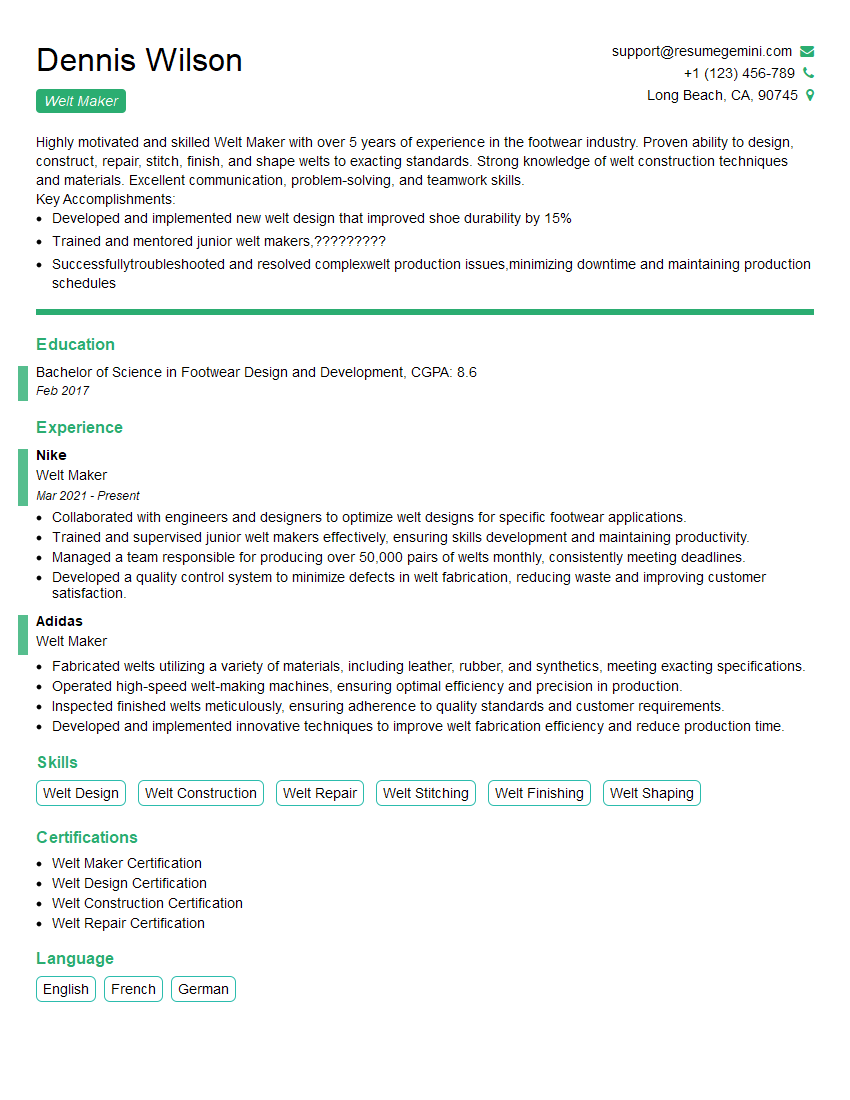