Ever felt underprepared for that crucial job interview? Or perhaps you’ve landed the interview but struggled to articulate your skills and experiences effectively? Fear not! We’ve got you covered. In this blog post, we’re diving deep into the Wire Welder interview questions that you’re most likely to encounter. But that’s not all. We’ll also provide expert insights into the key responsibilities of a Wire Welder so you can tailor your answers to impress potential employers.
Acing the interview is crucial, but landing one requires a compelling resume that gets you noticed. Crafting a professional document that highlights your skills and experience is the first step toward interview success. ResumeGemini can help you build a standout resume that gets you called in for that dream job.
Essential Interview Questions For Wire Welder
1. Describe the different types of wire welding processes and their respective advantages and disadvantages?
- Gas Metal Arc Welding (GMAW): Also known as MIG welding, this process uses a shielding gas to protect the weld pool from contamination. Advantages include high deposition rates, versatility, and ease of automation. Disadvantages include the need for a shielding gas and potential for spatter.
- Gas Tungsten Arc Welding (GTAW): Also known as TIG welding, this process uses a non-consumable tungsten electrode to create an arc. Advantages include high-quality welds, precise control, and the ability to weld thin materials. Disadvantages include lower deposition rates and a steeper learning curve.
- Flux-Cored Arc Welding (FCAW): This process uses a consumable electrode that contains a fluxing agent. Advantages include deep penetration, high deposition rates, and reduced spatter. Disadvantages include the need for flux removal and the potential for porosity.
2. Explain the importance of joint preparation and fit-up in wire welding?
Joint Preparation
- Removes contaminants and ensures a clean welding surface.
- Creates a proper gap for weld penetration and fusion.
- Improves weld quality, strength, and appearance.
Fit-Up
- Aligns and secures the workpieces to maintain proper joint fit.
- Prevents misalignment, distortion, and weld defects.
- Ensures consistent weld quality and structural integrity.
3. What are the key factors that affect wire welding quality and how can they be controlled?
- Welding Parameters: Voltage, current, wire feed speed, and travel speed need to be optimized for the specific materials and joint design.
- Material Properties: Thickness, composition, and surface condition can impact weld quality and require adjustments in welding parameters.
- Joint Fit-Up: Proper joint preparation and fit-up ensure good weld penetration and prevent defects.
- Welding Environment: Temperature, humidity, and wind can affect shielding gas protection and weld quality.
- Weld Cleaning: Removing slag, spatter, and oxides after welding improves weld appearance and prevents corrosion.
4. Describe the different types of welding defects and how to prevent them?
- Porosity: Caused by entrapped gases, can be prevented by using proper shielding gas and cleaning the weld area.
- Undercut: Grooving along the weld edges, can be prevented by adjusting welding parameters and maintaining proper joint fit.
- Cold Lap: Incomplete fusion between weld layers, can be prevented by using higher welding heat and proper joint preparation.
- Spatter: Molten metal droplets deposited outside the weld area, can be reduced by using anti-spatter spray and adjusting welding parameters.
5. How do you inspect wire welds to ensure quality and compliance with standards?
- Visual Inspection: Examination of the weld surface for defects, such as cracks, porosity, and undercuts.
- Non-Destructive Testing (NDT): Methods like radiography, ultrasonic testing, and magnetic particle inspection to detect internal defects.
- Destructive Testing: Tensile testing, bend testing, and impact testing to assess the mechanical properties of the weld.
- Compliance with Standards: Ensuring that welds meet industry standards, such as ASME, AWS, and ISO.
6. What is the importance of proper wire selection and how does it affect the welding process?
- Composition: Wire composition determines weld strength, corrosion resistance, and other properties.
- Diameter: Wire diameter affects deposition rate and penetration.
- Surface Condition: Clean wire ensures good electrical contact and weld quality.
- Shielding Gas Compatibility: Wire should be compatible with the shielding gas used for protection.
7. Describe the safety precautions that should be followed when wire welding?
- Personal Protective Equipment (PPE): Wearing proper clothing, gloves, helmet, and respirator to protect from heat, sparks, and fumes.
- Welding Area Ventilation: Ensuring adequate ventilation to remove welding fumes.
- Electrical Safety: Grounding equipment, proper wiring, and avoiding live electrical components.
- Fire Prevention: Using fire-resistant materials, having a fire extinguisher nearby, and clearing the work area of combustibles.
8. What are the common troubleshooting techniques for wire welding problems?
- Poor Weld Penetration: Increase welding heat, adjust wire speed, or check for proper joint fit.
- Excessive Spatter: Reduce welding current, adjust wire stickout, or use anti-spatter spray.
- Porosity: Check shielding gas flow, clean the weld area, or use a higher purity gas.
- Birdnesting (Wire Tangling): Adjust wire tension, check wire feed mechanism, or use a different type of wire.
9. How do you stay updated with advancements and best practices in wire welding?
- Trade Journals and Publications: Subscribing to industry magazines and reading technical articles.
- Conferences and Seminars: Attending events to learn from experts and network with peers.
- Online Resources: Utilizing websites, forums, and social media groups dedicated to wire welding.
- Manufacturer Training: Participating in training programs offered by welding equipment manufacturers.
10. Describe a complex wire welding project you have worked on and the challenges you faced?
- Project Description: Provide an overview of the project, including the materials, joint design, and welding specifications.
- Challenges: Explain the specific technical difficulties encountered, such as complex joint geometry, material thickness, or welding in confined spaces.
- Solutions: Describe the innovative methods or techniques used to overcome the challenges and ensure weld quality.
- Results: Highlight the successful completion of the project and any positive feedback received.
Interviewers often ask about specific skills and experiences. With ResumeGemini‘s customizable templates, you can tailor your resume to showcase the skills most relevant to the position, making a powerful first impression. Also check out Resume Template specially tailored for Wire Welder.
Career Expert Tips:
- Ace those interviews! Prepare effectively by reviewing the Top 50 Most Common Interview Questions on ResumeGemini.
- Navigate your job search with confidence! Explore a wide range of Career Tips on ResumeGemini. Learn about common challenges and recommendations to overcome them.
- Craft the perfect resume! Master the Art of Resume Writing with ResumeGemini’s guide. Showcase your unique qualifications and achievements effectively.
- Great Savings With New Year Deals and Discounts! In 2025, boost your job search and build your dream resume with ResumeGemini’s ATS optimized templates.
Researching the company and tailoring your answers is essential. Once you have a clear understanding of the Wire Welder‘s requirements, you can use ResumeGemini to adjust your resume to perfectly match the job description.
Key Job Responsibilities
Wire Welders play a crucial role in the fabrication industry, utilizing specialized equipment and techniques to join metal components through electric arc welding. Their key responsibilities are multifaceted and include the following:
1. Welding Operations
Wire Welders are responsible for operating specialized welding equipment to fuse metal components together, including gas metal arc welding (GMAW) and flux-cored arc welding (FCAW) techniques. They must demonstrate proficiency in handling various thicknesses and types of metals, producing welds that meet industry standards for strength, durability, and precision.
2. Quality Control
Ensuring the quality of welds is paramount for Wire Welders. They inspect their work thoroughly, identifying any defects or inconsistencies that may affect the structural integrity or functionality of the finished product. They may utilize non-destructive testing methods to evaluate weld quality and ensure compliance with specifications.
3. Equipment Maintenance
Wire Welders are responsible for maintaining their equipment to ensure optimal performance and safety. This includes tasks such as cleaning and calibrating welding machines, replacing consumables like welding tips and nozzles, and troubleshooting any technical issues that may arise during operations.
4. Work Area Safety
Adhering to safety protocols is essential in the welding profession. Wire Welders must follow established procedures to prevent accidents and protect themselves and others from potential hazards associated with welding operations. This includes wearing appropriate personal protective equipment (PPE), maintaining a clean and organized work area, and storing welding materials safely.
Interview Tips
Preparing for a Wire Welder interview requires meticulous attention to detail and a thorough understanding of the role. Candidates who take the following steps can increase their chances of making a positive impression and securing the position:
1. Technical Proficiency
Highlight your expertise in wire welding techniques, including GMAW and FCAW. Demonstrate your knowledge of different wire types and shielding gases used in welding operations. Be prepared to discuss your understanding of welding codes and standards, as well as your experience with various welding equipment.
- Example Outline:
- “I have extensive experience in gas metal arc welding (GMAW), having worked on projects involving stainless steel, aluminum, and mild steel fabrication. I’m proficient in selecting the appropriate wire and shielding gas combination for different metals and thicknesses.”
2. Problem-Solving and Critical Thinking
Emphasize your ability to identify and resolve welding-related issues, such as weld defects, equipment malfunctions, and material inconsistencies. Explain how you approach problem-solving and your experience in troubleshooting welding challenges.
- Example Outline:
- “In my previous role, I encountered a recurring issue with weld porosity. I conducted thorough investigations and identified the cause as moisture contamination in the shielding gas. By implementing proper gas handling procedures, I was able to eliminate the problem and improve the weld quality significantly.”
3. Safety Consciousness
Showcase your commitment to safety in the workplace. Describe your understanding of welding-related hazards and your adherence to safety protocols. Discuss your experience in using personal protective equipment (PPE) and maintaining a safe work environment.
- Example Outline:
- “Safety is paramount in my approach to welding. I consistently wear appropriate PPE, including a welding helmet, gloves, and flame-resistant clothing. I ensure that my work area is well-ventilated and free of tripping hazards, and I always follow established safety procedures to prevent accidents.”
4. Communication and Teamwork
Welders often work in collaborative environments. Highlight your ability to communicate effectively with colleagues, supervisors, and clients. Explain your experience in working as part of a team and your willingness to contribute to a positive and productive work atmosphere.
- Example Outline:
- “I’m a highly collaborative individual with a strong work ethic. In my previous role, I worked closely with engineers and fabricators to interpret drawings and ensure that welding operations were aligned with design specifications. I’m always willing to share my knowledge and expertise with others to achieve optimal results.”
Next Step:
Armed with this knowledge, you’re now well-equipped to tackle the Wire Welder interview with confidence. Remember, preparation is key. So, start crafting your resume, highlighting your relevant skills and experiences. Don’t be afraid to tailor your application to each specific job posting. With the right approach and a bit of practice, you’ll be well on your way to landing your dream job. Build your resume now from scratch or optimize your existing resume with ResumeGemini. Wish you luck in your career journey!
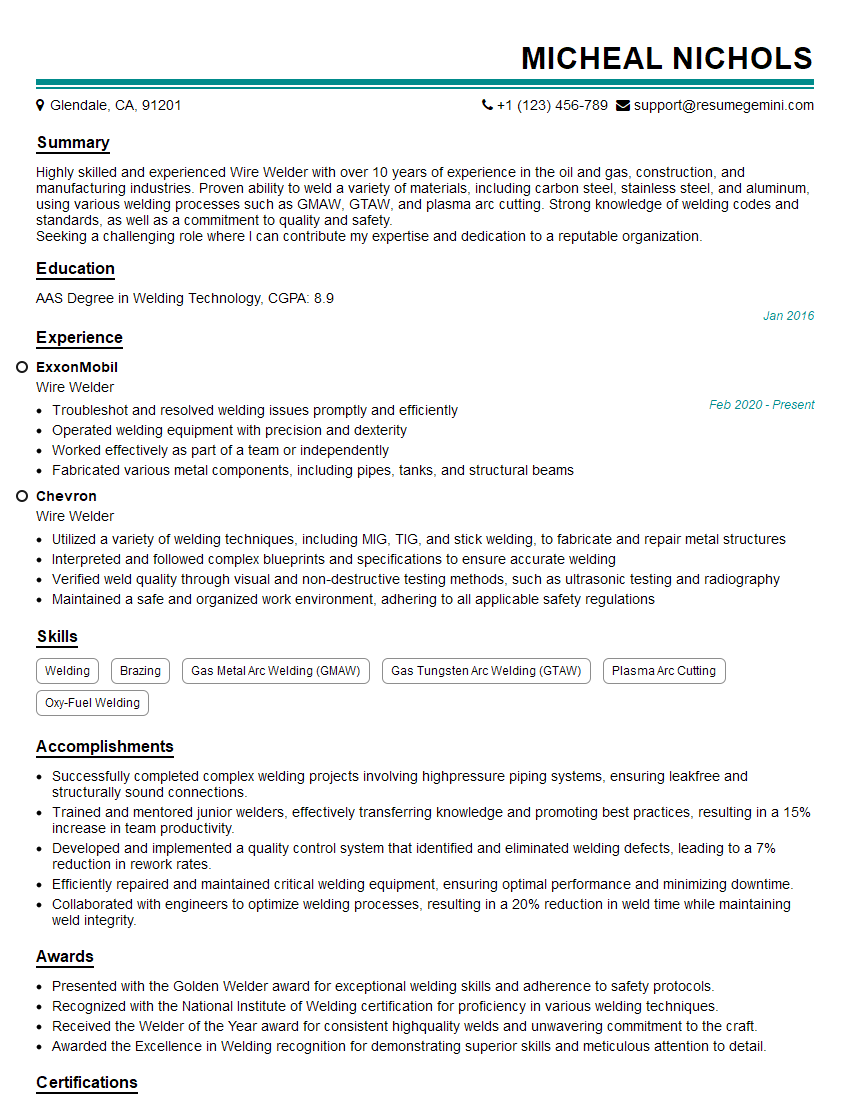