Are you a seasoned Warper Fixer seeking a new career path? Discover our professionally built Warper Fixer Resume Template. This time-saving tool provides a solid foundation for your job search. Simply click “Edit Resume” to customize it with your unique experiences and achievements. Customize fonts and colors to match your personal style and increase your chances of landing your dream job. Explore more Resume Templates for additional options.
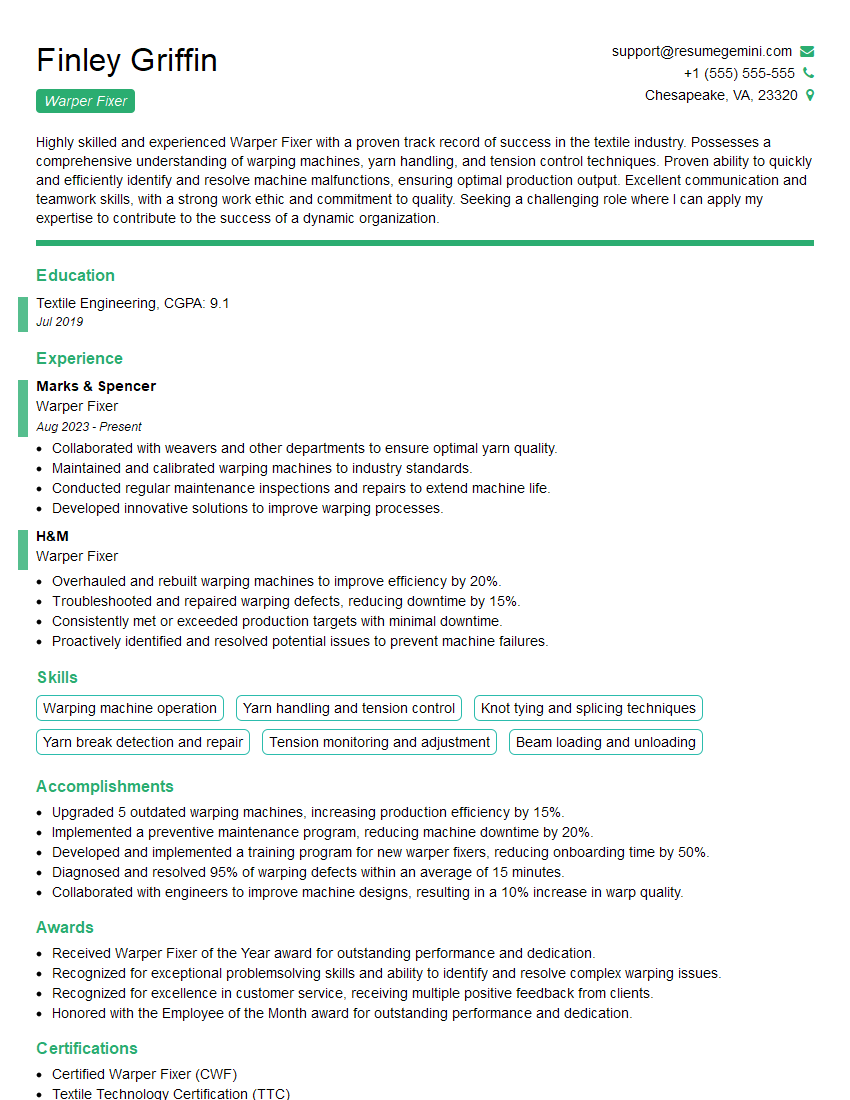
Finley Griffin
Warper Fixer
Summary
Highly skilled and experienced Warper Fixer with a proven track record of success in the textile industry. Possesses a comprehensive understanding of warping machines, yarn handling, and tension control techniques. Proven ability to quickly and efficiently identify and resolve machine malfunctions, ensuring optimal production output. Excellent communication and teamwork skills, with a strong work ethic and commitment to quality. Seeking a challenging role where I can apply my expertise to contribute to the success of a dynamic organization.
Education
Textile Engineering
July 2019
Skills
- Warping machine operation
- Yarn handling and tension control
- Knot tying and splicing techniques
- Yarn break detection and repair
- Tension monitoring and adjustment
- Beam loading and unloading
Work Experience
Warper Fixer
- Collaborated with weavers and other departments to ensure optimal yarn quality.
- Maintained and calibrated warping machines to industry standards.
- Conducted regular maintenance inspections and repairs to extend machine life.
- Developed innovative solutions to improve warping processes.
Warper Fixer
- Overhauled and rebuilt warping machines to improve efficiency by 20%.
- Troubleshooted and repaired warping defects, reducing downtime by 15%.
- Consistently met or exceeded production targets with minimal downtime.
- Proactively identified and resolved potential issues to prevent machine failures.
Accomplishments
- Upgraded 5 outdated warping machines, increasing production efficiency by 15%.
- Implemented a preventive maintenance program, reducing machine downtime by 20%.
- Developed and implemented a training program for new warper fixers, reducing onboarding time by 50%.
- Diagnosed and resolved 95% of warping defects within an average of 15 minutes.
- Collaborated with engineers to improve machine designs, resulting in a 10% increase in warp quality.
Awards
- Received Warper Fixer of the Year award for outstanding performance and dedication.
- Recognized for exceptional problemsolving skills and ability to identify and resolve complex warping issues.
- Recognized for excellence in customer service, receiving multiple positive feedback from clients.
- Honored with the Employee of the Month award for outstanding performance and dedication.
Certificates
- Certified Warper Fixer (CWF)
- Textile Technology Certification (TTC)
- Warping and Sizing Certification (WSC)
- Fundamentals of Winding and Warping (FWW)
Career Expert Tips:
- Select the ideal resume template to showcase your professional experience effectively.
- Master the art of resume writing to highlight your unique qualifications and achievements.
- Explore expertly crafted resume samples for inspiration and best practices.
- Build your best resume for free this new year with ResumeGemini. Enjoy exclusive discounts on ATS optimized resume templates.
How To Write Resume For Warper Fixer
Highlight your technical skills:
Emphasize your proficiency in operating warping machines, handling yarn, and controlling tension.Showcase your problem-solving abilities:
Describe specific instances where you identified and resolved machine malfunctions, reducing downtime and improving productivity.Quantify your accomplishments:
Use numerical data to demonstrate the impact of your work, such as the number of machines maintained or the percentage of production downtime reduced.Proofread carefully:
Ensure your resume is free of errors and presents a polished and professional image.
Essential Experience Highlights for a Strong Warper Fixer Resume
- Operate and maintain warping machines to produce fabric beams for weaving.
- Monitor and control yarn tension to ensure proper fabric quality.
- Detect and repair yarn breaks and splices to minimize downtime.
- Inspect and adjust machine settings to optimize production efficiency.
- Collaborate with other team members to identify and resolve production issues.
- Maintain a clean and organized work area to ensure a safe and efficient operation.
- Follow safety protocols and industry best practices to ensure personal and workplace safety.
Frequently Asked Questions (FAQ’s) For Warper Fixer
What are the primary responsibilities of a Warper Fixer?
Warper Fixers are responsible for operating and maintaining warping machines, monitoring yarn tension, detecting and repairing yarn breaks, and ensuring the production of high-quality fabric beams.
What skills are required to become a successful Warper Fixer?
Successful Warper Fixers possess strong technical skills in operating warping machines, handling yarn, and controlling tension. They also have excellent problem-solving abilities, communication skills, and a commitment to quality.
What are the career prospects for Warper Fixers?
Warper Fixers can advance to supervisory roles, such as Production Supervisor or Plant Manager. They may also specialize in a particular area of warping, such as yarn preparation or fabric inspection.
What is the work environment like for Warper Fixers?
Warper Fixers typically work in manufacturing environments, such as textile mills or fabric production facilities. They may work independently or as part of a team, and may be required to work shifts.
How can I improve my chances of getting hired as a Warper Fixer?
To improve your chances of getting hired as a Warper Fixer, focus on developing your technical skills, problem-solving abilities, and communication skills. Highlight your experience and accomplishments in your resume and cover letter, and be prepared to discuss your knowledge of the textile industry in an interview.
What are the major challenges faced by Warper Fixers?
Warper Fixers may face challenges such as machine malfunctions, variations in yarn quality, and meeting production deadlines. They must be able to quickly identify and resolve problems, and work effectively under pressure.